Table of Contents
- Introduction to PCB Insulation
- Types of PCB Insulation Materials
2.1. FR-4
2.2. Polyimide
2.3. PTFE (Teflon)
2.4. Ceramic
2.5. Other Insulation Materials - Properties of PCB Insulation Materials
3.1. Dielectric Constant
3.2. Dielectric Strength
3.3. Thermal Conductivity
3.4. Coefficient of Thermal Expansion (CTE)
3.5. Moisture Absorption - PCB Insulation Techniques
4.1. Solder Mask
4.2. Conformal Coating
4.3. Potting and Encapsulation
4.4. Layer Stacking and Separation - Applications of PCB Insulation
5.1. Consumer Electronics
5.2. Automotive Electronics
5.3. Medical Devices
5.4. Aerospace and Defense
5.5. Industrial Automation - Challenges in PCB Insulation
6.1. High-Frequency Applications
6.2. Miniaturization and High-Density PCBs
6.3. Harsh Environmental Conditions - Selecting the Right PCB Insulation Material
- PCB Insulation Testing and Quality Control
- Future Trends in PCB Insulation
- Frequently Asked Questions (FAQ)
- Conclusion
1. Introduction to PCB Insulation
PCB insulation is a fundamental aspect of PCB design and manufacturing that ensures the proper functioning and reliability of electronic devices. Its primary purpose is to prevent unwanted electrical interactions between conductive traces, components, and layers within a PCB. By isolating these elements, PCB insulation minimizes signal interference, crosstalk, and short circuits, thereby maintaining the integrity of the electronic signals.
In addition to its electrical insulation properties, PCB insulation also plays a crucial role in the mechanical and thermal stability of the PCB. The choice of insulation material and technique can significantly impact the PCB’s ability to withstand physical stress, vibrations, and temperature fluctuations.
As the electronics industry continues to evolve, with the growing demand for high-performance, miniaturized, and reliable electronic devices, the importance of effective PCB insulation has never been greater. In the following sections, we will explore the various types of PCB insulation materials, their properties, and their applications in different industries.
2. Types of PCB Insulation Materials
There are several types of insulation materials used in PCB manufacturing, each with its unique properties and advantages. The choice of insulation material depends on factors such as the intended application, environmental conditions, and performance requirements of the electronic device. Some of the most common PCB insulation materials include:
2.1. FR-4
FR-4 (Flame Retardant 4) is the most widely used insulation material in PCB manufacturing. It is a composite material made of woven fiberglass cloth impregnated with an epoxy resin binder. FR-4 offers good electrical insulation properties, mechanical strength, and thermal stability. It is also cost-effective and easy to manufacture, making it a popular choice for a wide range of electronic applications.
2.2. Polyimide
Polyimide is a high-performance polymer known for its excellent thermal stability, chemical resistance, and mechanical strength. It is often used in applications that require high-temperature operation or exposure to harsh environmental conditions. Polyimide PCBs are commonly found in aerospace, automotive, and military electronics.
2.3. PTFE (Teflon)
PTFE (Polytetrafluoroethylene), also known as Teflon, is a synthetic fluoropolymer with outstanding electrical insulation properties, low dielectric constant, and high thermal stability. PTFE PCBs are ideal for high-frequency applications, such as radar systems, wireless communications, and microwave devices, due to their low signal loss and low dielectric constant.
2.4. Ceramic
Ceramic PCBs are made of inorganic, non-metallic materials, such as alumina (Al2O3) or aluminum nitride (AlN). They offer excellent thermal conductivity, high dielectric strength, and low thermal expansion, making them suitable for high-power and high-temperature applications. Ceramic PCBs are commonly used in LED lighting, power electronics, and high-frequency devices.
2.5. Other Insulation Materials
In addition to the materials mentioned above, there are other insulation materials used in PCB manufacturing for specific applications or requirements. These include:
- CEM-1 and CEM-3 (Composite Epoxy Materials): Low-cost alternatives to FR-4 for less demanding applications.
- BT (Bismaleimide Triazine): A high-temperature alternative to FR-4 with better thermal stability and lower moisture absorption.
