Introduction to Ultra-Thin PCB Technology
Ultra-thin printed circuit boards (PCBs) are a revolutionary technology in the electronics industry, enabling the creation of highly compact and lightweight devices. These PCBs are characterized by their extremely thin profile, typically measuring less than 0.4 mm in thickness. The demand for ultra-thin PCBs has grown significantly in recent years, driven by the increasing miniaturization of electronic devices and the need for improved performance in applications such as smartphones, wearables, and medical devices.
Key Features of Ultra-Thin PCBs
- Reduced thickness: Ultra-thin PCBs have a thickness of 0.4 mm or less, compared to standard PCBs, which are typically 1.6 mm thick.
- Lightweight: The reduced thickness of ultra-thin PCBs results in a significant reduction in weight, making them ideal for portable and wearable devices.
- Enhanced flexibility: Ultra-thin PCBs offer increased flexibility, allowing them to be bent or folded to fit into compact spaces or conform to unique device shapes.
- Improved thermal management: The thin profile of ultra-thin PCBs enables better heat dissipation, reducing the risk of thermal issues in high-performance devices.
Manufacturing Process of Ultra-Thin PCBs
The manufacturing process of ultra-thin PCBs involves several specialized techniques and materials to achieve the desired thinness and performance. Here are the key steps involved in the production of ultra-thin PCBs:
1. Material Selection
The choice of substrate material is crucial in the manufacturing of ultra-thin PCBs. The most commonly used materials include:
- Polyimide (PI): Polyimide is a high-performance polymer that offers excellent thermal stability, mechanical strength, and electrical insulation properties. It is the preferred choice for ultra-thin PCBs due to its ability to maintain its properties even at reduced thicknesses.
- Liquid Crystal Polymer (LCP): LCP is another advanced polymer that combines the benefits of polyimide with enhanced electrical performance and moisture resistance. It is particularly suitable for high-frequency applications.
2. Copper Foil Lamination
Ultra-thin PCBs require the use of thin copper foils to maintain the overall thinness of the board. The typical copper foil thickness for ultra-thin PCBs ranges from 9 μm to 18 μm, compared to the standard 35 μm or 70 μm used in regular PCBs. The thin copper foil is laminated onto the substrate material using specialized lamination processes that ensure proper adhesion and minimize the risk of defects.
3. Circuit Patterning
The circuit patterning process for ultra-thin PCBs involves the use of advanced imaging and etching techniques to create the desired conductive traces on the copper foil. High-resolution photolithography is employed to transfer the circuit pattern onto the copper foil, followed by precise etching to remove the unwanted copper areas. The challenges in patterning ultra-thin PCBs include maintaining the integrity of the thin copper traces and ensuring accurate alignment of the layers in multi-layer designs.
4. Via Formation
Vias are the conductive pathways that connect different layers of a multi-layer PCB. In ultra-thin PCBs, the formation of vias requires specialized drilling and plating techniques to achieve the desired aspect ratio and ensure reliable electrical connections. Laser drilling is commonly used to create micro-vias with diameters as small as 50 μm, while advanced plating processes, such as electroless copper plating and direct metallization, are employed to metalize the via walls.
5. Solder Mask Application
The solder mask is a protective layer applied over the copper traces to prevent short circuits and improve the PCB’s durability. In ultra-thin PCBs, the solder mask must be thin enough to maintain the overall thinness of the board while providing adequate coverage and protection. Liquid photoimageable solder masks (LPI) are commonly used for ultra-thin PCBs, as they can be applied in thin layers and offer excellent resolution and adhesion properties.
6. Surface Finish
The surface finish on ultra-thin PCBs serves to protect the exposed copper pads and improve solderability. Common surface finishes for ultra-thin PCBs include:
- Electroless Nickel Immersion Gold (ENIG): ENIG is a popular choice for ultra-thin PCBs due to its excellent solderability, durability, and compatibility with fine-pitch components.
- Immersion Silver (IAg): IAg is a cost-effective alternative to ENIG, offering good solderability and shelf life. However, it may not be suitable for applications with strict storage requirements or exposure to harsh environments.
- Organic Solderability Preservative (OSP): OSP is a thin, organic coating that provides temporary protection to the copper pads. It is a low-cost option but may require careful handling and storage to maintain its effectiveness.
