Introduction to PCB Coatings
Printed Circuit Boards (PCBs) are essential components in modern electronic devices, providing a platform for electrical connections and supporting various components. To ensure the longevity, reliability, and performance of PCBs, they are often coated with protective layers. These PCB coatings serve multiple purposes, including protection against environmental factors, enhanced electrical insulation, and improved mechanical stability.
In this article, we will delve into the world of PCB coatings, exploring their types, properties, and applications. We will also discuss the importance of selecting the right coating for specific PCB requirements and the benefits they offer in various industries.
Types of PCB Coatings
There are several types of PCB coatings available, each with its unique characteristics and benefits. Let’s explore some of the most common PCB coatings:
1. Conformal Coatings
Conformal coatings are thin, protective layers applied to the surface of a PCB, conforming to its contours and components. These coatings provide insulation, moisture resistance, and protection against environmental contaminants. The most common types of conformal coatings include:
- Acrylic: Known for their excellent electrical insulation and ease of application, acrylic coatings offer good moisture and chemical resistance.
- Silicone: Silicone coatings provide excellent high-temperature stability and flexibility, making them suitable for applications with thermal cycling.
- Polyurethane: Offering superior abrasion and chemical resistance, polyurethane coatings are ideal for harsh environments.
- Epoxy: Epoxy coatings provide excellent moisture and chemical resistance, along with strong adhesion to the PCB surface.
2. Solder Mask
Solder mask, also known as solder resist, is a thin, protective layer applied to the copper traces of a PCB. Its primary purpose is to prevent solder bridging and short circuits during the soldering process. Solder mask also provides insulation and protection against oxidation and corrosion. The most common types of solder mask include:
- Liquid Photoimageable Solder Mask (LPI): LPI is a photosensitive liquid that is applied to the PCB surface and then exposed to UV light to create the desired pattern.
- Dry Film Solder Mask: This type of solder mask comes in the form of a dry film that is laminated onto the PCB surface and then exposed and developed to create the desired pattern.
3. Potting Compounds
Potting compounds are thick, encapsulating materials used to completely encase PCB components or entire assemblies. They provide excellent protection against moisture, vibration, and impact. Potting compounds are commonly used in high-reliability applications, such as aerospace, automotive, and medical devices. The most common types of potting compounds include:
- Epoxy: Epoxy potting compounds offer excellent moisture resistance, thermal stability, and strong adhesion to PCB components.
- Silicone: Silicone potting compounds provide good thermal conductivity and flexibility, making them suitable for applications with thermal management requirements.
- Polyurethane: Polyurethane potting compounds offer good electrical insulation and resistance to abrasion and chemicals.
Properties and Benefits of PCB Coatings
PCB coatings offer several key properties and benefits that enhance the performance and reliability of electronic devices. Let’s explore some of these properties and their corresponding benefits:
1. Insulation and Dielectric Strength
One of the primary functions of PCB coatings is to provide electrical insulation between conductive traces and components. The dielectric strength of a coating refers to its ability to withstand high voltages without breakdown. Higher dielectric strength ensures better insulation and prevents short circuits and electrical leakage.
Coating Type | Dielectric Strength (kV/mm) |
---|---|
Acrylic | 20-40 |
Silicone | 15-20 |
Polyurethane | 30-50 |
Epoxy | 20-40 |
2. Moisture and Chemical Resistance
PCB coatings provide a barrier against moisture and chemical contaminants, preventing corrosion and degradation of the PCB and its components. Different coatings offer varying levels of moisture and chemical resistance, depending on their material properties.
Coating Type | Moisture Resistance | Chemical Resistance |
---|---|---|
Acrylic | Good | Good |
Silicone | Excellent | Good |
Polyurethane | Excellent | Excellent |
Epoxy | Excellent | Excellent |
3. Thermal Stability and Heat Dissipation
Some PCB coatings, such as silicone and epoxy, offer excellent thermal stability and heat dissipation properties. These coatings can withstand high temperatures and help in distributing heat evenly across the PCB, preventing hot spots and thermal stress on components.
4. Mechanical Protection
PCB coatings provide mechanical protection against vibration, shock, and impact. Potting compounds, in particular, offer excellent mechanical stability by completely encapsulating the PCB and its components, reducing the risk of damage due to physical stresses.
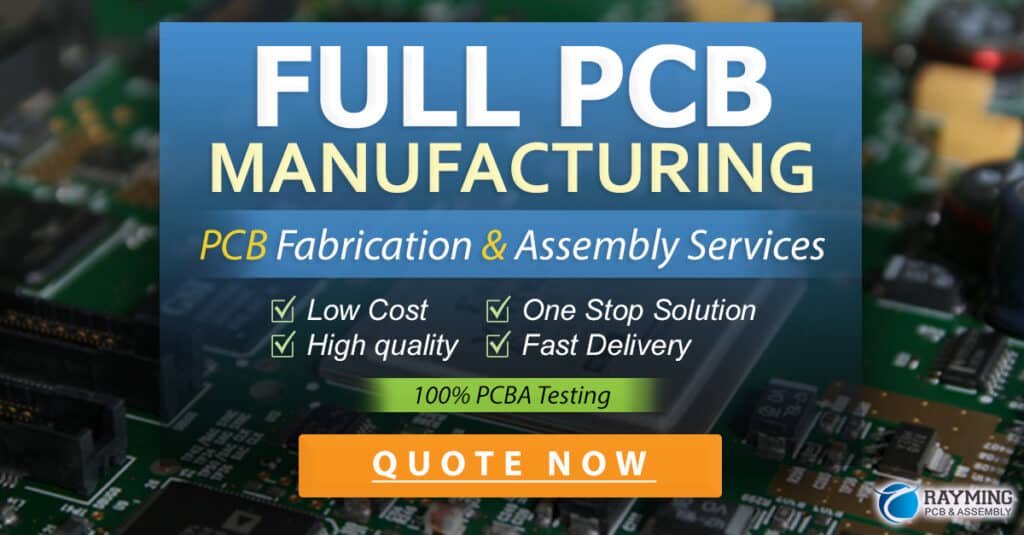
Selecting the Right PCB Coating
Choosing the appropriate PCB coating depends on several factors, including the application environment, performance requirements, and budget. Here are some key considerations when selecting a PCB coating:
-
Environmental Conditions: Consider the expected operating environment of the PCB, including temperature range, humidity levels, and exposure to chemicals or contaminants. Select a coating that offers the necessary protection against these environmental factors.