- Rogers materials (e.g., RO4000, RT/duroid): High-performance materials for high-frequency and microwave applications.
- Flexible materials (e.g., Kapton, PET): Used in flexible and rigid-flex PCBs for wearable electronics and compact devices.
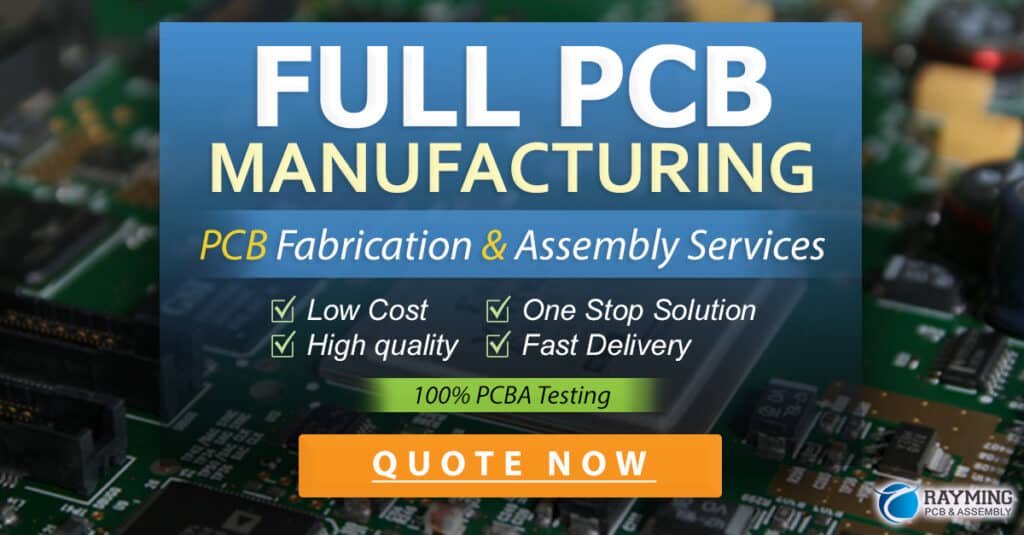
3. Properties of PCB Insulation Materials
To effectively insulate and protect the conductive elements within a PCB, insulation materials must possess specific electrical, thermal, and mechanical properties. These properties determine the material’s suitability for different applications and environmental conditions. Some of the key properties of PCB insulation materials include:
3.1. Dielectric Constant
The dielectric constant (Dk) is a measure of a material’s ability to store electrical energy in an electric field. A lower dielectric constant indicates better insulation properties and lower signal propagation delay. The dielectric constant of PCB insulation materials typically ranges from 2.5 to 10, with lower values being preferred for high-frequency applications.
3.2. Dielectric Strength
Dielectric strength is the maximum electric field strength that an insulation material can withstand before electrical breakdown occurs. It is measured in volts per millimeter (V/mm) or kilovolts per millimeter (kV/mm). A higher dielectric strength indicates better insulation properties and resistance to electrical breakdown.
3.3. Thermal Conductivity
Thermal conductivity is a measure of a material’s ability to conduct heat. It is expressed in watts per meter-kelvin (W/mK). A higher thermal conductivity allows for better heat dissipation, which is essential for maintaining the stability and reliability of electronic components. Ceramic and metal-core PCBs have higher thermal conductivity compared to FR-4 and other polymer-based materials.
3.4. Coefficient of Thermal Expansion (CTE)
The coefficient of thermal expansion (CTE) is a measure of a material’s dimensional change in response to temperature variations. It is expressed in parts per million per degree Celsius (ppm/°C). A lower CTE indicates better dimensional stability and reduces the risk of thermal stress and warpage in the PCB. Matching the CTE of the insulation material with that of the copper traces and components is crucial for ensuring the long-term reliability of the PCB.
3.5. Moisture Absorption
Moisture absorption refers to the ability of a material to absorb moisture from the environment. It is expressed as a percentage of weight gain. High moisture absorption can lead to the degradation of insulation properties, reduce the mechanical strength of the PCB, and cause delamination. Most PCB insulation materials are designed to have low moisture absorption to ensure long-term reliability.
