What are PCB test points?
PCB test points are small, exposed pads or vias on a printed circuit board that allow for easy access to specific signals or components for testing purposes. These test points enable engineers and technicians to quickly connect probes or other testing equipment to verify the functionality, performance, and integrity of the PCB and its components.
Test points serve as convenient access points for:
– Measuring voltages
– Checking continuity
– Injecting signals
– Monitoring waveforms
– Debugging circuits
By incorporating test points into PCB designs, manufacturers can streamline the testing process, reduce the time and effort required for troubleshooting, and improve overall product quality.
The importance of PCB test points
PCB test points play a vital role in the manufacturing process and offer several key benefits:
-
Quality assurance: Test points allow for thorough testing of PCBs at various stages of production, ensuring that the boards meet the required specifications and performance standards.
-
Faster troubleshooting: With easily accessible test points, engineers can quickly identify and isolate faults, reducing the time and effort spent on debugging and repairs.
-
Improved reliability: By facilitating comprehensive testing, test points help identify potential issues early in the production process, leading to more reliable and robust final products.
-
Cost reduction: Efficient testing and troubleshooting enabled by test points can reduce manufacturing costs associated with rework, repairs, and product returns.
-
Compliance with standards: Many industry standards and regulations require the inclusion of test points on PCBs to ensure product safety, reliability, and compatibility.
Types of PCB test points
There are several types of test points commonly used in PCB design:
-
Pad test points: These are small, exposed copper pads on the PCB surface that allow for direct probing with test equipment. Pad test points are the most common and easily accessible type of test point.
-
Via test points: These test points utilize vias, which are conductive holes drilled through the PCB layers, to provide access to internal signals or planes. Via test points are useful for accessing signals on inner layers of multi-layer PCBs.
-
Edge connector test points: These test points are located along the edge of the PCB and are designed to mate with special test connectors or probes. Edge connector test points are often used for high-volume production testing or when access to test points on the PCB surface is limited.
-
Bed-of-nails test points: These test points are designed for use with bed-of-nails testing fixtures, which consist of an array of spring-loaded pins that make contact with the test points on the PCB. Bed-of-nails testing is commonly used for high-volume, automated testing of PCBs.
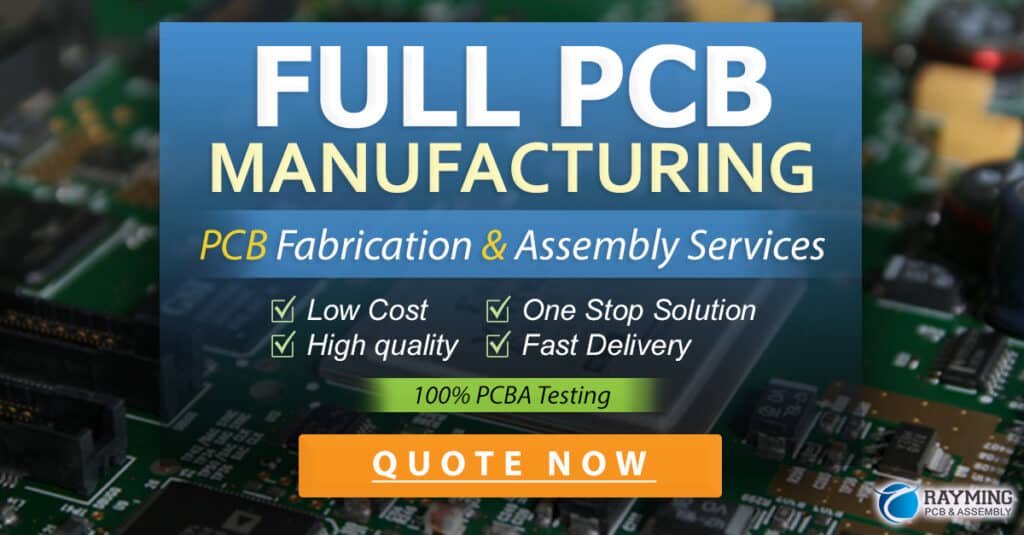
Placement and design considerations for PCB test points
When incorporating test points into a PCB design, engineers must consider several factors to ensure optimal testability and minimize the impact on the board’s functionality and performance.
-
Location: Test points should be placed in easily accessible locations, preferably on the top or bottom surface of the PCB. They should be positioned away from sensitive components, high-voltage areas, or regions with limited space to avoid interference and accessibility issues.
-
Spacing: Adequate spacing between test points is crucial to accommodate test probes and prevent short circuits. The spacing should be based on the size of the test probes and the PCB’s manufacturing capabilities.
