What are Flexible PCBs?
Flexible PCBs, also known as flex circuits or flexible printed wiring, are a type of printed circuit board that consists of a thin, flexible substrate with conductive traces and components mounted on its surface. Unlike traditional rigid PCBs, which are made from a solid substrate material such as FR-4, flexible PCBs use a pliable substrate, typically made from polyimide or other flexible polymers.
The key advantages of flexible PCBs include:
- Flexibility: The ability to bend, fold, and twist without damaging the circuit or components.
- Lightweight: Flexible PCBs are generally thinner and lighter than their rigid counterparts.
- Space-saving: The compact and conformable nature of flex circuits allows for more efficient use of space in electronic devices.
- Durability: Flexible PCBs can withstand repeated flexing and vibration without cracking or breaking.
- High-density interconnect: Flex circuits can accommodate a high density of components and traces, enabling more complex designs.
Flexible PCB Manufacturing Process
The manufacturing process for flexible PCBs shares many similarities with that of rigid PCBs, but with some unique considerations and techniques to account for the flexible nature of the substrate. The main steps in the flexible PCB manufacturing process are as follows:
1. Substrate Preparation
The first step in manufacturing a flexible PCB is to select and prepare the appropriate substrate material. The most common substrate used for flex circuits is polyimide, a high-performance polymer known for its excellent thermal, mechanical, and electrical properties. Other substrate materials include polyester, polyethylene naphthalate (PEN), and aramid.
The substrate is typically provided in the form of a roll or sheet, which is then cut to the desired size and shape using precision cutting tools such as lasers or die-cutters. The substrate may also undergo a cleaning process to remove any contaminants or debris that could affect the adhesion of the conductive layers.
2. Copper Lamination
Once the substrate is prepared, a thin layer of copper foil is laminated onto one or both sides of the substrate using heat and pressure. The copper foil serves as the conductive layer for the circuit traces and pads. The thickness of the copper foil can vary depending on the specific requirements of the design, with common thicknesses ranging from 9 to 70 microns (0.0004 to 0.0028 inches).
The lamination process typically involves placing the substrate and copper foil between two heated plates and applying pressure to ensure a strong bond between the layers. An adhesive layer, such as acrylic or epoxy, may be used to promote adhesion between the substrate and copper foil.
3. Circuit Patterning
With the copper-clad substrate prepared, the next step is to create the desired circuit pattern on the copper layer. This is typically done using a photolithographic process, which involves the following sub-steps:
a. Photoresist Application: A light-sensitive polymer, called photoresist, is applied to the copper surface in a thin, uniform layer. The photoresist can be either liquid or dry film, with the latter being more common in flexible PCB manufacturing due to its ease of handling and consistency.
b. Exposure: The photoresist-coated substrate is then exposed to UV light through a photomask, which is a transparent sheet with the circuit pattern printed on it. The areas of the photoresist exposed to UV light undergo a chemical change, making them either more soluble (positive photoresist) or less soluble (negative photoresist) in a developing solution.
c. Development: After exposure, the substrate is immersed in a developing solution, which selectively removes the soluble areas of the photoresist, revealing the underlying copper. The remaining photoresist serves as a protective mask for the desired circuit pattern during the etching process.
d. Etching: The exposed copper areas not protected by the photoresist are then removed using a chemical etching process, typically involving an acidic solution such as ferric chloride or ammonium persulfate. This leaves behind the desired circuit pattern on the substrate.
e. Photoresist Removal: After etching, the remaining photoresist is stripped away using a solvent or an alkaline solution, revealing the complete copper circuit pattern on the flexible substrate.
4. Via Formation
Vias are small holes drilled through the substrate and plated with copper to create electrical connections between different layers of the flexible PCB. There are several types of vias used in flexible PCBs, including:
a. Through Holes: These are vias that penetrate through the entire thickness of the substrate, connecting the copper layers on both sides.
b. Blind Vias: These vias connect an outer layer to an inner layer, but do not penetrate through the entire substrate.
c. Buried Vias: These are vias that connect two or more inner layers without reaching either outer layer.
The via formation process typically involves drilling the holes using mechanical drilling or laser drilling, followed by a plating process to create a conductive path through the holes. The plating process may involve electroless copper deposition followed by electrolytic copper plating to build up the desired thickness.
5. Coverlay Application
After the circuit pattern and vias are formed, a coverlay is often applied to protect the exposed copper traces and provide electrical insulation. The coverlay is a thin, flexible film, typically made from polyimide or a similar material, with adhesive on one side. The coverlay is cut to shape, aligned with the circuit pattern, and laminated onto the substrate using heat and pressure.
