Understanding the Layers of a PCB Stackup
A typical PCB stackup consists of multiple layers, each serving a specific purpose. Let’s take a closer look at the common layers found in a PCB stackup:
Copper Layers
Copper layers are the conductive layers of a PCB, responsible for carrying electrical signals and power. The number of copper layers in a PCB stackup can vary depending on the complexity of the design and the required functionality. Some common configurations include:
- Single-layer PCBs: These have only one copper layer, typically used for simple, low-cost designs.
- Double-layer PCBs: With two copper layers, one on each side of the substrate, double-layer PCBs offer more routing options and better signal integrity compared to single-layer boards.
- Multi-layer PCBs: These boards have three or more copper layers, allowing for complex routing, better signal integrity, and improved EMI (Electromagnetic Interference) performance.
Substrate Layers
The substrate is the insulating material that separates the copper layers in a PCB stackup. The most common substrate materials are:
- FR-4: A flame-retardant, glass-reinforced epoxy laminate, FR-4 is the most widely used substrate material for PCBs due to its excellent mechanical and electrical properties.
- High-frequency laminates: These substrates, such as Rogers or Isola materials, offer superior dielectric properties and are used for high-speed, high-frequency applications like RF (Radio Frequency) and microwave circuits.
Solder Mask Layers
Solder mask is a protective coating applied to the outer layers of a PCB. It serves several purposes:
- Insulates the exposed copper traces to prevent short circuits
- Protects the copper from oxidation and corrosion
- Provides a surface for silkscreen printing of component designators and other markings
- Helps to contain the molten solder during the assembly process
Silkscreen Layers
Silkscreen layers are used to print text, logos, and component designators on the surface of a PCB. This information helps in the assembly process and makes it easier to identify components during debugging and repair.
Types of PCB Stackups
PCB stackups can be categorized based on the number of layers and their arrangement. Let’s explore some common types of PCB stackups:
Single-Layer Stackup
A single-layer PCB stackup consists of one copper layer on a substrate, with a solder mask and silkscreen on the top side. This type of stackup is suitable for simple, low-cost designs with minimal routing requirements.
Layer | Material |
---|---|
Silkscreen | Epoxy Ink |
Solder Mask | Epoxy Resin |
Copper Layer | Copper Foil |
Substrate | FR-4 |
Double-Layer Stackup
Double-layer PCB stackups have two copper layers, one on each side of the substrate. This configuration allows for more routing options and better signal integrity compared to single-layer boards. The typical stackup for a double-layer PCB is as follows:
Layer | Material |
---|---|
Silkscreen | Epoxy Ink |
Solder Mask | Epoxy Resin |
Top Copper | Copper Foil |
Substrate | FR-4 |
Bottom Copper | Copper Foil |
Solder Mask | Epoxy Resin |
Silkscreen | Epoxy Ink |
Multi-Layer Stackup
Multi-layer PCB stackups have three or more copper layers, offering even more routing options and better signal integrity. The number of layers and their arrangement can vary depending on the design requirements. A typical 4-layer PCB stackup might look like this:
Layer | Material |
---|---|
Silkscreen | Epoxy Ink |
Solder Mask | Epoxy Resin |
Top Copper | Copper Foil |
Prepreg | FR-4 |
Inner Layer 1 | Copper Foil |
Core | FR-4 |
Inner Layer 2 | Copper Foil |
Prepreg | FR-4 |
Bottom Copper | Copper Foil |
Solder Mask | Epoxy Resin |
Silkscreen | Epoxy Ink |
In this stackup, the prepreg layers are used to bond the inner copper layers to the core substrate, while the core provides the main structural support for the board.
Design Considerations for PCB Stackups
When designing a PCB stackup, several factors must be considered to ensure optimal performance, reliability, and manufacturability. Let’s discuss some key design considerations:
Signal Integrity
Signal integrity refers to the quality of the electrical signals transmitted through the PCB. To maintain good signal integrity, designers should consider the following:
- Impedance control: Matching the impedance of the traces to the characteristic impedance of the signal source and load to minimize reflections and signal distortion.
- Crosstalk reduction: Minimizing the coupling between adjacent traces to reduce crosstalk, which can cause signal degradation and noise.
- Proper grounding and power distribution: Ensuring a low-impedance return path for signals and providing adequate power distribution to minimize noise and voltage drops.
EMI/EMC Performance
Electromagnetic Interference (EMI) and Electromagnetic Compatibility (EMC) are crucial aspects of PCB design. To minimize EMI and ensure EMC compliance, consider the following:
- Proper layer stacking: Arranging the layers to minimize the loop area between signal traces and their return paths, reducing electromagnetic radiation.
- Shielding: Using ground planes and copper pours to shield sensitive signals and components from external EMI sources.
- Filtering: Implementing filtering techniques, such as decoupling capacitors and ferrite beads, to suppress high-frequency noise.
Thermal Management
Thermal management is essential to ensure the reliable operation of components and prevent overheating. When designing a PCB stackup, consider the following:
- Copper weight: Using appropriate copper weights for power and ground layers to ensure adequate current-carrying capacity and heat dissipation.
- Thermal vias: Incorporating thermal vias to transfer heat from components to the inner layers and the opposite side of the board.
- Thermal planes: Using dedicated thermal planes or copper pours to spread heat evenly across the board.
Manufacturing Constraints
PCB stackup design must also take into account the limitations and capabilities of the manufacturing process. Some key manufacturing constraints include:
- Minimum trace width and spacing: Ensuring that the trace dimensions and spacing meet the manufacturer’s guidelines to avoid production issues.
