Factors That Affect PCB Price
Many variables go into calculating the final price of a printed circuit board. The main cost drivers include:
Board Specifications
The physical properties and manufacturing requirements of the PCB have a significant impact on cost:
-
Board size: Larger PCBs require more material and are priced higher. Minimizing board dimensions where possible helps reduce cost.
-
Layer count: Each additional copper layer increases the complexity and cost of the board. Designs should use the fewest layers necessary.
-
Thickness: Thicker boards use more insulating substrate material and are more expensive. Standard 1.6mm thickness is most economical.
-
Material type: FR-4 glass-reinforced epoxy laminate is the default choice for its good performance and reasonable cost. High-performance materials (Rogers, polyimide, etc.) have better properties but also higher prices.
-
Minimal hole size: Smaller drilled holes require more precise and expensive equipment. Avoiding tiny vias below 8 mil when possible reduces cost.
-
Copper weight: Thicker copper foil costs more but enables higher current carrying capacity. 1 oz. copper is standard for good performance and price.
Quantity and Setup Fees
Ordering PCBs in higher volumes yields a lower per-unit price due to economies of scale and bulk material discounts. However, fabricators also charge an initial setup fee to cover machine programming, stencil creation, and other tasks required to start a new production job. This one-time fee is amortized across the total number of boards ordered.
For these reasons, the price curve relative to quantity is non-linear:
Quantity | 5 | 10 | 25 | 50 | 100 | 250 | 500 | 1000 |
---|---|---|---|---|---|---|---|---|
Price ($) | $95 | $115 | $130 | $165 | $185 | $275 | $385 | $510 |
Example prices for a 2-layer 50x50mm PCB. Actual prices vary by supplier.
Requesting a quote for multiple quantities helps determine the most cost-effective option. In some cases, bumping up to the next tier can significantly reduce unit cost.
Surface Finishes
The outer surfaces of a PCB require plating to protect exposed copper traces from oxidation and facilitate soldering. Hot air solder leveling (HASL) is an economical Sn/Pb finish. More advanced lead-free options like ENIG (electroless nickel immersion gold) have flatter surfaces and higher reliability but cost 15-20% more than HASL.
Solder Mask Color
Green is the default solder mask color and lowest cost since it’s the most widely stocked. Custom colors like red, yellow, blue, black, and white are available for a ~10% upcharge to cover lower volume pigments and additional setup.
Silkscreen
The silkscreen layer prints labels and imagery on the board surfaces. White ink on a colored background is standard and lowest price. Using multiple silkscreen colors increases cost by ~$8-10 per color due to additional setup and printing steps.
Testing and Inspection
PCB fabs can perform flying probe or bed-of-nails testing to verify continuity and detect manufacturing defects. Automated optical inspection (AOI) compares the boards to a “golden sample” to check for errors. X-ray inspection examines solder joints beneath BGA and QFN packages. Each of these services adds cost but can greatly improve quality and reduce scrap:
Service | Price Adder |
---|---|
Electrical test | $0.10-$0.25 |
AOI | $0.20-$0.40 |
X-ray | $3-$5 |
Leadtime
Faster delivery increases cost since fabs must expedite your job ahead of others. Standard 2-3 week turns are lowest price. 5-day service adds a 15-20% “rush fee”, while 24-48 hour turns can increase price by 50% or more. Planning ahead avoids expensive rushed orders.
PCB Price Estimation Tools
Many PCB manufacturers provide instant online quoting tools to estimate pricing:
Entering your PCB’s properties will calculate an approximate price and allow you to optimize the cost by tweaking specifications. Note that these prices may not include setup fees, testing, or other options.
Design Tips to Reduce PCB Cost
Efficient PCB designs can minimize manufacturing cost without sacrificing performance or reliability:
-
Reduce board size: Shrinking the board dimensions cuts material cost. Use smaller components and higher density placement to pack more circuitry into a compact area. Consider panelizing multiple copies of smaller designs into a larger PCB for a lower per-unit cost.
-
Minimize layer count: More layers = higher price. Route signals on fewer layers where possible. 2-4 layers are most economical. 6+ layers are costlier specialty builds.
-
Increase hole sizes: Relaxing mini drill sizes from 6 to 8 mil and up makes fabrication easier and reduces cost. Reserve the smallest vias only for escape routing from fine-pitch BGA pads.
