Introduction to Custom PCB
Custom printed circuit boards (PCBs) are designed and manufactured to meet specific requirements for electronic devices. Unlike standard PCBs, custom PCBs are tailored to fit the unique needs of a particular application, offering several advantages over off-the-shelf solutions. However, custom PCBs also come with certain drawbacks that should be considered before opting for this approach.
In this article, we will explore the pros and cons of custom PCBs, helping you make an informed decision when designing and manufacturing electronic devices.
Advantages of Custom PCB
1. Tailored to Specific Requirements
One of the primary benefits of custom PCBs is that they are designed to meet the specific requirements of your electronic device. This means that you can optimize the PCB layout, component placement, and overall functionality to suit your needs. By tailoring the PCB to your application, you can improve the device’s performance, reliability, and efficiency.
2. Reduced Size and Weight
Custom PCBs allow you to minimize the size and weight of your electronic device. By designing a PCB that fits your exact specifications, you can eliminate unnecessary components and optimize the layout for a more compact and lightweight solution. This is particularly important for applications where space is limited or where weight reduction is crucial, such as in aerospace, automotive, and wearable technology.
3. Improved Reliability and Durability
Custom PCBs are designed with your specific application in mind, which means that you can choose materials and components that are best suited for the operating environment. This can include selecting high-quality substrates, copper traces, and protective coatings that enhance the PCB’s reliability and durability. By optimizing the PCB design for your application, you can reduce the risk of failures and extend the device’s lifespan.
4. Cost-Effective for Large-Scale Production
While custom PCBs may have higher upfront costs compared to standard PCBs, they can be more cost-effective for large-scale production. By designing a PCB that is optimized for your specific application, you can reduce the number of components required, simplify the assembly process, and minimize the risk of errors. This can lead to lower overall production costs, especially when manufacturing large quantities of devices.
5. Intellectual Property Protection
Custom PCBs offer a level of intellectual property protection that is not available with standard PCBs. By designing a unique PCB layout and incorporating proprietary components, you can make it more difficult for competitors to reverse-engineer your device. This can help safeguard your intellectual property and maintain a competitive advantage in the market.
Disadvantages of Custom PCB
1. Higher Upfront Costs
One of the main drawbacks of custom PCBs is the higher upfront costs associated with designing and manufacturing them. Unlike standard PCBs, which are readily available and can be purchased in small quantities, custom PCBs require specialized design and manufacturing processes. This can involve additional expenses for design software, prototyping, and tooling, which can be significant for small-scale production runs.
2. Longer Lead Times
Custom PCBs typically have longer lead times compared to standard PCBs. This is because the design and manufacturing processes are more complex and require additional time for planning, prototyping, and testing. Longer lead times can be a challenge for projects with tight deadlines or for companies that need to bring products to market quickly.
3. Minimum Order Quantities
Many PCB manufacturers have minimum order quantities (MOQs) for custom PCBs, which can be a barrier for small-scale production or prototyping. MOQs can vary depending on the complexity of the design, the materials used, and the manufacturing process. This can make custom PCBs less feasible for low-volume applications or for companies with limited budgets.
4. Design Complexity
Custom PCBs often involve more complex designs compared to standard PCBs. This can include incorporating advanced features, such as high-density interconnects (HDI), embedded components, or flexible substrates. Designing complex PCBs requires specialized knowledge and skills, which can be a challenge for companies that lack in-house expertise. Additionally, complex designs may require more iterations and testing to ensure optimal performance and reliability.
5. Supply Chain Risks
Custom PCBs may involve using specialized components or materials that are not widely available. This can create supply chain risks, as the availability and pricing of these components can be subject to market fluctuations or supplier issues. If a key component becomes unavailable or experiences a significant price increase, it can impact the production and profitability of the custom PCB.
