Introduction to Kapton PCB
Kapton PCB, also known as polyimide PCB, is a type of printed circuit board that uses Kapton as the base material. Kapton is a polyimide film developed by DuPont that possesses excellent thermal, mechanical, and electrical properties. These properties make Kapton PCB an ideal choice for various applications, especially in harsh environments where conventional PCBs may fail.
Key Features of Kapton PCB
- High temperature resistance
- Excellent electrical insulation
- Good mechanical strength
- Lightweight and flexible
- Chemical resistance
Advantages of Kapton PCB
1. High Temperature Resistance
One of the most significant advantages of Kapton PCB is its ability to withstand high temperatures. Kapton has a continuous operating temperature range of -269°C to 400°C, making it suitable for applications that require exposure to extreme temperatures, such as aerospace, automotive, and industrial electronics.
Temperature Range | Suitability |
---|---|
-269°C to -200°C | Cryogenic applications |
-200°C to 0°C | Low-temperature electronics |
0°C to 200°C | Most electronic applications |
200°C to 400°C | High-temperature electronics |
2. Excellent Electrical Insulation
Kapton PCB offers excellent electrical insulation properties, with a dielectric strength of 7,700 volts per mil (0.001 inch) and a dielectric constant of 3.5. These properties make Kapton PCB an ideal choice for high-voltage applications and help prevent electrical leakage and short circuits.
3. Good Mechanical Strength
Despite its lightweight and flexible nature, Kapton PCB possesses good mechanical strength. It has a tensile strength of 231 MPa and a elongation at break of 72%, making it resistant to tears and punctures. This mechanical strength allows Kapton PCB to withstand vibrations and shocks, which is crucial in applications such as aerospace and automotive electronics.
4. Lightweight and Flexible
Kapton PCB is lighter and more flexible compared to conventional PCBs, making it an excellent choice for applications that require compact and lightweight designs. The flexibility of Kapton PCB allows it to conform to various shapes and curves, enabling its use in wearable electronics, flexible displays, and sensors.
5. Chemical Resistance
Kapton PCB exhibits excellent chemical resistance, making it suitable for applications that involve exposure to harsh chemicals, solvents, and oils. This property ensures the longevity and reliability of Kapton PCB in demanding environments, such as industrial settings and laboratories.
Applications of Kapton PCB
1. Aerospace Electronics
Kapton PCB is widely used in aerospace electronics due to its ability to withstand extreme temperatures, vibrations, and shocks. It is used in various applications, such as:
– Satellite electronics
– Aircraft avionics
– Space exploration equipment
2. Automotive Electronics
The automotive industry relies on Kapton PCB for its high-temperature resistance and mechanical strength. Some common applications include:
– Engine control units (ECUs)
– Transmission control modules
– Sensors and actuators
3. Industrial Electronics
Kapton PCB is used in industrial electronics that require operation in harsh environments, such as:
– Oil and gas exploration equipment
– Power generation systems
– Chemical processing plants
4. Medical Devices
The biocompatibility and chemical resistance of Kapton PCB make it suitable for use in medical devices, such as:
– Implantable devices
– Surgical instruments
– Medical sensors
5. Wearable Electronics
The lightweight and flexible nature of Kapton PCB enables its use in wearable electronics, such as:
– Smartwatches
– Fitness trackers
– Medical monitoring devices
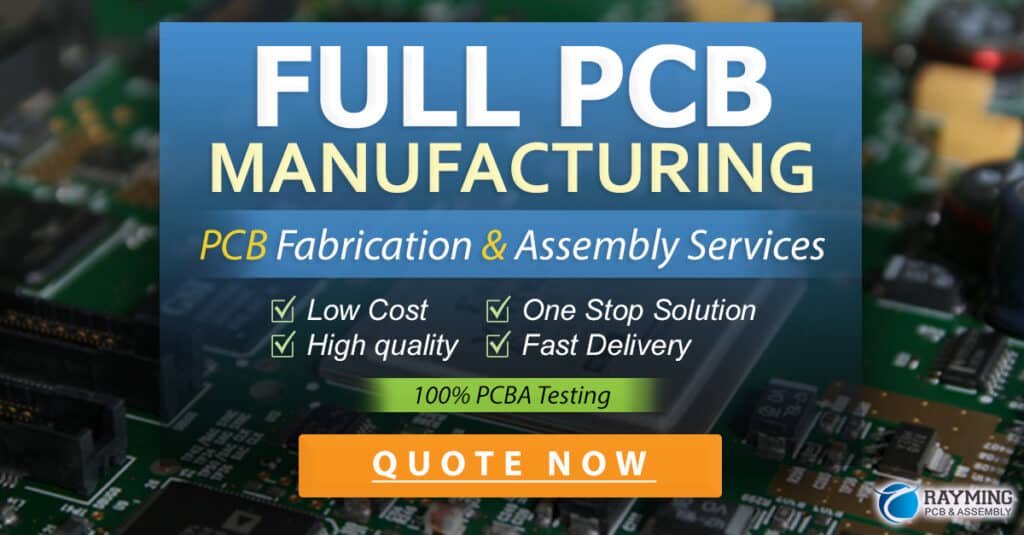
Kapton PCB Manufacturing Process
The manufacturing process of Kapton PCB is similar to that of conventional PCBs, with some additional considerations due to the unique properties of Kapton.
-
Substrate Preparation: The Kapton film is cut to the desired size and shape, and any necessary holes or slots are punched.
