Understanding Impedance in PCBs
Impedance, in the context of PCBs, refers to the opposition to the flow of alternating current (AC) in a circuit. It is a combination of resistance, capacitance, and inductance. In high-speed digital circuits, impedance matching is crucial to prevent signal reflections and maintain signal integrity.
Types of Impedance in PCBs
There are two main types of impedance in PCBs:
-
Characteristic Impedance: This is the impedance of a transmission line in a PCB, determined by its physical properties such as width, thickness, and dielectric constant of the substrate material.
-
Differential Impedance: This is the impedance between two coupled transmission lines, such as differential pairs used in high-speed interfaces like USB, HDMI, and Ethernet.
Common Impedance Values in PCBs
The common impedance values used in PCB design depend on the application and the standards followed. Here are some typical impedance values:
Impedance Value | Application |
---|---|
50 ohms | RF circuits, coaxial cables, USB |
75 ohms | Video applications, Ethernet |
90 ohms | Differential pairs in high-speed interfaces |
100 ohms | Ethernet, LVDS (Low-Voltage Differential Signaling) |
110 ohms | DDR3 memory interfaces |
These impedance values are chosen to match the impedance of the connectors, cables, and devices connected to the PCB, minimizing reflections and ensuring proper signal transmission.
Factors Affecting Impedance Control in PCBs
Several factors influence the impedance of a PCB transmission line:
-
Trace Width: Wider traces have lower impedance, while narrower traces have higher impedance.
-
Trace Thickness: Thicker traces have lower impedance compared to thinner traces.
-
Dielectric Constant: The dielectric constant of the substrate material affects the impedance. Higher dielectric constants result in lower impedance.
-
Substrate Thickness: The thickness of the substrate between the trace and the reference plane (ground or power plane) affects the impedance. Thicker substrates lead to higher impedance.
-
Trace Spacing: The spacing between traces, especially in differential pairs, affects the coupling and the differential impedance.
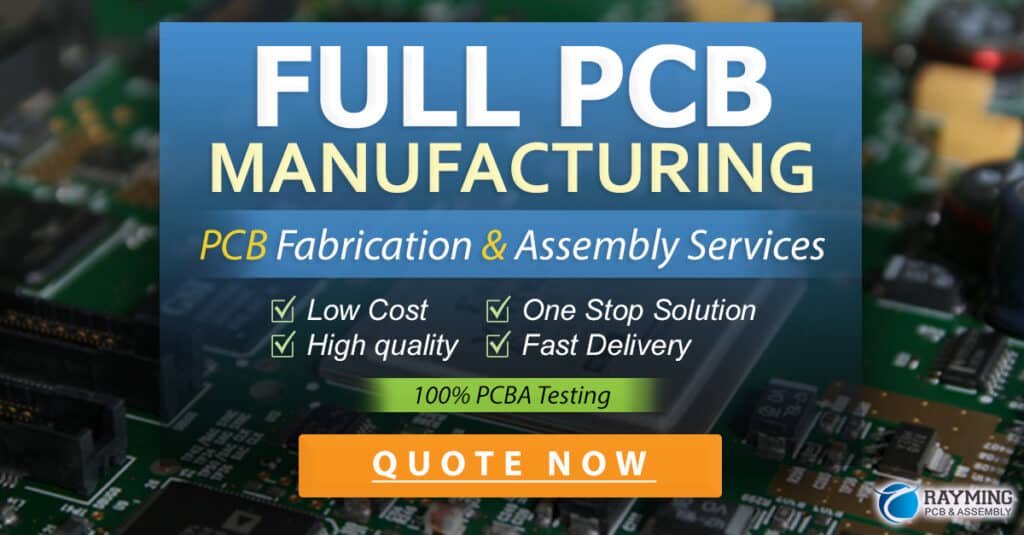
Designing for Impedance Control
To achieve impedance control in PCB design, consider the following guidelines:
-
Choose the right substrate material: Select a substrate material with a consistent dielectric constant and low loss tangent.
-
Calculate trace dimensions: Use impedance calculation tools or consult the PCB manufacturer to determine the appropriate trace width, thickness, and spacing for the desired impedance.
-
Maintain consistent trace geometry: Keep the trace width and spacing consistent throughout the length of the transmission line to avoid impedance discontinuities.
-
Use reference planes: Provide uninterrupted reference planes (ground or power) beneath the signal traces to maintain a constant impedance.
-
Route differential pairs carefully: Ensure that differential pairs are routed closely together, maintaining equal length and symmetry to minimize skew and maintain differential impedance.
