Introduction
In the world of printed circuit board (PCB) manufacturing, a stencil is an essential tool used to apply solder paste onto the PCB pads. The stencil is a thin sheet of metal, usually stainless steel, with laser-cut openings that correspond to the pads on the PCB. The openings allow for precise application of solder paste, ensuring that the correct amount is deposited on each pad. This process is crucial for achieving reliable and high-quality solder joints during the assembly of surface mount components.
What is solder paste?
Solder paste is a mixture of tiny solder particles suspended in a flux medium. The solder particles are typically made of a tin-lead alloy, although lead-free alternatives are becoming increasingly common due to environmental and health concerns. The flux medium serves to remove oxides from the metal surfaces and promote proper wetting of the solder during the reflow process.
Why use a stencil for applying solder paste?
Using a stencil to apply solder paste offers several advantages over other methods, such as manual application or screen printing:
-
Precision: Stencils allow for precise control over the amount and placement of solder paste on each pad. This is especially important for fine-pitch components and high-density PCB layouts.
-
Consistency: By using a stencil, the solder paste application process is highly repeatable, ensuring consistent results across multiple PCBs.
-
Efficiency: Stencil printing is a fast and efficient method for applying solder paste to a large number of PCBs, making it ideal for high-volume production.
Stencil materials and fabrication
Stencil materials
Stencils are typically made from stainless steel, which offers several advantages:
-
Durability: Stainless steel is a tough and wear-resistant material, allowing for a long stencil life and the ability to withstand multiple print cycles.
-
Precision: Stainless steel can be laser-cut with high precision, ensuring accurate openings that match the PCB pad layout.
-
Cleanliness: Stainless steel is easy to clean and maintain, which is important for preventing contamination of the solder paste.
In some cases, other materials, such as nickel or polyimide, may be used for specialized applications or for creating step stencils (more on this later).
Stencil fabrication process
The stencil fabrication process typically involves the following steps:
-
Design: The stencil design is created based on the PCB layout, taking into account factors such as pad size, shape, and pitch.
-
Laser cutting: The stencil is laser-cut from a sheet of stainless steel using a high-precision laser cutting machine. The laser follows the designed pattern, creating openings that correspond to the PCB pads.
-
Cleaning: After cutting, the stencil is cleaned to remove any debris or contamination.
-
Inspection: The stencil is inspected for accuracy and quality, ensuring that the openings match the PCB layout and meet the required specifications.
Stencil design considerations
Aperture size and shape
The size and shape of the stencil apertures (openings) play a critical role in determining the amount of solder paste deposited on each pad. Some key considerations include:
-
Area ratio: The area ratio is the ratio of the aperture opening area to the aperture wall area. A higher area ratio allows for better solder paste release and reduces the likelihood of clogging.
-
Aperture reduction: In some cases, the aperture size may need to be slightly reduced compared to the pad size to account for solder paste slumping and to prevent bridging between adjacent pads.
-
Aperture shape: The shape of the aperture can affect the solder paste deposit. Common shapes include square, circular, and home plate (a combination of square and circular).
Stencil thickness
The thickness of the stencil determines the volume of solder paste deposited on each pad. Thicker stencils deposit more solder paste, while thinner stencils deposit less. The optimal stencil thickness depends on factors such as the component pitch, pad size, and desired solder joint profile.
Typical stencil thicknesses range from 0.1 mm to 0.2 mm (4 to 8 mils), with thicker stencils used for larger components and higher-volume solder joints.
Step stencils
In some cases, a single stencil thickness may not be suitable for all components on a PCB. For example, a PCB may have a mix of fine-pitch and large components, each requiring a different solder paste volume. In such cases, a step stencil can be used.
A step stencil has multiple sections with different thicknesses, allowing for different solder paste volumes to be deposited on different areas of the PCB. Step stencils can be created by laminating multiple stencil layers or by using a special electroforming process.
