Understanding the Concept of Stub Resonance in PCBs
Before we explore back drilling, it is essential to understand the concept of stub resonance in PCBs. In multi-layer PCBs, signal vias are used to connect traces on different layers. However, these vias often extend beyond the target layer, creating an unused portion known as a stub. At high frequencies, these stubs can act as resonators, leading to signal reflections and distortions that can compromise signal integrity.
The Impact of Stub Resonance on Signal Integrity
Stub resonance can have a significant impact on signal integrity in high-speed PCBs. Some of the key effects include:
- Signal Reflections: Stubs can cause signal reflections, leading to signal distortions and reduced signal quality.
- Increased Crosstalk: Stub resonance can increase crosstalk between adjacent vias, further degrading signal integrity.
- Impedance Mismatches: Stubs can create impedance mismatches, resulting in signal reflections and reduced signal quality.
- Reduced Bandwidth: Stub resonance can limit the usable bandwidth of high-speed signals, affecting the overall performance of the system.
What is Back Drilling?
Back drilling is a process used to remove the unused portion of a via (stub) in multi-layer PCBs. By eliminating the stub, back drilling helps to minimize the effects of stub resonance and improve signal integrity in high-speed applications.
The Back Drilling Process
The back drilling process involves the following steps:
- Identifying the target vias: The first step is to identify the vias that require back drilling based on the PCB design and the desired signal integrity performance.
- Drilling from the back side: A specialized drill is used to remove the unwanted portion of the via from the back side of the PCB, leaving only the necessary length of the via to connect the target layers.
- Cleaning the drilled holes: After drilling, the holes are cleaned to remove any debris and ensure a clean, smooth surface.
- Filling the drilled holes (optional): In some cases, the drilled holes may be filled with a non-conductive material to provide additional support and protection to the via.
Advantages of Back Drilling
Back drilling offers several advantages in PCB design and manufacturing:
- Improved Signal Integrity: By removing the unused portion of the via, back drilling helps to minimize stub resonance and improve signal integrity in high-speed applications.
- Increased Bandwidth: Back drilling can help to increase the usable bandwidth of high-speed signals, enabling faster data transmission rates.
- Reduced Crosstalk: By minimizing stub resonance, back drilling can help to reduce crosstalk between adjacent vias, further improving signal integrity.
- Enhanced Reliability: Back drilling can contribute to the overall reliability of the PCB by reducing signal distortions and ensuring consistent performance over time.
Implementing Back Drilling in PCB Design
To effectively implement back drilling in PCB design, several factors must be considered:
Identifying Vias for Back Drilling
Not all vias in a PCB design require back drilling. Designers must carefully evaluate the signal integrity requirements and identify the specific vias that would benefit from the back drilling process. Factors to consider include:
- Signal Speed: Back drilling is primarily used for high-speed signals where stub resonance can have a significant impact on signal integrity.
- Via Length: Longer vias are more susceptible to stub resonance and are often prioritized for back drilling.
- Signal Criticality: Vias carrying critical signals, such as clock signals or high-speed data lines, are typically selected for back drilling to ensure optimal signal integrity.
Designing for Back Drilling
When designing a PCB with back drilling in mind, designers must consider several factors to ensure the process is effective and reliable:
- Via Placement: Vias should be strategically placed to minimize the overall number of vias required and to facilitate the back drilling process.
- Layer Stack-up: The PCB layer stack-up should be designed to minimize the stub length of vias and to ensure that back drilling can be performed effectively.
- Drill Sizes: The drill sizes used for vias must be carefully selected to ensure that back drilling can be performed accurately and reliably.
- Manufacturing Considerations: Designers must work closely with the PCB manufacturer to ensure that the back drilling process can be implemented effectively and efficiently.
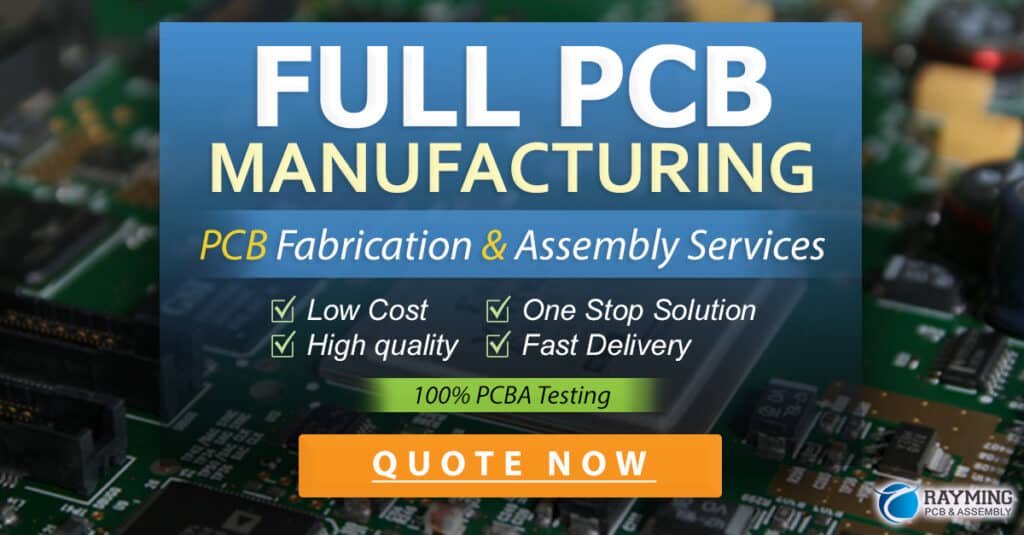
Back Drilling in PCB Manufacturing
The back drilling process is typically performed during the PCB manufacturing stage, after the initial drilling and plating of the vias. Specialized equipment and expertise are required to ensure that the process is performed accurately and reliably.