-
Avoid impedance discontinuities: Minimize vias, stubs, and sharp bends in the signal path, as they can cause impedance discontinuities and reflections.
Measuring and Verifying Impedance
After designing and manufacturing the PCB, it is essential to measure and verify the impedance to ensure that it meets the desired specifications. There are several methods for measuring impedance:
-
Time Domain Reflectometry (TDR): TDR measures the impedance by sending a fast rise time pulse through the transmission line and analyzing the reflected waveform.
-
Impedance Test Coupons: These are small test structures placed on the PCB panel that mimic the trace geometry and allow impedance measurement using a vector network analyzer (VNA) or impedance test equipment.
-
Simulation and Modeling: Electronic design automation (EDA) tools can simulate and model the impedance of transmission lines based on the PCB stackup and trace geometry.
Verifying the impedance helps identify any deviations from the desired values and enables corrective actions to be taken before mass production.
Impedance Control PCB Manufacturing
Manufacturing PCBs with controlled impedance requires specialized processes and equipment. Here are some key considerations:
-
Stackup Design: The PCB manufacturer works with the designer to create a stackup that meets the impedance requirements, specifying the substrate material, layer thicknesses, and trace geometries.
-
Impedance Controlled Etching: The etching process must be tightly controlled to maintain the specified trace width and thickness. This is achieved through precise photolithography and etching techniques.
-
Dielectric Thickness Control: The thickness of the dielectric layers must be consistent to maintain the desired impedance. This is achieved through careful lamination and pressing processes.
-
Impedance Testing: The manufacturer performs impedance testing on the test coupons to verify that the PCB meets the specified impedance values.
Choosing a PCB manufacturer with experience in impedance control and a proven track record of producing high-quality boards is crucial for successful impedance-controlled designs.
Common Challenges in Impedance Control PCB Design
Designing impedance-controlled PCBs comes with its own set of challenges. Here are some common issues and how to address them:
-
Signal Integrity Issues: High-speed signals are susceptible to reflections, crosstalk, and EMI. Proper impedance matching, routing techniques, and shielding can help mitigate these issues.
-
Manufacturing Tolerances: PCB manufacturing processes have inherent tolerances that can affect impedance. Designers must take these tolerances into account and work closely with the manufacturer to ensure that the impedance requirements are met.
-
Material Availability: Not all substrate materials are readily available or cost-effective for impedance-controlled designs. Designers must choose materials that balance performance, availability, and cost.
-
Design Complexity: As PCBs become more complex with higher layer counts and denser layouts, maintaining consistent impedance becomes more challenging. Designers must use advanced routing techniques and simulation tools to ensure impedance control throughout the board.
-
Cost Considerations: Impedance-controlled PCBs often require specialized materials, processes, and testing, which can increase manufacturing costs. Designers must strike a balance between impedance control requirements and cost constraints.
FAQ
-
What is impedance control in PCBs?
Impedance control in PCBs refers to the process of designing and manufacturing PCBs with specific impedance values for the transmission lines, ensuring proper signal integrity and minimizing reflections. -
Why is impedance control important in PCB design?
Impedance control is crucial in PCB design to maintain signal integrity, minimize reflections, reduce EMI, and ensure proper functioning of high-speed digital circuits. -
What are the common impedance values used in PCBs?
Common impedance values in PCBs include 50 ohms for RF circuits and USB, 75 ohms for video applications and Ethernet, 90 ohms for differential pairs, 100 ohms for Ethernet and LVDS, and 110 ohms for DDR3 memory interfaces. -
What factors affect the impedance of a PCB transmission line?
The impedance of a PCB transmission line is affected by trace width, trace thickness, dielectric constant of the substrate material, substrate thickness, and trace spacing. -
How can I ensure impedance control in my PCB design?
To ensure impedance control in PCB design, choose the right substrate material, calculate trace dimensions, maintain consistent trace geometry, use reference planes, route differential pairs carefully, and avoid impedance discontinuities. Work closely with the PCB manufacturer and perform impedance testing to verify the desired impedance values.
Conclusion
Impedance control is a critical aspect of PCB design, particularly for high-speed digital circuits. Understanding the common impedance values, factors affecting impedance, and design guidelines is essential for creating reliable and high-performance PCBs. By working closely with PCB manufacturers and following best practices for impedance control, designers can ensure signal integrity, minimize reflections, and reduce EMI in their designs. As technology advances and PCBs become more complex, mastering impedance control techniques will be crucial for successful PCB design and manufacturing.
Leave a Reply