What is a Ground Plane?
A ground plane is a layer of copper that covers most of the surface of a PCB, usually on the bottom layer or an inner layer. It is connected to the circuit’s ground (0V reference) through vias and acts as a return path for currents in the circuit.
The ground plane has three main purposes:
- Providing a low-impedance return path for currents
- Shielding against electromagnetic interference (EMI)
- Helping to maintain signal integrity
Low-Impedance Return Path
Electric current always flows in a loop – from the source, through the load, and back to the source. The return path needs to have a low impedance to minimize voltage drops and maintain stable voltage references throughout the circuit.
A ground plane provides an uninterrupted, low-resistance path for return currents to flow back to their source. By minimizing the impedance of this return path, the ground plane helps reduce ground bounce, improves power integrity, and maintains stable references for signals.
Electromagnetic Shielding
A ground plane also acts as a shield against both radiated and conducted electromagnetic interference (EMI). It does this in two ways:
-
The grounded copper absorbs electromagnetic waves, preventing them from coupling into sensitive circuit traces and causing interference. This is especially important for high-frequency signals.
-
The consistent ground potential across the plane prevents voltage gradients that could drive common-mode currents and cause EMI.
By shielding the circuit from external EMI and preventing the circuit from emitting EMI, the ground plane helps meet electromagnetic compatibility (EMC) requirements.
Signal Integrity
Finally, a ground plane helps maintain the integrity of signals in the circuit. High-speed digital signals and sensitive analog signals can be distorted by the impedance of the return path and coupling from nearby traces.
The low impedance and consistent reference provided by the ground plane minimizes signal distortion. For high-speed signals, the ground plane forms a controlled impedance transmission line with the signal trace, allowing the signal to propagate with minimal reflections.
Ground Plane Design Considerations
To make the most of a ground plane, there are several important design considerations to keep in mind. These include the placement of components and traces, the use of splits and cutouts, the connection of the ground plane to the ground point, and the stackup of the PCB layers.
Component and Trace Placement
The placement of components and routing of traces relative to the ground plane impacts both EMI and signal integrity. Generally, you want to place components and route traces as close to the ground plane as possible.
For mixed-signal boards with both analog and digital circuits, it’s best to split the ground plane into analog and digital sections. Sensitive analog components should be placed over the analog ground section, while noisy digital components should be placed over the digital ground. The two ground sections should be connected at a single point to prevent digital noise from coupling into the analog section.
High-frequency and high-current traces should be routed over the ground plane with an appropriate dielectric thickness to control their impedance. Traces should also be kept short and direct, and avoid crossing split planes or changing reference planes unnecessarily.
Splits and Cutouts
While a solid ground plane is ideal for most circuits, there are situations where you may need to split the plane or create cutouts. Splits are used to separate analog and digital grounds, isolate high-current traces, or route signals between different ground domains.
Cutouts are used to physically separate sections of the ground plane, usually to accommodate through-hole components, mounting holes, or connectors. It’s important to keep splits and cutouts to a minimum and to carefully consider their placement to avoid disrupting the flow of return currents.
When creating splits or cutouts, it’s critical to ensure that all components still have a low-impedance return path to ground. Cuts should be crossed with stitching capacitors or signals should be routed around them to maintain continuity of the return current.
Connecting to Ground
The ground plane needs a low-impedance connection to the circuit’s ground point, which is usually the power supply’s negative terminal or a designated ground pad. This connection should be made with multiple vias spread out across the plane to minimize impedance.
For mixed-signal designs with analog and digital ground planes, the two planes should be connected together at a single point, usually near the power supply. This “star grounding” technique prevents noisy return currents in the digital section from flowing through the analog ground and causing interference.
PCB Layer Stackup
The placement of the ground plane in the PCB stackup is another important consideration. In a typical 4-layer board, the ground plane is usually on Layer 2 (counting from the top), with the power plane on Layer 3.
This arrangement provides good shielding and minimizes the loop area between power and ground currents. It also allows the ground plane to be closely coupled to signal traces on the top and bottom layers for controlled impedance.
In boards with more layers, additional ground planes can be added to provide shielding between signal layers. In this case, the ground planes should be stitched together with vias to ensure continuity.
Ground Plane FAQ
To wrap up, let’s address some frequently asked questions about ground planes in PCBs:
1. Is a ground plane necessary in every PCB?
While a ground plane is beneficial in most designs, it’s not always strictly necessary. Simple, low-frequency circuits can often get by with a grid of ground traces instead of a full plane.
However, for any design with high-speed signals, low-level analog signals, or strict EMI requirements, a solid ground plane is strongly recommended.