Equipment Used for Back Drilling
Back drilling requires specialized equipment to ensure precise and accurate removal of the unwanted portion of the via. Some of the key equipment used in the process includes:
- High-Speed Drilling Machines: Back drilling is typically performed using high-speed drilling machines that can accurately drill the small, precise holes required for the process.
- Depth-Controlled Drills: Depth-controlled drills are used to ensure that the back drilling process removes only the unwanted portion of the via, leaving the necessary length intact.
- Cleaning Equipment: Specialized cleaning equipment is used to remove any debris from the drilled holes and ensure a clean, smooth surface.
Quality Control in Back Drilling
Quality control is critical in the back drilling process to ensure that the vias are drilled accurately and consistently. Some of the key quality control measures include:
- Visual Inspection: Visual inspection is performed to ensure that the drilled holes are clean, smooth, and free of any debris.
- Electrical Testing: Electrical testing is performed to verify that the back drilled vias maintain the required electrical performance and signal integrity.
- Cross-Sectional Analysis: Cross-sectional analysis may be performed to verify that the back drilling process has removed the unwanted portion of the via accurately and completely.
Alternatives to Back Drilling
While back drilling is a highly effective method for improving signal integrity in high-speed PCBs, there are alternative approaches that can be used in certain situations:
Blind and Buried Vias
Blind and buried vias are types of vias that do not extend through the entire thickness of the PCB. By using blind and buried vias, designers can minimize the stub length and reduce the impact of stub resonance without the need for back drilling.
Via-in-Pad Design
Via-in-pad design is a technique where the via is placed directly in the pad of a component. This approach can help to minimize the overall via length and reduce the impact of stub resonance. However, via-in-pad design requires careful planning and may not be suitable for all applications.
High-Speed PCB Material Selection
The choice of PCB material can also play a role in minimizing the impact of stub resonance. High-speed PCB materials, such as low-loss dielectrics and ultra-low-loss laminates, can help to reduce signal distortions and improve overall signal integrity, potentially reducing the need for back drilling in some cases.
Frequently Asked Questions (FAQ)
-
What is stub resonance in PCBs?
Stub resonance occurs when the unused portion of a via (stub) acts as a resonator at high frequencies, causing signal reflections and distortions that can compromise signal integrity. -
How does back drilling help to improve signal integrity?
Back drilling removes the unused portion of a via, minimizing the effects of stub resonance and improving signal integrity in high-speed applications. -
Is back drilling required for all vias in a PCB?
No, not all vias require back drilling. Designers must carefully evaluate the signal integrity requirements and identify the specific vias that would benefit from the back drilling process. -
What equipment is used for back drilling in PCB manufacturing?
Back drilling typically requires high-speed drilling machines, depth-controlled drills, and specialized cleaning equipment to ensure precise and accurate removal of the unwanted portion of the via. -
Are there alternatives to back drilling for improving signal integrity?
Yes, alternatives to back drilling include using blind and buried vias, via-in-pad design, and selecting high-speed PCB materials that can help to minimize the impact of stub resonance.
Conclusion
Back drilling is a critical process in the design and manufacturing of high-speed PCBs, helping to minimize signal integrity issues caused by stub resonance. By removing the unused portion of a via, back drilling can improve signal integrity, increase bandwidth, reduce crosstalk, and enhance the overall reliability of the PCB.
To effectively implement back drilling, designers must carefully evaluate the signal integrity requirements, identify the specific vias that require back drilling, and design the PCB with manufacturing considerations in mind. PCB manufacturers must have the necessary equipment, expertise, and quality control measures in place to ensure that the back drilling process is performed accurately and reliably.
While back drilling is a highly effective approach, alternative methods such as blind and buried vias, via-in-pad design, and high-speed PCB material selection can also be used to improve signal integrity in certain situations.
As the demand for high-speed electronic devices continues to grow, the importance of back drilling in PCB design and manufacturing will only increase. By understanding the principles and best practices of back drilling, designers and manufacturers can work together to create high-performance PCBs that meet the ever-increasing demands of modern electronic systems.
Leave a Reply