Introduction to Aluminum PCBs
Aluminum PCBs, also known as metal core PCBs (MCPCBs), are a type of printed circuit board that uses an aluminum substrate instead of the traditional FR-4 material. The aluminum substrate provides excellent thermal conductivity, making these PCBs ideal for applications that generate significant heat. In this article, we will explore the various uses of aluminum PCBs and their advantages over traditional PCBs.
Advantages of Aluminum PCBs
- Superior thermal conductivity
- Improved mechanical stability
- Enhanced electrical performance
- Increased durability
- Lightweight construction
Applications of Aluminum PCBs
1. LED Lighting
One of the most common applications for aluminum PCBs is in LED lighting. LED lights generate a significant amount of heat, which can reduce their lifespan and efficiency if not properly dissipated. Aluminum PCBs provide an excellent solution for this problem, as the aluminum substrate effectively transfers heat away from the LEDs, ensuring optimal performance and longevity.
Advantages of using aluminum PCBs in LED lighting
- Improved heat dissipation
- Increased LED lifespan
- Enhanced light output and efficiency
- Reduced need for additional heat sinks
2. Power Electronics
Aluminum PCBs are also widely used in power electronics, such as power supplies, motor drives, and inverters. These applications often involve high current densities and generate substantial heat, making efficient thermal management crucial. The excellent thermal conductivity of aluminum PCBs helps to dissipate heat quickly, preventing components from overheating and ensuring reliable operation.
Examples of power electronic applications using aluminum PCBs
- Switching mode power supplies (SMPS)
- Motor control circuits
- Inverters for solar and wind energy systems
- High-power amplifiers
3. Automotive Electronics
The automotive industry has increasingly adopted aluminum PCBs for various applications, particularly in electric and hybrid vehicles. These vehicles rely heavily on power electronics for propulsion and energy management, which generate significant heat. Aluminum PCBs provide an effective solution for managing this heat, ensuring the reliability and performance of the vehicle’s electronic systems.
Automotive applications using aluminum PCBs
- Electric vehicle battery management systems
- Motor controllers for electric and hybrid vehicles
- Engine control units (ECUs)
- Automotive lighting systems
4. Telecommunications
Aluminum PCBs are also used in telecommunications equipment, such as base stations and servers. These applications often require high-speed data transmission and generate substantial heat due to the high-frequency operation. The superior thermal conductivity of aluminum PCBs helps to dissipate this heat efficiently, ensuring reliable performance and preventing signal integrity issues.
Telecommunications applications using aluminum PCBs
- 5G base stations
- High-speed routers and switches
- Server power supplies
- Wireless communication modules
5. Aerospace and Defense
In the aerospace and defense industries, aluminum PCBs are used in various applications that require high reliability and performance under extreme conditions. The excellent thermal conductivity and mechanical stability of aluminum PCBs make them well-suited for these demanding applications.
Aerospace and defense applications using aluminum PCBs
- Radar systems
- Avionics
- Satellite communication equipment
- Military-grade power supplies
Designing with Aluminum PCBs
When designing circuits using aluminum PCBs, there are several factors to consider to ensure optimal performance and reliability.
