Understanding Heavy copper pcbs
Definition and Characteristics
A heavy copper PCB is a printed circuit board that uses copper traces with a thickness greater than the standard 1 oz. (35 μm) copper. Typically, heavy copper PCBs have copper thicknesses ranging from 2 oz. (70 μm) to 20 oz. (700 μm) or more. The increased copper thickness allows these boards to handle higher currents and provides better thermal dissipation compared to standard PCBs.
Comparison with Standard PCBs
Characteristic | Standard PCB | Heavy Copper PCB |
---|---|---|
Copper Thickness | 1 oz. (35 μm) | 2 oz. (70 μm) to 20 oz. (700 μm) or more |
Current Handling | Low to moderate | High |
Thermal Management | Limited | Superior |
Applications | General electronics | Power electronics, high-current applications |
Applications of Heavy Copper PCBs
Heavy copper PCBs find applications in various industries where high current handling and efficient thermal management are critical. Some of the common applications include:
Power Electronics
- Switched-mode power supplies (SMPS)
- Motor drives
- Inverters and converters
Automotive Electronics
- Electric vehicle battery management systems
- High-power lighting systems
- Engine control units (ECUs)
Industrial Equipment
- Welding machines
- High-power lasers
- Induction heating systems
Telecommunications
- Base station power amplifiers
- High-power RF transmitters
- Satellite communication systems
Manufacturing Process of Heavy Copper PCBs
The manufacturing process of heavy copper PCBs involves several steps that ensure the proper formation of thick copper traces and reliable performance.
Substrate Preparation
The process begins with the selection and preparation of the PCB substrate, typically FR-4 or other high-temperature materials. The substrate is cleaned and conditioned to ensure proper adhesion of the copper layers.
Copper Deposition
Thick copper layers are deposited onto the substrate using electroplating or foil lamination techniques. Electroplating involves the electrochemical deposition of copper onto the substrate, while foil lamination involves bonding pre-formed copper foils to the substrate using heat and pressure.
Circuit Patterning
The desired circuit pattern is transferred onto the copper layers using photolithography. A photoresist layer is applied, exposed to UV light through a photomask, and developed to create the circuit pattern.
Etching and Plating
The exposed copper areas are etched away using chemical processes, leaving only the desired circuit traces. Additional copper plating may be applied to further increase the thickness of the traces.
Finishing and Inspection
The PCB undergoes final finishing processes, such as solder mask application, surface finish (e.g., HASL, ENIG), and silkscreen printing. The board is then inspected for quality and functionality before packaging and shipping.
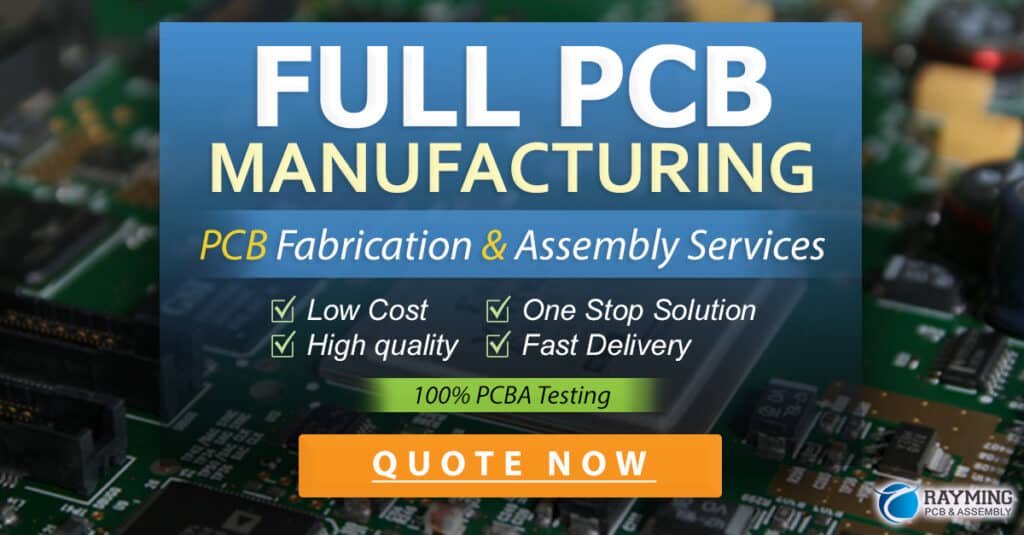
Benefits of Heavy Copper PCBs
Heavy copper PCBs offer several advantages over standard PCBs, making them ideal for high-current and thermally demanding applications.
