The Importance of Supply Chain Information in Product Development
In today’s globalized and interconnected world, supply chain management has become an integral part of product development. Companies are increasingly recognizing the importance of having detailed and accurate supply chain information for each component used in their products. This information enables them to make informed decisions, mitigate risks, and ensure the smooth flow of materials and goods throughout the supply chain.
Benefits of Incorporating Supply Chain Information
Incorporating supply chain information into component data offers several key benefits:
-
Improved Traceability: By having detailed information about the origin, movement, and status of each component, companies can easily trace the path of materials from suppliers to end products. This traceability is crucial for identifying and resolving issues, such as quality defects or supply disruptions.
-
Enhanced Risk Management: Supply chain information helps companies assess and manage potential risks associated with their components. By understanding the suppliers, manufacturing locations, and logistics involved, companies can proactively identify and mitigate risks related to quality, delivery, or compliance.
-
Increased Transparency: Detailed supply chain information promotes transparency throughout the organization and with external stakeholders. It enables effective communication and collaboration among different departments, such as procurement, engineering, and manufacturing. Moreover, it allows companies to provide accurate and timely information to customers, regulators, and other stakeholders.
-
Compliance with Regulations: Many industries are subject to stringent regulations regarding the sourcing and use of materials. Supply chain information helps companies ensure compliance with these regulations by providing the necessary documentation and data. This is particularly important for industries such as aerospace, automotive, and medical devices.
-
Optimization of Inventory and Logistics: By having visibility into the supply chain, companies can optimize their inventory levels and logistics operations. They can better forecast demand, plan production schedules, and manage inventory to minimize costs and improve efficiency.
Key Elements of Supply Chain Information
When adding supply chain information to components, it is essential to capture the following key elements:
-
Supplier Details: Include information about the supplier, such as their name, location, contact information, and any relevant certifications or qualifications.
-
Material Sourcing: Specify the origin of the materials used in the component, including the country of origin, raw material suppliers, and any applicable ethical or environmental certifications.
-
Manufacturing Process: Provide details about the manufacturing process, including the production location, equipment used, and any specific process parameters or standards followed.
-
Quality Control: Document the quality control measures in place, such as inspections, testing, and certifications. Include information about any quality management systems (e.g., ISO 9001) implemented by the supplier or manufacturer.
-
Logistics and Transportation: Capture information about the transportation and logistics involved in moving the component from the supplier to the company’s facilities. This may include shipping methods, lead times, and any special handling requirements.
-
Compliance and Regulatory Information: Include any relevant compliance or regulatory information, such as RoHS (Restriction of Hazardous Substances) compliance, REACH (Registration, Evaluation, Authorization, and Restriction of Chemicals) registration, or conflict mineral declarations.
-
Pricing and Contractual Details: Document the pricing, payment terms, and any contractual agreements related to the component and its supply chain.
Implementing Supply Chain Information in Product Development
To effectively incorporate supply chain information into product development, companies should follow these best practices:
-
Establish a Centralized Database: Create a centralized database or product lifecycle management (PLM) system to store and manage supply chain information for all components. This ensures that the information is easily accessible, up-to-date, and consistent across the organization.
-
Collaborate with Suppliers: Work closely with suppliers to gather accurate and comprehensive supply chain information. Establish clear communication channels and protocols for exchanging and updating this information regularly.
-
Integrate with Existing Systems: Integrate the supply chain information database with other relevant systems, such as enterprise resource planning (ERP), manufacturing execution systems (MES), and quality management systems (QMS). This enables seamless data flow and ensures that the information is utilized effectively throughout the product development process.
-
Conduct Regular Audits and Updates: Regularly audit and update the supply chain information to ensure its accuracy and completeness. This may involve conducting supplier audits, reviewing documentation, and verifying the information against actual practices.
-
Train Employees: Provide training to employees on the importance of supply chain information and how to effectively use and maintain the database. Ensure that all relevant departments, including procurement, engineering, and manufacturing, are involved in the process.
-
Leverage Data Analytics: Utilize data analytics tools to analyze the supply chain information and gain insights into trends, patterns, and potential risks. This can help companies make data-driven decisions and optimize their supply chain operations.