Material | Dielectric Constant (Dk) | Dielectric Strength (kV/mm) | Thermal Conductivity (W/mK) | CTE (ppm/°C) | Moisture Absorption (%) |
---|---|---|---|---|---|
FR-4 | 4.2 – 4.8 | 20 – 30 | 0.3 – 0.4 | 12 – 16 | 0.15 – 0.20 |
Polyimide | 3.5 – 3.9 | 60 – 120 | 0.2 – 0.3 | 12 – 20 | 0.40 – 0.80 |
PTFE | 2.0 – 2.1 | 40 – 80 | 0.2 – 0.3 | 50 – 100 | 0.01 – 0.03 |
Ceramic | 8.0 – 10.0 | 20 – 40 | 20 – 200 | 4 – 8 | 0.00 – 0.02 |
4. PCB Insulation Techniques
In addition to the choice of insulation material, various techniques are employed in PCB manufacturing to enhance the insulation properties and protect the conductive elements. These techniques are applied at different stages of the PCB fabrication process and serve specific purposes. Some of the most common PCB insulation techniques include:
4.1. Solder Mask
Solder mask, also known as solder resist, is a thin layer of polymer applied to the outer surfaces of a PCB. Its primary purpose is to protect the copper traces from oxidation, prevent solder bridges during assembly, and provide electrical insulation between adjacent traces. Solder mask is typically applied using screen printing or photoimaging techniques and is available in various colors, with green being the most common.
4.2. Conformal Coating
Conformal coating is a protective layer applied to the assembled PCB to provide additional insulation, moisture resistance, and protection against environmental contaminants. The coating material, such as acrylic, silicone, or polyurethane, is applied using spraying, dipping, or brushing techniques. Conformal coating is particularly useful in applications exposed to harsh environments, such as automotive, aerospace, and industrial electronics.
4.3. Potting and Encapsulation
Potting and encapsulation involve filling the voids and spaces within an assembled PCB with a protective compound, such as epoxy or silicone. This technique provides complete isolation and protection of the electronic components from environmental factors, such as moisture, dust, and vibrations. Potting and encapsulation are commonly used in high-reliability applications, such as medical devices, military electronics, and underwater equipment.
4.4. Layer Stacking and Separation
In multi-layer PCBs, proper insulation between the conductive layers is achieved through layer stacking and separation techniques. This involves the use of insulating materials, such as prepreg (pre-impregnated fiberglass) and core laminates, to separate the conductive layers. The thickness and properties of these insulating layers are carefully chosen to ensure adequate electrical isolation and minimize signal interference between the layers.
5. Applications of PCB Insulation
PCB insulation plays a crucial role in various industries and applications, each with its specific requirements and challenges. Some of the key areas where PCB insulation is of utmost importance include:
5.1. Consumer Electronics
In consumer electronics, such as smartphones, tablets, and laptops, PCB insulation is essential for ensuring the proper functioning and reliability of the devices. The high-density and compact nature of these PCBs require effective insulation techniques to prevent signal interference and short circuits. FR-4 is the most commonly used insulation material in consumer electronics due to its cost-effectiveness and good electrical properties.
5.2. Automotive Electronics
Automotive electronics are subjected to harsh environmental conditions, such as extreme temperatures, vibrations, and moisture. PCB insulation in automotive applications must withstand these challenges and ensure the long-term reliability of the electronic systems. High-temperature materials, such as polyimide and ceramic, are often used in automotive PCBs, along with conformal coating and potting techniques for additional protection.
5.3. Medical Devices
Medical devices, such as implantable devices and diagnostic equipment, require high levels of electrical insulation and biocompatibility. PCB insulation materials used in medical applications must meet stringent regulatory requirements and ensure patient safety. Ceramic and polyimide PCBs are commonly used in medical devices due to their excellent insulation properties and chemical resistance.
5.4. Aerospace and Defense
Aerospace and defense applications demand the highest levels of reliability and performance from their electronic systems. PCBs in these applications must withstand extreme environmental conditions, such as high altitudes, radiation, and electromagnetic interference. PTFE and ceramic PCBs are widely used in aerospace and defense electronics due to their exceptional insulation properties, thermal stability, and low dielectric constant.