-
Copper Lamination: A thin layer of copper is laminated onto the Kapton substrate using heat and pressure. The copper layer can be applied on one or both sides of the substrate, depending on the PCB design.
-
Photoresist Application: A photoresist layer is applied onto the copper-laminated Kapton substrate. This layer is sensitive to UV light and will be used to transfer the PCB pattern onto the copper layer.
-
Exposure and Development: The photoresist-coated Kapton substrate is exposed to UV light through a photomask that contains the PCB pattern. The exposed areas of the photoresist become soluble and are removed during the development process, leaving the desired PCB pattern on the copper layer.
-
Etching: The exposed copper areas are etched away using a chemical solution, leaving only the copper traces that form the PCB pattern.
-
Photoresist Removal: The remaining photoresist layer is removed using a chemical stripper, revealing the final copper PCB pattern on the Kapton substrate.
-
Surface Finish: A surface finish, such as gold plating or solder mask, may be applied to the PCB to improve its durability, solderability, and aesthetic appearance.
-
Cutting and Drilling: The Kapton PCB panel is cut into individual boards, and any necessary holes or slots are drilled for component mounting and interconnections.
Designing with Kapton PCB
When designing with Kapton PCB, there are several factors to consider to ensure optimal performance and reliability:
-
Thermal Management: Although Kapton PCB can withstand high temperatures, it is essential to consider thermal management in the design to prevent overheating of components and ensure proper heat dissipation.
-
Flexible Design: When designing flexible Kapton PCBs, it is crucial to consider the bending radius, bend direction, and the placement of components to minimize stress on the board and ensure reliable operation.
-
Adhesion: Due to the smooth surface of Kapton, achieving good adhesion between the copper layer and the substrate can be challenging. Proper surface treatment and the use of suitable adhesives can help improve adhesion.
-
Impedance Control: Kapton PCB’s dielectric constant and thickness can affect the impedance of the traces. Careful design and simulation are necessary to ensure proper impedance control, especially in high-frequency applications.
-
Component Selection: When selecting components for Kapton PCB, it is essential to choose parts that can withstand the same environmental conditions as the board, such as high temperatures and chemical exposure.
Kapton PCB vs. Other PCB Materials
Kapton PCB offers several advantages over other PCB materials, such as FR-4 and polyester. However, it is essential to consider the specific requirements of the application when choosing the most suitable PCB material.
Property | Kapton PCB | FR-4 PCB | Polyester PCB |
---|---|---|---|
Temperature Resistance | -269°C to 400°C | 130°C (Tg) | -40°C to 150°C |
Dielectric Strength (kV/mm) | 154 | 20 | 50 |
Dielectric Constant (1 MHz) | 3.5 | 4.7 | 3.2 |
Tensile Strength (MPa) | 231 | 310 | 180 |
Flexibility | High | Low | High |
Future Trends in Kapton PCB
As technology advances and the demand for high-performance electronics in harsh environments continues to grow, Kapton PCB is expected to play an increasingly important role in various industries. Some future trends in Kapton PCB include:
-
Miniaturization: The development of thinner and more flexible Kapton films will enable the creation of smaller and more compact electronic devices.
-
High-Speed Applications: Advances in Kapton PCB manufacturing processes and materials will allow for the fabrication of high-speed circuits that can operate at higher frequencies and with lower signal losses.
-
Hybrid Materials: The combination of Kapton with other materials, such as ceramics or metal foils, will lead to the development of hybrid PCBs with enhanced properties and performance.
-
Additive Manufacturing: The adoption of additive manufacturing techniques, such as 3D printing, in Kapton PCB fabrication will enable the creation of complex and customized PCB designs with reduced lead times and costs.
Frequently Asked Questions (FAQ)
-
Q: What is the maximum operating temperature of Kapton PCB?
A: Kapton PCB has a continuous operating temperature range of -269°C to 400°C, making it suitable for high-temperature applications. -
Q: Can Kapton PCB be used in flexible electronics?
A: Yes, Kapton PCB is lightweight and flexible, making it an excellent choice for applications that require compact and flexible designs, such as wearable electronics and flexible displays. -
Q: Is Kapton PCB resistant to chemicals?
A: Kapton PCB exhibits excellent chemical resistance, making it suitable for applications that involve exposure to harsh chemicals, solvents, and oils. -
Q: How does Kapton PCB compare to FR-4 PCB in terms of temperature resistance?
A: Kapton PCB has a much higher temperature resistance (-269°C to 400°C) compared to FR-4 PCB, which has a glass transition temperature (Tg) of 130°C. -
Q: What are the key considerations when designing with Kapton PCB?
A: When designing with Kapton PCB, it is essential to consider factors such as thermal management, flexible design, adhesion, impedance control, and component selection to ensure optimal performance and reliability.
Conclusion
Kapton PCB is a high-performance printed circuit board material that offers excellent thermal, mechanical, and electrical properties. Its ability to withstand extreme temperatures, provide excellent electrical insulation, and resist chemicals makes it an ideal choice for various applications in harsh environments, such as aerospace, automotive, industrial, and medical electronics.
As technology advances and the demand for reliable electronics in challenging conditions continues to grow, Kapton PCB is expected to play an increasingly important role in shaping the future of electronic devices. By understanding the properties, manufacturing process, design considerations, and future trends of Kapton PCB, engineers and designers can leverage its unique capabilities to create innovative and reliable electronic solutions for a wide range of applications.
Leave a Reply