Key Features of IMS PCBs
Thermal Management
The primary advantage of an IMS PCB is its excellent thermal management capabilities. The metal substrate, typically aluminum or copper, acts as a heat sink, efficiently transferring heat away from the components mounted on the board. This helps to maintain a stable operating temperature, preventing overheating and ensuring optimal performance of the electronic devices.
Dielectric Layer
Between the metal substrate and the copper circuit layer, there is a thin dielectric layer that provides electrical insulation while allowing efficient heat transfer. The dielectric layer is typically made of a thermally conductive material, such as ceramic-filled epoxy or polyimide. The thickness and thermal conductivity of the dielectric layer play a crucial role in determining the overall thermal performance of the IMS PCB.
Circuit Layer
The copper circuit layer on an IMS PCB is similar to that of a standard PCB, with conductive traces, pads, and vias. However, the circuit layer on an IMS PCB is usually thinner compared to FR-4 PCBs, as the primary focus is on heat dissipation rather than electrical performance. The circuit layer can be single-sided or double-sided, depending on the complexity of the design and the application requirements.
Advantages of IMS PCBs
- Enhanced thermal management
- Improved reliability and longevity of electronic components
- Reduced size and weight compared to traditional PCBs with separate heat sinks
- Simplified assembly process, as the metal substrate serves as both a heat sink and a structural support
- Lower overall system cost due to reduced cooling requirements and improved efficiency
Applications of IMS PCBs
IMS PCBs find applications in various industries and products where thermal management is critical. Some common applications include:
- Power electronics: IGBT modules, power converters, motor drives
- LED lighting: High-power LED arrays, LED drivers
- Automotive electronics: Engine control units, power steering modules, headlight systems
- Telecommunications: High-power RF amplifiers, base station equipment
- Industrial automation: Motion control systems, power supplies
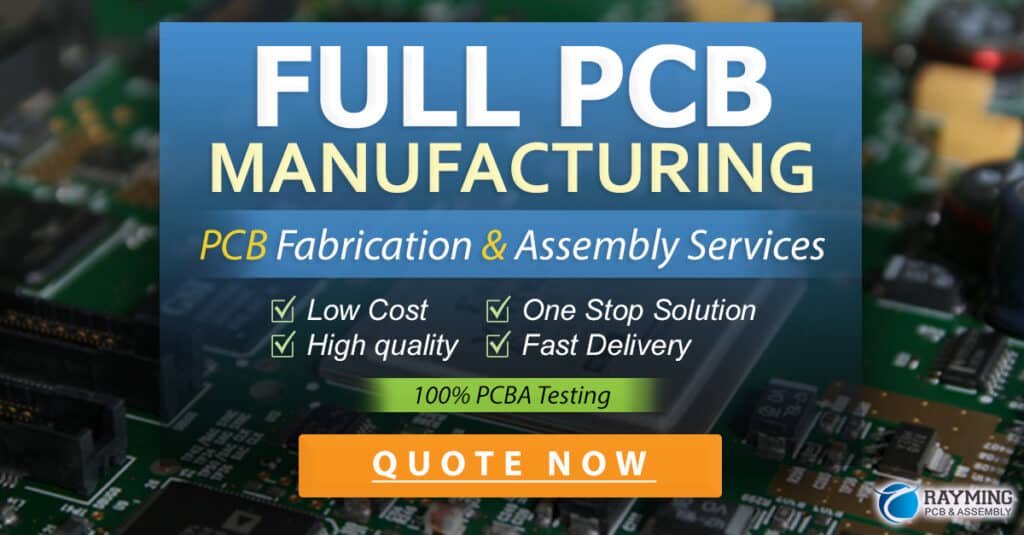
Manufacturing Process of IMS PCBs
The manufacturing process of IMS PCBs differs from that of standard FR-4 PCBs due to the presence of the metal substrate and the dielectric layer. The main steps involved in the manufacturing of IMS PCBs are:
- Substrate preparation: The metal substrate, usually aluminum or copper, is cleaned and surface-treated to ensure proper adhesion of the dielectric layer.