5.5. Industrial Automation
Industrial automation systems, such as process control and monitoring equipment, require robust and reliable PCBs that can operate in harsh industrial environments. PCB insulation in these applications must provide protection against moisture, dust, and chemical contaminants. Conformal coating and potting techniques are commonly employed in industrial PCBs to enhance their durability and long-term reliability.
6. Challenges in PCB Insulation
Despite the advancements in PCB insulation materials and techniques, there are still several challenges that designers and manufacturers must address to ensure the optimal performance and reliability of electronic devices. Some of the key challenges in PCB insulation include:
6.1. High-Frequency Applications
With the increasing demand for high-speed and high-frequency electronic devices, PCB insulation materials must exhibit low dielectric constant and low loss tangent to minimize signal attenuation and distortion. Traditional insulation materials, such as FR-4, may not be suitable for high-frequency applications due to their higher dielectric constant and loss tangent. Designers must select specialized materials, such as PTFE or Rogers materials, to meet the stringent requirements of high-frequency PCBs.
6.2. Miniaturization and High-Density PCBs
The trend towards miniaturization and high-density PCBs poses significant challenges for PCB insulation. As the spacing between conductive traces and components decreases, the risk of signal interference and crosstalk increases. Designers must employ advanced insulation techniques, such as high-resolution solder mask and fine-pitch layer stacking, to ensure adequate insulation in high-density PCBs. Additionally, the use of thinner insulation materials may be necessary to accommodate the reduced space available in miniaturized devices.
6.3. Harsh Environmental Conditions
Electronic devices used in harsh environmental conditions, such as extreme temperatures, humidity, and chemical exposure, require robust PCB insulation that can withstand these challenges. Designers must select insulation materials with appropriate thermal, mechanical, and chemical properties to ensure the long-term reliability of the PCBs. Conformal coating and potting techniques can provide additional protection against environmental factors, but they also introduce challenges in terms of material selection, application process, and rework capabilities.
7. Selecting the Right PCB Insulation Material
Choosing the appropriate PCB insulation material is crucial for ensuring the optimal performance, reliability, and cost-effectiveness of an electronic device. Several factors must be considered when selecting the insulation material, including:
- Electrical properties: Dielectric constant, dielectric strength, and loss tangent
- Thermal properties: Glass transition temperature (Tg), thermal conductivity, and CTE
- Mechanical properties: Flexural strength, tensile strength, and elongation
- Environmental resistance: Moisture absorption, chemical resistance, and flammability
- Manufacturability: Ease of processing, adhesion to copper, and compatibility with other materials
- Cost: Raw material cost, processing cost, and availability
Designers must carefully evaluate these factors and prioritize them based on the specific requirements of the application. Trade-offs may be necessary to balance performance, reliability, and cost. Consultation with PCB manufacturers and material suppliers can provide valuable insights and recommendations for selecting the most suitable insulation material for a given application.
8. PCB Insulation Testing and Quality Control
To ensure the quality and reliability of PCB insulation, various testing and quality control methods are employed during the manufacturing process and final inspection. Some of the common PCB insulation testing techniques include:
- Insulation resistance (IR) testing: Measures the resistance between conductive elements to ensure adequate insulation.
- Dielectric withstanding voltage (DWV) testing: Applies a high voltage between conductive elements to detect any insulation breakdowns.
- Thermal cycling: Subjects the PCB to repeated temperature cycles to evaluate the stability of the insulation materials and the integrity of the interconnections.
- Moisture resistance testing: Exposes the PCB to high humidity conditions to assess the insulation material’s resistance to moisture absorption and its impact on electrical properties.
- Microsectioning: Involves cross-sectioning the PCB and examining the insulation layers under a microscope to detect any defects or delamination.
Implementing a robust quality control system, including incoming material inspection, process control, and final testing, is essential for maintaining the consistency and reliability of PCB insulation. Adherence to industry standards, such as IPC (Association Connecting Electronics Industries) specifications, ensures that the PCBs meet the required quality and performance criteria.
9. Future Trends in PCB Insulation
As the electronics
Leave a Reply