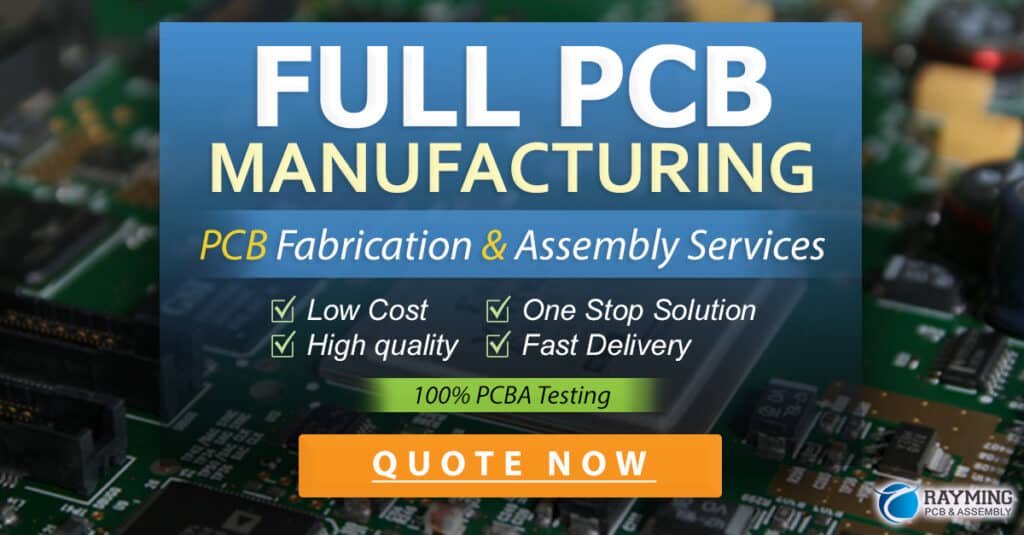
Examples of Supply Chain Information in Practice
To illustrate the application of supply chain information in different industries, let’s consider a few examples:
Aerospace Industry
In the aerospace industry, supply chain information is critical for ensuring the safety, reliability, and compliance of aircraft components. For example, consider a manufacturer of aircraft engines. They would capture the following supply chain information for each component:
Component | Supplier | Material | Manufacturing Process | Quality Control | Compliance |
---|---|---|---|---|---|
Turbine Blade | ABC Metals | Titanium Alloy | Precision Casting | Dimensional Inspection, NDT | AS9100 Certified |
Fuel Pump | XYZ Electronics | Various | Assembled in-house | Functional Testing, Leak Test | FAA Approved |
This information enables the manufacturer to trace the origin of each component, ensure compliance with aviation regulations, and quickly identify and address any quality issues that may arise.
Automotive Industry
In the automotive industry, supply chain information is essential for managing the complex network of suppliers and ensuring the timely delivery of high-quality components. For instance, consider an automotive OEM (Original Equipment Manufacturer) sourcing components for a new vehicle model:
Component | Supplier | Location | Lead Time | Logistics | Compliance |
---|---|---|---|---|---|
Airbag Module | Safety Systems Inc. | Mexico | 8 weeks | Ground Shipping | IATF 16949 Certified |
Infotainment System | Tech Electronics Co. | China | 12 weeks | Sea Freight | PPAP Approved |
By having this information readily available, the OEM can effectively plan production schedules, manage inventory levels, and ensure that all components meet the required quality and safety standards.
Medical Device Industry
In the medical device industry, supply chain information is vital for ensuring the safety, efficacy, and compliance of medical devices. Consider a manufacturer of pacemakers:
Component | Supplier | Material | Manufacturing Process | Quality Control | Compliance |
---|---|---|---|---|---|
Pacemaker Battery | Power Solutions Ltd. | Lithium-Ion | Clean Room Assembly | 100% Inspection, Accelerated Life Testing | ISO 13485 Certified |
Pacemaker Leads | MedWires Inc. | Platinum-Iridium | Extrusion, Insulation | Dimensional Inspection, Biocompatibility Testing | FDA Approved |
By maintaining detailed supply chain information, the manufacturer can ensure traceability, comply with regulatory requirements, and promptly address any potential issues related to the safety or performance of the pacemaker.
Frequently Asked Questions (FAQ)
-
What is the purpose of adding supply chain information to components?
The purpose of adding supply chain information to components is to improve traceability, enhance risk management, increase transparency, ensure compliance with regulations, and optimize inventory and logistics operations. -
What are the key elements of supply chain information that should be captured?
The key elements of supply chain information include supplier details, material sourcing, manufacturing process, quality control measures, logistics and transportation details, compliance and regulatory information, and pricing and contractual details. -
How can companies effectively implement supply chain information in product development?
To effectively implement supply chain information in product development, companies should establish a centralized database, collaborate with suppliers, integrate with existing systems, conduct regular audits and updates, train employees, and leverage data analytics. -
Why is supply chain information particularly important in regulated industries?
Supply chain information is crucial in regulated industries, such as aerospace, automotive, and medical devices, because it helps ensure compliance with stringent regulations, maintain product safety and quality, and facilitate prompt issue resolution. -
What are the benefits of using data analytics in supply chain information management?
Data analytics can help companies analyze supply chain information to identify trends, patterns, and potential risks. This enables data-driven decision-making and optimization of supply chain operations, leading to improved efficiency, cost savings, and risk mitigation.
Conclusion
In today’s complex and dynamic business environment, incorporating supply chain information into component data is no longer optional—it is a necessity. By capturing and managing detailed information about suppliers, materials, manufacturing processes, quality control, logistics, and compliance, companies can enhance traceability, mitigate risks, ensure regulatory compliance, and optimize their supply chain operations.
Implementing supply chain information in product development requires a systematic approach, including establishing a centralized database, collaborating with suppliers, integrating with existing systems, conducting regular audits, and leveraging data analytics. By following these best practices and adapting them to their specific industry requirements, companies can unlock the full potential of supply chain information and gain a competitive edge in the market.
As the business landscape continues to evolve, the importance of supply chain information will only continue to grow. Companies that prioritize the integration of supply chain data into their product development processes will be well-positioned to navigate the challenges and opportunities of the future, ensuring the delivery of high-quality, compliant, and sustainable products to their customers.
Leave a Reply