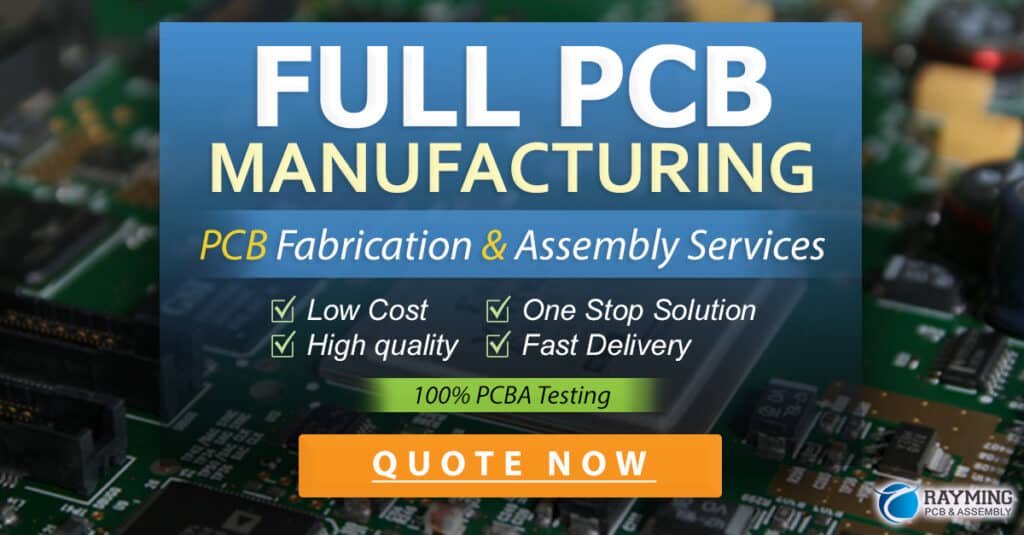
Comparison of Custom PCB and Standard PCB
Factor | Custom PCB | Standard PCB |
---|---|---|
Design Flexibility | High | Low |
Size and Weight | Optimized | Fixed |
Reliability and Durability | High | Moderate |
Cost-Effectiveness (Large-Scale) | High | Moderate |
Intellectual Property Protection | High | Low |
Upfront Costs | High | Low |
Lead Times | Longer | Shorter |
Minimum Order Quantities | Higher | Lower |
Design Complexity | High | Low |
Supply Chain Risks | Higher | Lower |
When to Choose Custom PCB
Custom PCBs are best suited for applications that require specific functionality, high performance, or unique form factors. Some scenarios where custom PCBs are recommended include:
- Specialized applications with unique requirements
- Devices that require miniaturization or weight reduction
- High-reliability applications, such as aerospace, medical, or automotive
- Large-scale production runs where cost optimization is crucial
- Applications that involve proprietary technology or intellectual property
Frequently Asked Questions (FAQ)
1. What is the difference between a custom PCB and a standard PCB?
A custom PCB is designed and manufactured to meet specific requirements for a particular application, while a standard PCB is a generic, off-the-shelf solution that is readily available and can be used for a variety of applications.
2. How much does a custom pcb cost?
The cost of a custom PCB depends on several factors, including the complexity of the design, the materials used, the manufacturing process, and the order quantity. Generally, custom PCBs have higher upfront costs compared to standard PCBs, but they can be more cost-effective for large-scale production.
3. What are the benefits of using a custom PCB?
Custom PCBs offer several benefits, including design flexibility, optimized size and weight, improved reliability and durability, cost-effectiveness for large-scale production, and intellectual property protection.
4. What are the disadvantages of using a custom PCB?
The main disadvantages of custom PCBs include higher upfront costs, longer lead times, minimum order quantities, design complexity, and supply chain risks.
5. When should I choose a custom PCB over a standard PCB?
Custom PCBs are best suited for applications that require specific functionality, high performance, or unique form factors. They are recommended for specialized applications, devices that require miniaturization or weight reduction, high-reliability applications, large-scale production runs, and applications that involve proprietary technology or intellectual property.
Conclusion
Custom PCBs offer numerous advantages over standard PCBs, including design flexibility, optimized size and weight, improved reliability and durability, cost-effectiveness for large-scale production, and intellectual property protection. However, they also come with certain drawbacks, such as higher upfront costs, longer lead times, minimum order quantities, design complexity, and supply chain risks.
When deciding between a custom PCB and a standard PCB, it is essential to consider the specific requirements of your application, the production scale, and the available resources. Custom PCBs are best suited for specialized applications that demand high performance, unique form factors, or proprietary technology.
By understanding the pros and cons of custom PCBs and carefully evaluating your needs, you can make an informed decision that balances the benefits and drawbacks of this approach to electronic device design and manufacturing.
Leave a Reply