Openings in the coverlay, called windows, are created to expose specific areas of the circuit, such as pads for component assembly or connectors. These windows can be formed by laser cutting, die-cutting, or photoimaging, depending on the design requirements and manufacturing capabilities.
6. Surface Finish
To enhance the solderability, durability, and electrical performance of the flexible PCB, a surface finish may be applied to the exposed copper areas. Some common surface finishes used in flexible PCB manufacturing include:
a. ENIG (Electroless Nickel Immersion Gold): A thin layer of nickel is deposited on the copper, followed by a thin layer of gold. This finish provides excellent solderability, corrosion resistance, and shelf life.
b. HASL (Hot Air Solder Leveling): A layer of solder is applied to the copper surface and then leveled using hot air to create a smooth, uniform finish. This is a cost-effective option but may not be suitable for fine-pitch components or high-density designs.
c. OSP (Organic Solderability Preservative): A thin, organic coating is applied to the copper surface to prevent oxidation and maintain solderability. This is a low-cost option but may have a limited shelf life compared to other finishes.
7. Component Assembly
Once the flexible PCB is fabricated, the next step is to assemble the electronic components onto the board. This process can be done using various techniques, depending on the component types and the design requirements:
a. Surface Mount Technology (SMT): Surface mount components are placed on the pads of the flexible PCB and soldered using reflow soldering, where the entire board is heated to melt the solder paste and form a connection between the component leads and the pads.
b. Through-Hole Technology (THT): Through-hole components have long leads that are inserted into the through holes of the flexible PCB and soldered on the opposite side using wave soldering or manual soldering.
c. Chip-on-Flex (COF): Bare semiconductor die are directly mounted onto the flexible substrate and connected using wire bonding or flip-chip bonding. This allows for a highly compact and lightweight assembly.
8. Final Testing and Inspection
After component assembly, the flexible PCB undergoes a series of testing and inspection procedures to ensure its functionality, reliability, and conformance to the design specifications. Some common tests include:
a. Continuity Test: This test verifies that all the intended electrical connections are present and that there are no short circuits or open circuits in the assembly.
b. Insulation Resistance Test: This test measures the resistance between adjacent conductors to ensure adequate electrical insulation and prevent leakage currents.
c. Functional Test: The assembled flexible PCB is powered on and tested for its intended functionality, such as signal integrity, timing, and input/output performance.
d. Visual Inspection: The board is visually examined for any defects, such as misaligned components, solder bridges, or damaged traces.
e. Flexing Test: The flexible PCB is subjected to repeated bending and folding cycles to ensure its mechanical integrity and reliability under flexing conditions.
Once the flexible PCB passes all the required tests and inspections, it is packaged and shipped to the customer for integration into the final product.
Quality Control in Flexible PCB Manufacturing
Ensuring the quality and reliability of flexible PCBs is crucial for their successful application in various industries. Manufacturers employ several quality control measures throughout the production process to minimize defects and maintain consistent performance. Some key quality control practices in flexible PCB manufacturing include:
-
Material Selection: Choosing high-quality substrate materials, copper foils, and other components that meet the required specifications and standards.
-
Process Control: Implementing strict process controls and monitoring systems to ensure that each manufacturing step is performed within the specified parameters, such as temperature, pressure, and time.
-
Cleanliness: Maintaining a clean and controlled manufacturing environment to prevent contamination and ensure the quality of the finished product.
-
Automated Inspection: Using automated optical inspection (AOI) and X-ray inspection systems to detect and analyze defects in the circuit pattern, solder joints, and component placement.
-
Traceability: Implementing a traceability system to track the materials, processes, and operators involved in the production of each flexible PCB, enabling easier identification and resolution of quality issues.
-
Testing and Validation: Conducting comprehensive electrical, mechanical, and environmental testing to validate the performance and reliability of the flexible PCBs under various conditions.
-
Continuous Improvement: Regularly reviewing and analyzing quality data to identify areas for improvement and implementing corrective actions to prevent recurring issues.