- Dielectric layer application: The dielectric material is applied to the metal substrate using techniques such as screen printing, roller coating, or lamination. The thickness of the dielectric layer is carefully controlled to achieve the desired thermal and electrical properties.
- Circuit layer manufacturing: The copper circuit layer is fabricated using standard PCB manufacturing techniques, such as photolithography, etching, and plating. The circuit layer is then laminated onto the dielectric layer.
- Finishing and assembly: The IMS PCB undergoes final finishing processes, such as solder mask application and surface finishing. Components are then assembled onto the board using standard SMT or through-hole assembly techniques.
Thermal Performance of IMS PCBs
The thermal performance of an IMS PCB is determined by several factors, including the thermal conductivity of the metal substrate, the thickness and thermal conductivity of the dielectric layer, and the design of the copper circuit layer. The following table compares the thermal conductivity of common materials used in IMS PCBs:
Material | Thermal Conductivity (W/mK) |
---|---|
Aluminum (alloy 5052) | 138 |
Copper (C10200) | 385 |
Ceramic-filled epoxy | 1-4 |
Polyimide | 0.2-0.5 |
To optimize the thermal performance of an IMS PCB, designers must carefully consider the layout of the copper circuit layer, ensuring that heat-generating components are placed close to the metal substrate and that there are sufficient thermal vias to facilitate heat transfer. Thermal simulations and modeling tools are often used to analyze the thermal behavior of the PCB and make necessary design adjustments.
Comparing IMS PCBs with Traditional FR-4 PCBs
Parameter | IMS PCB | FR-4 PCB |
---|---|---|
Thermal conductivity | High (1-4 W/mK) | Low (0.3-0.4 W/mK) |
Heat dissipation | Excellent | Poor |
Dielectric thickness | Thin (50-200 μm) | Thick (0.5-1.5 mm) |
Copper thickness | Thin (18-70 μm) | Thick (18-105 μm) |
Mechanical strength | High (metal substrate) | Moderate (glass-epoxy) |
Cost | Higher than FR-4 | Lower than IMS |
Applications | Power electronics, LEDs | General-purpose electronics |
Frequently Asked Questions (FAQ)
1. What is the difference between an IMS PCB and a standard PCB?
An IMS PCB has a metal substrate (usually aluminum or copper) that acts as a built-in heat sink, providing superior thermal management compared to a standard FR-4 PCB. The metal substrate is electrically insulated from the copper circuit layer by a thin dielectric layer.
2. What are the main advantages of using IMS PCBs?
The main advantages of using IMS PCBs include enhanced thermal management, improved reliability and longevity of electronic components, reduced size and weight, simplified assembly process, and lower overall system cost due to reduced cooling requirements.
3. What industries commonly use IMS PCBs?
IMS PCBs are commonly used in industries and applications where thermal management is critical, such as power electronics, LED lighting, automotive electronics, telecommunications, and industrial automation.
4. How does the thermal conductivity of the dielectric layer affect the performance of an IMS PCB?
The thermal conductivity of the dielectric layer directly impacts the overall thermal performance of an IMS PCB. A higher thermal conductivity allows for more efficient heat transfer from the copper circuit layer to the metal substrate, resulting in better heat dissipation and lower operating temperatures.
5. Can IMS PCBs be manufactured with multiple copper layers?
Yes, IMS PCBs can be manufactured with multiple copper layers, although it is less common compared to single-layer or double-layer designs. Multi-layer IMS PCBs are used in applications that require more complex circuitry while still maintaining good thermal management properties.
Conclusion
IMS PCBs offer a unique solution for applications that demand efficient thermal management and heat dissipation. By combining a metal substrate with a thin dielectric layer and a copper circuit layer, IMS PCBs provide superior thermal performance compared to traditional FR-4 PCBs. This makes them ideal for use in power electronics, LED lighting, automotive systems, and other applications where maintaining stable operating temperatures is crucial. As electronic devices continue to push the boundaries of performance and power density, the importance of IMS PCBs in enabling reliable and efficient operation will only continue to grow.
Leave a Reply