Thermal Management Considerations
- Thermal interface materials
- Heat sink selection and placement
- Thermal vias and copper pours
- Thermal simulation and analysis
Mechanical Design Considerations
- Mounting and fastening methods
- Vibration and shock resistance
- Thermal expansion and contraction
Electrical Design Considerations
- Impedance matching
- Signal integrity
- Grounding and shielding
- Power distribution
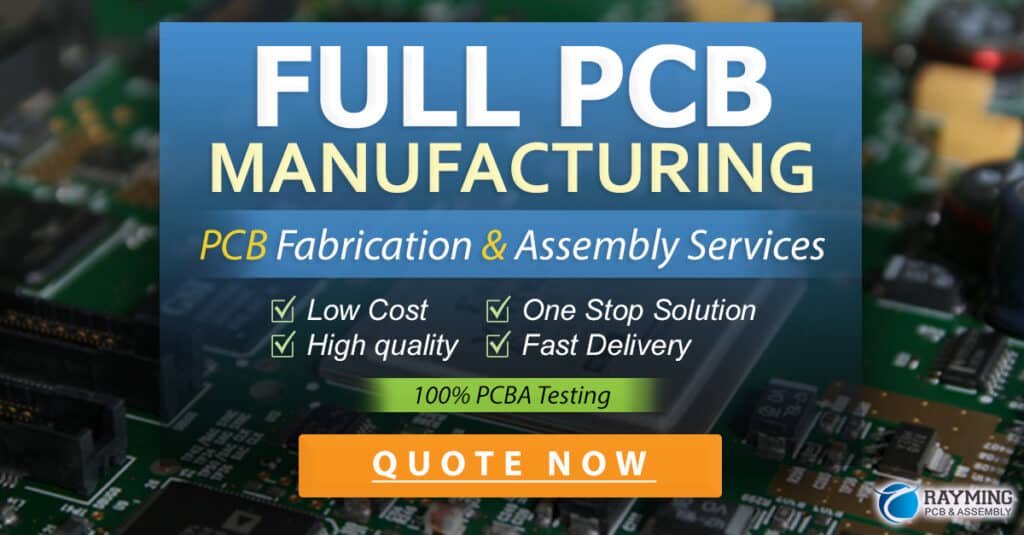
Manufacturing Aluminum PCBs
The manufacturing process for aluminum PCBs differs from that of traditional FR-4 PCBs due to the unique properties of the aluminum substrate.
Key Steps in Aluminum PCB Manufacturing
- Substrate preparation
- Insulation layer application
- Copper foil lamination
- Circuit patterning and etching
- Solder mask and surface finish application
- Singulation and final inspection
Challenges in Aluminum PCB Manufacturing
- Thermal expansion mismatch between aluminum and copper
- Adhesion of insulation layer to aluminum substrate
- Dimensional stability during manufacturing process
Future Trends in Aluminum PCBs
As technology continues to advance, the demand for aluminum PCBs is expected to grow, driven by the increasing need for efficient thermal management and high-performance electronics.
Emerging Applications for Aluminum PCBs
- High-power laser diodes
- Advanced driver assistance systems (ADAS) in vehicles
- Wearable electronics
- Internet of Things (IoT) devices
Advancements in Aluminum PCB Technology
- Improved insulation materials
- Advanced thermal interface materials
- Embedded components and 3D structures
- Integration with other substrate materials (e.g., ceramics)
Frequently Asked Questions (FAQ)
1. What is the difference between aluminum PCBs and traditional FR-4 PCBs?
Aluminum PCBs use an aluminum substrate instead of the traditional FR-4 material, providing superior thermal conductivity and mechanical stability. This makes them ideal for applications that generate significant heat or require high reliability in demanding environments.
2. Can aluminum PCBs be used for all types of electronic circuits?
While aluminum PCBs offer many advantages, they may not be suitable for all types of electronic circuits. They are primarily used in applications that require efficient thermal management or high mechanical stability, such as power electronics, LED lighting, and automotive electronics.
3. Are aluminum PCBs more expensive than traditional PCBs?
Yes, aluminum PCBs are generally more expensive than traditional FR-4 PCBs due to the higher cost of the aluminum substrate and the specialized manufacturing processes required. However, the added cost is often justified by the improved performance and reliability in demanding applications.
4. How do you attach components to aluminum PCBs?
Components can be attached to aluminum PCBs using standard soldering techniques, such as reflow soldering or wave soldering. However, special considerations must be taken to account for the thermal expansion mismatch between the aluminum substrate and the components.
5. Can aluminum PCBs be used in high-frequency applications?
Yes, aluminum PCBs can be used in high-frequency applications, such as telecommunications equipment. The excellent thermal conductivity of the aluminum substrate helps to dissipate heat generated by high-frequency operation, ensuring reliable performance and maintaining signal integrity.
Conclusion
Aluminum PCBs have emerged as a crucial technology for applications that require efficient thermal management and high reliability. Their superior thermal conductivity, mechanical stability, and durability make them well-suited for a wide range of industries, including LED lighting, power electronics, automotive, telecommunications, and aerospace and defense.
As technology continues to advance, the demand for aluminum PCBs is expected to grow, driven by the need for high-performance electronics in increasingly demanding environments. By understanding the advantages and applications of aluminum PCBs, designers and engineers can leverage this technology to create innovative solutions that push the boundaries of electronic performance and reliability.
Leave a Reply