Understanding the Basics of a 6 layer pcb Stackup
A typical 6 layer PCB stackup consists of the following arrangement of copper layers and insulating dielectric material:
Layer | Type | Function |
---|---|---|
1 | Signal | Top layer for component placement and signal routing |
2 | Ground | Ground plane for controlled impedance and shielding |
3 | Signal | Inner signal routing layer |
4 | Signal | Inner signal routing layer |
5 | Power | Power plane for power distribution |
6 | Signal | Bottom layer for component placement and signal routing |
The signal layers (1, 3, 4, and 6) are used for routing traces between components, while the ground (2) and power (5) layers provide stable reference planes for controlled impedance, noise reduction, and power distribution.
Determining Layer Thickness and Dielectric Material
The choice of dielectric material and the thickness of each layer are critical factors in determining the electrical properties and manufacturability of the PCB. Common dielectric materials include:
- FR-4: Standard glass-reinforced epoxy laminate, suitable for most applications
- High-Tg FR-4: FR-4 with higher glass transition temperature for improved thermal stability
- Rogers: High-performance materials for demanding RF and high-speed applications
The thickness of the dielectric layers affects the impedance of the traces and the overall board thickness. A common 6 layer PCB stackup might use the following thicknesses:
Layer | Thickness (mm) |
---|---|
1-2 | 0.20 |
2-3 | 0.25 |
3-4 | 0.30 |
4-5 | 0.25 |
5-6 | 0.20 |
Consult with your PCB manufacturer to determine the optimal layer thicknesses and dielectric materials for your specific application and manufacturing capabilities.
Signal Integrity and Controlled Impedance
Maintaining signal integrity is crucial in high-speed digital designs. Controlled impedance is essential for preventing signal reflections, crosstalk, and other issues that can degrade performance. To achieve controlled impedance:
- Calculate the required trace width and spacing for your target impedance using a PCB stackup calculator or simulation software.
- Route critical traces on the inner signal layers (3 and 4) whenever possible, as they benefit from the shielding provided by the adjacent ground and power planes.
- Maintain consistent trace width and spacing for each impedance-controlled net, and avoid abrupt changes in direction or layer transitions.
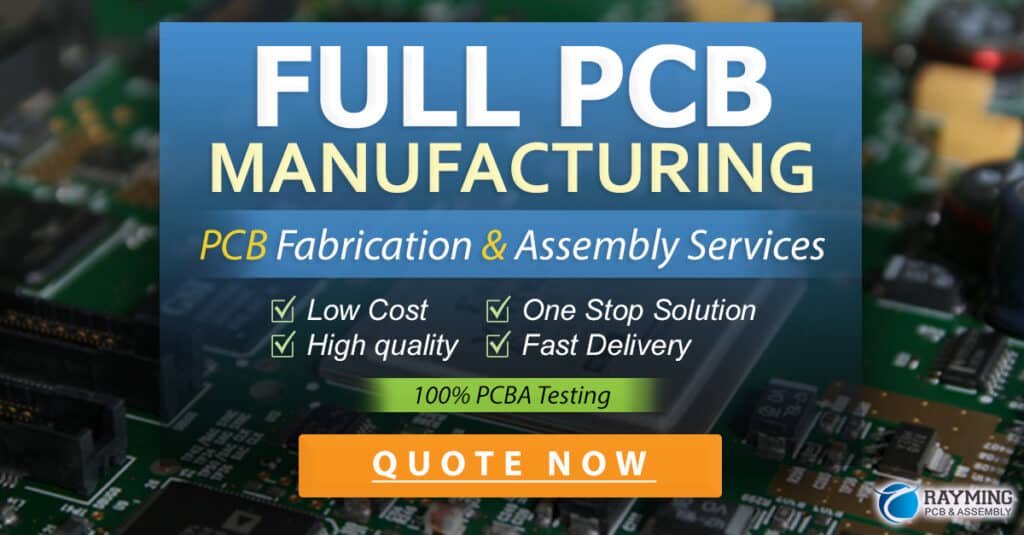
Power Distribution and Decoupling
Proper power distribution and decoupling are essential for minimizing noise and ensuring reliable operation. Follow these guidelines:
- Use wide, low-impedance traces or copper pours to connect the power plane to the power supply and distribute power to components.
- Place decoupling capacitors close to the power pins of ICs to minimize the loop area and provide a local, low-impedance power source.
- Use multiple capacitor values (e.g., 0.1 µF, 1 µF, 10 µF) to target different noise frequencies and ensure a low impedance across a wide frequency range.
- Consider using a power plane split or isolated power islands for sensitive analog or RF sections of the board.
Grounding and EMI Reduction
A solid ground plane is critical for controlling impedance, reducing noise, and minimizing electromagnetic interference (EMI). Follow these best practices:
- Maintain a continuous ground plane on layer 2, with minimal splits or cutouts.
- Use stitching vias to connect ground planes on different layers, especially near connectors and at the board edges.
- Route high-speed signals on inner layers, sandwiched between the ground and power planes, to minimize radiation and coupling.
- Use ground vias to provide shielding for sensitive signals or to create a “picket fence” around potential sources of EMI.
Thermal Management
Proper thermal management is crucial for ensuring the reliability and longevity of your PCB. Consider the following:
- Use thermal vias to conduct heat from power-dissipating components to the inner copper layers or a dedicated thermal plane.
- Increase the copper weight (thickness) of the power and ground planes to improve their heat-spreading capabilities.
- Use thermal interface materials (TIMs) or heatsinks to dissipate heat from high-power components.
FAQ
1. When should I choose a 6 layer PCB stackup over a 4 layer stackup?
A 6 layer PCB stackup is recommended when:
– Your design has a high component density or complex routing requirements that exceed the capabilities of a 4 layer board.
– You need better signal integrity and controlled impedance for high-speed signals.
– You require more power distribution options or isolated power domains.
2. Can I mix different dielectric materials in a 6 layer PCB stackup?
Yes, it is possible to mix different dielectric materials in a 6 layer stackup, such as using FR-4 for most layers and a high-performance material like Rogers for RF or high-speed sections. However, this can increase manufacturing complexity and cost, so it should only be done when necessary.
3. How do I determine the optimal trace width and spacing for controlled impedance?
To determine the optimal trace width and spacing for controlled impedance, you can use a PCB stackup calculator or simulation software. These tools take into account the dielectric material properties, layer thicknesses, and target impedance to calculate the required trace geometry. It’s essential to work closely with your PCB manufacturer to ensure that your design is compatible with their manufacturing capabilities.
4. What are some common pitfalls to avoid when designing a 6 layer PCB stackup?
Some common pitfalls to avoid when designing a 6 layer PCB stackup include:
– Neglecting to consider controlled impedance requirements for high-speed signals.
– Failing to provide adequate power distribution and decoupling, leading to noise and reliability issues.
– Splitting or cutting the ground plane excessively, which can compromise signal integrity and EMI performance.
– Not accounting for thermal management, especially for power-dissipating components.
5. How can I ensure my 6 layer PCB stackup is manufacturable and cost-effective?
To ensure your 6 layer PCB stackup is manufacturable and cost-effective:
– Communicate early and often with your PCB manufacturer, discussing your requirements, design, and any potential challenges.
– Follow the manufacturer’s design guidelines for minimum trace width and spacing, via size and spacing, and other design rules.
– Consider the impact of material choice and layer thickness on cost and lead time.
– Optimize your design to minimize the board size and layer count while still meeting your performance and reliability goals.
By following these guidelines and best practices, you can design a 6 layer PCB stackup that achieves optimal performance, reliability, and manufacturability for your application.
Leave a Reply