Understanding High Voltage PCBs
What Constitutes a High Voltage PCB?
A high voltage PCB is a printed circuit board that is specifically designed to withstand and operate at higher voltage levels compared to standard PCBs. The exact voltage threshold that defines a high voltage PCB can vary depending on the industry and application. However, PCBs that handle voltages above 50V are generally considered high voltage boards.
Key Characteristics of High Voltage PCBs
High voltage PCBs possess several distinct characteristics that set them apart from standard PCBs:
-
Increased Dielectric Strength: The dielectric material used in high voltage PCBs has a higher dielectric strength, which is the ability to withstand high electric fields without breaking down. This property ensures that the PCB can handle the high voltages without causing short circuits or damage to the board.
-
Thicker Copper Traces: To accommodate the higher currents associated with high voltages, high voltage PCBs often feature thicker copper traces compared to standard PCBs. The increased trace width and thickness help prevent excessive heating and ensure the reliable flow of electrical current.
-
Larger Clearances and Creepage Distances: High voltage PCBs require larger clearances (the shortest distance through air) and creepage distances (the shortest distance along the surface) between conductors to prevent arcing and maintain proper insulation. These increased distances help mitigate the risk of electrical breakdown and ensure the safety and reliability of the PCB.
-
Specialized Materials: High voltage PCBs may utilize specialized substrate materials, such as ceramic or polyimide, that offer superior thermal and electrical properties. These materials provide enhanced insulation, heat dissipation, and mechanical stability to withstand the demanding conditions of high voltage applications.
Designing High Voltage PCBs
Design Considerations for High Voltage PCBs
Designing high voltage PCBs requires careful consideration of several key factors to ensure optimal performance and safety:
-
Voltage and Current Requirements: The first step in designing a high voltage PCB is to determine the voltage and current levels that the board needs to handle. This information guides the selection of appropriate materials, trace widths, and clearances.
-
Insulation and Spacing: Adequate insulation and spacing between conductors are crucial in high voltage PCB design. Designers must adhere to industry standards and guidelines, such as the IPC-2221 standard, which provides recommendations for minimum clearances and creepage distances based on the voltage levels and environmental conditions.
-
Trace Routing and Placement: Proper trace routing and component placement are essential to minimize electromagnetic interference (EMI) and ensure the reliable operation of the high voltage PCB. Traces should be routed to minimize crosstalk and avoid sharp bends or narrow necks that can create high electric field concentrations.
-
Thermal Management: High voltage PCBs often generate significant heat due to the high power dissipation. Effective thermal management techniques, such as the use of heat sinks, thermal vias, and proper component placement, are necessary to prevent overheating and ensure the longevity of the PCB.
-
Safety Features: Incorporating safety features, such as fuses, circuit breakers, and discharge resistors, is crucial in high voltage PCB design. These components protect the board and connected devices from overvoltage, overcurrent, and electrostatic discharge (ESD) events.
High Voltage PCB Layout Guidelines
When laying out a high voltage PCB, designers should follow these guidelines to ensure optimal performance and safety:
-
Maximize Clearances and Creepage Distances: Maintain sufficient clearances and creepage distances between conductors, as per industry standards, to prevent arcing and maintain proper insulation.
-
Avoid Sharp Edges and Corners: Minimize sharp edges and corners in the PCB layout, as they can create high electric field concentrations and increase the risk of electrical breakdown.
-
Use Rounded Traces: Employ rounded traces instead of sharp bends to reduce electric field concentrations and improve the overall reliability of the high voltage PCB.
-
Separate High and Low Voltage Regions: Clearly separate the high voltage and low voltage regions of the PCB to prevent unintended interactions and ensure the safety of the board and connected devices.
-
Implement Proper Grounding: Establish a robust grounding scheme to provide a low-impedance path for fault currents and minimize the risk of electrical shock.