2. What’s the difference between a ground plane and a ground pour?
A ground plane is a continuous layer of copper that spans the entire PCB or a large section of it. A ground pour, on the other hand, is a smaller area of copper, usually on the top or bottom layer, that is filled in around signal traces and connected to ground.
Ground pours are used to provide shielding and reduce loop areas in specific areas of the board, but they don’t provide the same low-impedance return path as a full plane.
3. Can I have multiple ground planes in a single PCB?
Yes, it’s common to have multiple ground planes in a multi-layer PCB. In fact, this is often necessary to provide proper shielding and reference planes for signals on different layers.
When using multiple ground planes, it’s important to stitch them together with vias to ensure continuity of the ground reference.
4. How do I connect signals to the ground plane?
Signals are connected to the ground plane through vias, which are plated holes that pass through the board to connect different layers. In a typical 4-layer board, signals on the top layer would be connected to the ground plane on Layer 2 with vias.
For high-speed signals, the vias should be placed as close to the signal source as possible to minimize loop area and return path discontinuities.
5. What happens if I don’t use a ground plane?
Without a ground plane, the return currents in your circuit will have to find their way back to the source through whatever paths are available, such as signal traces, power planes, or chassis ground. This can lead to several problems:
- Increased impedance in the return path, leading to signal distortion and ground bounce
- Radiated and conducted EMI due to large loop areas and antenna-like structures
- Decreased immunity to external EMI due to lack of shielding
- Difficulty in controlling signal impedance and crosstalk
While you can mitigate these issues with careful design techniques, such as gridded grounds and localised pours, a solid ground plane is always the best solution for high-performance circuits.
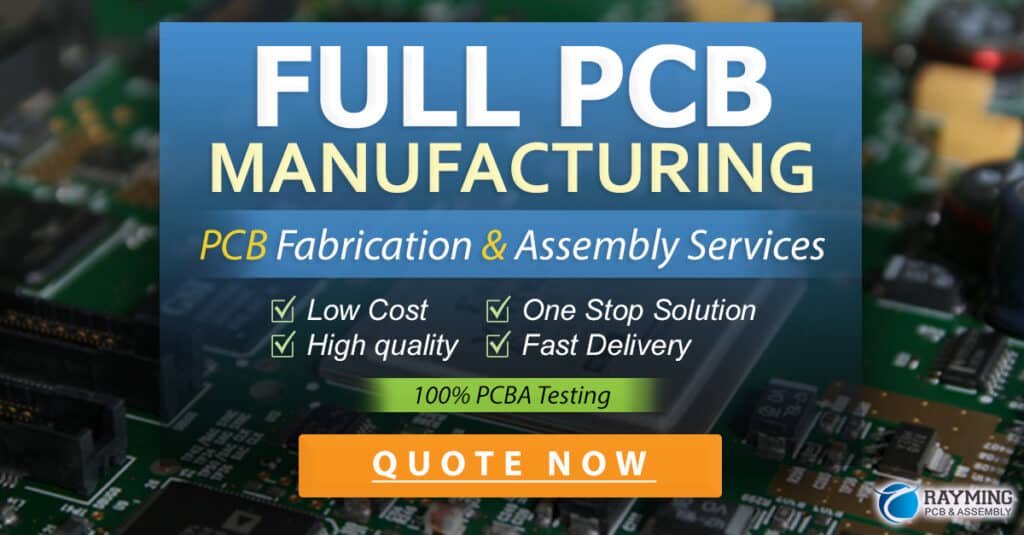
Conclusion
In summary, a ground plane is a critical component of most high-quality PCB designs. By providing a low-impedance return path, shielding against EMI, and maintaining signal integrity, ground planes ensure that your circuit performs optimally and reliably.
When designing with ground planes, it’s important to consider factors such as component placement, split planes, return paths, and layer stackup. By following best practices and carefully planning your ground strategy, you can unlock the full potential of your PCB design.
Here is an example table summarizing some key points about ground planes:
Feature | Benefit |
---|---|
Low impedance | Reduces ground bounce and maintains stable references |
EMI shielding | Prevents interference and meets EMC requirements |
Signal integrity | Minimizes distortion and controls impedance |
Split planes | Isolates analog and digital sections |
Stitching vias | Maintains continuity between multiple planes |
By understanding the role and proper implementation of ground planes, you can design PCBs that are both functionally sound and electromagnetically compliant. Whether you’re working on a simple prototype or a complex, high-speed system, a well-designed ground plane is an essential tool in your PCB design toolkit.
Leave a Reply