Introduction to Programmable PCBs
A programmable printed circuit board (PCB) is a type of PCB that contains a microcontroller or other programmable device, allowing the functionality of the board to be customized through software. Unlike traditional PCBs with fixed circuitry, programmable PCBs offer flexibility and can be reprogrammed to perform different tasks or behave in different ways.
Programmable PCBs are widely used in various applications, such as:
- Embedded systems
- IoT devices
- Robotics
- Automotive electronics
- Industrial automation
The ability to program and reprogram these boards makes them versatile and adaptable to changing requirements or updates.
Key Components of a Programmable PCB
To understand how programmable PCBs work, let’s look at the key components that make up these boards:
Microcontroller or Programmable Device
The heart of a programmable PCB is the microcontroller or programmable device. This component contains a processor, memory (RAM and ROM or flash), and input/output (I/O) peripherals. Some common microcontrollers used in programmable PCBs include:
- Arduino boards (based on ATmega microcontrollers)
- PIC microcontrollers
- ARM Cortex-M microcontrollers
- FPGA (Field-Programmable Gate Array) chips
The choice of microcontroller depends on factors such as processing power, memory requirements, power consumption, and the specific application.
Input/Output Interfaces
Programmable PCBs often include various input/output interfaces to communicate with external devices or sensors. These interfaces can include:
- Digital I/O pins
- Analog input pins
- PWM (Pulse-Width Modulation) pins
- Communication interfaces (UART, I2C, SPI)
- USB or Ethernet ports
These interfaces allow the programmable PCB to receive data from sensors, control actuators, or communicate with other devices.
Power Supply
Programmable PCBs require a stable power supply to function properly. The power supply circuitry on the board typically includes:
- Voltage regulators to provide stable voltage levels
- Decoupling capacitors to reduce noise
- Reverse polarity protection
- Over-current and over-voltage protection
The power supply requirements depend on the specific microcontroller and other components used on the board.
Programming Interface
To program the microcontroller on the PCB, a programming interface is necessary. This interface allows the user to write and upload code to the microcontroller’s memory. Common programming interfaces include:
- ICSP (In-Circuit Serial Programming) headers
- JTAG (Joint Test Action Group) connectors
- USB ports with bootloaders
The choice of programming interface depends on the microcontroller and the development tools used.
Designing a Programmable PCB
Designing a programmable PCB involves several steps and considerations:
-
Schematic Design: Create a schematic diagram that shows the connections between the microcontroller, power supply, I/O interfaces, and other components. Use PCB design software like KiCad, Eagle, or Altium Designer.
-
Component Selection: Choose the appropriate microcontroller, voltage regulators, connectors, and other components based on the requirements of your project. Consider factors such as processing speed, memory size, power consumption, and cost.
-
PCB Layout: Design the physical layout of the PCB, placing components and routing traces. Follow best practices for PCB layout, such as minimizing trace lengths, avoiding sharp angles, and providing proper grounding.
-
Manufacturing: Once the PCB design is complete, generate Gerber files and send them to a PCB manufacturer for fabrication. Choose the appropriate PCB material, copper weight, and surface finish based on your requirements.
-
Assembly: After receiving the fabricated PCB, assemble the components onto the board. Use proper soldering techniques and follow the component placement diagram.
-
Testing: Test the assembled PCB to ensure proper functionality. Use multimeters, oscilloscopes, and other tools to verify voltages, signals, and communication.
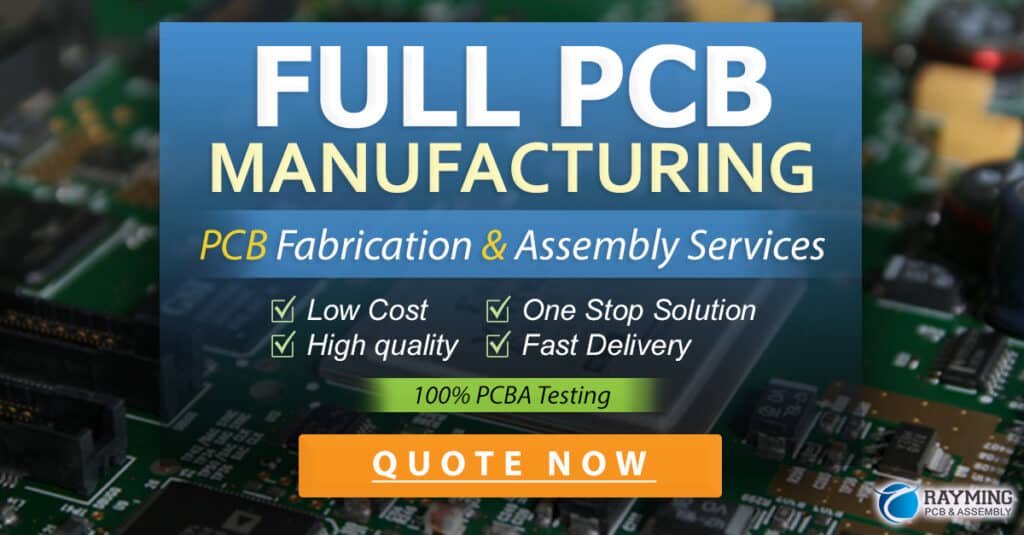
Programming a Programmable PCB
Programming a programmable PCB involves writing code for the microcontroller and uploading it to the board. The specific steps depend on the microcontroller and development tools used, but here’s a general overview:
-
Set up the Development Environment: Install the necessary software tools, such as the Arduino IDE, MPLAB X IDE, or Keil MDK, depending on the microcontroller. These tools provide an integrated development environment (IDE) for writing, compiling, and uploading code.
