Introduction to Annular Rings in PCB Design
In the world of printed circuit board (PCB) design, the annular ring plays a crucial role in ensuring the reliability and functionality of the board. An annular ring, also known as a pad or land, is a circular copper area that surrounds a drilled hole on a PCB. The primary purpose of the annular ring is to provide a secure electrical and mechanical connection between the component lead and the copper trace on the board.
The Importance of Annular Rings
Annular rings serve several important functions in PCB design:
- Electrical connectivity: The annular ring ensures a reliable electrical connection between the component lead and the copper trace on the PCB.
- Mechanical stability: The annular ring provides mechanical support to the component, preventing it from shifting or becoming dislodged during the soldering process or in use.
- Manufacturing tolerance: Annular rings help accommodate manufacturing tolerances, such as drill bit wandering or misalignment, ensuring that the component lead still makes a proper connection with the copper trace.
Annular Ring Design Considerations
When designing annular rings for your PCB, there are several factors to consider to ensure optimal performance and reliability.
Annular Ring Size
The size of the annular ring is determined by the drill hole size and the required copper-to-hole clearance. The copper-to-hole clearance is the minimum distance between the edge of the drilled hole and the edge of the annular ring. This clearance is essential to prevent the drill bit from damaging the annular ring during the drilling process.
The minimum annular ring size can be calculated using the following formula:
Minimum Annular Ring = (Drill Hole Diameter / 2) + Copper-to-Hole Clearance
For example, if the drill hole diameter is 0.8mm and the required copper-to-hole clearance is 0.2mm, the minimum annular ring size would be:
Minimum Annular Ring = (0.8mm / 2) + 0.2mm = 0.6mm
It is important to note that the minimum annular ring size may vary depending on the PCB manufacturer’s capabilities and the specific requirements of your design.
Annular Ring Shape
While annular rings are typically circular, there are instances where other shapes may be used to accommodate specific design requirements. Some common variations include:
- Oblong or oval annular rings: These shapes are used when the component lead is not perfectly aligned with the drilled hole, allowing for some movement or adjustment during the soldering process.
- Teardrop annular rings: Teardrop-shaped annular rings are used to reduce stress concentrations at the junction between the annular ring and the copper trace, improving the mechanical strength of the connection.
- Rounded rectangular annular rings: These shapes are sometimes used for surface-mount components to provide a larger contact area for the component lead.
Annular Ring Placement
The placement of annular rings on a PCB is determined by the component layout and the routing of the copper traces. When placing annular rings, consider the following:
- Component orientation: Ensure that the annular rings are aligned with the component leads and that there is sufficient space between adjacent components to accommodate the annular rings.
- Trace routing: Route the copper traces to the annular rings in a way that minimizes the risk of signal interference and ensures proper electrical connectivity.
- Manufacturing constraints: Consider the limitations of your PCB manufacturer, such as minimum annular ring size and spacing requirements, when placing annular rings on your board.
Annular Ring Manufacturing Processes
The manufacturing of annular rings involves several processes that ensure the accurate and reliable creation of these critical PCB features.
Drilling
The first step in creating annular rings is drilling the holes in the PCB substrate. This process is typically performed using a computer-controlled drilling machine, which ensures precise hole placement and size. The drill bit size is selected based on the required hole diameter and the thickness of the PCB substrate.
Plating
After drilling, the holes are plated with a conductive material, usually copper, to create a continuous electrical connection between the top and bottom layers of the PCB. This process is known as through-hole plating and is essential for creating reliable annular rings.
The plating process involves several steps:
- Cleaning: The drilled holes are cleaned to remove any debris or contaminants that may interfere with the plating process.
- Deposition: A thin layer of copper is deposited onto the walls of the drilled holes using an electroless plating process. This layer acts as a seed for the subsequent electrolytic plating step.
- Electrolytic plating: The PCB is immersed in an electrolytic plating bath, where an electric current is applied to deposit a thicker layer of copper onto the walls of the drilled holes and the annular rings.
- Inspection: The plated holes are inspected to ensure that the plating is uniform and meets the required thickness and quality standards.
