The Importance of PCB Inspection
PCB inspection plays a vital role in ensuring the quality, reliability, and functionality of electronic devices. Some key reasons why PCB inspection is essential include:
- Identifying manufacturing defects
- Ensuring proper component placement and orientation
- Verifying solder joint quality
- Detecting potential short circuits or open connections
- Maintaining high product quality and reliability
- Reducing warranty claims and product returns
- Complying with industry standards and regulations
Types of PCBA Inspection
There are several types of PCBA inspection methods used in the electronics manufacturing industry. Each method has its advantages and limitations, and the choice of inspection method depends on factors such as the complexity of the PCB, production volume, and required accuracy. The main types of PCBA inspection are:
Visual Inspection
Visual inspection is the most basic form of PCBA inspection. It involves examining the assembled PCB with the naked eye or using magnifying tools to identify visible defects such as:
- Incorrect component placement
- Damaged or missing components
- Solder bridging or insufficient solder
- Flux residue or contamination
While visual inspection is relatively quick and low-cost, it is prone to human error and may not detect subtle defects.
Automated Optical Inspection (AOI)
Automated Optical Inspection (AOI) uses high-resolution cameras and advanced image processing software to inspect PCBAs. AOI systems compare the captured images of the assembled PCB to a pre-defined set of criteria or a “golden sample” to identify defects such as:
- Component placement errors
- Solder joint defects (e.g., bridging, insufficient solder, tombstoning)
- Missing or incorrect components
- Polarity errors
AOI is faster and more consistent than visual inspection, making it suitable for high-volume production. However, it may have difficulty detecting certain types of defects, such as those hidden under components or within solder joints.
X-Ray Inspection
X-ray inspection uses X-ray technology to examine the internal structure of solder joints and components on a PCBA. This method is particularly useful for inspecting:
- Ball Grid Array (BGA) and Chip Scale Package (CSP) solder joints
- Through-hole solder joints
- Voids or cracks within solder joints
- Component placement and alignment in multi-layer boards
X-ray inspection can detect defects that are not visible to the naked eye or AOI systems. However, it is slower and more expensive than other inspection methods and may require specialized training to interpret the X-ray images.
In-Circuit Testing (ICT)
In-Circuit Testing (ICT) is a functional testing method that uses a bed-of-nails fixture to make electrical contact with specific points on the PCBA. ICT systems apply electrical signals to the board and measure the response to verify:
- Component presence and value
- Short circuits and open connections
- Resistance, capacitance, and inductance values
- Basic component functionality
ICT is an effective way to detect electrical defects and ensure that the PCBA functions as intended. However, it requires the development of a custom test fixture for each unique PCB design, which can be time-consuming and costly.
Functional Testing
Functional testing involves powering up the assembled PCBA and testing its functionality using software or hardware-based test systems. This method verifies that the PCBA performs as intended in its final application by:
- Executing test scripts or programs
- Applying input signals and measuring output responses
- Verifying communication protocols and interfaces
- Checking for proper power management and thermal performance
Functional testing is essential for ensuring that the PCBA meets its design specifications and operates correctly in its intended environment. However, it may not detect all manufacturing defects and is typically performed after other inspection methods.
PCBA Inspection Process
The PCBA inspection process typically involves several stages, each with its own set of inspection methods and criteria. A typical PCBA inspection process may include:
-
Solder Paste Inspection (SPI): Inspects the solder paste deposition on the PCB prior to component placement using 2D or 3D vision systems.
-
Pre-Reflow Inspection: Verifies component placement and orientation before the soldering process using AOI or vision systems.
-
Post-Reflow Inspection: Examines the solder joints and component placement after the soldering process using AOI, X-ray, or visual inspection.
-
In-Circuit Testing (ICT): Verifies the electrical functionality of the PCBA using a bed-of-nails fixture and test software.
-
Functional Testing: Tests the PCBA’s performance and functionality in its final application using software or hardware-based test systems.
-
Final Visual Inspection: A final visual check of the PCBA for any visible defects or cosmetic issues before packaging and shipping.
The specific inspection process may vary depending on the product requirements, manufacturing capabilities, and industry standards.
