The Role of Embedded PCBs in Modern Electronics
Embedded PCBs play a crucial role in the functionality and performance of modern electronic devices. They are responsible for interconnecting various components, such as microprocessors, memory chips, sensors, and communication modules, enabling them to work together seamlessly. The compact and efficient design of embedded PCBs allows for the development of smaller, more powerful, and energy-efficient devices.
Key Characteristics of Embedded PCBs
-
Customization: Embedded PCBs are designed to meet the specific requirements of the device they are intended for, taking into account factors such as size constraints, power consumption, and environmental conditions.
-
Miniaturization: With the increasing demand for smaller and more portable electronic devices, embedded PCBs are designed to be as compact as possible while maintaining optimal performance.
-
Reliability: Embedded PCBs must be highly reliable, as they are often used in critical applications where failure is not an option. They undergo rigorous testing and quality control processes to ensure their durability and longevity.
-
Cost-effectiveness: By integrating multiple functions onto a single PCB, embedded PCBs help reduce the overall cost of the device, as well as simplify the manufacturing process.
Applications of Embedded PCBs
Embedded PCBs find applications in a wide range of industries and devices, including:
- Consumer Electronics: Smartphones, tablets, wearables, and smart home devices.
- Automotive Industry: In-vehicle infotainment systems, advanced driver assistance systems (ADAS), and engine control units (ECUs).
- Industrial Automation: Programmable logic controllers (PLCs), human-machine interfaces (HMIs), and industrial IoT devices.
- Medical Devices: Wearable health monitors, implantable devices, and diagnostic equipment.
- Aerospace and Defense: Avionics systems, satellite communication devices, and military-grade electronics.
Industry | Applications |
---|---|
Consumer Electronics | Smartphones, tablets, wearables, smart home devices |
Automotive | Infotainment systems, ADAS, ECUs |
Industrial Automation | PLCs, HMIs, industrial IoT devices |
Medical Devices | Wearable health monitors, implantable devices, diagnostic equipment |
Aerospace and Defense | Avionics systems, satellite communication devices, military-grade electronics |
Designing and Manufacturing Embedded PCBs
The design and manufacturing process of embedded PCBs involves several key steps:
1. Schematic Design
The first step in creating an embedded PCB is to develop a schematic diagram that outlines the electrical connections between the various components. This diagram serves as a blueprint for the PCB layout and helps ensure that the circuit functions as intended.
2. PCB Layout
Once the schematic is finalized, the next step is to create the physical layout of the PCB. This involves determining the optimal placement of components, routing the traces that connect them, and ensuring that the design meets the required specifications, such as size constraints and signal integrity.
3. Fabrication
After the PCB layout is complete, the design files are sent to a PCB fabrication facility. Here, the PCB is manufactured using a multi-step process that includes:
- Printing the circuit pattern onto copper-clad laminate sheets
- Etching away the unwanted copper to create the desired traces
- Drilling holes for through-hole components and vias
- Applying solder mask and silkscreen layers for protection and labeling
4. Assembly
Once the PCB is fabricated, the components are mounted onto the board using various techniques, such as surface-mount technology (SMT) or through-hole mounting. This process can be done manually or using automated assembly lines, depending on the complexity of the board and the production volume.
5. Testing and Quality Control
Before the embedded PCB is integrated into the final device, it undergoes thorough testing to ensure that it functions as intended and meets the required quality standards. This may include visual inspections, electrical tests, and environmental stress tests to validate the board’s performance and reliability.
