Introduction to PCB Trace Current and Heating
Printed Circuit Boards (PCBs) are essential components in modern electronic devices, serving as the foundation for interconnecting various components. One crucial aspect of PCB design is ensuring that the traces can handle the required current without overheating or experiencing excessive voltage drop. The IPC-2221 standard provides guidelines for determining the appropriate trace width based on the expected current and acceptable temperature rise.
In this article, we will explore the IPC-2221 standard and its implications for PCB trace current and heating. We will also provide a comprehensive guide on using a PCB trace calculator to determine the optimal trace width for your design.
Understanding the IPC-2221 Standard
The IPC-2221 standard, titled “Generic Standard on Printed Board Design,” is a widely accepted guideline in the electronics industry. It provides recommendations for various aspects of PCB design, including trace width and spacing, via sizing, and more.
Key Concepts in IPC-2221
-
Current Carrying Capacity: The current carrying capacity of a PCB trace refers to the maximum amount of current that can flow through the trace without causing excessive heating or damage.
-
Temperature Rise: As current flows through a PCB trace, it generates heat due to the trace’s resistance. The temperature rise is the increase in temperature above the ambient temperature caused by this heating effect.
-
Trace Width: The width of a PCB trace directly affects its current carrying capacity and temperature rise. Wider traces can handle higher currents with lower temperature rises compared to narrower traces.
-
Copper Thickness: The thickness of the copper layer on a PCB also influences the current carrying capacity. Thicker copper layers can handle higher currents than thinner layers.
Factors Affecting PCB Trace Current and Heating
Several factors influence the current carrying capacity and temperature rise of PCB traces. Understanding these factors is crucial for designing reliable and efficient PCBs.
Trace Length
The length of a PCB trace affects its resistance and, consequently, the voltage drop and power dissipation. Longer traces have higher resistance, leading to greater voltage drops and increased heating.
Ambient Temperature
The ambient temperature surrounding the PCB impacts the temperature rise of the traces. In higher ambient temperatures, the traces will have less margin for temperature rise before reaching their maximum allowable temperature.
Copper Weight
Copper weight, expressed in ounces per square foot (oz/ft²), represents the thickness of the copper layer on the PCB. Higher copper weights provide better current carrying capacity and lower resistance.
Adjacent Traces
The proximity of other traces to the trace of interest can affect its temperature rise. Closely spaced traces may contribute to localized heating, requiring wider traces or greater spacing to mitigate the effect.
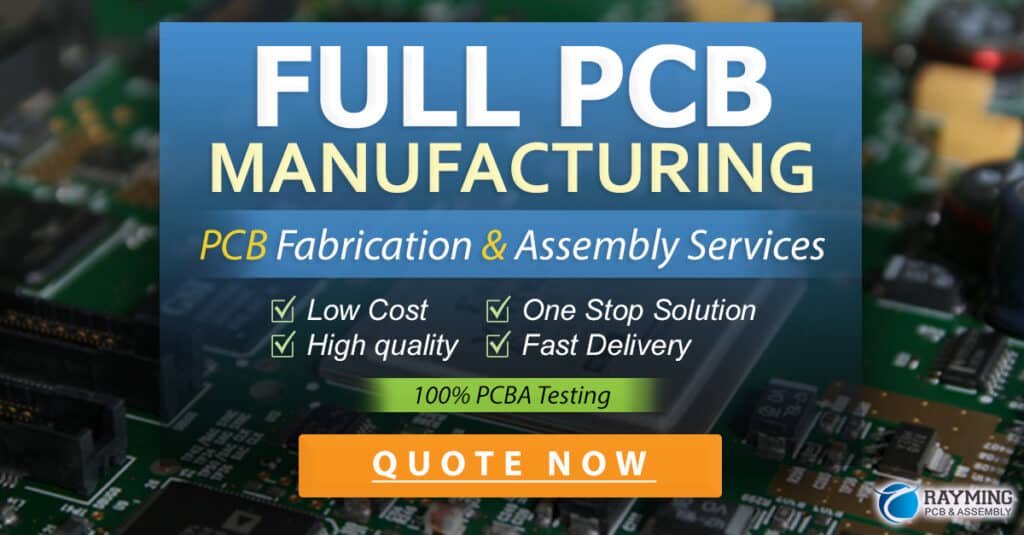
Using a PCB Trace Calculator
To simplify the process of determining the appropriate trace width based on the IPC-2221 standard, designers often use PCB trace calculators. These calculators take into account various parameters and provide recommendations for trace width.
