What is PCB Testing?
PCB testing is a crucial step in the manufacturing process that verifies the functionality, reliability, and quality of printed circuit boards. It involves a series of techniques and procedures designed to detect defects, ensure proper connections, and validate the overall performance of the PCB.
Why is PCB Testing Important?
PCB testing plays a vital role in the electronics industry for several reasons:
- Quality Assurance: Testing helps identify and eliminate defects, ensuring that only high-quality PCBs are delivered to customers.
- Reliability: Thorough testing minimizes the risk of PCB failures, enhancing the reliability of the final product.
- Cost Savings: Detecting issues early in the manufacturing process saves time and resources that would otherwise be wasted on faulty PCBs.
- Compliance: Testing ensures that PCBs meet industry standards and regulatory requirements.
PCB Testing Methods
1. In-Circuit Testing (ICT)
In-circuit testing is a comprehensive testing method that verifies the functionality of individual components on a PCB. It involves using specialized test fixtures and probes to access and test each component separately.
How In-Circuit Testing Works
- The PCB is placed in a custom-designed test fixture that aligns with the board’s test points.
- Spring-loaded probes or “bed of nails” make contact with the test points on the PCB.
- The test system applies stimuli and measures the response of each component, comparing it to predefined specifications.
- Any deviations from the expected values are flagged as potential defects.
Advantages of In-Circuit Testing
- Comprehensive testing of individual components
- High fault coverage
- Automated and fast testing process
- Ability to detect both manufacturing and component defects
Limitations of In-Circuit Testing
- Requires custom test fixtures, which can be expensive
- Limited access to components in high-density PCBs
- Difficulty testing certain components, such as ball grid arrays (BGAs)
2. Flying Probe Testing
Flying probe testing is an alternative to in-circuit testing that uses movable probes to access test points on the PCB. Instead of a fixed test fixture, the probes move across the board to perform tests on individual components.
Advantages of Flying Probe Testing
- Flexibility in testing different PCB designs
- No need for custom test fixtures
- Ability to test high-density PCBs and hard-to-reach components
Limitations of Flying Probe Testing
- Slower testing process compared to in-circuit testing
- Limited number of probes, which can affect test coverage
3. Automated Optical Inspection (AOI)
Automated optical inspection uses high-resolution cameras and image processing algorithms to visually inspect PCBs for defects. It compares the captured images to a reference image of a known good PCB to identify anomalies.
Advantages of AOI
- Non-contact testing method
- Fast inspection process
- Ability to detect surface-level defects, such as solder bridges and missing components
Limitations of AOI
- Limited to visual defects on the surface of the PCB
- Difficulty detecting issues beneath component packages
- Potential for false positives or false negatives
4. X-Ray Inspection
X-ray inspection uses X-ray imaging to examine the internal structure of a PCB, including solder joints and component connections. It is particularly useful for inspecting hidden or obscured areas of the board.
Advantages of X-Ray Inspection
- Non-destructive testing method
- Ability to inspect hidden solder joints and connections
- Effective for analyzing multi-layer PCBs and BGAs
Limitations of X-Ray Inspection
- Expensive equipment and setup
- Requires skilled operators to interpret X-ray images
- Potential health and safety concerns due to radiation exposure
5. Boundary Scan Testing
Boundary scan testing, also known as JTAG testing, is a method that utilizes built-in test circuitry within integrated circuits (ICs) to test the interconnections between components on a PCB. It follows the IEEE 1149.1 standard.
Advantages of Boundary Scan Testing
- Ability to test complex digital circuits
- No physical access required to test points
- Fault isolation and diagnosis capabilities
Limitations of Boundary Scan Testing
- Limited to ICs that support the JTAG standard
- Cannot test analog components or passive devices
6. Functional Testing
Functional testing verifies the overall functionality of a PCB by simulating real-world operating conditions. It involves applying input signals and measuring output responses to ensure that the PCB performs as intended.
Advantages of Functional Testing
- Tests the PCB under realistic operating conditions
- Verifies the overall system functionality
- Can detect issues not caught by other testing methods
Limitations of Functional Testing
- Requires specialized test equipment and software
- Time-consuming and labor-intensive
- Difficulty in identifying the root cause of failures
7. Burn-In Testing
Burn-in testing subjects PCBs to elevated temperatures and extended operating periods to identify early-life failures and ensure long-term reliability. It accelerates the aging process to weed out weak components.