-
Signal integrity: Test points should be placed in a manner that minimizes their impact on signal integrity. Avoid placing test points on high-speed signal lines or near sensitive analog circuits to prevent signal distortion or interference.
-
Labeling: Clear and consistent labeling of test points is essential for efficient testing and troubleshooting. Use descriptive names, numbers, or symbols to identify each test point and include this information in the PCB documentation and schematic.
-
Manufacturability: Consider the manufacturing process when designing test points. Ensure that the test points are compatible with the chosen fabrication and assembly methods, and adhere to the manufacturer’s design guidelines for pad sizes, drill sizes, and clearances.
Best practices for implementing PCB test points
To optimize the effectiveness of PCB test points and streamline the testing process, consider the following best practices:
-
Collaborate with the testing team: Engage the testing and quality assurance teams early in the pcb design process to understand their requirements and preferences for test point placement and accessibility.
-
Prioritize critical signals: Focus on placing test points on critical signals, power rails, and interfaces that are essential for the PCB’s functionality and performance. This allows for targeted testing and efficient troubleshooting.
-
Use consistent naming conventions: Establish and adhere to a consistent naming convention for test points across all PCB designs. This improves clarity, reduces confusion, and facilitates better communication between design, manufacturing, and testing teams.
-
Provide comprehensive documentation: Develop clear and detailed documentation that includes the location, naming, and purpose of each test point. This documentation should be easily accessible to all team members involved in the PCB design, fabrication, and testing processes.
-
Conduct design reviews: Regularly review PCB designs with a focus on test point placement and accessibility. Solicit feedback from the manufacturing and testing teams to identify potential issues and improvements early in the design cycle.
-
Monitor and analyze test results: Collect and analyze test data from PCBs to identify trends, common issues, and areas for improvement. Use this information to refine test point placement, update design guidelines, and enhance overall PCB quality and reliability.
PCB Test Point Placement Guidelines
Test Point Type | Placement Guidelines |
---|---|
Pad Test Points | – Place on top or bottom PCB surface – Ensure easy accessibility for probing – Avoid placing near sensitive components or high-voltage areas |
Via Test Points | – Use for accessing signals on inner layers of multi-layer PCBs – Ensure proper via sizing and spacing for reliable probing – Consider the impact on signal integrity |
Edge Connector Test Points | – Place along the edge of the PCB – Design for compatibility with specific test connectors or probes – Consider the mechanical stability and alignment of the PCB during testing |
Bed-of-Nails Test Points | – Design for compatibility with bed-of-nails testing fixtures – Ensure proper pad size, spacing, and placement for reliable contact – Consider the force applied by the test pins and the PCB’s mechanical strength |
FAQ
-
What is the purpose of test points on a PCB?
Test points on a PCB provide convenient access points for testing, measuring, and debugging the board’s functionality and performance. They allow engineers to easily connect test equipment and probes to specific signals or components for verification and troubleshooting purposes. -
How do test points differ from other components on a PCB?
Test points are specifically designed for testing and debugging purposes and do not contribute to the PCB’s primary functionality. They are typically small, exposed pads or vias that provide access to signals without affecting the normal operation of the circuit. -
Can test points affect the signal integrity of a PCB?
If not placed and designed properly, test points can potentially affect the signal integrity of a PCB. It is important to consider the location and spacing of test points, especially on high-speed signal lines or sensitive analog circuits, to minimize any potential signal distortion or interference. -
Are test points required on all PCBs?
While test points are highly recommended for most PCBs to facilitate testing and troubleshooting, they may not be necessary for every design. The decision to include test points depends on factors such as the complexity of the circuit, the manufacturing process, and the specific testing requirements of the product. -
How can I ensure the proper placement and design of test points on my PCB?
To ensure proper placement and design of test points, collaborate with the testing and quality assurance teams early in the design process, prioritize critical signals, use consistent naming conventions, provide comprehensive documentation, conduct regular design reviews, and monitor and analyze test results. Following best practices and guidelines for test point placement can help optimize the testability and reliability of your PCB.
Conclusion
PCB test points are essential elements in the design and manufacturing of reliable and high-quality electronic products. By providing convenient access points for testing and debugging, test points enable faster troubleshooting, improved quality assurance, and reduced manufacturing costs.
When incorporating test points into PCB designs, engineers must consider factors such as location, spacing, signal integrity, labeling, and manufacturability. Following best practices and collaborating closely with testing and manufacturing teams can help optimize the placement and effectiveness of test points.
As the electronics industry continues to evolve and demands for product quality and reliability increase, the proper implementation of PCB test points will remain a critical aspect of successful PCB design and manufacturing processes.
Leave a Reply