-
Electrical Requirements: Evaluate the electrical insulation and dielectric strength requirements of the PCB. Choose a coating with suitable dielectric properties to prevent electrical leakage and ensure proper insulation.
-
Thermal Management: If the PCB generates significant heat or operates in high-temperature environments, consider coatings with good thermal stability and heat dissipation properties, such as silicone or epoxy.
-
Mechanical Stresses: Assess the expected mechanical stresses on the PCB, such as vibration, shock, or impact. Select a coating that provides adequate mechanical protection, such as potting compounds for high-stress applications.
-
Cost and Processing: Consider the cost of the coating material and the associated processing requirements. Some coatings may require specialized equipment or curing processes, which can impact the overall cost and production timeline.
Applications of PCB Coatings
PCB coatings find applications in various industries and sectors, each with its specific requirements and challenges. Some common applications of PCB coatings include:
-
Automotive Electronics: PCBs in automotive applications are exposed to harsh environments, including extreme temperatures, vibration, and moisture. Conformal coatings and potting compounds are commonly used to protect automotive PCBs and ensure reliable performance.
-
Aerospace and Defense: PCBs in aerospace and defense applications must withstand extreme conditions, such as high altitudes, temperature fluctuations, and exposure to radiation. High-performance coatings, such as silicone and epoxy, are often used to meet the stringent requirements of these applications.
-
Medical Devices: PCBs in medical devices require high reliability and protection against moisture and chemicals. Conformal coatings and potting compounds are used to ensure the longevity and performance of medical electronics, particularly in implantable devices and diagnostic equipment.
-
Industrial Automation: PCBs in industrial automation systems are exposed to harsh environments, including dust, moisture, and chemical contaminants. Conformal coatings and potting compounds provide the necessary protection against these environmental factors, ensuring reliable operation and reduced maintenance costs.
-
Consumer Electronics: Consumer electronic devices, such as smartphones, tablets, and wearables, often require PCB coatings to protect against moisture, dust, and everyday wear and tear. Thin conformal coatings, such as acrylic or silicone, are commonly used in consumer electronics to maintain device aesthetics while providing essential protection.
Frequently Asked Questions (FAQ)
-
Q: Can PCB coatings be removed if needed?
A: Yes, most PCB coatings can be removed using appropriate solvents or mechanical methods. However, the removal process may require specialized equipment and expertise to avoid damaging the PCB or its components. -
Q: How do I choose between conformal coating and potting for my PCB?
A: The choice between conformal coating and potting depends on the level of protection required and the specific application. Conformal coatings provide a thin, protective layer and are suitable for most general-purpose applications. Potting, on the other hand, offers complete encapsulation and is ideal for high-reliability applications with severe environmental or mechanical stresses. -
Q: Can PCB coatings affect the thermal performance of the board?
A: Some PCB coatings, such as silicone and epoxy, have good thermal conductivity and can help in dissipating heat from the PCB. However, thick coatings or potting compounds may act as thermal insulators, trapping heat and affecting the thermal performance of the board. It is important to consider the thermal requirements of the application when selecting a PCB coating. -
Q: Are PCB coatings necessary for all applications?
A: Not all PCB applications require coatings. The decision to use a coating depends on the specific environmental, electrical, and mechanical requirements of the application. PCBs operating in benign environments or with low-reliability requirements may not need coatings, while those exposed to harsh conditions or requiring high reliability often benefit from appropriate coatings. -
Q: How are PCB coatings applied?
A: PCB coatings can be applied using various methods, depending on the type of coating and the desired thickness. Conformal coatings are typically applied using spray coating, brush coating, or dip coating techniques. Potting compounds are usually dispensed or poured into a mold or enclosure containing the PCB. The coating application process may also involve curing or drying steps to achieve the final protective layer.
Conclusion
PCB coatings play a crucial role in protecting printed circuit boards from environmental, electrical, and mechanical stresses. By understanding the types of coatings available, their properties, and their applications, designers and manufacturers can select the most suitable coating for their specific PCB requirements. Whether it’s a thin conformal coating for general-purpose protection or a thick potting compound for high-reliability applications, PCB coatings enhance the performance, reliability, and longevity of electronic devices across various industries.
As technology advances and electronic devices become more sophisticated, the importance of PCB coatings will continue to grow. By staying informed about the latest developments in PCB coating materials and application techniques, engineers and manufacturers can ensure that their products meet the ever-increasing demands for reliability and durability in today’s complex electronic landscape.
Leave a Reply