Advantages of Burn-In Testing
- Identifies components prone to early failure
- Improves overall product reliability
- Reduces warranty claims and field failures
Limitations of Burn-In Testing
- Time-consuming process
- Requires specialized temperature-controlled chambers
- Potential for over-stressing components beyond normal operating conditions
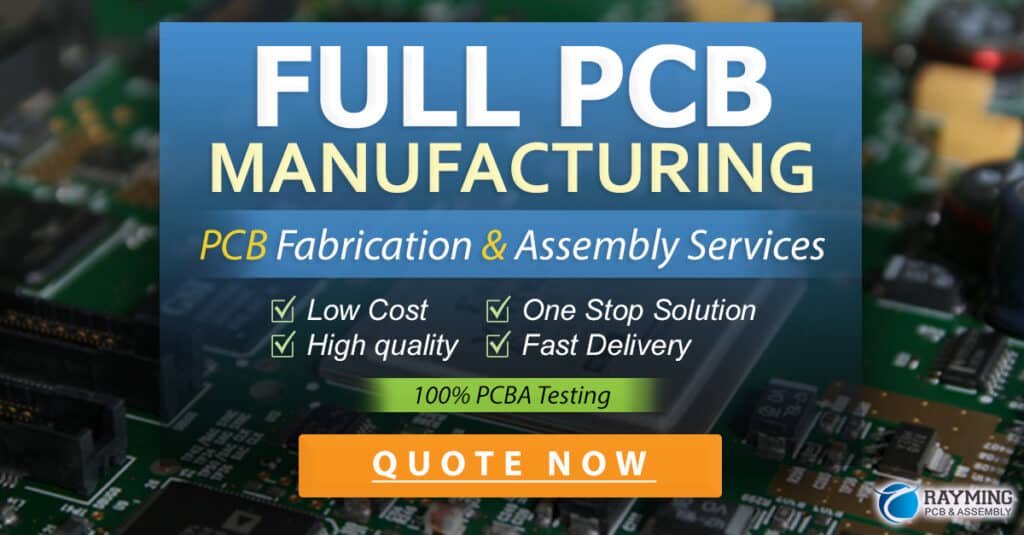
Frequently Asked Questions (FAQ)
-
Q: What is the difference between in-circuit testing and functional testing?
A: In-circuit testing focuses on testing individual components on a PCB, while functional testing verifies the overall functionality of the PCB under real-world operating conditions. -
Q: Can in-circuit testing detect all types of PCB defects?
A: While in-circuit testing is comprehensive, it may have limitations in detecting certain defects, such as those related to BGA packages or high-density PCBs. -
Q: Is X-ray inspection safe for operators?
A: X-ray inspection requires proper safety measures and trained operators to minimize radiation exposure risks. Manufacturers must follow safety guidelines and regulations when using X-ray equipment. -
Q: How does boundary scan testing work?
A: Boundary scan testing utilizes built-in test circuitry within ICs to test the interconnections between components on a PCB. It follows the IEEE 1149.1 standard, also known as JTAG. -
Q: What are the benefits of performing burn-in testing on PCBs?
A: Burn-in testing helps identify early-life failures and weak components by subjecting PCBs to elevated temperatures and extended operating periods. This improves overall product reliability and reduces warranty claims and field failures.
Conclusion
PCB testing is a critical aspect of the electronics manufacturing process, ensuring the quality, reliability, and functionality of printed circuit boards. From in-circuit testing to burn-in testing, each method offers unique advantages and limitations. By employing a combination of these testing techniques, manufacturers can comprehensively validate PCBs and deliver high-quality products to their customers.
As technology advances and PCBs become more complex, the importance of effective testing methods cannot be overstated. Manufacturers must continually adapt and refine their testing processes to keep pace with industry demands and ensure the reliability of their products.
By understanding the various PCB testing methods and their applications, engineers and technicians can make informed decisions when designing and manufacturing PCBs. Investing in the right testing equipment, training, and processes will ultimately lead to improved product quality, customer satisfaction, and business success in the competitive electronics industry.
Leave a Reply