Etching
After the plating process, the unwanted copper on the PCB surface is removed through an etching process. This process involves applying a photoresist layer to the PCB, exposing it to UV light through a photomask, and then developing the photoresist to reveal the desired copper patterns, including the annular rings.
The exposed copper is then removed using a chemical etching solution, typically an acidic solution containing cupric chloride or ferric chloride. The remaining photoresist is then stripped away, leaving the final copper pattern, including the annular rings, on the PCB surface.
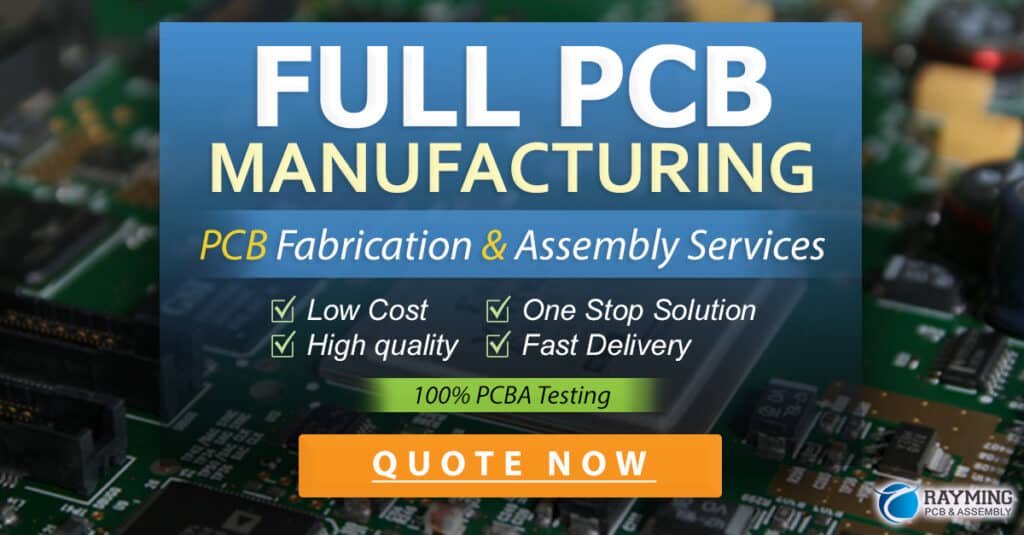
Annular Ring Quality Control and Inspection
To ensure the reliability and functionality of the annular rings on a PCB, it is essential to implement a rigorous quality control and inspection process. This process includes several key steps:
Visual Inspection
A visual inspection of the annular rings is performed to identify any obvious defects, such as:
- Missing or incomplete annular rings
- Annular rings with insufficient copper coverage
- Annular rings with excessive copper buildup or protrusions
- Misaligned or off-center annular rings
Visual inspection can be performed manually by trained operators or using automated optical inspection (AOI) systems that use high-resolution cameras and image processing algorithms to detect defects.
Electrical Testing
Electrical testing is performed to ensure that the annular rings provide a reliable electrical connection between the component leads and the copper traces on the PCB. This testing can include:
- Continuity testing: Verifying that there is a continuous electrical path between the annular ring and the corresponding copper trace.
- Resistance testing: Measuring the resistance between the annular ring and the copper trace to ensure that it falls within acceptable limits.
- Insulation resistance testing: Measuring the resistance between adjacent annular rings to ensure that there is no unintended electrical connection or leakage.
Electrical testing can be performed using automated test equipment (ATE) or manual test methods, such as using a multimeter or continuity tester.
Microsectioning
Microsectioning is a destructive testing method used to evaluate the quality of the plating inside the drilled holes and the annular rings. This process involves cutting a cross-section of the PCB through the annular ring and examining it under a microscope.
Microsectioning can reveal defects such as:
- Insufficient plating thickness
- Voids or discontinuities in the plating
- Poor adhesion between the plating and the PCB substrate
- Cracks or other mechanical damage to the annular ring
While microsectioning is a destructive testing method, it provides valuable insights into the quality of the annular rings and can help identify process improvements needed to enhance the reliability of the PCB.
