The Importance of PCB Footprints
Accurate PCB footprints are essential for several reasons:
-
Proper component placement: Footprints determine where components are placed on the PCB, ensuring they align correctly with the board’s layout.
-
Electrical connectivity: Footprints define the electrical connections between components and the PCB, ensuring proper signal integrity and power distribution.
-
Manufacturing compatibility: Accurate footprints ensure that the PCB can be manufactured and assembled correctly, minimizing the risk of errors and defects.
-
Design reliability: Well-designed footprints contribute to the overall reliability and performance of the PCB, reducing the likelihood of failures or malfunctions.
Elements of a PCB Footprint
A typical PCB footprint consists of several elements:
Pads
Pads are the conductive areas on the PCB where the component pins or contacts are soldered. They come in various shapes and sizes, depending on the component and the soldering technique used. Common pad shapes include:
- Circular
- Rectangular
- Oval
- Rounded rectangle
The size of the pad depends on the component’s pin size and the soldering requirements. For example, surface-mount devices (SMDs) typically have smaller pads compared to through-hole components.
Holes
Some components, such as through-hole devices, require holes in the PCB for their leads to pass through. The hole size depends on the lead diameter and the soldering technique used. For example, wave soldering requires larger holes compared to hand soldering.
Soldermask Openings
Soldermask is a protective coating applied to the PCB that prevents accidental soldering and short circuits. Soldermask openings expose the pads and other conductive areas where soldering is required. The size and shape of the soldermask openings depend on the pad size and the soldering technique used.
Silkscreen
Silkscreen is a printed layer on the PCB that provides information about the components and their orientation. It typically includes the component outline, reference designator, and polarity indicators. The silkscreen helps in the assembly process and makes it easier to identify components during debugging or repair.
Courtyard
The courtyard is a virtual boundary around the footprint that defines the minimum clearance required between the component and other elements on the PCB. It ensures that the component has sufficient space for placement and soldering without interfering with adjacent components or tracks.
Footprint Design Considerations
When designing or selecting a footprint for a component, several factors must be considered:
Component Dimensions
The footprint must match the physical dimensions of the component, including the body size, pin spacing, and lead length. Inaccurate dimensions can lead to assembly issues or mechanical stress on the component.
Soldering Technique
The footprint must be compatible with the soldering technique used in the manufacturing process. For example, wave soldering requires larger pads and holes compared to reflow soldering.
Electrical Requirements
The footprint must provide adequate electrical connectivity between the component and the PCB. This includes ensuring proper pad size and spacing for signal integrity and power handling.
Thermal Management
Some components, such as power devices, generate significant heat during operation. The footprint must provide sufficient thermal relief, such as large pads or thermal vias, to dissipate the heat effectively.
Manufacturing Tolerances
The footprint must account for manufacturing tolerances, such as variations in pad size, hole diameter, and soldermask alignment. Adequate tolerances ensure that the component can be assembled correctly despite minor variations in the manufacturing process.
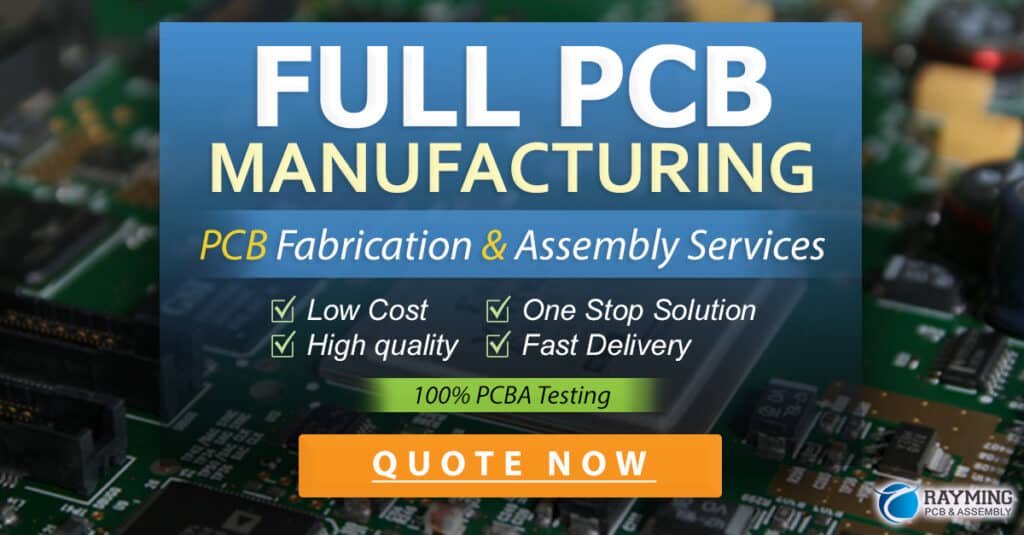
Common Footprint Standards
To simplify the design process and ensure compatibility, several industry standards define common footprints for various component types. Some of the most widely used standards include:
Standard | Description |
---|---|
IPC-7351 | Generic Requirements for Surface Mount Design and Land Pattern Standard |
JEDEC MO-187 | Mechanical Outline for Microelectronic Devices |
JEDEC MS-012 | Registered and Standard Outlines for Solid State and Related Products |
JEITA EDR-7320 | Semiconductor Device Outlines and Footprints |
These standards provide detailed specifications for footprint dimensions, tolerances, and nomenclature, ensuring consistency across different designs and manufacturers.
