Introduction to PCB Cross-Section
A printed circuit board (PCB) cross-section is a vital tool for analyzing the internal structure and layers of a PCB. By examining a cross-section, engineers and technicians can assess the quality of the manufacturing process, identify potential issues, and ensure that the PCB meets the required specifications. In this article, we will explore the concept of PCB cross-section, its importance, and the various techniques used to create and analyze these cross-sections.
What is a PCB?
Before delving into PCB cross-sections, it is essential to understand what a PCB is. A printed circuit board is a flat, insulating substrate that supports and connects electronic components using conductive tracks, pads, and other features etched from copper sheets laminated onto the substrate. PCBs are used in almost all electronic devices, from smartphones and computers to industrial equipment and medical devices.
Why PCB Cross-Sections are Important
PCB cross-sections provide valuable insights into the internal structure of a PCB, which is crucial for several reasons:
- Quality control: By examining a cross-section, manufacturers can ensure that the PCB has been produced according to the specified design and meets the required quality standards.
- Troubleshooting: When a PCB fails or exhibits unexpected behavior, a cross-section can help identify the root cause of the problem, such as manufacturing defects or design flaws.
- Research and development: Cross-sections are essential for studying the effects of different materials, manufacturing processes, and environmental conditions on PCB performance and reliability.
Techniques for Creating PCB Cross-Sections
There are several methods for creating PCB cross-sections, each with its advantages and limitations. The choice of technique depends on factors such as the desired level of detail, the available equipment, and the specific requirements of the analysis.
Mechanical Sectioning
Mechanical sectioning involves cutting the PCB along a selected plane using a specialized saw or cutting tool. The exposed cross-section is then polished to remove any roughness or debris. This method is relatively simple and inexpensive, but it can cause damage to the PCB structure and may not provide the highest level of detail.
Laser Cutting
Laser cutting uses a high-powered laser beam to precisely cut through the PCB material. This technique offers several advantages over mechanical sectioning, including:
- Minimal damage to the PCB structure
- High precision and accuracy
- Ability to create complex cutting patterns
However, laser cutting requires specialized equipment and may be more expensive than mechanical sectioning.
Ion Beam Milling
Ion beam milling is a highly advanced technique that uses a focused beam of ions to remove material from the PCB surface. This method offers the highest level of precision and can reveal intricate details of the PCB structure. However, ion beam milling is also the most expensive and time-consuming technique, and it requires specialized equipment and expertise.
Analyzing PCB Cross-Sections
Once a PCB cross-section has been created, it can be analyzed using various methods to gain insights into the PCB structure and performance.
Optical Microscopy
Optical microscopy is the most common method for analyzing PCB cross-sections. It involves using a microscope to visually inspect the exposed layers and features of the PCB. Optical microscopy can reveal information such as:
- Layer thickness and uniformity
- Copper trace width and spacing
- Drill hole quality and alignment
- Solder mask and silkscreen coverage
However, optical microscopy has limitations in terms of resolution and depth of focus, and it may not be suitable for analyzing very small or complex features.
Scanning Electron Microscopy (SEM)
Scanning electron microscopy (SEM) is a more advanced technique that uses a focused beam of electrons to produce high-resolution images of the PCB cross-section. SEM can reveal much finer details than optical microscopy, including:
- Grain structure and morphology of the copper traces
- Defects or voids in the PCB materials
- Contamination or corrosion on the PCB surface
SEM requires specialized equipment and expertise, and it can be more time-consuming and expensive than optical microscopy.
Energy-Dispersive X-ray Spectroscopy (EDS)
Energy-dispersive X-ray spectroscopy (EDS) is a technique that can be used in conjunction with SEM to analyze the chemical composition of the PCB materials. EDS works by detecting the characteristic X-rays emitted by the atoms in the sample when they are excited by the electron beam. This information can be used to identify the presence of contaminants, corrosion products, or other unwanted materials in the PCB.
