What is a PCB?
A PCB is a flat board made of insulating material, such as fiberglass or plastic, with conductive tracks, pads, and other features etched from copper sheets laminated onto the board. It is used to mechanically support and electrically connect electronic components using conductive pathways, tracks, or signal traces.
Tools needed for drawing a PCB
Before we begin drawing a PCB, let’s take a look at the tools you will need:
- PCB design software (e.g., KiCad, Eagle, Altium Designer)
- Schematic capture software (often included with the PCB design software)
- Component libraries
- A computer with sufficient processing power and memory
Step 1: Create a schematic diagram
The first step in drawing a PCB is to create a schematic diagram. A schematic is a graphical representation of the electrical connections between components in a circuit. It uses standardized symbols to represent components and lines to represent the connections between them.
To create a schematic:
- Open your schematic capture software.
- Place the required components on the schematic sheet.
- Connect the components using wires or nets.
- Assign unique identifiers to each component (e.g., R1 for the first resistor, C1 for the first capacitor).
- Specify the values or ratings of each component.
Schematic diagram best practices
- Keep the schematic organized and easy to read.
- Use consistent labeling and numbering for components.
- Group related components together.
- Use buses for common signals like power and ground.
- Add notes and comments to clarify the purpose of specific sections of the circuit.
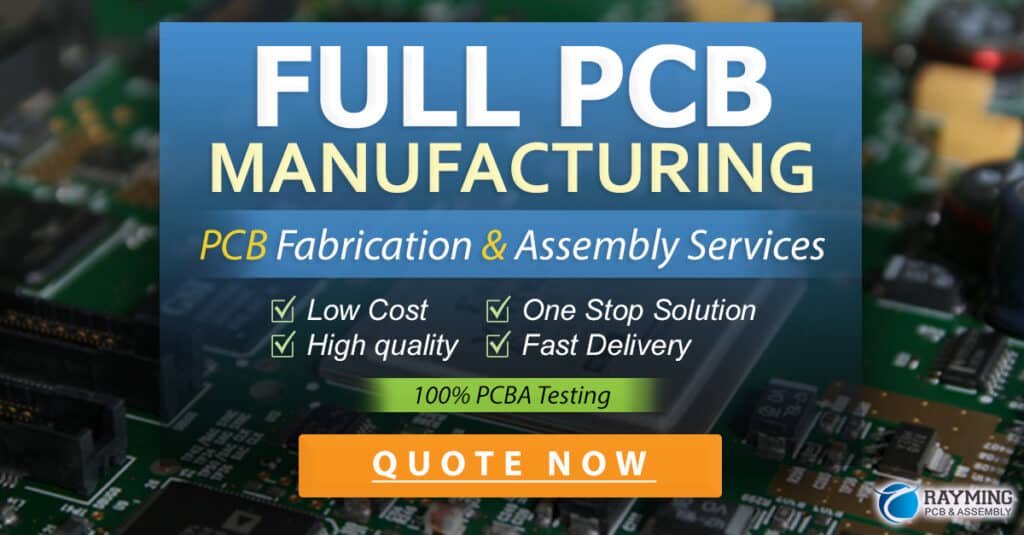
Step 2: Design the PCB layout
Once you have created the schematic, you can move on to designing the PCB layout. The PCB layout is a physical representation of the schematic, showing the actual placement of components and the routing of the connections between them.
To design the PCB layout:
- Open your PCB design software.
- Import the schematic into the PCB layout editor.
- Define the board dimensions and shape.
- Place the components on the board, considering factors such as size, heat dissipation, and signal integrity.
- Route the connections between the components using copper traces.
- Add power and ground planes if necessary.
- Perform a design rule check (DRC) to ensure that your design meets the manufacturing requirements.
PCB layout best practices
- Keep the layout organized and easy to understand.
- Minimize the length of traces to reduce signal integrity issues.
- Avoid sharp angles in traces to reduce signal reflections.
- Provide adequate spacing between components and traces to avoid interference.
- Use ground planes to reduce noise and improve signal integrity.
- Consider the manufacturing capabilities of your PCB fabricator when designing the layout.
Step 3: Generate manufacturing files
After completing the PCB layout, you need to generate the necessary manufacturing files. These files are used by the PCB fabricator to manufacture the physical board.