Manufacturing High Voltage PCBs
Material Selection for High Voltage PCBs
The choice of materials is critical in the manufacturing of high voltage PCBs. The substrate material should have high dielectric strength, low dissipation factor, and good thermal stability. Some commonly used materials for high voltage PCBs include:
-
FR-4: FR-4 is a popular choice for high voltage PCBs due to its good dielectric properties, mechanical strength, and cost-effectiveness. However, it may not be suitable for extremely high voltage applications.
-
Polyimide: Polyimide offers excellent dielectric strength, thermal stability, and mechanical properties, making it ideal for high voltage PCBs in demanding environments.
-
Ceramic: Ceramic substrates, such as alumina or beryllia, provide exceptional dielectric strength and thermal conductivity, making them suitable for high-power, high-voltage applications.
Manufacturing Processes for High Voltage PCBs
The manufacturing process for high voltage PCBs follows similar steps to standard PCB fabrication, with additional considerations for the specific requirements of high voltage applications:
-
Substrate Preparation: The chosen substrate material is cut to the desired size and shape, and any necessary holes or cutouts are made.
-
Copper Cladding: The substrate is then laminated with copper foil on one or both sides, depending on the PCB design.
-
Patterning: The copper layer is patterned using photolithography and etching processes to create the desired traces and pads.
-
Drilling: Holes are drilled through the PCB to accommodate through-hole components and vias.
-
Plating: The drilled holes are plated with copper to establish electrical connections between layers.
-
Solder Mask and Silkscreen: A solder mask is applied to protect the copper traces, and a silkscreen layer is added for component labeling and identification.
-
Surface Finishing: The exposed copper areas are coated with a surface finish, such as HASL (Hot Air Solder Leveling) or ENIG (Electroless Nickel Immersion Gold), to prevent oxidation and improve solderability.
-
Electrical Testing: The manufactured high voltage PCB undergoes rigorous electrical testing to ensure it meets the specified voltage and current requirements and to detect any potential defects or issues.
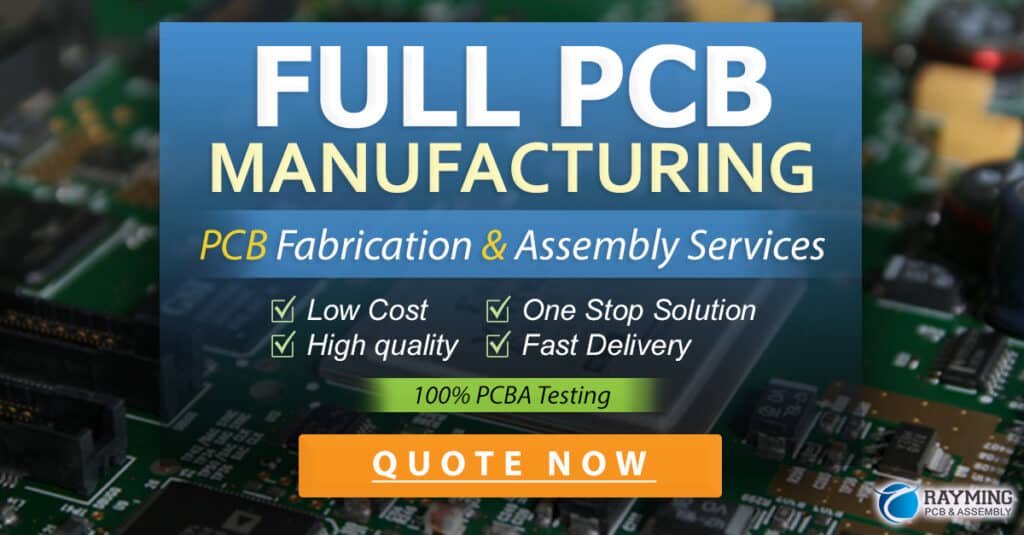
Applications of High Voltage PCBs
High voltage PCBs find applications in a wide range of industries and products, including:
-
Power Electronics: High voltage PCBs are used in power supplies, inverters, and converters for various applications, such as renewable energy systems, electric vehicles, and industrial equipment.