-
Standardize on common specs: Using conventional materials, thicknesses, copper weights, and colors saves money by matching the PCB shop’s standard processes and inventory.
-
Panelize designs: Combining multiple copies of a design into a larger array reduces setup and tooling amortization compared to building them separately. Rails with tooling holes simplify depanelization after assembly.
-
Design for Tab Assembly Adding edge rails with tooling holes to your PCB panel allows it to be loaded directly into pick-and-place feeders for robotic assembly. This avoids slower hand assembly and lowers cost.
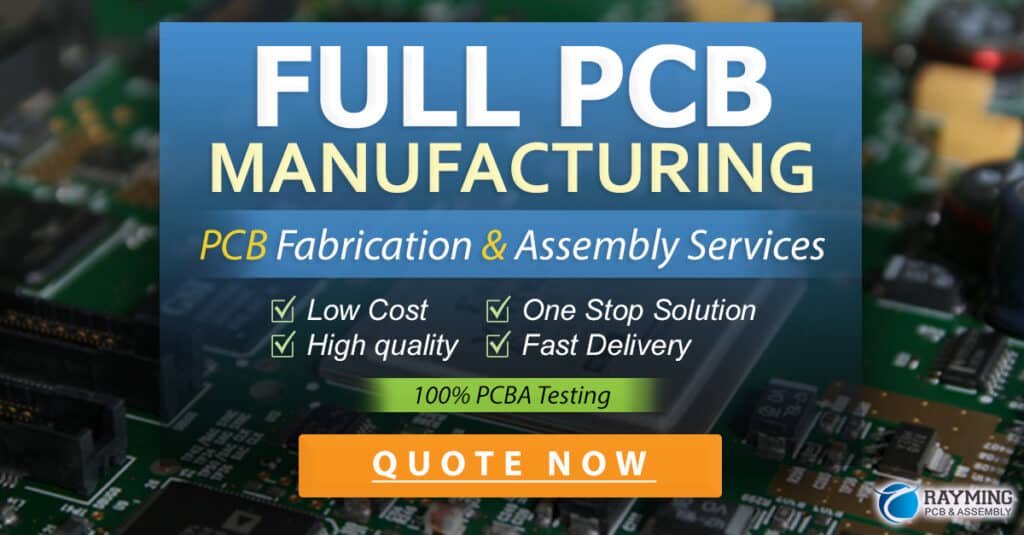
Frequently Asked Questions
What is the typical cost of a PCB?
Prices vary widely based on board specs and quantity. A basic 2-layer 1″ x 2″ PCB might cost $20-50 in quantity 5, $50-$100 for 100 units, or $300-$800 for 1000 pieces. More complex 4-6 layer boards with tight tolerances and special requirements can easily exceed $1000 for a prototype set and $1-$5 per board in volume.
Why are small quantity PCBs so expensive?
There are significant fixed setup costs involved in producing a PCB (CAM review, tooling, etc.). Ordering just a few pieces concentrates all those initial expenses into the small batch. Larger volumes allow spreading the setup costs across more units for a lower price each.
How much do additional PCB layers cost?
Each extra layer adds about 20-50% to the base PCB price, although this scales with volume. A 4-layer board might be 40% more than 2-layer in qty. 5 but only 25% more in qty. 1000+. The price jump from 2 to 4 layers is less than 4 to 6 due to the extra processing steps for 6+ layer boards.
What are the most effective ways to reduce PCB cost?
- Minimize board size
- Use fewer layers
- Avoid small vias below 8 mil
- Choose standard specs and materials
- Order larger quantities
- Panelize multiple copies
- Relax tolerances and leadtimes where possible
How much does assembly add to the cost of a PCB?
Assembling the components to a populated PCB typically adds 25-200% to the bare board cost. Factors include component count, package sizes, special handling (moisture sensitivity, etc.), and testing/programming requirements. Simpler builds with larger chip packages and wider pitches are less expensive than dense SMT assemblies with many tiny chips. Get quotes from multiple suppliers to compare full turnkey pricing.
I hope this article provides a useful overview of the factors involved in PCB costing and how to optimize your designs for the best price. Let me know if you have any other questions!
Leave a Reply