Introduction to Testpoints on PCBs
Testpoints are an essential component of modern printed circuit board (PCB) design. They provide a convenient and reliable way to access specific points on a PCB for testing, debugging, and programming purposes. By incorporating testpoints into your PCB layout, you can greatly simplify the process of verifying the functionality of your board and identifying any issues that may arise during the manufacturing or assembly process.
In this article, we will explore the various aspects of adding testpoints to PCBs. We will discuss the different types of testpoints available, their applications, and best practices for incorporating them into your PCB design. Additionally, we will delve into the benefits of using testpoints and how they can help streamline your testing and debugging processes.
Types of Testpoints for PCBs
There are several types of testpoints commonly used in PCB design. Each type has its own unique characteristics and is suited for specific applications. Let’s take a closer look at the most common types of testpoints:
Through-Hole Testpoints
Through-hole testpoints are the most traditional type of testpoints used in PCB design. They consist of a small hole drilled through the PCB, with a conductive pad surrounding the hole on both sides of the board. These testpoints are typically accessed using a test probe or a spring-loaded pin.
Advantages | Disadvantages |
---|---|
Easy to access | Requires drilling holes in the PCB |
Reliable connection | Consumes more board space |
Suitable for high-current applications | Not suitable for high-density designs |
Surface Mount Testpoints
Surface mount testpoints, also known as SMT testpoints, are becoming increasingly popular in modern PCB design. They are small, flat pads that are placed on the surface of the PCB. These testpoints are accessed using a test probe or a specially designed test fixture.
Advantages | Disadvantages |
---|---|
Compact size | Requires specialized test fixtures |
Suitable for high-density designs | Less reliable than through-hole testpoints |
Easy to place using automated assembly processes | Not suitable for high-current applications |
Edge Connector Testpoints
Edge connector testpoints are used when testing needs to be performed through the edge of the PCB. These testpoints are typically located along the edge of the board and are accessed using a mating connector or a test probe.
Advantages | Disadvantages |
---|---|
Convenient access from the edge of the board | Requires additional space along the PCB edge |
Suitable for automated testing | May require custom connectors |
Can be used for programming and debugging | Limited number of testpoints available |
Placement and Routing Considerations for Testpoints
When adding testpoints to your PCB design, there are several placement and routing considerations to keep in mind. Proper placement and routing of testpoints can greatly improve the accessibility and reliability of your testing and debugging processes.
Testpoint Placement
- Place testpoints in easily accessible locations on the PCB, such as near the edges or in dedicated test areas.
- Ensure that testpoints are spaced adequately to allow for easy probing and to avoid accidental short circuits.
- Consider the placement of testpoints in relation to other components and connectors on the board.
- Keep testpoints away from high-speed signals and sensitive analog circuits to minimize interference.
Testpoint Routing
- Route traces to testpoints using appropriate trace widths and spacing to ensure signal integrity.
- Avoid routing traces under or near testpoints to prevent accidental damage during probing.
- Use ground planes or guard rings around testpoints to reduce noise and improve signal quality.
- Consider the use of test pads or vias to route signals to inner layers of the PCB for improved accessibility.
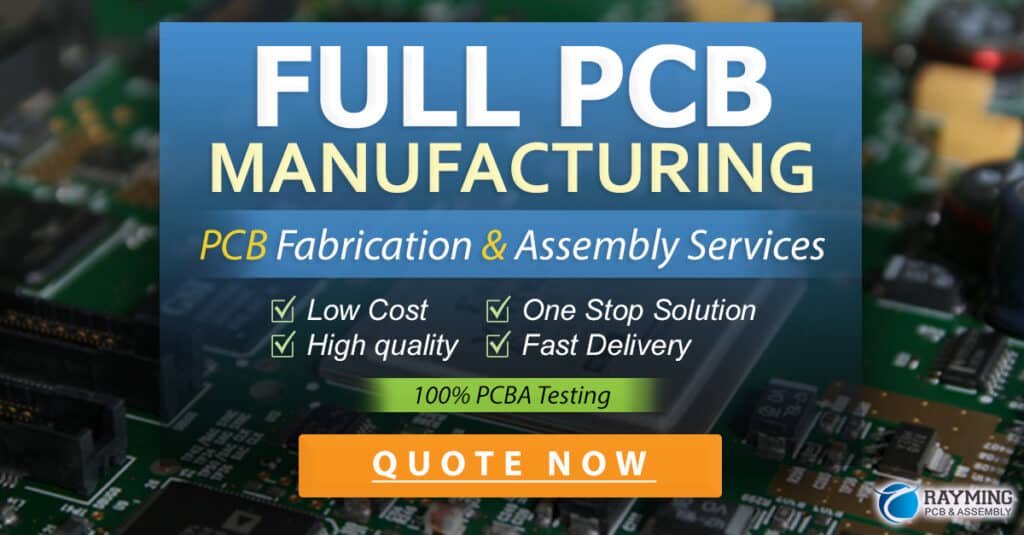
Best Practices for Incorporating Testpoints in PCB Design
To ensure the effective use of testpoints in your PCB design, consider the following best practices:
-
Plan testpoints early in the design process: Incorporate testpoints into your PCB layout from the beginning, rather than adding them as an afterthought. This allows for optimal placement and routing of testpoints.
