Introduction to signaling Flex Circuits
Flex circuits, also known as flexible printed circuits (FPCs), have revolutionized the electronics industry by providing a lightweight, compact, and versatile solution for interconnecting electronic components. Among the various types of flex circuits, those employing differential signaling have gained significant attention due to their ability to transmit high-speed signals with improved noise immunity and reduced electromagnetic interference (EMI). In this article, we will delve into the world of differential signaling flex circuits, exploring their fundamentals, design considerations, manufacturing processes, and applications.
What are Differential Signaling Flex Circuits?
Differential signaling flex circuits are a type of flex circuit that utilizes differential signaling techniques to transmit data between electronic components. Differential signaling involves using two complementary signals, typically labeled as positive (P) and negative (N), to represent a single piece of information. The receiver interprets the difference between these two signals, rather than their absolute values, to determine the transmitted data.
Benefits of Differential Signaling in Flex Circuits
Differential signaling offers several advantages over single-ended signaling in flex circuits:
-
Noise Immunity: By using two complementary signals, differential signaling cancels out common-mode noise, which affects both signals equally. This results in a higher signal-to-noise ratio (SNR) and improved noise immunity.
-
Reduced EMI: Differential signaling minimizes electromagnetic radiation, as the equal and opposite currents on the differential pair cancel out each other’s electromagnetic fields. This reduction in EMI helps to prevent interference with nearby electronic devices and ensures compliance with electromagnetic compatibility (EMC) regulations.
-
High-Speed Signal Transmission: Differential signaling enables high-speed data transmission over longer distances compared to single-ended signaling. The improved noise immunity and reduced EMI allow for faster signal transitions and higher data rates.
-
Reduced Crosstalk: The complementary nature of differential signals minimizes crosstalk between adjacent signal traces on the flex circuit. This is particularly important in high-density designs where multiple differential pairs are routed in close proximity.
Designing Differential Signaling Flex Circuits
Designing differential signaling flex circuits requires careful consideration of various factors to ensure optimal signal integrity and performance. Let’s explore some key design aspects.
Signal Integrity Considerations
Signal integrity is crucial in differential signaling flex circuits to maintain the quality and reliability of transmitted signals. Several factors influence signal integrity:
-
Impedance Matching: Proper impedance matching between the differential pair and the receiver is essential to minimize signal reflections and ensure efficient power transfer. The characteristic impedance of the differential pair should be matched to the receiver’s input impedance, typically 50Ω or 100Ω.
-
Trace Geometry: The geometry of the differential pair traces plays a significant role in maintaining signal integrity. The traces should be routed as a tightly coupled pair with a controlled spacing between them. The trace width and spacing determine the characteristic impedance of the differential pair.
-
Length Matching: To maintain signal integrity, it is important to ensure that the lengths of the positive and negative traces in a differential pair are closely matched. Any mismatch in length can lead to signal skew and degrade the differential signal quality.
-
Termination: Proper termination techniques, such as parallel termination or AC termination, should be employed to minimize signal reflections and maintain signal integrity. The choice of termination depends on the signal frequency, trace length, and receiver characteristics.
Layout and Routing Guidelines
Proper layout and routing techniques are essential for optimal performance of differential signaling flex circuits. Here are some guidelines to follow:
-
Differential Pair Routing: Route differential pairs as closely coupled traces with a controlled spacing between them. Maintain a consistent spacing along the entire length of the differential pair to ensure a constant characteristic impedance.
-
Trace Width and Spacing: Choose appropriate trace widths and spacing based on the desired characteristic impedance and the manufacturing capabilities of the flex circuit fabricator. Consult with the fabricator to determine the minimum trace width and spacing that can be reliably manufactured.
-
Layer Arrangement: When using multi-layer flex circuits, carefully plan the layer arrangement to minimize crosstalk and optimize signal integrity. Separate differential pairs from other signal traces and power/ground planes using appropriate spacing and shielding techniques.
-
Length Matching: Ensure that the lengths of the positive and negative traces in a differential pair are closely matched. Use serpentine routing or delay lines to equalize the lengths if necessary.
