Table of Contents
- Introduction to Battery PCBs
- Functions of a Battery PCB
- Types of Battery PCBs
- Battery PCB Design Considerations
- Battery PCB Manufacturing Process
- Applications of Battery PCBs
- Future Trends in Battery PCB Technology
- Frequently Asked Questions (FAQ)
- Conclusion
Introduction to Battery PCBs
Battery PCBs are specialized printed circuit boards designed to interface with battery cells and facilitate the distribution of power to electronic devices. They play a crucial role in ensuring the safe and efficient operation of portable devices, such as smartphones, tablets, laptops, and wearable technology.
A typical battery PCB consists of a substrate material, usually made of FR-4 or other high-quality materials, with conductive traces, pads, and vias that connect the battery cells to the device’s main circuit board. The PCB also includes various components, such as protection circuits, fuel gauges, and charging controllers, which help optimize battery performance and extend its lifespan.
Functions of a Battery PCB
Battery PCBs perform several essential functions in electronic devices:
-
Power Distribution: The primary function of a battery PCB is to distribute power from the battery cells to the device’s main circuit board. The PCB’s conductive traces and vias ensure that the power is delivered efficiently and with minimal losses.
-
Battery Protection: Battery PCBs incorporate protection circuits that safeguard the battery cells from overcharging, overdischarging, short-circuiting, and other potential hazards. These protection features help prevent damage to the battery and the device, ensuring user safety and prolonging the battery’s lifespan.
-
Battery Monitoring: Many battery PCBs include fuel gauge circuits that monitor the battery’s state of charge (SoC), state of health (SoH), and other parameters. This information is crucial for accurately displaying the battery level to the user and for optimizing the device’s power management system.
-
Charging Control: Battery PCBs often feature charging controllers that regulate the charging process, ensuring that the battery cells are charged safely and efficiently. These controllers support various charging methods, such as constant current (CC), constant voltage (CV), and trickle charging, depending on the battery chemistry and application requirements.
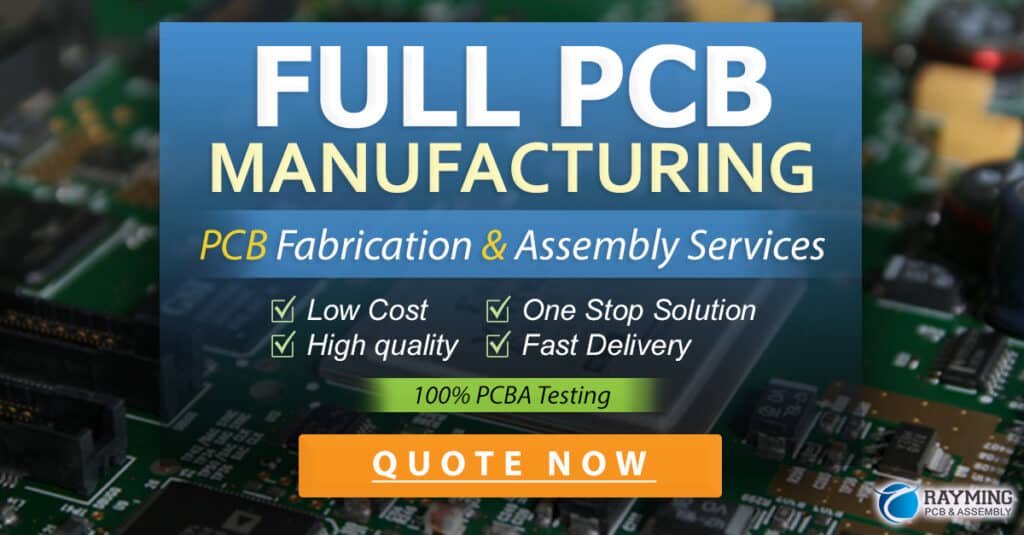
Types of Battery PCBs
Battery PCBs can be classified based on various factors, such as the number of layers, the type of battery cells supported, and the specific application requirements.
Number of Layers
-
Single-Layer PCBs: These PCBs have conductive traces on only one side of the substrate. They are simple, cost-effective, and suitable for low-complexity battery applications.
