Composition of Rogers PCB Materials
Rogers PCB materials are typically composed of a combination of polymers, ceramics, and other additives, each carefully selected to impart specific properties to the final product. The most common base materials used in Rogers PCB laminates include:
- Polytetrafluoroethylene (PTFE)
- Hydrocarbon ceramics
- Woven glass reinforcement
Polytetrafluoroethylene (PTFE)
PTFE, also known by the brand name Teflon, is a fluoropolymer known for its excellent dielectric properties, low dissipation factor, and high thermal stability. It is often used as the primary base material in Rogers PCB laminates due to its ability to maintain stable electrical properties over a wide range of frequencies and temperatures.
Key properties of PTFE:
– Dielectric constant: 2.1
– Dissipation factor: 0.0002
– Temperature resistance: -200°C to +260°C
Hydrocarbon Ceramics
Hydrocarbon ceramics, such as silicon dioxide (SiO2) and aluminum oxide (Al2O3), are often added to Rogers PCB materials to enhance their thermal conductivity and mechanical strength. These ceramics help to dissipate heat more efficiently, preventing thermal buildup and improving the overall reliability of the PCB.
Typical properties of hydrocarbon ceramics:
– Thermal conductivity: 1-30 W/mK
– Dielectric constant: 3.5-10
– Coefficient of thermal expansion (CTE): 3-8 ppm/°C
Woven Glass Reinforcement
Woven glass reinforcement, typically in the form of E-glass or S-glass fibers, is used to provide mechanical strength and dimensional stability to Rogers PCB laminates. The glass fibers are impregnated with the polymer matrix (e.g., PTFE) to create a composite material that can withstand the stresses and strains encountered during PCB manufacturing and operation.
Properties of woven glass reinforcement:
– Tensile strength: 3500 MPa
– Elastic modulus: 72 GPa
– Dielectric constant: 6.3
– Dissipation factor: 0.002
Popular Rogers PCB Materials and Their Compositions
Rogers Corporation offers a wide range of PCB materials, each optimized for specific applications and performance requirements. Some of the most popular Rogers PCB materials include:
RO3000 Series
The RO3000 series is a family of high-frequency laminates designed for applications requiring low dielectric loss and stable electrical properties. These materials are composed of a PTFE matrix reinforced with ceramic filler and woven glass.
Material | Dielectric Constant | Dissipation Factor | Thermal Conductivity (W/mK) |
---|---|---|---|
RO3003 | 3.00 | 0.0013 | 0.50 |
RO3006 | 6.15 | 0.0025 | 0.61 |
RO3010 | 10.20 | 0.0035 | 0.66 |
RO4000 Series
The RO4000 series is a family of hydrocarbon ceramic laminates designed for high-frequency applications requiring low dielectric loss and good thermal management. These materials are composed of a hydrocarbon ceramic matrix reinforced with woven glass.
Material | Dielectric Constant | Dissipation Factor | Thermal Conductivity (W/mK) |
---|---|---|---|
RO4003C | 3.38 | 0.0027 | 0.71 |
RO4350B | 3.48 | 0.0037 | 0.62 |
RO4360G2 | 6.15 | 0.0038 | 0.66 |
RT/duroid Series
The RT/duroid series is a family of PTFE-based laminates designed for high-frequency and high-speed digital applications. These materials are composed of a PTFE matrix reinforced with woven glass and ceramic filler.
Material | Dielectric Constant | Dissipation Factor | Thermal Conductivity (W/mK) |
---|---|---|---|
RT/duroid 5870 | 2.33 | 0.0012 | 0.22 |
RT/duroid 5880 | 2.20 | 0.0009 | 0.20 |
RT/duroid 6002 | 2.94 | 0.0012 | 0.60 |
Manufacturing Process of Rogers PCB Materials
The manufacturing process of Rogers PCB materials involves several steps, each carefully controlled to ensure consistent quality and performance:
-
Raw material preparation: The base polymers (e.g., PTFE), ceramics, and woven glass reinforcement are prepared and mixed according to the specific formulation for each material.
-
Impregnation: The woven glass reinforcement is impregnated with the polymer matrix, typically using a hot-melt process or solvent impregnation.
-
Lamination: The impregnated glass fabric is laminated with copper foils under high pressure and temperature to create a consolidated laminate.
-
Cutting and packaging: The laminate is cut to the desired size and packaged for distribution to PCB manufacturers.
Throughout the manufacturing process, strict quality control measures are implemented to ensure that the materials meet the specified electrical, thermal, and mechanical properties.