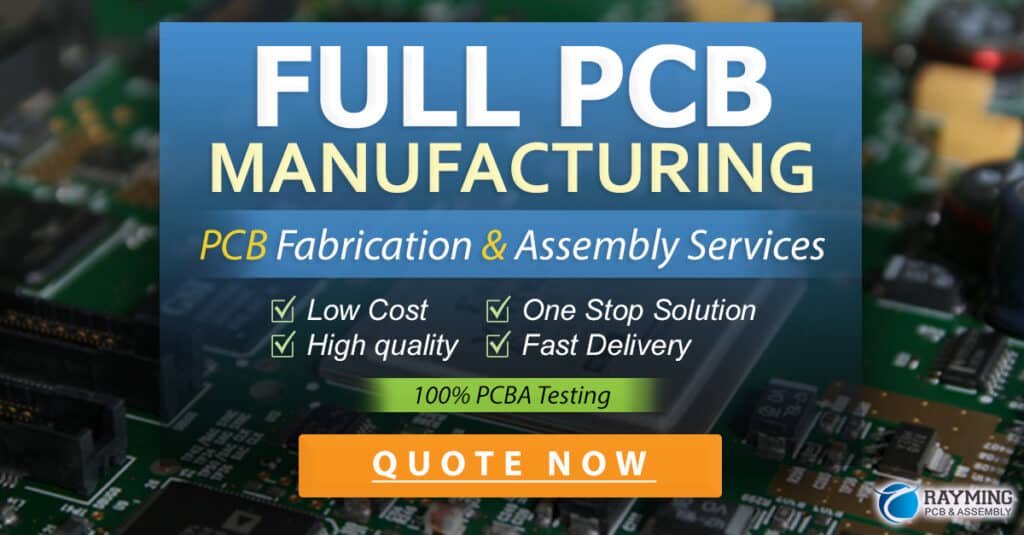
Common PCB Cross-Section Features and Defects
By analyzing PCB cross-sections, engineers and technicians can identify various features and defects that can affect the performance and reliability of the PCB.
Copper Thickness
The thickness of the copper traces is a critical factor in PCB performance, as it determines the current-carrying capacity and resistance of the traces. PCB cross-sections can be used to measure the copper thickness and ensure that it meets the specified requirements.
Layer | Minimum Thickness (μm) | Typical Thickness (μm) |
---|---|---|
Outer | 17.5 | 35 |
Inner | 17.5 | 35 |
Dielectric Thickness
The thickness of the dielectric layers between the copper traces is also important, as it affects the impedance and signal integrity of the PCB. Cross-sections can be used to measure the dielectric thickness and ensure that it is consistent and within the specified tolerances.
Drill Hole Quality
The quality of the drill holes is crucial for ensuring reliable connections between the layers of the PCB. Cross-sections can reveal defects such as:
- Misaligned or oversized holes
- Rough or damaged hole walls
- Incomplete plating or voids in the hole filling
Solder Mask and Silkscreen Coverage
Solder mask and silkscreen are protective and informative layers applied to the surface of the PCB. Cross-sections can be used to assess the coverage and adhesion of these layers, as well as any defects or inconsistencies.
Frequently Asked Questions (FAQ)
-
What is the purpose of creating a PCB cross-section?
A PCB cross-section is created to analyze the internal structure and layers of a PCB, assess the quality of the manufacturing process, identify potential issues, and ensure that the PCB meets the required specifications. -
What are the most common techniques for creating PCB cross-sections?
The most common techniques for creating PCB cross-sections are mechanical sectioning, laser cutting, and ion beam milling. Each method has its advantages and limitations, and the choice depends on factors such as the desired level of detail, available equipment, and specific requirements of the analysis. -
What can be learned from analyzing a PCB cross-section using optical microscopy?
Optical microscopy can reveal information such as layer thickness and uniformity, copper trace width and spacing, drill hole quality and alignment, and solder mask and silkscreen coverage. -
What are the advantages of using scanning electron microscopy (SEM) for analyzing PCB cross-sections?
SEM can reveal much finer details than optical microscopy, including grain structure and morphology of the copper traces, defects or voids in the PCB materials, and contamination or corrosion on the PCB surface. -
What are some common defects that can be identified by analyzing PCB cross-sections?
Common defects that can be identified by analyzing PCB cross-sections include misaligned or oversized drill holes, rough or damaged hole walls, incomplete plating or voids in the hole filling, and inconsistencies in solder mask and silkscreen coverage.
Conclusion
PCB cross-sections are essential tools for analyzing the internal structure and quality of printed circuit boards. By creating and examining cross-sections, engineers and technicians can identify potential issues, ensure that the PCB meets the required specifications, and optimize the manufacturing process for improved performance and reliability. Various techniques, such as mechanical sectioning, laser cutting, and ion beam milling, can be used to create PCB cross-sections, while optical microscopy, scanning electron microscopy, and energy-dispersive X-ray spectroscopy are common methods for analyzing the exposed layers and features. Understanding the importance of PCB cross-sections and the techniques used to create and analyze them is crucial for anyone involved in PCB design, manufacturing, or quality control.
Leave a Reply