-
Double-Layer PCBs: These PCBs have conductive traces on both sides of the substrate, allowing for more complex routing and higher component density. They are commonly used in mid-range battery applications.
-
Multi-Layer PCBs: These PCBs have three or more conductive layers, enabling even more complex routing and higher component density. They are used in high-performance battery applications that require advanced features and compact designs.
Battery Cell Types
-
Li-ion Battery PCBs: These PCBs are designed to interface with lithium-ion battery cells, which are widely used in portable electronic devices due to their high energy density, low self-discharge, and long lifespan.
-
LiPo Battery PCBs: These PCBs are compatible with lithium-polymer battery cells, which offer higher energy density and flexibility compared to Li-ion cells. LiPo batteries are commonly used in applications that require thin and lightweight designs, such as smartphones and wearables.
-
NiMH Battery PCBs: These PCBs are designed for nickel-metal hydride battery cells, which are known for their high capacity, durability, and environmental friendliness. NiMH batteries are often used in high-drain devices, such as digital cameras and power tools.
-
Lead-Acid Battery PCBs: These PCBs are used with lead-acid battery cells, which are robust, low-cost, and commonly found in automotive and industrial applications.
Battery PCB Design Considerations
Designing a battery PCB involves several key considerations to ensure optimal performance, reliability, and safety:
-
Battery Chemistry: The PCB design must be tailored to the specific battery chemistry (e.g., Li-ion, LiPo, NiMH) to ensure compatibility and optimal performance.
-
Current and Voltage Ratings: The PCB’s conductive traces and components must be designed to handle the expected current and voltage levels without overheating or suffering from excessive voltage drops.
-
Protection Circuits: Incorporating appropriate protection circuits, such as overcharge, overdischarge, and short-circuit protection, is crucial for ensuring battery safety and longevity.
-
Thermal Management: Proper thermal management is essential to prevent overheating, which can degrade battery performance and lifespan. The PCB design should consider the placement of temperature sensors and the use of heat-dissipating materials or structures.
-
EMI/EMC Considerations: The PCB design must minimize electromagnetic interference (EMI) and ensure electromagnetic compatibility (EMC) with other components and devices.
-
Size and Form Factor: The battery PCB must be designed to fit within the available space in the device while accommodating the required number and arrangement of battery cells.
-
Manufacturing Feasibility: The PCB design must be optimized for manufacturability, considering factors such as minimum trace widths, clearances, and drill sizes, to ensure reliable and cost-effective production.
Battery PCB Manufacturing Process
The manufacturing process for battery PCBs involves several key steps:
-
PCB Design: The battery PCB is designed using specialized software, such as Altium Designer or Eagle, based on the specific requirements of the application and the selected battery chemistry.
-
Material Selection: The appropriate substrate material, typically FR-4 or a high-quality alternative, is selected based on the PCB’s performance and environmental requirements.
-
Fabrication: The PCB is fabricated using a combination of processes, including etching, drilling, plating, and solder mask application, to create the conductive traces, pads, and vias.
-
Component Placement: The various components, such as protection circuits, fuel gauges, and connectors, are placed onto the PCB using automated pick-and-place machines or manual assembly methods.
-
Soldering: The components are soldered onto the PCB using reflow soldering, wave soldering, or hand soldering techniques, depending on the component types and production volume.
-
Testing and Inspection: The assembled battery PCB undergoes rigorous testing and inspection to ensure proper functionality, reliability, and safety. This may include automated optical inspection (AOI), x-ray inspection, and functional testing.
-
Packaging and Shipping: The finished battery PCBs are packaged and shipped to the device manufacturer for integration into the final product.
Applications of Battery PCBs
Battery PCBs find applications in a wide range of portable electronic devices, including:
-
Smartphones and Tablets: Battery PCBs in these devices manage the power supply from high-capacity Li-ion or LiPo battery cells, enabling long battery life and fast charging capabilities.
-
Laptops: Battery PCBs in laptops handle the power distribution from multi-cell battery packs, providing sufficient power for the device’s processing, display, and peripheral components.
-
Wearable Technology: Battery PCBs in smartwatches, fitness trackers, and other wearable devices are designed to be compact, lightweight, and efficient, ensuring long battery life in a small form factor.