-
Medical Devices: Medical equipment, such as X-ray machines, defibrillators, and high-frequency surgical devices, relies on high voltage PCBs for their operation.
-
Aerospace and Defense: High voltage PCBs are employed in radar systems, avionics, and satellite communication equipment in the aerospace and defense sectors.
-
Industrial Automation: Industrial control systems, motor drives, and high-power LED lighting solutions utilize high voltage PCBs for reliable operation in demanding environments.
-
Consumer Electronics: Some consumer electronics products, such as televisions, monitors, and audio amplifiers, incorporate high voltage PCBs for power management and signal processing.
Frequently Asked Questions (FAQ)
-
What is the difference between a high voltage PCB and a standard PCB?
A high voltage PCB is designed to handle higher voltage levels compared to a standard PCB. It features increased dielectric strength, thicker copper traces, larger clearances and creepage distances, and specialized materials to ensure safe and reliable operation at high voltages. -
What voltage range is considered “high voltage” for PCBs?
The exact voltage threshold for a high voltage PCB can vary depending on the industry and application. However, PCBs that handle voltages above 50V are generally considered high voltage boards. -
What safety precautions should be taken when working with high voltage PCBs?
When working with high voltage PCBs, it is crucial to follow proper safety procedures, including: - Wearing appropriate personal protective equipment (PPE) such as insulated gloves and safety glasses.
- Ensuring the work area is clean, dry, and free from conductive materials.
- Using insulated tools and test equipment rated for the voltage levels being handled.
- Disconnecting power sources and discharging any stored energy before working on the PCB.
-
Following lockout/tagout procedures to prevent accidental energization of the circuit.
-
How do I select the appropriate materials for a high voltage PCB?
When selecting materials for a high voltage PCB, consider factors such as the required dielectric strength, thermal stability, and mechanical properties. Common materials include FR-4, polyimide, and ceramic substrates. Consult with your PCB manufacturer or material supplier to determine the most suitable option for your specific application. -
Can high voltage PCBs be multilayer boards?
Yes, high voltage PCBs can be designed as multilayer boards. However, special considerations must be taken to ensure proper insulation and spacing between layers, as well as the use of appropriate materials and manufacturing techniques to maintain the integrity of the high voltage design.
Conclusion
High voltage PCBs are essential components in a wide range of applications that require the handling of high electrical voltages and currents. These specialized boards feature unique characteristics, such as increased dielectric strength, thicker copper traces, and larger clearances and creepage distances, to ensure safe and reliable operation in demanding environments.
Designing and manufacturing high voltage PCBs requires careful consideration of factors such as voltage and current requirements, insulation and spacing, trace routing, thermal management, and safety features. By adhering to industry standards and guidelines, and selecting appropriate materials and manufacturing processes, designers and manufacturers can create high voltage PCBs that meet the specific needs of their applications.
As technology continues to advance, the demand for high voltage PCBs is expected to grow, driven by the increasing adoption of power electronics, renewable energy systems, and other applications that require the handling of high voltages. By understanding the principles and best practices of high voltage PCB design and manufacturing, engineers and technicians can develop innovative solutions that push the boundaries of electrical performance and reliability.
Characteristic | High Voltage PCB | Standard PCB |
---|---|---|
Voltage Range | Above 50V | Below 50V |
Dielectric Strength | High | Standard |
Copper Trace Thickness | Thicker | Standard |
Clearances and Creepage Distances | Larger | Standard |
Materials | Specialized (e.g., ceramic, polyimide) | Standard (e.g., FR-4) |
Table 1: Comparison of High Voltage PCBs and Standard PCBs
In conclusion, high voltage PCBs are crucial components that enable the safe and reliable operation of electrical systems in a variety of industries. By understanding their unique characteristics, design considerations, and manufacturing processes, engineers and technicians can develop high-performance solutions that meet the demanding requirements of high voltage applications.
Leave a Reply