Applications of Ultra-Thin PCBs
Ultra-thin PCBs find applications in a wide range of industries and products where size, weight, and performance are critical factors. Some of the key applications include:
1. Smartphones and Tablets
The demand for sleeker and more powerful smartphones and tablets has driven the adoption of ultra-thin PCBs in these devices. Ultra-thin PCBs enable the integration of advanced features, such as high-resolution displays, multi-camera systems, and 5G connectivity, while keeping the device thickness to a minimum. The use of ultra-thin PCBs also allows for better battery optimization and improved thermal management in these compact devices.
2. Wearable Electronics
Wearable devices, such as smartwatches, fitness trackers, and smart clothing, require PCBs that are not only thin but also flexible to conform to the body’s contours. Ultra-thin PCBs made from flexible materials, such as polyimide, are ideal for wearable applications. They enable the integration of sensors, wireless connectivity, and power management components in a compact and lightweight form factor, enhancing user comfort and functionality.
3. Medical Devices
Ultra-thin PCBs are increasingly used in medical devices, particularly in implantable and ingestible electronics. These devices require PCBs that are not only thin but also biocompatible and reliable. Ultra-thin PCBs enable the development of miniaturized medical devices, such as pacemakers, neurostimulators, and drug delivery systems, that can be implanted with minimal invasiveness. The use of ultra-thin PCBs also allows for the integration of advanced sensing and wireless communication capabilities in these devices, enabling remote monitoring and treatment optimization.
4. Automotive Electronics
The automotive industry is increasingly adopting ultra-thin PCBs to meet the demands for lightweight, compact, and high-performance electronic systems. Ultra-thin PCBs are used in various automotive applications, such as infotainment systems, advanced driver assistance systems (ADAS), and vehicle-to-everything (V2X) communication modules. The reduced weight and size of ultra-thin PCBs contribute to overall vehicle weight reduction, improving fuel efficiency and reducing emissions. Additionally, the enhanced thermal management properties of ultra-thin PCBs help ensure reliable operation in the harsh automotive environment.
5. Internet of Things (IoT) Devices
The Internet of Things (IoT) relies on a vast network of connected devices that collect, process, and transmit data. Ultra-thin PCBs are essential in enabling the miniaturization and integration of IoT devices, such as sensors, actuators, and communication modules. The compact size and low power consumption of ultra-thin PCB-based IoT devices allow for their widespread deployment in various applications, including smart homes, industrial automation, and environmental monitoring. The flexibility offered by ultra-thin PCBs also enables the development of IoT devices that can be embedded in everyday objects, such as clothing, furniture, and packaging.
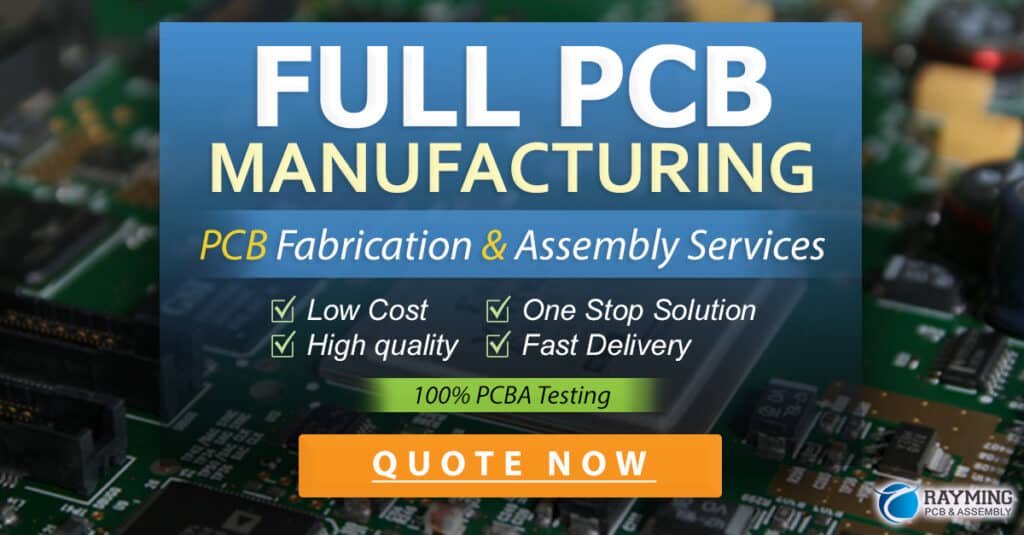
Challenges and Future Trends in Ultra-Thin PCB Technology
While ultra-thin PCBs offer numerous benefits, their development and adoption also present several challenges. Some of the key challenges include:
- Manufacturing complexity: The production of ultra-thin PCBs requires specialized equipment, materials, and processes, which can increase manufacturing costs and lead times.
