Introduction to LED PCBs
Light-emitting diode (LED) printed circuit boards (PCBs) are specialized boards designed to efficiently control and power LED components. These PCBs are widely used in various applications, such as lighting fixtures, automotive lighting, display boards, and more. Creating an LED PCB requires careful planning, design, and execution to ensure optimal performance and longevity.
In this comprehensive guide, we will walk you through the process of making an LED PCB, covering everything from the basics of LED technology to the final assembly and testing of your board. Whether you are a hobbyist or a professional, this article will provide you with the knowledge and tools necessary to create your own custom LED PCBs.
Understanding LED Technology
What is an LED?
An LED is a semiconductor device that emits light when an electric current passes through it. Unlike traditional incandescent bulbs, LEDs are more energy-efficient, have a longer lifespan, and emit less heat. LEDs come in various colors, sizes, and package types, making them versatile for a wide range of applications.
LED Characteristics and Specifications
When selecting LEDs for your PCB, it is essential to consider their key characteristics and specifications, such as:
- Forward voltage (Vf): The voltage required to turn on the LED and allow current to flow through it.
- Forward current (If): The current that flows through the LED when it is illuminated.
- Luminous intensity: The amount of light emitted by the LED, measured in candelas (cd).
- Viewing angle: The angle at which the LED emits light, typically measured at 50% of the maximum luminous intensity.
- Color temperature: The perceived color of the light emitted by the LED, measured in Kelvin (K).
Understanding these specifications will help you choose the appropriate LEDs for your PCB and design a suitable driving circuit.
Designing Your LED PCB
Schematic Design
The first step in creating your LED PCB is to design the schematic. The schematic represents the electrical connections between the components on your board. When designing the schematic for an LED PCB, consider the following:
- Power supply: Determine the voltage and current requirements for your LEDs and select an appropriate power supply.
- Current-limiting resistors: Calculate the value of the current-limiting resistors needed to protect your LEDs from excessive current.
- LED arrangement: Decide on the number and arrangement of LEDs on your PCB, considering factors such as desired brightness, power consumption, and available space.
There are several software tools available for schematic design, such as KiCad, Eagle, and Altium Designer. These tools allow you to create a digital representation of your circuit and generate a bill of materials (BOM) for your components.
PCB Layout
Once your schematic is complete, you can move on to the PCB layout. The layout determines the physical placement of components and the routing of traces on your board. When laying out your LED PCB, keep the following in mind:
- Component placement: Arrange your components in a logical and space-efficient manner, considering factors such as heat dissipation and signal integrity.
- Trace width: Ensure that your traces are wide enough to handle the expected current flow without excessive resistance or heat generation.
- Grounding: Provide adequate grounding for your components to minimize noise and ensure proper operation.
- Thermal management: Consider the use of thermal vias or heat sinks to dissipate heat generated by your LEDs and other components.
PCB layout software, such as the tools mentioned earlier, allows you to create a virtual representation of your board and generate the necessary files for manufacturing.