Annular Ring Failure Modes and Prevention
Despite the best efforts in design, manufacturing, and quality control, annular rings can still fail due to various factors. Understanding these failure modes and implementing preventive measures can help minimize the risk of annular ring failures.
Common Annular Ring Failure Modes
- Mechanical stress: Annular rings can be subjected to mechanical stress during the assembly process or in use, leading to cracks, fractures, or complete separation from the PCB substrate.
- Thermal stress: Temperature fluctuations during the soldering process or in use can cause the annular ring to expand and contract, leading to mechanical stress and potential failure.
- Chemical attack: Exposure to harsh chemicals, such as cleaning agents or flux residues, can degrade the copper plating and weaken the annular ring.
- Corrosion: Moisture and other environmental factors can cause the copper plating to corrode, leading to a weakened or broken connection.
Prevention Strategies
To minimize the risk of annular ring failures, consider the following prevention strategies:
- Robust design: Ensure that the annular ring design meets the required mechanical and electrical specifications, with sufficient copper coverage and clearance from the drilled hole.
- Material selection: Choose PCB substrate materials and copper plating processes that are compatible with the intended application and environment.
- Controlled manufacturing: Implement strict process controls during the drilling, plating, and etching processes to ensure consistent and high-quality annular rings.
- Thorough inspection: Perform regular visual, electrical, and microsectioning inspections to identify and address any potential annular ring defects early in the manufacturing process.
- Proper handling and assembly: Follow best practices for handling, storage, and assembly of PCBs to minimize the risk of mechanical damage to the annular rings.
- Environmental protection: Apply conformal coatings or other protective measures to shield the annular rings from moisture, chemicals, and other environmental factors that can cause corrosion or degradation.
By understanding the failure modes and implementing appropriate prevention strategies, designers and manufacturers can significantly reduce the risk of annular ring failures and ensure the long-term reliability of their PCBs.
Frequently Asked Questions (FAQ)
- What is the difference between an annular ring and a pad?
-
An annular ring and a pad are often used interchangeably, but technically, an annular ring specifically refers to the circular copper area surrounding a drilled hole, while a pad can refer to any copper area on a PCB, including surface-mount pads and other shapes.
-
How do I calculate the minimum annular ring size for my PCB?
-
The minimum annular ring size can be calculated using the formula: Minimum Annular Ring = (Drill Hole Diameter / 2) + Copper-to-Hole Clearance. The copper-to-hole clearance is determined by your PCB manufacturer’s capabilities and the specific requirements of your design.
-
What is the purpose of through-hole plating in annular ring manufacturing?
-
Through-hole plating creates a continuous electrical connection between the top and bottom layers of the PCB by depositing a conductive material, usually copper, onto the walls of the drilled holes. This process is essential for creating reliable annular rings that provide a secure connection between the component lead and the copper trace.
-
How can I prevent annular ring failures in my PCB design?
-
To prevent annular ring failures, ensure that your design meets the required mechanical and electrical specifications, choose compatible materials, implement strict manufacturing process controls, perform thorough inspections, follow proper handling and assembly practices, and apply environmental protection measures when necessary.
-
What are the most common annular ring failure modes?
- The most common annular ring failure modes include mechanical stress, thermal stress, chemical attack, and corrosion. These failures can lead to cracks, fractures, separation from the PCB substrate, or degradation of the copper plating, resulting in a weakened or broken electrical connection.
Conclusion
Annular rings are a critical component of PCB design, providing a secure electrical and mechanical connection between component leads and copper traces. By understanding the purpose, design considerations, manufacturing processes, quality control, and failure modes associated with annular rings, designers and manufacturers can create reliable and high-performing PCBs.
Careful attention to annular ring size, shape, and placement, along with robust manufacturing and inspection processes, can help ensure the long-term reliability of the PCB. Additionally, implementing appropriate prevention strategies can minimize the risk of annular ring failures, leading to improved product quality and customer satisfaction.
As PCB technology continues to advance, the importance of annular rings in ensuring reliable electrical connections will remain paramount. By staying informed about best practices and emerging technologies related to annular rings, designers and manufacturers can continue to push the boundaries of PCB performance and reliability.
Leave a Reply