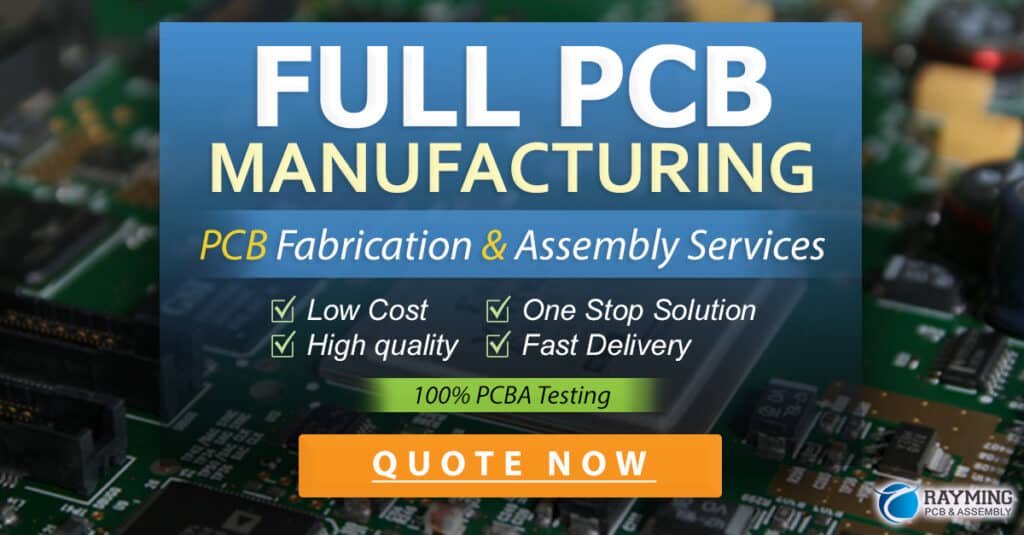
Challenges in Embedded PCB Design and Manufacturing
Designing and manufacturing embedded PCBs comes with its own set of challenges, including:
-
Miniaturization: As devices become smaller and more compact, designing embedded PCBs that fit within the available space while maintaining optimal performance becomes increasingly difficult.
-
Signal Integrity: With higher clock speeds and more complex circuits, maintaining signal integrity is crucial to ensure the proper functioning of the device. This requires careful consideration of factors such as trace routing, impedance matching, and electromagnetic interference (EMI) shielding.
-
Thermal Management: Embedded PCBs often operate in confined spaces with limited airflow, making thermal management a significant challenge. Designers must employ various techniques, such as using high-thermal-conductivity materials, incorporating heat sinks, and optimizing component placement, to ensure that the board operates within its thermal limits.
-
Cost Optimization: Balancing the need for high-quality, reliable embedded PCBs with the pressure to reduce costs is an ongoing challenge for manufacturers. This requires careful selection of materials, optimized design for manufacturing (DFM), and efficient production processes.
The Future of Embedded PCBs
As technology continues to advance, the future of embedded PCBs looks promising:
-
Increased Integration: With the advent of system-on-chip (SoC) and package-on-package (PoP) technologies, embedded PCBs will become even more integrated, allowing for more complex functions to be performed on a single board.
-
Flexible and Stretchable PCBs: The development of flexible and stretchable PCBs will enable the creation of wearable devices and other applications that require conformable electronics.
-
Advanced Materials: The use of advanced materials, such as high-frequency laminates and low-loss dielectrics, will enable embedded PCBs to operate at higher speeds and frequencies, opening up new possibilities for high-performance applications.
-
Additive Manufacturing: The adoption of additive manufacturing techniques, such as 3D printing, will allow for the rapid prototyping and production of embedded PCBs with complex geometries and unique features.
Frequently Asked Questions (FAQ)
-
Q: What is the difference between an embedded PCB and a standard PCB?
A: Embedded PCBs are custom-designed to fit within a specific device or system, while standard PCBs are general-purpose boards that can be used in a variety of applications. Embedded PCBs are often smaller, more complex, and designed to meet the unique requirements of the device they are intended for. -
Q: What are the benefits of using embedded PCBs?
A: Embedded PCBs offer several benefits, including improved device performance, reduced size and weight, increased reliability, and lower overall costs. By integrating multiple functions onto a single board, embedded PCBs simplify the design and manufacturing process, leading to more efficient and cost-effective devices. -
Q: What industries commonly use embedded PCBs?
A: Embedded PCBs are used in a wide range of industries, including consumer electronics, automotive, industrial automation, medical devices, and aerospace and defense. They are essential components in devices such as smartphones, in-vehicle infotainment systems, programmable logic controllers, wearable health monitors, and avionics systems. -
Q: What are some of the challenges in designing and manufacturing embedded PCBs?
A: Some of the main challenges include miniaturization, maintaining signal integrity, thermal management, and cost optimization. Designers must balance the need for high-performance, reliable boards with the constraints of limited space, power consumption, and budget. -
Q: What does the future hold for embedded PCBs?
A: The future of embedded PCBs is expected to involve increased integration, the development of flexible and stretchable PCBs, the use of advanced materials, and the adoption of additive manufacturing techniques. These advancements will enable the creation of even smaller, more powerful, and more versatile electronic devices.
Leave a Reply