-
Write the Code: Write the code for your programmable PCB using the appropriate programming language, such as C, C++, or Arduino sketches. Use libraries and frameworks specific to your microcontroller to interact with I/O pins, communicate with sensors and actuators, and implement the desired functionality.
-
Compile and Debug: Compile the code to check for syntax errors and warnings. Debug the code using simulation tools or by uploading it to the PCB and using debugging probes to step through the code and monitor variables.
-
Upload the Code: Connect the PCB to your computer using the programming interface (e.g., USB, ICSP). Use the development tools to upload the compiled code to the microcontroller’s memory.
-
Test and Verify: Test the programmed PCB to ensure it functions as intended. Verify the behavior of inputs, outputs, and communication interfaces. Use serial monitors, LEDs, or other indicators to debug and troubleshoot if necessary.
-
Iterate and Optimize: Based on the testing results, iterate on the code and make necessary optimizations. This may involve refining algorithms, improving performance, or fixing bugs.
Applications of Programmable PCBs
Programmable PCBs find applications in various domains due to their flexibility and customization options. Some common applications include:
Embedded Systems
Programmable PCBs are extensively used in embedded systems, where a microcontroller is integrated into a device to control its functions. Examples include:
- Home automation systems
- Smart appliances
- Wearable devices
- Medical devices
Internet of Things (IoT)
Programmable PCBs are the building blocks of IoT devices, enabling them to collect data from sensors, communicate wirelessly, and perform local processing. Some IoT applications include:
- Smart home devices
- Industrial monitoring and control systems
- Agricultural sensors and automation
- Environmental monitoring
Robotics and Automation
Programmable PCBs are used in robotics and automation systems to control motors, sensors, and actuators. Examples include:
- Industrial robots
- Drones and unmanned vehicles
- Automated guided vehicles (AGVs)
- 3D printers and CNC machines
Automotive Electronics
Programmable PCBs are used in various automotive electronic systems, such as:
- Engine control units (ECUs)
- Body control modules
- Infotainment systems
- Advanced driver assistance systems (ADAS)
Education and Prototyping
Programmable PCBs, such as Arduino boards and Raspberry Pi, are widely used in education and prototyping. They provide an accessible platform for learning electronics, programming, and building projects. Many universities, schools, and makerspaces use these boards for teaching and hands-on learning.
Advantages of Programmable PCBs
Programmable PCBs offer several advantages over traditional fixed-function PCBs:
-
Flexibility: Programmable PCBs can be customized and reprogrammed to perform different tasks or adapt to changing requirements. This flexibility allows for faster development cycles and easier updates.
-
Cost-effective: Using programmable PCBs can be more cost-effective than designing and manufacturing custom fixed-function PCBs for each application. The same programmable PCB can be used across multiple projects with different software.
-
Rapid Prototyping: Programmable PCBs enable rapid prototyping and iteration. Designers can quickly test and refine their ideas by modifying the code without changing the hardware.
-
Reusability: Programmable PCBs can be reused across different projects or applications by simply reprogramming them. This reduces waste and minimizes the need for new hardware.
-
Ease of Updates: Firmware updates can be easily deployed to programmable PCBs, allowing for bug fixes, feature enhancements, or security patches without requiring hardware modifications.
Challenges and Considerations
While programmable PCBs offer many benefits, there are also some challenges and considerations to keep in mind:
-
Complexity: Programmable PCBs can be more complex to design and develop compared to fixed-function PCBs. They require knowledge of both hardware and software development.
-
Power Consumption: Programmable PCBs often consume more power than fixed-function PCBs due to the presence of a microcontroller and additional components. Power optimization techniques may be necessary to minimize power consumption.