- Handling and assembly: The reduced thickness and increased flexibility of ultra-thin PCBs make them more susceptible to damage during handling and assembly. Special care and techniques are required to prevent bending, warping, or cracking of the boards.
- Thermal management: Although ultra-thin PCBs offer improved thermal management compared to thicker boards, the high component density and reduced board thickness can still pose challenges in managing heat dissipation, particularly in high-performance applications.
- Signal integrity: As the thickness of the PCB decreases, the risk of signal integrity issues, such as crosstalk and electromagnetic interference (EMI), increases. Careful design and layout techniques are necessary to maintain signal integrity in ultra-thin PCBs.
Despite these challenges, the future of ultra-thin PCB technology looks promising, with several trends and developments on the horizon:
- Advanced materials: Ongoing research and development in advanced PCB materials, such as high-performance polymers and nanomaterials, are expected to further enhance the mechanical, thermal, and electrical properties of ultra-thin PCBs.
- Embedded components: The integration of passive components, such as resistors and capacitors, directly into the PCB substrate is gaining traction in ultra-thin PCB design. Embedded components not only save space but also improve electrical performance and reliability.
- 3D printing: The adoption of 3D printing technologies in PCB manufacturing is expected to revolutionize the production of ultra-thin PCBs. 3D printing enables the creation of complex, multi-layer PCB structures with intricate geometries and embedded components, offering new design possibilities and reduced manufacturing costs.
- Flexible and stretchable electronics: The development of ultra-thin PCBs using flexible and stretchable materials, such as elastomers and conductive polymers, is opening up new opportunities in wearable and implantable electronics. These advanced PCBs can conform to complex shapes and withstand repeated bending and stretching, enabling the creation of truly flexible electronic devices.
Frequently Asked Questions (FAQ)
1. What is the typical thickness of an ultra-thin PCB?
Ultra-thin PCBs typically have a thickness of 0.4 mm or less, compared to the standard PCB thickness of 1.6 mm.
2. What materials are commonly used for ultra-thin PCBs?
The most commonly used materials for ultra-thin PCBs are polyimide (PI) and liquid crystal polymer (LCP). These advanced polymers offer excellent mechanical, thermal, and electrical properties, even at reduced thicknesses.
3. Are ultra-thin PCBs more expensive than standard PCBs?
Yes, ultra-thin PCBs are generally more expensive than standard PCBs due to the specialized materials, manufacturing processes, and handling requirements involved in their production.
4. Can ultra-thin PCBs be used in high-frequency applications?
Yes, ultra-thin PCBs can be used in high-frequency applications, particularly when made from materials like liquid crystal polymer (LCP), which offers superior electrical performance and low dielectric loss.
5. How do ultra-thin PCBs contribute to the miniaturization of electronic devices?
Ultra-thin PCBs enable the miniaturization of electronic devices by reducing the overall thickness and weight of the PCB assembly. This allows for more compact and lightweight device designs, as well as the integration of advanced features and components in a smaller form factor.
Conclusion
Ultra-thin PCBs are a game-changing technology in the electronics industry, enabling the development of highly compact, lightweight, and high-performance devices. With their reduced thickness, enhanced flexibility, and improved thermal management properties, ultra-thin PCBs are finding applications in a wide range of industries, from smartphones and wearables to medical devices and automotive electronics.
The manufacturing of ultra-thin PCBs involves specialized materials, processes, and techniques to achieve the desired thinness and performance. While the production of ultra-thin PCBs presents challenges in terms of manufacturing complexity, handling, and signal integrity, ongoing research and development in advanced materials, embedded components, and 3D printing technologies are expected to further enhance the capabilities and adoption of ultra-thin PCBs.
As the demand for miniaturized and high-performance electronic devices continues to grow, ultra-thin PCBs will play an increasingly critical role in shaping the future of the electronics industry. By enabling the creation of ever-smaller, lighter, and more advanced devices, ultra-thin PCBs are poised to revolutionize the way we interact with technology in our everyday lives.
PCB Type | Thickness | Key Features | Common Applications |
---|---|---|---|
Ultra-Thin PCB | 0.4 mm or less | – Lightweight – Flexible – Improved thermal management |
– Smartphones and tablets – Wearable electronics – Medical devices – Automotive electronics – IoT devices |
Standard PCB | 1.6 mm | – Robust – Suitable for general-purpose applications |
– Consumer electronics – Industrial control systems – Telecommunications equipment |
Leave a Reply