-
Grounding and Shielding: Provide adequate grounding and shielding to minimize noise and crosstalk. Use ground planes and shields to isolate differential pairs from other signals and reduce EMI.
Manufacturing Differential Signaling Flex Circuits
Manufacturing differential signaling flex circuits involves several processes and considerations to ensure high-quality and reliable products.
Flex Circuit Materials
The choice of materials for differential signaling flex circuits is crucial for signal integrity and mechanical performance. Common materials include:
-
Polyimide: Polyimide is the most widely used substrate material for flex circuits due to its excellent electrical, mechanical, and thermal properties. It offers high dielectric strength, low dielectric constant, and good flexibility.
-
Copper: Copper is the primary conductor material used in flex circuits. It is chosen for its high conductivity, durability, and compatibility with various plating processes.
-
Adhesives: Adhesives are used to bond the copper traces to the polyimide substrate. The selection of adhesives depends on the specific requirements of the application, such as temperature range, chemical resistance, and flexibility.
Manufacturing Processes
The manufacturing process for differential signaling flex circuits typically involves the following steps:
-
Substrate Preparation: The polyimide substrate is cleaned and prepared for the subsequent processes.
-
Copper Lamination: Copper foils are laminated onto the polyimide substrate using heat and pressure.
-
Patterning: The desired circuit pattern is transferred onto the copper-laminated substrate using photolithography or laser direct imaging (LDI) techniques.
-
Etching: The unwanted copper areas are etched away using chemical or laser etching processes, leaving behind the desired circuit traces.
-
Plating: Additional plating processes, such as electroless nickel/immersion gold (ENIG) or electroplated nickel/gold, may be applied to improve solderability and protect the copper traces.
-
Coverlay Application: A coverlay, which is an insulating layer, is laminated over the circuit traces to provide protection and insulation.
-
Finishing: The flex circuit undergoes final finishing processes, such as solder mask application, legend printing, and surface finish treatments.
Quality Control and Testing
Stringent quality control and testing procedures are essential to ensure the reliability and performance of differential signaling flex circuits. Some common quality control measures include:
-
Visual Inspection: Flex circuits are visually inspected for any defects, such as misalignment, shorts, or opens, using magnification aids or automated optical inspection (AOI) systems.
-
Electrical Testing: Electrical tests, such as continuity, insulation resistance, and high-potential (HiPot) tests, are performed to verify the electrical integrity of the flex circuits.
-
Impedance Testing: Time-domain reflectometry (TDR) or vector network analyzer (VNA) measurements are used to verify the characteristic impedance of the differential pairs and ensure proper impedance matching.
-
Signal Integrity Testing: Signal integrity tests, such as eye diagram analysis or bit error rate (BER) testing, are conducted to assess the quality of the transmitted signals and ensure compliance with the required specifications.
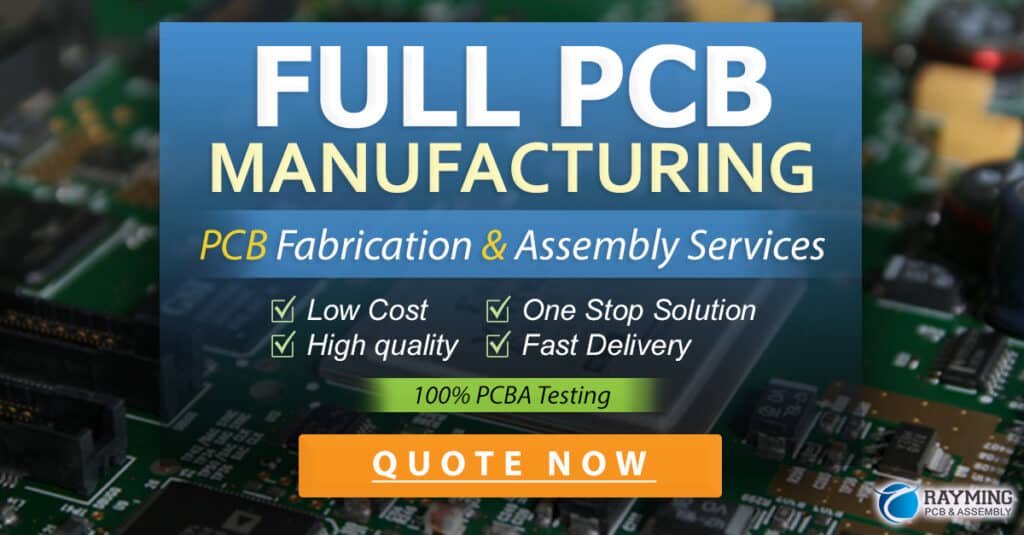
Applications of Differential Signaling Flex Circuits
Differential signaling flex circuits find applications in various industries and products where high-speed data transmission, noise immunity, and flexibility are crucial. Some common applications include:
-
Consumer Electronics: Differential signaling flex circuits are widely used in consumer electronics devices, such as smartphones, tablets, laptops, and wearables, to interconnect high-speed components like cameras, displays, and sensors.