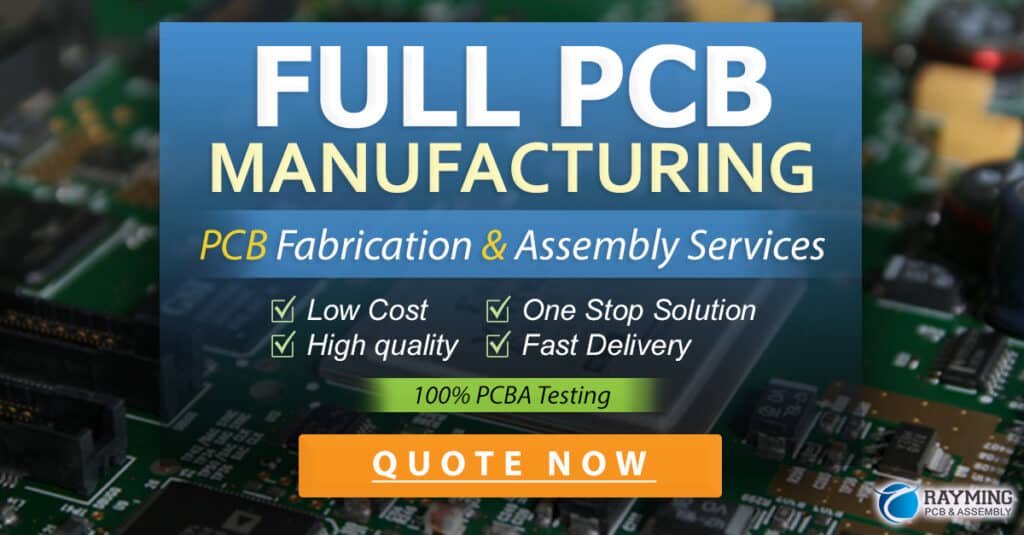
Applications of Rogers PCB Materials
Rogers PCB materials are used in a wide range of high-frequency and high-speed digital applications, including:
- Wireless communication systems (e.g., 5G, WiFi, Bluetooth)
- Automotive radar and sensors
- Aerospace and defense electronics
- Medical imaging equipment
- High-speed digital systems (e.g., data centers, supercomputers)
The choice of Rogers PCB material depends on the specific requirements of the application, such as the operating frequency, power handling capability, and environmental conditions.
Advantages of Using Rogers PCB Materials
Rogers PCB materials offer several advantages over traditional FR-4 laminates:
-
Low dielectric loss: Rogers materials have lower dissipation factors, which minimizes signal attenuation and distortion at high frequencies.
-
Stable electrical properties: The dielectric constant and dissipation factor of Rogers materials remain stable over a wide range of frequencies and temperatures, ensuring consistent performance.
-
Improved thermal management: The high thermal conductivity of Rogers materials helps to dissipate heat more efficiently, reducing thermal stress on components and improving reliability.
-
Mechanical stability: The woven glass reinforcement provides excellent dimensional stability and mechanical strength, minimizing warpage and delamination.
-
Wide range of options: Rogers offers a diverse portfolio of PCB materials, allowing designers to select the optimal material for their specific application requirements.
FAQ
-
What is the main difference between Rogers PCB materials and traditional FR-4 laminates?
Rogers PCB materials are engineered for high-frequency and high-speed digital applications, offering lower dielectric loss, more stable electrical properties, and better thermal management compared to traditional FR-4 laminates. -
Can Rogers PCB materials be used for multilayer PCBs?
Yes, Rogers PCB materials can be used to fabricate multilayer PCBs. The laminates are compatible with standard PCB manufacturing processes, such as drilling, plating, and lamination. -
Are Rogers PCB materials suitable for high-temperature applications?
Many Rogers PCB materials, such as the RO4000 series and RT/duroid series, are designed to withstand high temperatures, typically up to 260°C. This makes them suitable for applications that involve high operating temperatures or exposure to harsh environments. -
How do I select the right Rogers PCB material for my application?
The selection of the appropriate Rogers PCB material depends on several factors, including the operating frequency, dielectric constant, dissipation factor, thermal conductivity, and mechanical requirements. Consult the Rogers material selection guide and work with your PCB manufacturer to determine the best material for your specific application. -
Are Rogers PCB materials more expensive than traditional FR-4 laminates?
Yes, Rogers PCB materials are generally more expensive than traditional FR-4 laminates due to their advanced properties and specialized manufacturing processes. However, the improved performance and reliability offered by Rogers materials often justify the higher cost in high-frequency and high-speed digital applications.
In conclusion, Rogers PCB materials are engineered to provide superior performance in high-frequency and high-speed digital applications. By combining advanced polymers, ceramics, and woven glass reinforcement, Rogers materials offer low dielectric loss, stable electrical properties, improved thermal management, and mechanical stability. With a wide range of materials available, designers can select the optimal Rogers PCB material for their specific application requirements, ensuring reliable and consistent performance in demanding environments.
Leave a Reply