Introduction to Heavy Copper PCBs
Heavy copper PCBs, also known as thick copper PCBs, are printed circuit boards that feature copper traces and planes significantly thicker than those found in standard PCBs. These boards are designed to handle high currents, provide better heat dissipation, and offer increased mechanical stability. Heavy copper PCBs are essential for applications that require high power handling capabilities, such as power electronics, automotive systems, and industrial equipment.
Understanding Copper Thickness in PCBs
Copper thickness in PCBs is typically measured in ounces per square foot (oz/ft²). One ounce of copper per square foot translates to a thickness of approximately 35 microns or 1.4 mils. Standard PCBs usually have copper thicknesses ranging from 0.5 oz/ft² to 2 oz/ft², while heavy copper PCBs can have copper thicknesses ranging from 3 oz/ft² to 20 oz/ft² or more.
Copper Weight (oz/ft²) | Thickness (microns) | Thickness (mils) |
---|---|---|
0.5 | 17.5 | 0.7 |
1 | 35 | 1.4 |
2 | 70 | 2.8 |
3 | 105 | 4.2 |
4 | 140 | 5.6 |
6 | 210 | 8.4 |
8 | 280 | 11.2 |
10 | 350 | 14.0 |
12 | 420 | 16.8 |
16 | 560 | 22.4 |
20 | 700 | 28.0 |
Benefits of Heavy Copper PCBs
1. High Current Carrying Capacity
One of the primary benefits of heavy copper PCBs is their ability to handle high currents. As the copper thickness increases, the current carrying capacity of the PCB also increases. This is particularly important in power electronics applications, where high currents are common. By using heavy copper PCBs, designers can ensure that their circuits can handle the required current without overheating or experiencing voltage drops.
2. Improved Heat Dissipation
Thick copper traces and planes in heavy copper PCBs provide better heat dissipation compared to standard PCBs. The increased copper mass helps to spread heat more efficiently, reducing the risk of thermal damage to components and improving the overall reliability of the circuit. This is especially crucial in high-power applications where heat generation is a significant concern.
3. Enhanced Mechanical Stability
Heavy copper PCBs offer increased mechanical stability due to the thicker copper layers. This makes them more resistant to vibration, shock, and other mechanical stresses. The enhanced mechanical stability is particularly beneficial in automotive, aerospace, and industrial applications where the PCBs are subjected to harsh environmental conditions.
4. Reduced Resistance and Voltage Drop
The thicker copper traces in heavy copper PCBs result in lower resistance and reduced voltage drop across the circuit. This is essential for maintaining signal integrity and ensuring that power is delivered efficiently to the connected components. By minimizing voltage drop, heavy copper PCBs can help improve the overall performance and efficiency of the system.
Applications of Heavy Copper PCBs
Power Electronics
Heavy copper PCBs are widely used in power electronics applications, such as power supplies, inverters, and motor drives. These applications require high current handling capabilities and efficient heat dissipation, making heavy copper PCBs an ideal choice. The thick copper layers enable the PCBs to handle the high currents without experiencing thermal issues or compromising the reliability of the circuit.
Automotive Systems
In the automotive industry, heavy copper PCBs are used in various systems, including engine control units (ECUs), power distribution modules, and battery management systems. These PCBs must withstand harsh environmental conditions, such as extreme temperatures, vibrations, and exposure to chemicals. The increased mechanical stability and heat dissipation properties of heavy copper PCBs make them suitable for these demanding automotive applications.
Industrial Equipment
Industrial equipment, such as welding machines, CNC machines, and robotics, often require PCBs that can handle high currents and dissipate heat efficiently. Heavy copper PCBs are commonly used in these applications to ensure reliable operation and long-term durability. The thick copper layers provide the necessary current carrying capacity and thermal management properties to meet the demands of industrial environments.
Renewable Energy Systems
Heavy copper PCBs are also used in renewable energy systems, such as solar inverters and wind turbine controllers. These applications involve high power handling and exposure to outdoor conditions. The enhanced current carrying capacity and mechanical stability of heavy copper PCBs make them suitable for use in renewable energy systems, ensuring reliable operation and long service life.
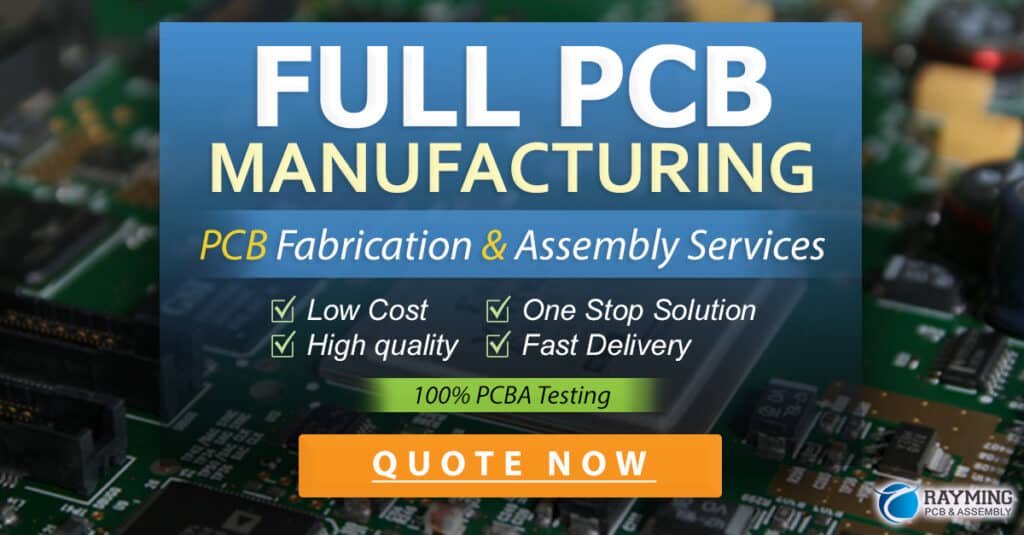
Thickest Copper PCBs Available
The thickest copper PCBs available in the market can have copper thicknesses of 20 oz/ft² or more. Some manufacturers even offer custom solutions with copper thicknesses up to 200 oz/ft², which translates to a thickness of 7,000 microns or 280 mils. These ultra-thick copper PCBs are used in specialized applications that require extremely high current handling capabilities or exceptional heat dissipation properties.