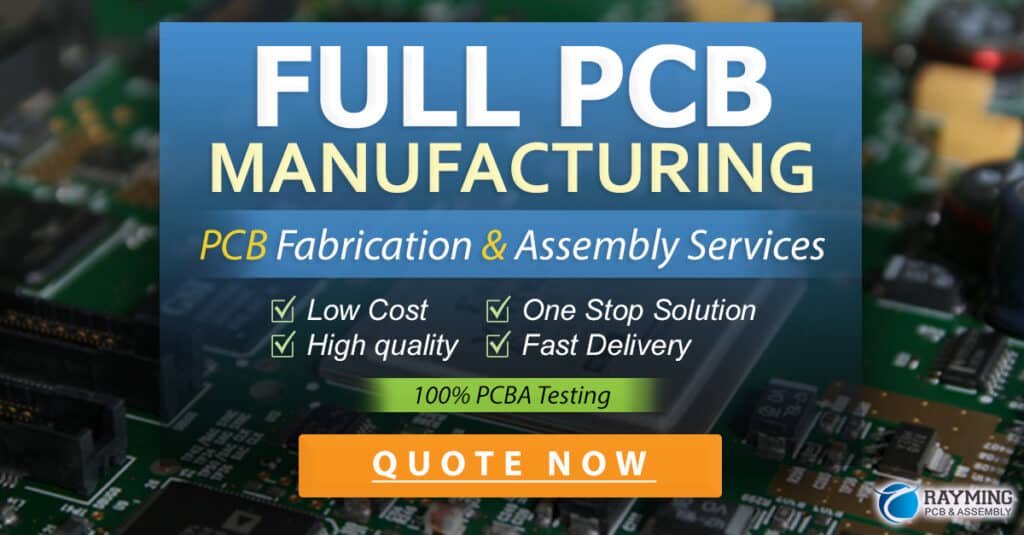
Manufacturing Your LED PCB
PCB Fabrication
With your PCB layout complete, you can now send your design files to a PCB fabrication service. These services will manufacture your board according to your specifications, typically offering options such as:
- Board material: Choose from a variety of substrate materials, such as FR-4, aluminum, or flexible PCBs.
- Copper weight: Select the appropriate copper weight for your traces, based on the expected current flow and desired trace width.
- Solder mask: Opt for a solder mask to protect your board from oxidation and improve its appearance.
- Silkscreen: Add a silkscreen layer to your board for component labeling and branding.
When selecting a PCB fabrication service, consider factors such as cost, turnaround time, and quality to ensure the best results for your project.
Component Sourcing
While your PCB is being manufactured, you can begin sourcing the components for your board. Refer to your BOM and purchase the necessary LEDs, resistors, and other components from reputable suppliers.
When sourcing components, consider the following:
- Quality: Choose components from reliable manufacturers to ensure optimal performance and longevity.
- Quantity: Purchase enough components for your project, including extras to account for potential damage or loss during assembly.
- Lead time: Be aware of the lead time for each component, as some may have longer delivery times than others.
Assembling Your LED PCB
Soldering Techniques
Once you have received your manufactured pcb and sourced components, you can begin the assembly process. The most common method for assembling LED PCBs is through soldering. There are two primary soldering techniques:
-
Through-hole soldering: This method involves inserting component leads through holes in the PCB and soldering them on the opposite side. Through-hole soldering is ideal for larger components and is generally easier for beginners.
-
Surface-mount soldering: Surface-mount components are placed directly on the surface of the PCB and soldered in place. This method requires more precise placement and soldering techniques but allows for a more compact board design.
When soldering your components, ensure that you use the appropriate soldering iron temperature and tip size for your specific components and board. Apply solder sparingly and avoid creating solder bridges between adjacent pads.
Inspection and Cleaning
After soldering your components, inspect your board for any potential issues, such as:
- Cold solder joints: These appear dull and lumpy and may result in poor electrical connections.
- Solder bridges: Accidentally connecting adjacent pads with excess solder can cause short circuits.
- Damaged components: Check for any components that may have been damaged during the soldering process.
If you identify any issues, carefully rework the affected areas using a soldering iron and desoldering tools as needed.
Once your board has been inspected and any issues have been addressed, clean your PCB using isopropyl alcohol and a soft brush to remove any flux residue or debris.
Testing and Troubleshooting Your LED PCB
Power-On Test
Before fully powering your LED PCB, perform a power-on test to ensure that there are no short circuits or other issues that could damage your components. To do this:
- Apply a current-limited power source to your board, starting with a low current setting.
- Gradually increase the current while monitoring the voltage across your LEDs and other components.
- If you notice any unusual voltage drops or excessive current draw, power off your board immediately and investigate the issue.
Functional Testing
Once your power-on test is successful, you can move on to functional testing. This involves verifying that your LEDs illuminate as expected and that any additional features, such as dimming or color-changing, function properly.
If you encounter any issues during functional testing, consider the following troubleshooting steps:
- Check for loose or damaged connections: Inspect your solder joints and component leads for any signs of damage or poor contact.
- Verify component values: Double-check that you have used the correct resistor values and LED specifications for your design.