-
Medical Devices: Battery PCBs power various portable medical devices, such as blood glucose monitors, heart rate monitors, and drug delivery systems, ensuring reliable and safe operation.
-
Power Tools: Battery PCBs in cordless power tools, such as drills and saws, manage the power supply from high-capacity battery packs, enabling high-performance operation and fast charging.
-
Electric Vehicles: Battery PCBs play a crucial role in electric vehicle battery management systems, monitoring and balancing the large battery packs to ensure optimal performance, safety, and longevity.
Future Trends in Battery PCB Technology
As the demand for portable electronic devices continues to grow, battery PCB technology is evolving to meet the increasing requirements for performance, efficiency, and safety:
-
Advanced Materials: Researchers are exploring new substrate materials, such as high-temperature laminates and flexible polymers, to enable battery PCBs with improved thermal stability, mechanical flexibility, and reduced thickness.
-
Integrated Electronics: The integration of more advanced electronics, such as battery fuel gauges, protection circuits, and power management ICs, directly onto the battery PCB is becoming increasingly common, enabling more compact and efficient designs.
-
Wireless Charging: Battery PCBs are being designed to support wireless charging capabilities, allowing devices to be charged without the need for physical connectors, improving convenience and durability.
-
Smart Battery Management: The development of smart battery management systems, which utilize advanced algorithms and machine learning techniques, is enabling more accurate state of charge estimation, improved safety features, and optimized charging profiles for extended battery life.
-
Sustainable Manufacturing: There is a growing emphasis on sustainable manufacturing practices in the PCB industry, including the use of eco-friendly materials, reduced waste generation, and improved recycling processes, to minimize the environmental impact of battery PCB production.
Frequently Asked Questions (FAQ)
-
What is the difference between a battery PCB and a regular PCB?
A battery PCB is specifically designed to interface with battery cells and manage power distribution, protection, and monitoring functions. In contrast, a regular PCB is a general-purpose board that can be used for various electronic applications. -
Can a battery PCB be replaced if it fails?
In most cases, a faulty battery PCB can be replaced by a skilled technician. However, the replacement process may be complex and time-consuming, depending on the device and the specific PCB design. -
How does a battery PCB protect the battery cells?
A battery PCB incorporates various protection circuits, such as overcharge, overdischarge, and short-circuit protection, which monitor the battery’s voltage, current, and temperature. These circuits can detect abnormal conditions and take appropriate actions, such as cutting off the power supply or triggering a safety shutdown, to prevent damage to the battery and the device. -
What factors influence the lifespan of a battery PCB?
The lifespan of a battery PCB depends on several factors, including the quality of the materials used, the manufacturing process, the operating environment, and the usage patterns of the device. Proper design, manufacturing, and usage can help extend the lifespan of a battery PCB. -
Are battery PCBs recyclable?
Yes, battery PCBs can be recycled to recover valuable materials, such as copper, gold, and other metals. However, the recycling process must be carried out by specialized facilities to ensure proper handling and disposal of the various components and materials.
Conclusion
Battery PCBs are essential components in modern portable electronic devices, enabling efficient power distribution, protection, and management. They come in various types and designs to accommodate different battery chemistries, application requirements, and form factors.
Designing and manufacturing battery PCBs involves several key considerations, including battery compatibility, current and voltage ratings, protection features, thermal management, and manufacturing feasibility. As the demand for portable devices continues to grow, battery PCB technology is evolving to meet the increasing requirements for performance, efficiency, and safety.
By understanding the functions, types, design considerations, and manufacturing processes of battery PCBs, engineers and manufacturers can develop more advanced and reliable portable electronic devices that meet the ever-changing needs of consumers.
Component | Function |
---|---|
Substrate Material | Provides a base for the conductive traces and components |
Conductive Traces | Distribute power and signals between components |
Pads and Vias | Allow for component attachment and inter-layer connections |
Protection Circuits | Safeguard battery cells from overcharge, overdischarge, and short-circuit |
Fuel Gauge Circuits | Monitor battery state of charge, state of health, and other parameters |
Charging Controllers | Regulate the charging process for safe and efficient battery charging |
Connectors | Enable connection between the battery PCB and the main device PCB |
Leave a Reply