-
Use consistent naming and labeling conventions: Assign clear and descriptive names to your testpoints, and label them accordingly on the PCB silkscreen. This helps prevent confusion and errors during testing and debugging.
-
Provide comprehensive documentation: Create detailed documentation that includes the location, function, and expected values of each testpoint. This documentation should be easily accessible to anyone involved in the testing and debugging process.
-
Consider the use of test fixtures: For high-volume testing or automated testing processes, consider designing custom test fixtures that interface with your testpoints. This can greatly streamline the testing process and improve reliability.
-
Regularly review and update testpoint designs: As your PCB design evolves, review and update your testpoint placement and routing to ensure they remain accessible and functional. This is particularly important when making changes to the board layout or component placement.
Benefits of Using Testpoints on PCBs
Incorporating testpoints into your PCB design offers numerous benefits that can greatly improve the efficiency and effectiveness of your testing and debugging processes. Some of the key benefits include:
-
Improved accessibility: Testpoints provide convenient access points for probing and measuring signals on the PCB. This can greatly simplify the process of testing and debugging, particularly for complex or densely populated boards.
-
Faster troubleshooting: By strategically placing testpoints at key locations on the PCB, you can quickly isolate and identify issues during the troubleshooting process. This can help reduce downtime and improve overall product quality.
-
Enhanced manufacturing testability: Testpoints enable automated testing during the manufacturing process, allowing for quick verification of board functionality and reducing the likelihood of defective products reaching the end-user.
-
Simplified programming and firmware updates: Testpoints can be used to access programming interfaces, such as JTAG or SWD, allowing for easy programming and firmware updates without the need for specialized connectors.
-
Reduced development time and costs: By incorporating testpoints early in the design process and using them effectively throughout the development cycle, you can catch and resolve issues more quickly, reducing overall development time and costs.
Frequently Asked Questions (FAQ)
-
What is the purpose of adding testpoints to a PCB?
Testpoints are added to a PCB to provide convenient access points for testing, debugging, and programming purposes. They allow engineers and technicians to easily probe and measure signals at specific locations on the board. -
What are the different types of testpoints used in PCB design?
The most common types of testpoints used in PCB design include through-hole testpoints, surface mount testpoints, and edge connector testpoints. Each type has its own unique characteristics and is suited for specific applications. -
How do I choose the appropriate type of testpoint for my PCB design?
The choice of testpoint type depends on several factors, such as the available board space, the desired accessibility, and the specific testing or programming requirements. Through-hole testpoints are suitable for high-current applications and provide reliable connections, while surface mount testpoints are compact and ideal for high-density designs. Edge connector testpoints are convenient for accessing signals from the edge of the board. -
What are some best practices for placing testpoints on a PCB?
When placing testpoints on a PCB, consider the following best practices: - Place testpoints in easily accessible locations, such as near the edges or in dedicated test areas.
- Ensure adequate spacing between testpoints to avoid accidental short circuits and allow for easy probing.
- Keep testpoints away from high-speed signals and sensitive analog circuits to minimize interference.
-
Use consistent naming and labeling conventions for clarity and ease of use.
-
How can testpoints help streamline the testing and debugging process?
Testpoints provide several benefits that can streamline the testing and debugging process: - They improve accessibility, allowing for convenient probing and measurement of signals on the PCB.
- Strategically placed testpoints enable faster troubleshooting by isolating and identifying issues more quickly.
- Testpoints facilitate automated testing during the manufacturing process, ensuring board functionality and reducing the likelihood of defective products.
- They simplify programming and firmware updates by providing access to programming interfaces without the need for specialized connectors.
- Incorporating testpoints early in the design process can help catch and resolve issues more quickly, reducing overall development time and costs.
Conclusion
Adding testpoints to your PCB design is a crucial step in ensuring the testability, debuggability, and overall quality of your electronic products. By understanding the different types of testpoints available, considering placement and routing best practices, and leveraging the benefits they offer, you can greatly enhance your testing and debugging processes.
Remember to plan testpoints early in the design process, use consistent naming and labeling conventions, provide comprehensive documentation, and regularly review and update your testpoint designs as your PCB evolves. By following these guidelines and best practices, you can unlock the full potential of testpoints in your PCB design and streamline your development efforts.
As the complexity of electronic systems continues to grow, the importance of effective testing and debugging techniques cannot be overstated. By incorporating testpoints into your PCB design strategy, you can ensure that your products meet the highest standards of quality, reliability, and functionality, ultimately leading to greater customer satisfaction and success in the marketplace.
Leave a Reply