Improved Current Handling
The thick copper traces in heavy copper PCBs allow for higher current carrying capacity without excessive heating or voltage drop. This makes them suitable for power-intensive applications where reliable current delivery is crucial.
Enhanced Thermal Management
The increased copper thickness provides better thermal conductivity, allowing heat to be efficiently dissipated from critical components. This helps in maintaining stable operating temperatures and prevents thermal damage to the PCB and its components.
Reduced Resistance and Voltage Drop
Thicker copper traces have lower electrical resistance, minimizing voltage drop across the board. This ensures that the required voltage levels are maintained throughout the circuit, improving overall system performance and reliability.
Improved Mechanical Strength
Heavy copper PCBs exhibit higher mechanical strength and durability compared to standard PCBs. The thicker copper layers provide better support for heavy components and help in withstanding vibrations and mechanical stresses.
Design Considerations for Heavy Copper PCBs
When designing heavy copper PCBs, several factors need to be considered to ensure optimal performance and manufacturability.
Trace Width and Spacing
The increased copper thickness allows for wider trace widths and larger spacing between traces. However, designers must still adhere to the minimum trace width and spacing requirements based on the specific copper thickness and manufacturing capabilities.
Thermal Management
Proper thermal management is crucial in heavy copper PCB design. Adequate copper coverage, thermal vias, and heat sinks should be incorporated to efficiently dissipate heat from critical components and prevent thermal hotspots.
Component Selection
Components used in heavy copper PCBs must be capable of handling the higher currents and temperatures. Designers should select components with appropriate current ratings and thermal specifications to ensure reliable operation.
Manufacturing Considerations
The manufacturing process for heavy copper PCBs may have specific limitations and requirements. Designers should consult with the PCB manufacturer to understand the available copper thicknesses, minimum feature sizes, and any special design rules to ensure successful fabrication.
Frequently Asked Questions (FAQ)
-
Q: What is the typical copper thickness range for heavy copper PCBs?
A: Heavy copper PCBs typically have copper thicknesses ranging from 2 oz. (70 μm) to 20 oz. (700 μm) or more, depending on the specific application requirements. -
Q: Can heavy copper PCBs be used in high-frequency applications?
A: Yes, heavy copper PCBs can be used in high-frequency applications, such as RF power amplifiers and high-speed digital circuits. However, designers must consider the skin effect and ensure proper impedance matching and signal integrity. -
Q: Are heavy copper PCBs more expensive than standard PCBs?
A: Yes, heavy copper PCBs are generally more expensive than standard PCBs due to the increased copper usage and specialized manufacturing processes involved. The cost depends on factors such as copper thickness, board size, and complexity. -
Q: Can heavy copper PCBs be combined with other PCB technologies?
A: Yes, heavy copper PCBs can be combined with other PCB technologies, such as multilayer boards, flexible circuits, and high-density interconnects (HDI). This allows for the integration of heavy copper layers with other features to meet specific design requirements. -
Q: How does the increased copper thickness affect the weight of the PCB?
A: The increased copper thickness in heavy copper PCBs results in a higher overall weight compared to standard PCBs. This should be considered when designing systems where weight is a critical factor, such as in aerospace or portable applications.
Conclusion
Heavy copper PCBs are specialized printed circuit boards that offer superior current handling and thermal management capabilities compared to standard PCBs. With copper thicknesses ranging from 2 oz. to 20 oz. or more, these boards find applications in power electronics, automotive systems, industrial equipment, and telecommunications.
The manufacturing process of heavy copper PCBs involves careful substrate preparation, copper deposition, circuit patterning, etching, and plating to ensure reliable performance. Designers must consider factors such as trace width and spacing, thermal management, component selection, and manufacturing limitations when creating heavy copper PCB designs.
By leveraging the benefits of improved current handling, enhanced thermal management, reduced resistance, and increased mechanical strength, heavy copper PCBs enable the development of high-performance electronic systems that can withstand demanding operating conditions.
As technology continues to advance, the use of heavy copper PCBs is expected to grow in various industries, driving innovation and pushing the boundaries of electronic design. With their unique characteristics and capabilities, heavy copper PCBs will remain a vital component in the realm of power electronics and high-current applications.
Leave a Reply