- Drill sizes and pad dimensions: Selecting appropriate drill sizes and pad dimensions for vias and through-hole components to ensure reliable plating and soldering.
- Layer count and thickness: Considering the maximum number of layers and the overall thickness of the board that the manufacturer can produce reliably.
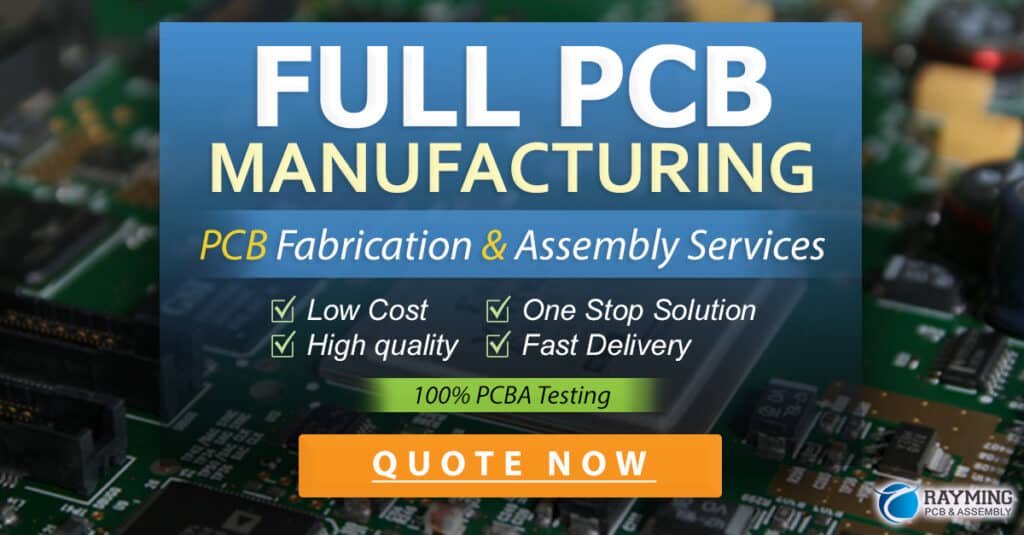
Best Practices for PCB Stackup Design
To create a robust and reliable PCB stackup, follow these best practices:
Keep It Simple
Whenever possible, keep your PCB stackup as simple as possible. Use the minimum number of layers required to achieve your design goals, as adding unnecessary layers increases cost and complexity.
Plan Your Layer Arrangement
Carefully plan the arrangement of your layers to optimize signal integrity, EMI performance, and thermal management. Some general guidelines include:
- Place signal layers close to their reference planes (ground or power) to minimize loop area and reduce EMI.
- Alternate signal layers with ground and power planes to provide shielding and reduce crosstalk.
- Use symmetrical stackups to minimize warpage and ensure consistent mechanical properties.
Use Appropriate Copper Weights
Select appropriate copper weights for your layers based on the current-carrying requirements and thermal management needs. Thicker copper layers can handle higher currents and provide better heat dissipation, but they also increase the overall thickness of the board.
Follow Manufacturer’s Guidelines
Always consult with your PCB manufacturer and follow their guidelines for minimum trace widths, spacings, drill sizes, and other design parameters. This will help ensure that your PCB stackup is manufacturable and meets the required quality standards.
Simulate and Test
Use simulation tools to analyze your PCB stackup’s electrical and thermal performance before finalizing your design. Conduct thorough testing and validation of your prototype boards to identify and address any issues early in the development process.
FAQ
1. What is the difference between a single-layer and a double-layer PCB stackup?
A single-layer PCB stackup has only one copper layer on a substrate, while a double-layer stackup has two copper layers, one on each side of the substrate. Double-layer stackups offer more routing options and better signal integrity compared to single-layer boards.
2. How does the choice of substrate material affect the performance of a PCB?
The choice of substrate material can significantly impact the electrical and mechanical properties of a PCB. For example, high-frequency laminates like Rogers or Isola materials offer superior dielectric properties compared to standard FR-4, making them suitable for high-speed, high-frequency applications.
3. What is the purpose of solder mask in a PCB stackup?
Solder mask is a protective coating applied to the outer layers of a PCB. It insulates the exposed copper traces to prevent short circuits, protects the copper from oxidation and corrosion, provides a surface for silkscreen printing, and helps contain the molten solder during the assembly process.
4. How can I improve the signal integrity of my PCB stackup?
To improve signal integrity, consider implementing impedance control, minimizing crosstalk, and ensuring proper grounding and power distribution. Techniques like matching trace impedances, increasing spacing between traces, and using ground planes can help achieve better signal integrity.
5. What are some key manufacturing constraints to consider when designing a PCB stackup?
When designing a PCB stackup, it’s essential to consider manufacturing constraints such as minimum trace widths and spacings, drill sizes and pad dimensions, and the maximum number of layers and overall thickness that the manufacturer can reliably produce. Always consult with your PCB manufacturer and follow their guidelines to ensure manufacturability.
Conclusion
A well-designed PCB stackup is crucial for ensuring the optimal performance, reliability, and manufacturability of a printed circuit board. By understanding the layers, types, design considerations, and best practices involved in PCB stackup design, you can create robust and efficient PCBs that meet your specific application requirements.
Remember to keep your stackup as simple as possible, plan your layer arrangement carefully, use appropriate copper weights, follow manufacturer’s guidelines, and simulate and test your design thoroughly. By following these principles and staying up-to-date with the latest industry trends and technologies, you can master the art of PCB stackup design and create high-quality, reliable PCBs for a wide range of applications.
Leave a Reply