What is Fabrication Tolerance?
Fabrication tolerance refers to the acceptable range of deviation from the specified dimensions, shapes, or positions in a manufactured product. It is a crucial aspect of product design and manufacturing, as it ensures that the final product meets the desired quality standards and functions as intended. Fabrication tolerance is expressed as a plus or minus value, indicating the allowable variation from the nominal dimension.
Types of Fabrication Tolerances
There are several types of fabrication tolerances that designers and manufacturers need to consider:
-
Dimensional Tolerance: This refers to the acceptable variation in the linear dimensions of a part, such as length, width, height, or diameter.
-
Geometric Tolerance: This type of tolerance specifies the allowable deviation in the shape, orientation, or location of a feature, such as flatness, perpendicularity, or concentricity.
-
Positional Tolerance: This tolerance defines the acceptable variation in the position of a feature relative to another feature or datum.
-
Surface Finish Tolerance: This refers to the allowable roughness or smoothness of a surface, which can affect the part’s appearance, friction, and wear properties.
Why is Fabrication Tolerance Important?
Fabrication tolerance is essential for several reasons:
-
Functionality: Proper tolerances ensure that the manufactured parts fit together and function as intended. If the tolerances are too tight, the parts may not fit together, while if they are too loose, the product may not perform optimally.
-
Interchangeability: Consistent tolerances allow for the interchangeability of parts, which is crucial for mass production and easy replacement of worn or damaged components.
-
Cost: Tighter tolerances generally require more precise manufacturing processes, which can increase production costs. By specifying appropriate tolerances, designers can balance the need for accuracy with the cost of manufacturing.
-
Quality: Adherence to fabrication tolerances contributes to the overall quality of the product, ensuring that it meets the required specifications and customer expectations.
How to Specify Fabrication Tolerances
When creating manufacturer deliverables, it is essential to clearly communicate the required fabrication tolerances. Here are some steps to follow:
1. Determine the Critical Dimensions
Identify the dimensions, shapes, and positions that are critical to the function and performance of the product. These are the features that will require specific tolerances.
2. Consider the Manufacturing Process
Different manufacturing processes have varying capabilities in terms of achievable tolerances. Consider the limitations and advantages of the chosen manufacturing method when specifying tolerances.
Manufacturing Process | Typical Tolerance Range |
---|---|
Casting | ±0.5 to ±2.0 mm |
Forging | ±0.2 to ±1.0 mm |
Machining | ±0.01 to ±0.1 mm |
Injection Molding | ±0.05 to ±0.5 mm |
3D Printing | ±0.1 to ±0.5 mm |
3. Use Standard Tolerance Grades
Whenever possible, use standard tolerance grades, such as those specified by ISO (International Organization for Standardization) or ANSI (American National Standards Institute). These standards provide a consistent way of expressing tolerances and are widely understood by manufacturers.
4. Specify Tolerances on Drawings
Include the fabrication tolerances on the technical drawings or CAD models provided to the manufacturer. Use appropriate symbols and notation to clearly communicate the tolerances, such as:
- ±0.1 for dimensional tolerances
- ⌀0.05 for diameter tolerances
- 0.1 A for geometric tolerances (where A is the datum reference)
5. Provide a Tolerance Stack-Up Analysis
In complex assemblies, the individual component tolerances can accumulate, affecting the overall fit and function of the product. Perform a tolerance stack-up analysis to ensure that the cumulative tolerances are within acceptable limits.