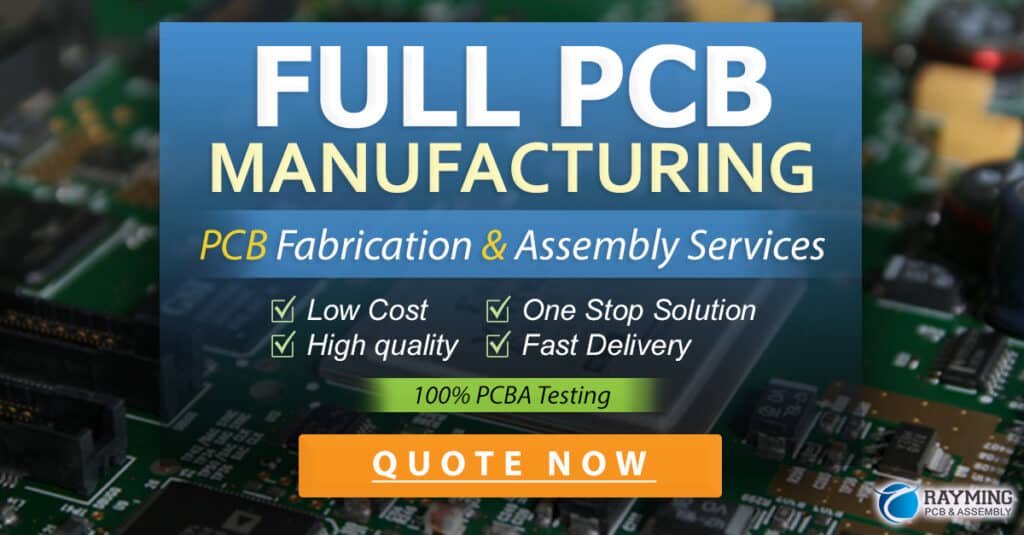
Stencil printing process
Solder paste selection
Selecting the appropriate solder paste is crucial for achieving good printing results and reliable solder joints. Factors to consider when choosing a solder paste include:
-
Alloy composition: The solder alloy should be compatible with the component finishes and the desired solder joint properties.
-
Particle size: The solder particle size should be appropriate for the stencil aperture size and the desired solder joint profile. Smaller particles are typically used for fine-pitch components.
-
Flux type: The flux should be compatible with the PCB surface finish and the soldering process. Different flux types (e.g., rosin, no-clean, water-soluble) have different properties and cleaning requirements.
Stencil alignment
Proper alignment of the stencil to the PCB is essential for accurate solder paste deposition. Stencil printers use various methods for aligning the stencil, including:
-
Fiducial recognition: Fiducials are reference marks on the PCB and stencil that are used for alignment. The printer uses a vision system to locate the fiducials and adjust the stencil position accordingly.
-
Edge detection: Some printers use the edges of the PCB as a reference for alignment, eliminating the need for fiducials.
-
Pin alignment: In some cases, alignment pins on the stencil and corresponding holes on the PCB are used for manual alignment.
Print settings
Several print settings can affect the quality and consistency of the solder paste deposition:
-
Print speed: The speed at which the squeegee moves across the stencil. Slower speeds typically result in better paste deposition and fewer defects.
-
Print pressure: The pressure applied by the squeegee to the stencil. Higher pressure can improve paste transfer but may also cause bleeding or smearing.
-
Separation speed: The speed at which the stencil is lifted off the PCB after printing. A slower separation speed can help prevent paste from sticking to the stencil.
-
Snap-off distance: The distance between the stencil and PCB during printing. A smaller snap-off distance can improve print definition but may also increase the risk of smearing.
Cleaning and maintenance
Regular cleaning and maintenance of the stencil and printer are essential for ensuring consistent and high-quality prints. Key considerations include:
-
Understencil cleaning: The underside of the stencil should be cleaned regularly to prevent paste buildup and clogging of apertures. Various cleaning methods can be used, such as manual wiping, automated understencil cleaners, or ultrasonic cleaning.