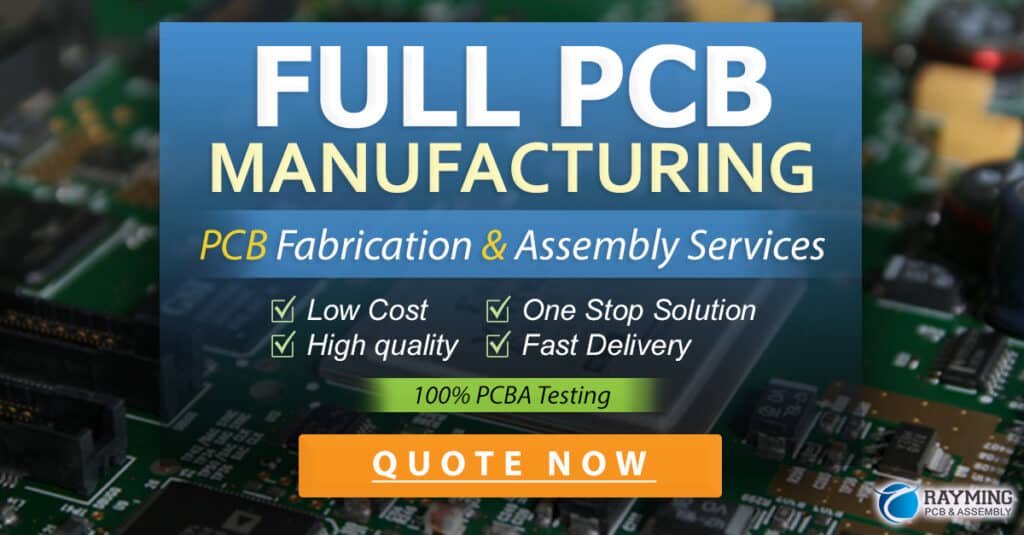
Advantages of Automated PCBA Inspection
Automated PCBA inspection methods, such as AOI and X-ray inspection, offer several advantages over manual inspection:
- Increased speed and efficiency
- Improved accuracy and consistency
- Reduced human error and fatigue
- Ability to detect subtle or hidden defects
- Real-time data collection and analysis
- Scalability for high-volume production
- Cost savings through early defect detection and prevention
Automated inspection systems can significantly enhance the quality and reliability of PCBAs while reducing manufacturing costs and time-to-market.
Challenges in PCBA Inspection
Despite the benefits of automated PCBA inspection, there are still some challenges that manufacturers face:
- High initial investment costs for automated inspection equipment
- Need for specialized training and expertise to operate and maintain inspection systems
- Difficulty in inspecting complex or densely populated pcbAs
- Limited ability to detect certain types of defects, such as those related to component quality or long-term reliability
- Need for continuous updating of inspection criteria and programs to keep up with new technologies and designs
Manufacturers must carefully consider their specific needs and requirements when selecting and implementing PCBA inspection solutions.
Best Practices for Effective PCBA Inspection
To ensure effective and efficient PCBA inspection, manufacturers should follow these best practices:
- Develop a comprehensive inspection plan that covers all stages of the PCBA manufacturing process
- Use a combination of inspection methods to detect a wide range of defects
- Establish clear inspection criteria and acceptance standards based on product requirements and industry guidelines
- Regularly calibrate and maintain inspection equipment to ensure accurate and consistent results
- Provide adequate training and support for inspection personnel
- Implement statistical process control (SPC) to monitor and analyze inspection data for continuous improvement
- Foster a culture of quality and collaboration among all stakeholders in the PCBA manufacturing process
By following these best practices, manufacturers can optimize their PCBA inspection process and deliver high-quality, reliable products to their customers.
PCBA Inspection Standards and Guidelines
There are several industry standards and guidelines that provide requirements and recommendations for PCBA inspection, such as:
- IPC-A-610: Acceptability of Electronic Assemblies
- IPC-J-STD-001: Requirements for Soldered Electrical and Electronic Assemblies
- IPC-7912: Specification for Data Transfer from AOI to Statistical Process Control (SPC) Software
- IEC 61191: Printed Board Assemblies
- MIL-STD-883: Test Method Standard for Microcircuits
These standards help to ensure consistency and quality in PCBA inspection across different manufacturers and industries.
FAQ
- What is the difference between PCB and PCBA inspection?
-
PCB inspection focuses on examining the bare printed circuit board for defects in the copper traces, solder mask, and silk screen. PCBA inspection, on the other hand, involves examining the fully assembled PCB with all components soldered in place.
-
What are the most common defects found during PCBA inspection?
-
Some of the most common defects found during PCBA inspection include component placement errors, solder joint defects (e.g., bridging, insufficient solder, tombstoning), missing or incorrect components, and short circuits or open connections.
-
How does automated optical inspection (AOI) work?
-
AOI systems use high-resolution cameras and advanced image processing software to capture images of the assembled PCB. These images are then compared to a pre-defined set of criteria or a “golden sample” to identify defects or deviations from the expected assembly.
-
What are the advantages of using X-ray inspection for PCBA?
-
X-ray inspection can detect defects that are not visible to the naked eye or AOI systems, such as voids or cracks within solder joints, BGA and CSP solder joint defects, and component placement issues in multi-layer boards. It is particularly useful for inspecting dense or complex PCBAs.
-
How can manufacturers ensure the effectiveness of their PCBA inspection process?
- Manufacturers can ensure the effectiveness of their PCBA inspection process by developing a comprehensive inspection plan, using a combination of inspection methods, establishing clear inspection criteria and acceptance standards, regularly calibrating and maintaining inspection equipment, providing adequate training for personnel, implementing statistical process control, and fostering a culture of quality and collaboration.
In conclusion, PCBA inspection is a critical process in the manufacturing of electronic devices, ensuring the quality, reliability, and functionality of the final product. By understanding the various inspection methods, challenges, best practices, and industry standards, manufacturers can optimize their PCBA inspection process and deliver high-quality products to their customers.
Leave a Reply