Footprint Libraries
To streamline the pcb design process, most CAD (computer-aided design) tools include footprint libraries that contain pre-defined footprints for common components. These libraries can be customized or expanded to accommodate specific design requirements.
Some popular footprint libraries include:
- IPC-7351 Compliant Footprint Library
- Altium Vault
- SnapEDA
- PCB Libraries
- Ultra Librarian
Using standardized footprints from these libraries can save time and reduce the risk of errors in the design process. However, it is essential to verify the footprint dimensions against the component datasheet to ensure compatibility.
Creating Custom Footprints
In some cases, a component may not have a pre-defined footprint available in the libraries, or the existing footprints may not meet the specific design requirements. In such situations, designers must create custom footprints.
The process of creating a custom footprint involves the following steps:
-
Obtain component specifications: Gather the necessary information about the component, including its dimensions, pin configuration, and soldering requirements, from the datasheet or manufacturer’s resources.
-
Define footprint elements: Determine the pad sizes, shapes, and spacing based on the component specifications and the soldering technique to be used. Also, define the soldermask openings, silkscreen markings, and courtyard dimensions.
-
Create the footprint in the CAD tool: Use the CAD tool’s footprint editor to create the footprint, following the defined specifications. Most CAD tools provide a graphical interface and parametric settings to simplify the process.
-
Verify the footprint: Check the footprint dimensions and alignment against the component specifications to ensure accuracy. Also, verify the footprint’s compatibility with the PCB layout and manufacturing constraints.
-
Document the footprint: Provide clear documentation of the footprint, including its dimensions, tolerances, and any specific requirements. This documentation helps in maintaining consistency and facilitates future modifications or reuse of the footprint.
Creating custom footprints requires a good understanding of the component specifications and the PCB design guidelines. It is essential to follow the industry standards and best practices to ensure the footprint’s compatibility and reliability.
FAQ
What is the difference between a pad and a hole in a PCB footprint?
Pads are the conductive areas on the PCB where the component pins or contacts are soldered, while holes are the openings in the PCB that allow the leads of through-hole components to pass through. Pads are used for both surface-mount and through-hole components, while holes are specific to through-hole components.
What is the purpose of the courtyard in a PCB footprint?
The courtyard is a virtual boundary around the footprint that defines the minimum clearance required between the component and other elements on the PCB. It ensures that the component has sufficient space for placement and soldering without interfering with adjacent components or tracks.
Can I use the same footprint for different soldering techniques?
Not necessarily. Different soldering techniques, such as wave soldering and reflow soldering, have different requirements for pad sizes, shapes, and spacing. It is essential to choose a footprint that is compatible with the specific soldering technique used in the manufacturing process.
How do I ensure the accuracy of a custom footprint?
To ensure the accuracy of a custom footprint, follow these steps:
- Obtain accurate component specifications from the datasheet or manufacturer’s resources.
- Define the footprint elements based on the specifications and industry standards.
- Create the footprint in the CAD tool using precise dimensions and tolerances.
- Verify the footprint against the component specifications and the PCB layout requirements.
- Document the footprint clearly, including its dimensions, tolerances, and any specific requirements.
Can I modify a standard footprint from a library?
Yes, most CAD tools allow you to modify standard footprints from libraries to suit your specific design requirements. However, it is essential to document any modifications and ensure that the modified footprint still complies with the relevant industry standards and manufacturing constraints.
Conclusion
PCB footprints are a critical element of PCB design, ensuring the correct mechanical and electrical connection between components and the board. Accurate footprints are essential for proper component placement, electrical connectivity, manufacturing compatibility, and overall design reliability.
When designing or selecting footprints, designers must consider various factors, such as component dimensions, soldering techniques, electrical requirements, thermal management, and manufacturing tolerances. Industry standards and footprint libraries provide a foundation for consistent and compatible footprint design.
For custom footprints, designers must follow a systematic approach, obtaining accurate component specifications, defining footprint elements, creating the footprint in the CAD tool, verifying its accuracy, and documenting it clearly.
By understanding the importance of PCB footprints and following best practices in their design and selection, PCB designers can ensure the successful manufacturing and performance of their electronic products.
Leave a Reply