-
Automotive Electronics: In the automotive industry, differential signaling flex circuits are employed in advanced driver assistance systems (ADAS), infotainment systems, and vehicle networking applications, where reliable and high-speed data communication is essential.
-
Medical Devices: Differential signaling flex circuits are used in medical devices, such as patient monitoring systems, imaging equipment, and wearable health monitors, to transmit sensitive medical data with high fidelity and reliability.
-
Industrial Automation: In industrial automation systems, differential signaling flex circuits are utilized for high-speed data communication between sensors, controllers, and actuators, enabling precise control and monitoring of manufacturing processes.
-
Aerospace and Defense: Differential signaling flex circuits are employed in aerospace and defense applications, such as avionics systems, satellite communications, and military equipment, where high-speed data transmission, reliability, and space constraints are critical.
Frequently Asked Questions (FAQ)
-
What is the difference between differential signaling and single-ended signaling in flex circuits?
Differential signaling uses two complementary signals to represent a single piece of information, while single-ended signaling uses a single signal referenced to a common ground. Differential signaling offers better noise immunity, reduced EMI, and higher data rates compared to single-ended signaling. -
How does differential signaling improve noise immunity in flex circuits?
Differential signaling improves noise immunity by using two complementary signals that are affected equally by common-mode noise. The receiver interprets the difference between the two signals, effectively canceling out the common-mode noise and resulting in a higher signal-to-noise ratio. -
What are the key design considerations for differential signaling flex circuits?
The key design considerations for differential signaling flex circuits include impedance matching, trace geometry, length matching, termination, and proper layout and routing techniques. These factors are crucial for maintaining signal integrity and optimizing the performance of the flex circuit. -
What materials are commonly used in the manufacturing of differential signaling flex circuits?
The most commonly used materials in differential signaling flex circuits are polyimide for the substrate, copper for the conductors, and various adhesives for bonding the layers together. The choice of materials depends on the specific requirements of the application, such as electrical properties, mechanical flexibility, and environmental conditions. -
What are some common applications of differential signaling flex circuits?
Differential signaling flex circuits find applications in various industries, including consumer electronics, automotive electronics, medical devices, industrial automation, and aerospace and defense. They are used in products and systems that require high-speed data transmission, noise immunity, and flexibility, such as smartphones, advanced driver assistance systems, patient monitoring devices, and avionics systems.
Conclusion
Differential signaling flex circuits have emerged as a crucial technology for high-speed data transmission in a wide range of applications. By leveraging the benefits of differential signaling, these flex circuits offer improved noise immunity, reduced EMI, and faster data rates compared to traditional single-ended signaling. Designing and manufacturing differential signaling flex circuits requires careful consideration of signal integrity, layout, and material selection to ensure optimal performance and reliability.
As the demand for high-speed data communication continues to grow across industries, differential signaling flex circuits will play an increasingly important role in enabling the development of advanced electronic systems. By understanding the principles, design considerations, and manufacturing processes involved in differential signaling flex circuits, engineers and designers can create innovative solutions that push the boundaries of performance and functionality in the ever-evolving world of electronics.
Leave a Reply