However, it is important to note that as the copper thickness increases, the manufacturing process becomes more challenging and expensive. Thicker copper layers require specialized equipment and processes, such as multi-step plating, to ensure uniform copper distribution and proper adhesion to the substrate. Additionally, the increased copper thickness can impact the minimum feature sizes and spacing that can be achieved on the PCB.
Choosing the Right Heavy Copper PCB Manufacturer
When selecting a heavy copper PCB manufacturer, it is essential to consider several factors to ensure that you receive high-quality boards that meet your specific requirements. Some key considerations include:
-
Experience and Expertise
Look for a manufacturer with extensive experience in producing heavy copper PCBs. They should have a deep understanding of the unique challenges associated with manufacturing thick copper boards and have the necessary expertise to overcome these challenges. -
Manufacturing Capabilities
Ensure that the manufacturer has the equipment and processes in place to produce the specific copper thickness and feature sizes that your application requires. They should also have strict quality control measures to guarantee the consistency and reliability of the manufactured PCBs. -
Material Selection
Choose a manufacturer that offers a wide range of substrate materials and copper foil options. This will allow you to select the most suitable combination of materials for your specific application, taking into account factors such as thermal performance, dielectric properties, and cost. -
Lead Time and Pricing
Consider the manufacturer’s lead times and pricing structure. While heavy copper PCBs may be more expensive than standard PCBs due to the specialized manufacturing processes involved, it is important to find a manufacturer that offers competitive pricing without compromising on quality or lead times. -
Customer Support
Select a manufacturer that provides excellent customer support throughout the entire manufacturing process. They should be responsive to your inquiries, offer design assistance if needed, and provide timely updates on the status of your order.
FAQ
1. What is the difference between heavy copper PCBs and standard PCBs?
Heavy copper PCBs have significantly thicker copper layers compared to standard PCBs. While standard PCBs typically have copper thicknesses ranging from 0.5 oz/ft² to 2 oz/ft², heavy copper PCBs can have copper thicknesses of 3 oz/ft² or more, up to 20 oz/ft² or even higher in some specialized applications.
2. What are the main benefits of using heavy copper PCBs?
The main benefits of using heavy copper PCBs include:
– High current carrying capacity
– Improved heat dissipation
– Enhanced mechanical stability
– Reduced resistance and voltage drop
These properties make heavy copper PCBs suitable for applications that require high power handling, reliable operation in harsh environments, and efficient thermal management.
3. What industries commonly use heavy copper PCBs?
Heavy copper PCBs are commonly used in industries such as:
– Power electronics
– Automotive
– Industrial equipment
– Renewable energy
These industries often require PCBs that can handle high currents, dissipate heat efficiently, and withstand demanding environmental conditions.
4. Can heavy copper PCBs be manufactured with the same feature sizes as standard PCBs?
As the copper thickness increases, it becomes more challenging to achieve the same minimum feature sizes and spacing as standard PCBs. The thicker copper layers may require adjustments to the design and manufacturing process to ensure proper etching and plating of the features. However, experienced heavy copper PCB manufacturers can typically accommodate most design requirements.
5. How do I choose the right copper thickness for my application?
The choice of copper thickness depends on several factors, including the required current carrying capacity, heat dissipation needs, mechanical stability requirements, and cost considerations. It is essential to work closely with your PCB manufacturer to determine the optimal copper thickness for your specific application. They can provide guidance based on their experience and expertise in manufacturing heavy copper PCBs.
Conclusion
Heavy copper PCBs offer numerous benefits over standard PCBs, including high current carrying capacity, improved heat dissipation, enhanced mechanical stability, and reduced resistance and voltage drop. These properties make them essential for applications in power electronics, automotive systems, industrial equipment, and renewable energy.
When considering the use of heavy copper PCBs, it is crucial to understand the specific requirements of your application and choose a copper thickness that balances performance, manufacturability, and cost. Working with an experienced heavy copper PCB manufacturer can help ensure that you receive high-quality boards that meet your unique needs.
As technology advances and the demand for high-power electronics continues to grow, the importance of heavy copper PCBs will only increase. By staying informed about the latest developments in heavy copper PCB manufacturing and partnering with reliable manufacturers, engineers and designers can create innovative solutions that push the boundaries of performance and reliability in their respective industries.
Leave a Reply