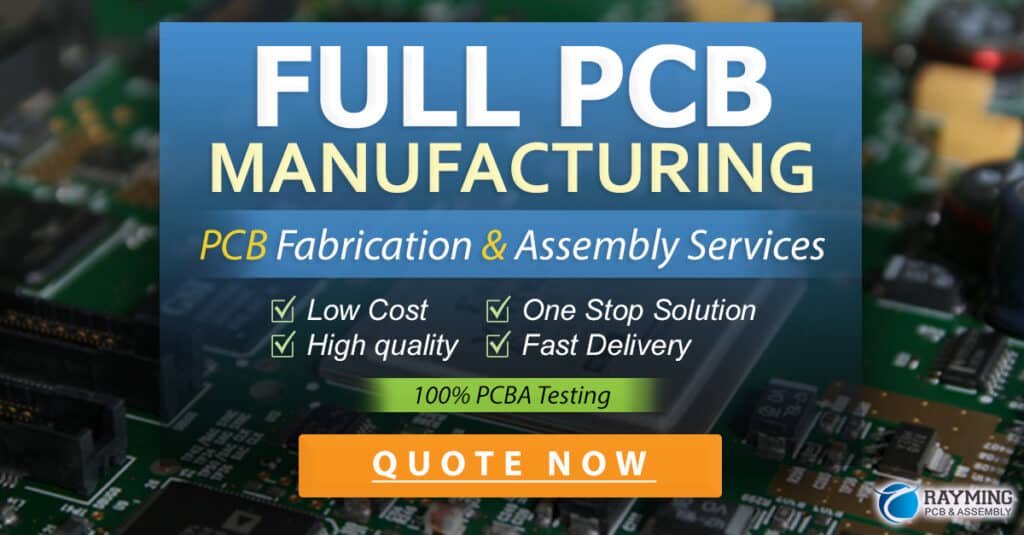
Applications of Flexible PCBs
Flexible PCBs find applications in a wide range of industries and products, thanks to their unique properties and advantages. Some common applications of flexible PCBs include:
-
Consumer Electronics: Flexible PCBs are widely used in smartphones, tablets, laptops, and wearable devices, enabling compact and lightweight designs with improved reliability and functionality.
-
Medical Devices: Flex circuits are employed in various medical applications, such as implantable devices, diagnostic equipment, and patient monitoring systems, where their flexibility and biocompatibility are crucial.
-
Automotive Electronics: Flexible PCBs are used in automotive applications, such as dashboard displays, sensors, and control modules, where their ability to withstand vibration, temperature extremes, and harsh environments is essential.
-
Aerospace and Defense: Flex circuits are used in satellites, aircraft, and military equipment, where their lightweight, compact design, and high reliability are critical for mission success.
-
Industrial Equipment: Flexible PCBs are employed in various industrial applications, such as robotics, machine vision systems, and process control equipment, where their flexibility and durability enable improved performance and reliability.
Frequently Asked Questions (FAQ)
-
Q: What is the difference between a flexible PCB and a rigid PCB?
A: Flexible PCBs use a thin, pliable substrate material, such as polyimide, which allows them to bend, fold, and twist without damaging the circuit or components. Rigid PCBs, on the other hand, use a solid substrate material, such as FR-4, which provides a stable platform for the circuit but cannot be flexed or bent. -
Q: What are the advantages of using flexible PCBs over rigid PCBs?
A: Flexible PCBs offer several advantages over rigid PCBs, including increased flexibility, lighter weight, space savings, improved durability, and the ability to accommodate high-density interconnects. These properties make flexible PCBs ideal for applications that require compact, lightweight, and conformable circuit solutions. -
Q: What materials are commonly used for flexible PCB substrates?
A: The most common substrate material used for flexible PCBs is polyimide, a high-performance polymer known for its excellent thermal, mechanical, and electrical properties. Other substrate materials include polyester, polyethylene naphthalate (PEN), and aramid. -
Q: How are components assembled onto flexible PCBs?
A: Components can be assembled onto flexible PCBs using various techniques, depending on the component types and design requirements. Surface mount technology (SMT) is commonly used for surface mount components, while through-hole technology (THT) is used for components with long leads. Chip-on-flex (COF) is another technique where bare semiconductor die are directly mounted onto the flexible substrate. -
Q: What industries commonly use flexible PCBs?
A: Flexible PCBs find applications in a wide range of industries, including consumer electronics, medical devices, automotive electronics, aerospace and defense, and industrial equipment. Their unique properties and advantages make them suitable for applications that require compact, lightweight, and reliable circuit solutions.
Conclusion
Flexible PCB manufacturing is a complex and sophisticated process that involves a combination of advanced materials, precision manufacturing techniques, and stringent quality control measures. By understanding the various steps involved in the production of flexible PCBs, from substrate preparation to final testing and inspection, we can better appreciate the remarkable capabilities of these versatile components and their growing importance in the electronics industry.
As technology continues to evolve and the demand for compact, lightweight, and flexible electronic devices increases, the role of flexible PCBs in enabling these advancements will only become more significant. With ongoing research and development in materials science, manufacturing processes, and design tools, we can expect to see even more innovative and ambitious applications of flexible PCBs in the future.
Leave a Reply