The most common manufacturing files are:
- Gerber files: These files contain the information needed to fabricate the copper layers, solder mask, and silkscreen of the PCB.
- Drill files: These files specify the location, size, and type of holes to be drilled in the PCB.
- Pick and place files: These files provide the location and orientation of each component on the PCB for automated assembly.
- Bill of Materials (BOM): This file lists all the components used in the PCB, along with their quantities, part numbers, and other relevant information.
PCB design considerations
When drawing a PCB circuit, there are several key factors to consider to ensure the best performance and reliability of your design:
Component placement
- Place components in a logical order based on their function in the circuit.
- Keep related components close together to minimize trace lengths.
- Consider the size and shape of components when placing them on the board.
- Ensure adequate spacing between components to avoid physical interference and thermal issues.
Signal integrity
- Route high-speed signals first and keep their traces as short as possible.
- Avoid routing high-speed signals parallel to each other to minimize crosstalk.
- Use ground planes to provide a low-impedance return path for signals.
- Consider using differential signaling for high-speed signals to reduce noise and electromagnetic interference (EMI).
Power management
- Provide adequate power and ground connections to all components.
- Use wide traces for power and ground connections to minimize resistance and voltage drop.
- Decouple power supplies using capacitors placed close to the power pins of components.
- Use separate power and ground planes for analog and digital sections of the circuit to minimize noise.
Manufacturability
- Ensure that your design meets the manufacturing capabilities of your PCB fabricator.
- Adhere to the minimum trace width and spacing requirements.
- Provide adequate clearance around holes and board edges.
- Use standard component sizes and footprints when possible.
PCB design software
There are several PCB design software options available, ranging from free and open-source to commercial and enterprise-level solutions. Some popular PCB design software include:
- KiCad (free and open-source)
- Eagle (free for non-commercial use, paid versions available)
- Altium Designer (commercial)
- Cadence OrCAD (commercial)
- Mentor Graphics PADS (commercial)
Each software has its own strengths and weaknesses, and the choice ultimately depends on your specific needs, budget, and experience level.
Frequently Asked Questions (FAQ)
1. What is the difference between a schematic and a PCB layout?
A schematic is a graphical representation of the electrical connections between components in a circuit, while a PCB layout is a physical representation of the schematic, showing the actual placement of components and the routing of the connections between them.
2. What are the most common PCB manufacturing files?
The most common PCB manufacturing files are Gerber files (for fabricating copper layers, solder mask, and silkscreen), drill files (for specifying hole locations and sizes), pick and place files (for automated component assembly), and the Bill of Materials (BOM) which lists all the components used in the PCB.
3. What is a design rule check (DRC) in PCB design?
A design rule check (DRC) is an automated process that checks your PCB design against a set of predefined rules to ensure that it meets the manufacturing requirements. These rules include minimum trace width and spacing, hole sizes, and clearances.
4. What is the purpose of a ground plane in a PCB?
A ground plane serves several purposes in a PCB, including providing a low-impedance return path for signals, reducing noise and electromagnetic interference (EMI), and improving signal integrity.
5. Can I design a PCB without using specialized software?
While it is theoretically possible to design a simple PCB by hand, using specialized PCB design software is highly recommended for all but the most basic designs. PCB design software automates many of the tedious and error-prone tasks involved in PCB design, such as component placement, trace routing, and design rule checking.
Conclusion
Drawing a PCB circuit involves several steps, including creating a schematic diagram, designing the PCB layout, and generating manufacturing files. To ensure the best performance and reliability of your design, consider factors such as component placement, signal integrity, power management, and manufacturability.
By following best practices and using appropriate PCB design software, you can create high-quality PCBs that meet your specific requirements. As with any skill, practice and experience will help you become proficient in PCB design.
Remember to consult with your PCB fabricator early in the design process to ensure that your design is compatible with their manufacturing capabilities. This can save you time and money by avoiding design revisions later in the process.
With patience, attention to detail, and a willingness to learn, anyone can master the art of drawing PCB circuits.
Step | Description |
---|---|
1 | Create a schematic diagram |
2 | Design the PCB layout |
3 | Generate manufacturing files |
PCB Design Software | Type |
---|---|
KiCad | Free and open-source |
Eagle | Free for non-commercial use, paid versions available |
Altium Designer | Commercial |
Cadence OrCAD | Commercial |
Mentor Graphics PADS | Commercial |
Leave a Reply