- Review your schematic and layout: Look for any design errors that may be causing the issue, such as incorrect component placement or routing.
By systematically investigating and addressing any issues, you can ensure that your LED PCB functions as intended.
Advanced LED PCB Techniques
PWM Dimming
Pulse-width modulation (PWM) is a technique used to control the brightness of LEDs by rapidly turning them on and off at a high frequency. By varying the duty cycle of the PWM signal, you can achieve different levels of brightness.
To implement PWM dimming on your LED PCB, you will need to use a microcontroller or dedicated PWM driver IC. These components generate the necessary PWM signals and allow you to control the brightness of your LEDs programmatically.
Color Mixing
Color mixing involves combining multiple LEDs of different colors to produce a wide range of hues. This technique is commonly used in applications such as stage lighting, decorative lighting, and display backlighting.
To achieve color mixing on your LED PCB, you will need to use a combination of red, green, and blue (RGB) LEDs and a suitable control system. This can be accomplished using a microcontroller or a dedicated LED driver IC that supports color mixing.
Thermal Management
As LEDs generate heat during operation, proper thermal management is essential to ensure optimal performance and longevity. Inadequate thermal management can lead to reduced light output, color shifts, and premature failure of your LEDs.
To manage heat on your LED PCB, consider the following techniques:
- Thermal vias: Place thermal vias near your LEDs to transfer heat from the component to the opposite side of the board, where it can be dissipated more effectively.
- Heat sinks: Attach heat sinks to your LEDs or other heat-generating components to increase the surface area available for heat dissipation.
- Adequate copper pour: Ensure that your PCB has sufficient copper pour around your LEDs and other components to help spread heat evenly across the board.
By implementing proper thermal management techniques, you can ensure that your LED PCB operates reliably and maintains optimal performance over its lifetime.
FAQs
-
Q: What is the difference between through-hole and surface-mount LEDs?
A: Through-hole LEDs have longer leads that are inserted through holes in the PCB and soldered on the opposite side. Surface-mount LEDs are smaller and are soldered directly onto the surface of the PCB. Surface-mount LEDs allow for more compact board designs, while through-hole LEDs are easier to work with for beginners. -
Q: How do I calculate the current-limiting resistor value for my LEDs?
A: To calculate the current-limiting resistor value, use the following formula: R = (Vs – Vf) / If, where R is the resistor value, Vs is the supply voltage, Vf is the forward voltage of the LED, and If is the desired forward current. Be sure to choose a resistor with a power rating sufficient to handle the expected power dissipation. -
Q: Can I use a single current-limiting resistor for multiple LEDs in series?
A: Yes, you can use a single current-limiting resistor for multiple LEDs connected in series. However, ensure that the total forward voltage of the LEDs in series does not exceed the supply voltage, and that the resistor is sized appropriately to handle the expected current and power dissipation. -
Q: How do I ensure proper heat dissipation for my LED PCB?
A: To ensure proper heat dissipation, use thermal vias near your LEDs to transfer heat to the opposite side of the board, attach heat sinks to your LEDs or other heat-generating components, and provide adequate copper pour around your components to help spread heat evenly across the board. -
Q: Can I use my LED PCB with a battery power source?
A: Yes, you can use a battery power source for your LED PCB, provided that the battery voltage is compatible with your LED and resistor specifications. Be sure to consider the expected battery life and any additional power management circuitry that may be required, such as voltage regulators or low-battery indicators.
Conclusion
Creating a custom LED PCB can be a rewarding and educational experience, whether you are a hobbyist or a professional. By understanding the basics of LED technology, carefully designing your schematic and layout, and following best practices for manufacturing, assembly, and testing, you can create a high-quality LED PCB that meets your specific needs.
Remember to consider factors such as component selection, thermal management, and advanced techniques like PWM dimming and color mixing to take your LED pcb projects to the next level.
With the knowledge and skills gained from this comprehensive guide, you are now well-equipped to design, manufacture, and assemble your own custom LED PCBs. Happy creating!
Leave a Reply