-
Security: Programmable PCBs introduce security considerations, as the firmware can be vulnerable to tampering or reverse-engineering. Proper security measures, such as encryption and secure boot, should be implemented to protect the system.
-
Debugging: Debugging programmable PCBs can be more challenging than fixed-function PCBs. It requires using debugging tools, such as in-circuit debuggers or serial monitors, to identify and resolve issues in both hardware and software.
-
Cost: While programmable PCBs can be cost-effective in the long run, the initial development costs may be higher compared to fixed-function PCBs. The cost of the microcontroller, development tools, and programming time should be considered.
PCB Programmer
A PCB programmer, also known as a device programmer or firmware programmer, is a tool used to transfer the compiled code or firmware to the microcontroller’s memory on a programmable PCB. PCB programmers communicate with the microcontroller using specific programming protocols, such as ICSP, JTAG, or SWD (Serial Wire Debug).
PCB programmers can be hardware-based or software-based:
-
Hardware PCB Programmers: These are standalone devices that connect to the PCB through a programming interface, such as ICSP or JTAG headers. They typically have a USB or serial interface to communicate with a computer. Examples of hardware PCB programmers include:
-
PICkit programmers for PIC microcontrollers
- AVR ISP programmers for AVR microcontrollers
-
J-Link programmers for ARM Cortex-M microcontrollers
-
Software PCB Programmers: These are software tools that use the microcontroller’s built-in bootloader or firmware update mechanism to program the device. They typically communicate with the PCB through a USB or serial interface. Examples of software PCB programmers include:
-
Arduino IDE for Arduino boards
- STM32 ST-LINK Utility for STM32 microcontrollers
- MPLAB IPE for PIC microcontrollers
When using a PCB programmer, the general steps involve:
- Connecting the programmer to the PCB’s programming interface.
- Selecting the appropriate device and programming settings in the programmer software.
- Loading the compiled code or firmware file into the programmer.
- Initiating the programming process to transfer the code to the microcontroller’s memory.
- Verifying the successful programming and disconnecting the programmer.
PCB programmers play a crucial role in the development and deployment of programmable PCBs, allowing developers to update and modify the firmware as needed.
Frequently Asked Questions (FAQ)
-
What is the difference between a programmable PCB and a fixed-function PCB?
A programmable PCB contains a microcontroller or programmable device that can be customized through software, while a fixed-function PCB has a fixed circuitry and cannot be reprogrammed. -
What are some common microcontrollers used in programmable PCBs?
Common microcontrollers used in programmable PCBs include Arduino boards (based on ATmega microcontrollers), PIC microcontrollers, ARM Cortex-M microcontrollers, and FPGA chips. -
What software tools are used for programming PCBs?
Software tools used for programming PCBs depend on the specific microcontroller. Some common tools include the Arduino IDE, MPLAB X IDE, Keil MDK, and manufacturer-specific programming utilities. -
Can a programmable PCB be reprogrammed multiple times?
Yes, a programmable PCB can be reprogrammed multiple times. The microcontroller’s memory (flash) can be erased and rewritten with new code as needed, allowing for updates, bug fixes, or functionality changes. -
What are some best practices for designing programmable PCBs?
Some best practices for designing programmable PCBs include: - Selecting appropriate components based on requirements
- Following proper PCB layout guidelines
- Providing adequate power supply and decoupling
- Implementing proper grounding and shielding
- Including programming and debugging interfaces
- Considering security measures for firmware protection
Conclusion
Programmable PCBs offer a flexible and customizable solution for a wide range of applications. By combining hardware and software, programmable PCBs enable designers to create intelligent systems that can be adapted and updated as needed. From embedded systems and IoT devices to robotics and automotive electronics, programmable PCBs are driving innovation and functionality across industries.
Designing and developing programmable PCBs requires a combination of hardware and software skills. Understanding the key components, such as microcontrollers, I/O interfaces, and power supply, is essential for creating robust and reliable designs. Programming these PCBs involves writing code, compiling, and uploading it to the microcontroller using PCB programmers.
While programmable PCBs offer numerous advantages, such as flexibility, cost-effectiveness, and rapid prototyping, they also come with challenges like complexity, power consumption, and security considerations. Designers must carefully evaluate these factors and follow best practices to ensure the success of their projects.
As technology advances, programmable PCBs will continue to evolve, offering even more powerful and efficient solutions. With the increasing demand for smart and connected devices, the role of programmable PCBs in shaping the future of electronics is undeniable. By leveraging the capabilities of these versatile boards, designers and engineers can create innovative products that push the boundaries of what is possible.
Leave a Reply