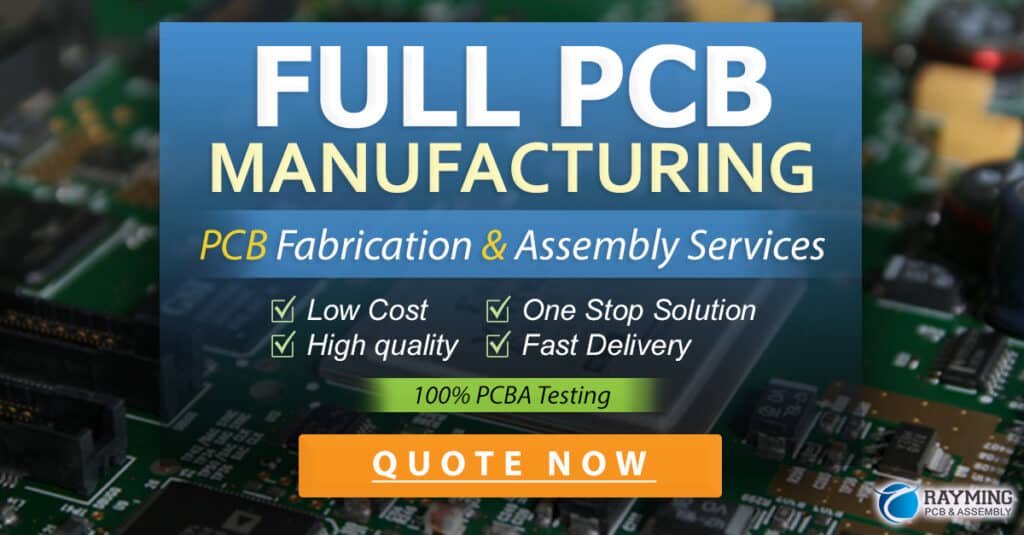
Best Practices for Fabrication Tolerance Design
To optimize the use of fabrication tolerances in your designs, consider the following best practices:
-
Avoid Over-Tolerancing: Specifying unnecessarily tight tolerances can increase manufacturing costs and lead times. Be pragmatic and assign tolerances based on the functional requirements of the product.
-
Use Geometric Dimensioning and Tolerancing (GD&T): GD&T is a symbolic language that defines the geometry of parts and assemblies, including tolerances. It provides a clear and consistent way to communicate design intent to manufacturers.
-
Collaborate with Manufacturers: Engage with manufacturers early in the design process to discuss tolerances and manufacturing capabilities. Their expertise can help optimize the design for manufacturability and cost-effectiveness.
-
Conduct Tolerance Analysis: Use tolerance analysis tools, such as statistical tolerance stacks or Monte Carlo simulations, to predict the effect of tolerances on the final product. This helps identify potential issues and optimize the design.
-
Consider Assembly Sequence: The order in which components are assembled can influence the accumulation of tolerances. Design the assembly sequence to minimize the impact of tolerance stack-up on critical dimensions.
FAQ
-
What is the difference between tolerance and allowance?
Tolerance refers to the acceptable range of deviation from a specified dimension, while allowance is an intentional difference between mating parts to accommodate factors such as thermal expansion or lubrication. -
How do I choose the appropriate tolerance for my product?
The choice of tolerance depends on factors such as the product’s function, the manufacturing process, the materials used, and the cost constraints. Consult with manufacturers and refer to industry standards to determine suitable tolerances. -
Can I use different tolerances for different dimensions of the same part?
Yes, it is common to specify different tolerances for different dimensions based on their criticality to the part’s function. This allows for a balance between accuracy and manufacturing feasibility. -
What happens if the manufactured parts exceed the specified tolerances?
If the parts do not meet the specified tolerances, they may not fit together properly or function as intended. In such cases, the parts may need to be reworked or rejected, leading to additional costs and delays. -
How can I ensure that my manufacturer understands and follows the specified tolerances?
Clearly communicate the tolerances in the technical drawings and documentation provided to the manufacturer. Use standard notation and symbols, and discuss the tolerances with the manufacturer to ensure a common understanding. Regular quality control checks can help verify adherence to the specified tolerances.
Conclusion
Fabrication tolerance is a critical aspect of product design and manufacturing, ensuring that parts fit together and function as intended. By understanding the types of tolerances, their importance, and how to specify them in manufacturer deliverables, designers can create products that meet quality standards and customer expectations.
To effectively incorporate fabrication tolerances into your designs, consider the manufacturing process, use standard tolerance grades, and clearly communicate the tolerances on drawings. Collaborate with manufacturers, conduct tolerance analyses, and optimize the assembly sequence to minimize the impact of tolerances on the final product.
By following best practices and engaging with manufacturers throughout the design process, you can successfully add fabrication tolerance options to your deliverables, resulting in high-quality, reliable products that meet the desired specifications.
Leave a Reply