-
Stencil storage: When not in use, stencils should be stored in a clean, dry environment to prevent contamination and damage.
-
Printer maintenance: Regular maintenance of the printer, including cleaning of the squeegee blades and calibration of the alignment system, is important for ensuring consistent performance.
Troubleshooting common stencil printing issues
Insufficient or excessive solder paste
Insufficient or excessive solder paste deposition can lead to poor solder joint quality and reliability issues. Common causes and solutions include:
-
Stencil thickness: If the stencil is too thin, insufficient paste may be deposited. If too thick, excessive paste may be deposited. Adjust the stencil thickness as needed.
-
Aperture size: If the apertures are too small, insufficient paste may be deposited. If too large, excessive paste may be deposited. Adjust the aperture size as needed.
-
Print settings: Adjust the print speed, pressure, and separation speed to optimize paste deposition.
Solder paste bridging
Solder paste bridging occurs when paste from adjacent apertures connects, potentially causing short circuits. Common causes and solutions include:
-
Aperture design: Ensure that the aperture size and spacing are appropriate for the pad layout and pitch.
-
Stencil quality: Inspect the stencil for damage or contamination that may cause bridging.
-
Print settings: Adjust the print settings, particularly the print pressure and separation speed, to minimize bridging.
Poor solder paste release
Poor solder paste release occurs when paste sticks to the stencil apertures, resulting in incomplete or inconsistent deposition. Common causes and solutions include:
-
Aperture design: Ensure that the aperture walls are smooth and have a sufficient area ratio for good paste release.
-
Stencil quality: Inspect the stencil for wear or damage that may affect paste release.
-
Solder paste properties: Select a solder paste with good printability and release characteristics.
-
Print settings: Adjust the print settings, particularly the separation speed, to improve paste release.
FAQ
1. How often should I clean my stencil?
A: The frequency of stencil cleaning depends on factors such as the solder paste type, print volume, and environment. As a general guideline, understencil cleaning should be performed every 1-4 hours of continuous printing or between print jobs. More frequent cleaning may be necessary for high-volume production or when using more viscous solder pastes.
2. How long do stencils typically last?
A: The lifespan of a stencil depends on factors such as the material, thickness, and usage. Stainless steel stencils can typically last for 50,000 to 100,000 print cycles with proper care and maintenance. However, the actual lifespan may vary depending on the specific application and printing conditions.
3. Can I reuse a stencil for different PCB designs?
A: In general, a stencil is designed for a specific PCB layout and cannot be reused for different designs. However, if the new PCB design has an identical pad layout, the same stencil may be used. It is important to ensure that the stencil apertures match the pad size and spacing of the new design.
4. How do I store my stencils when not in use?
A: Stencils should be stored in a clean, dry environment to prevent contamination and damage. Store stencils vertically in a rack or on a flat surface, ensuring that they do not touch each other. Avoid exposing stencils to extreme temperatures or humidity, as this can cause warping or corrosion.
5. Can I modify a stencil if I need to change the aperture design?
A: In most cases, modifying a stencil is not recommended, as it can affect the precision and quality of the solder paste deposition. If changes to the aperture design are necessary, it is best to have a new stencil fabricated to ensure accurate and consistent results. However, in some situations, minor modifications may be possible using laser cutting or chemical etching techniques.
Conclusion
Stencils play a vital role in the PCB assembly process, enabling precise and consistent solder paste deposition. By understanding the fundamentals of stencil design, fabrication, and printing, engineers and technicians can optimize the solder paste application process and achieve high-quality solder joints.
Key considerations for successful stencil printing include selecting the appropriate stencil material and thickness, designing apertures with the proper size and shape, and optimizing print settings such as speed, pressure, and separation speed. Regular cleaning and maintenance of the stencil and printer are also essential for ensuring consistent and reliable results.
By following best practices and troubleshooting common issues, manufacturers can leverage the benefits of stencil printing to produce high-quality, reliable PCBs efficiently and cost-effectively.
Leave a Reply