Input Parameters
When using a PCB trace calculator, you typically need to provide the following input parameters:
- Current: The maximum expected current flowing through the trace.
- Trace Length: The length of the trace in question.
- Copper Thickness: The thickness of the copper layer, usually expressed in ounces.
- Temperature Rise: The acceptable temperature rise above the ambient temperature.
- Ambient Temperature: The expected ambient temperature surrounding the PCB.
Output Results
Based on the input parameters, the PCB trace calculator will provide the following output results:
- Recommended Trace Width: The calculator will suggest the minimum trace width required to meet the specified current and temperature rise requirements.
- Resistance: The calculator may also provide the estimated resistance of the trace based on the recommended width and length.
- Voltage Drop: The calculator can calculate the expected voltage drop across the trace, which is important for ensuring proper circuit operation.
PCB Trace Calculator Example
Let’s consider an example to illustrate the usage of a PCB trace calculator. Suppose we have the following requirements:
- Current: 1 A
- Trace Length: 50 mm
- Copper Thickness: 1 oz
- Temperature Rise: 10°C
- Ambient Temperature: 25°C
Using a PCB trace calculator with these input parameters, we might obtain the following results:
Parameter | Value |
---|---|
Recommended Width | 0.5 mm |
Resistance | 0.02 Ω |
Voltage Drop | 0.02 V |
Based on these results, we can conclude that a trace width of 0.5 mm would be sufficient to handle the 1 A current with a temperature rise of 10°C above the ambient temperature of 25°C.
PCB Trace Current and Heating Considerations
When designing PCBs, it’s essential to consider the current and heating aspects of traces to ensure reliable and efficient operation. Here are some key considerations:
Trace Routing
Proper trace routing is crucial for minimizing the length of traces and reducing resistance. Avoid unnecessarily long traces and aim for the most direct path between components.
Trace Spacing
Adequate spacing between traces helps prevent electromagnetic interference (EMI) and reduces the risk of short circuits. The IPC-2221 standard provides guidelines for minimum trace spacing based on various factors.
Thermal Management
In addition to selecting appropriate trace widths, thermal management techniques can help dissipate heat and prevent excessive temperature rises. These techniques include using thermal vias, incorporating heatsinks, and providing adequate ventilation.
High-Current Applications
For high-current applications, it may be necessary to use thicker copper layers or multiple trace layers in parallel to distribute the current and minimize heating. The IPC-2221 standard provides guidance on current carrying capacity for different copper weights.
Frequently Asked Questions (FAQ)
-
What is the IPC-2221 standard?
The IPC-2221 standard is a widely accepted guideline in the electronics industry that provides recommendations for various aspects of PCB design, including trace width and spacing, via sizing, and more. -
How does trace width affect current carrying capacity?
Wider traces can handle higher currents with lower temperature rises compared to narrower traces. Increasing the trace width allows for better heat dissipation and reduces resistance. -
What factors influence the temperature rise of PCB traces?
Several factors influence the temperature rise of PCB traces, including trace length, ambient temperature, copper weight, and the proximity of adjacent traces. Longer traces, higher ambient temperatures, thinner copper layers, and closely spaced traces can all contribute to increased temperature rise. -
What input parameters are required for a PCB trace calculator?
To use a PCB trace calculator, you typically need to provide the maximum expected current, trace length, copper thickness, acceptable temperature rise, and ambient temperature. -
How can I ensure reliable operation of PCB traces in high-current applications?
For high-current applications, you can use thicker copper layers or multiple trace layers in parallel to distribute the current and minimize heating. Additionally, proper trace routing, adequate trace spacing, and effective thermal management techniques can help ensure reliable operation.
Conclusion
PCB trace current and heating are critical considerations in PCB design. The IPC-2221 standard provides valuable guidelines for determining the appropriate trace width based on the expected current and acceptable temperature rise. By understanding the factors affecting trace current and heating, and utilizing PCB trace calculators, designers can create reliable and efficient PCBs.
When designing PCBs, it’s essential to consider trace routing, spacing, thermal management, and the specific requirements of high-current applications. By following best practices and leveraging the guidance provided by the IPC-2221 standard, designers can ensure the optimal performance and longevity of their PCB designs.
Leave a Reply