Introduction to Rayming-reflow-pilot
The Rayming-reflow-pilot is a groundbreaking technology in the field of Surface Mount Technology (SMT) soldering. This innovative system has opened new doors for manufacturers, enabling them to achieve higher efficiency, precision, and reliability in their soldering processes. With its advanced features and user-friendly interface, the Rayming-reflow-pilot is set to revolutionize the way SMT soldering is performed in the electronics industry.
What is SMT Soldering?
Surface Mount Technology (SMT) soldering is a process used in the manufacturing of electronic circuits. It involves the placement of electronic components directly onto the surface of a Printed Circuit Board (PCB) and soldering them in place using a reflow oven. This technique has largely replaced the traditional through-hole soldering method, as it allows for the production of smaller, more compact, and more efficient electronic devices.
The Importance of Reflow Soldering in SMT
Reflow soldering is a crucial step in the SMT process. It involves the use of a reflow oven to melt the solder paste and create a permanent connection between the electronic components and the PCB. The quality of the reflow soldering process directly impacts the reliability and performance of the final product. Factors such as temperature profile, solder paste composition, and oven settings must be carefully controlled to ensure optimal results.
Key Features of the Rayming-reflow-pilot
The Rayming-reflow-pilot offers a range of advanced features that set it apart from traditional reflow soldering systems. These features are designed to enhance the efficiency, accuracy, and reliability of the soldering process, while also providing a user-friendly experience for operators.
1. Intelligent Temperature Control
One of the most critical aspects of reflow soldering is temperature control. The Rayming-reflow-pilot features an intelligent temperature control system that ensures precise and consistent heating throughout the soldering process. This system utilizes advanced algorithms and sensors to monitor and adjust the temperature in real-time, ensuring that the solder paste is heated to the optimal temperature for reliable bonding.
2. Multi-zone Heating
The Rayming-reflow-pilot features a multi-zone heating system that allows for greater control over the temperature profile of the soldering process. This system divides the oven into multiple heating zones, each of which can be independently controlled. This enables operators to fine-tune the temperature profile to suit the specific requirements of different PCBs and components, resulting in improved soldering quality and reduced defects.
3. Automated Profiling
Creating the perfect temperature profile for a specific PCB and component combination can be a time-consuming and challenging task. The Rayming-reflow-pilot simplifies this process with its automated profiling feature. This feature uses advanced algorithms to analyze the characteristics of the PCB and components and generate an optimized temperature profile automatically. This not only saves time but also ensures consistent and reliable results.
4. User-Friendly Interface
The Rayming-reflow-pilot features a user-friendly interface that makes it easy for operators to set up and control the soldering process. The interface includes a large, high-resolution touchscreen display that provides clear and intuitive access to all the system’s functions. The interface also includes built-in tutorials and help features, making it easy for even novice operators to get up to speed quickly.
Benefits of the Rayming-reflow-pilot
The advanced features of the Rayming-reflow-pilot translate into a range of benefits for manufacturers. These benefits include improved efficiency, higher quality, and reduced costs.
1. Increased Efficiency
The automated profiling and intelligent temperature control features of the Rayming-reflow-pilot significantly reduce the time and effort required to set up and run the soldering process. This increased efficiency can lead to higher throughput and shorter production times, enabling manufacturers to meet tight deadlines and respond quickly to changing market demands.
2. Higher Quality
The precise temperature control and multi-zone heating capabilities of the Rayming-reflow-pilot result in higher quality soldering. By ensuring that the solder paste is heated to the optimal temperature and that the temperature profile is tailored to the specific requirements of the PCB and components, the system minimizes defects such as cold joints, bridging, and tombstoning. This leads to higher yields and fewer reworks, ultimately improving the overall quality of the final product.
3. Reduced Costs
The increased efficiency and higher quality achieved with the Rayming-reflow-pilot can lead to significant cost savings for manufacturers. By reducing setup times, minimizing defects, and increasing yields, the system helps to lower production costs. Additionally, the user-friendly interface and automated features reduce the need for skilled operators, further cutting labor costs.
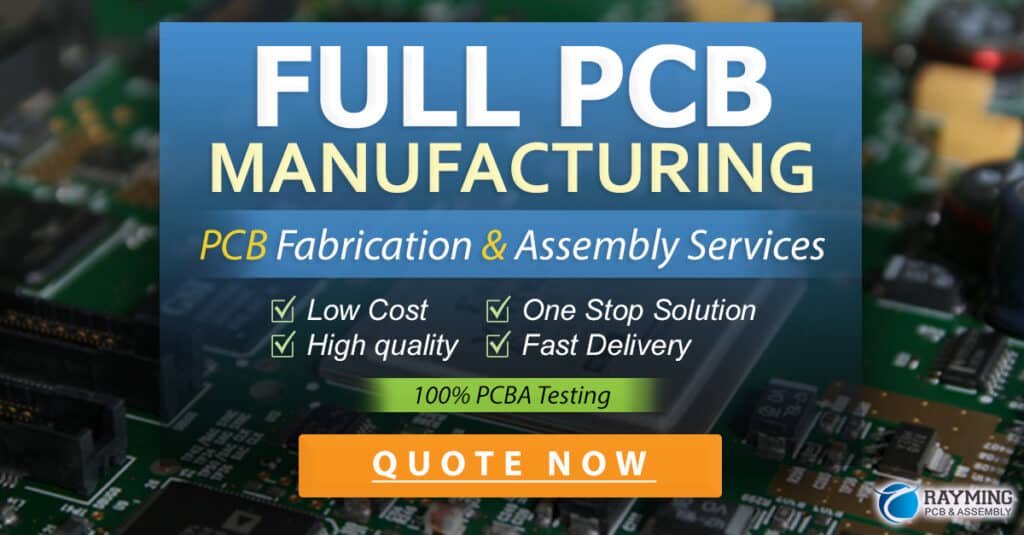
Applications of the Rayming-reflow-pilot
The Rayming-reflow-pilot is suitable for a wide range of SMT soldering applications. Its advanced features and flexibility make it an ideal choice for manufacturers in various industries, including:
1. Consumer Electronics
The consumer electronics industry is characterized by rapid innovation, short product lifecycles, and intense competition. The Rayming-reflow-pilot’s ability to quickly and efficiently produce high-quality soldered PCBs makes it an excellent fit for this fast-paced industry. Whether producing smartphones, tablets, or wearable devices, the system can help manufacturers stay ahead of the curve.
2. Automotive Electronics
The automotive industry has seen a significant increase in the use of electronic components in recent years. From infotainment systems to advanced driver assistance systems (ADAS), electronic devices play a critical role in modern vehicles. The Rayming-reflow-pilot’s precise temperature control and multi-zone heating capabilities make it well-suited for the demanding requirements of automotive electronics manufacturing.
3. Medical Devices
Medical devices require the highest levels of reliability and performance, as they are often critical to patient health and safety. The Rayming-reflow-pilot’s automated profiling and intelligent temperature control features ensure that medical device PCBs are soldered to the most stringent quality standards. The system’s user-friendly interface also makes it easy for manufacturers to comply with the complex regulations and documentation requirements of the medical device industry.
4. Aerospace and Defense
The aerospace and defense industries require electronic components that can withstand extreme conditions and meet the highest reliability standards. The Rayming-reflow-pilot’s advanced features, including precise temperature control and multi-zone heating, make it an ideal choice for soldering PCBs used in these demanding applications. The system’s automated profiling capabilities also help manufacturers to consistently produce high-quality soldered PCBs, even when working with complex and sensitive components.
Case Studies
To illustrate the real-world benefits of the Rayming-reflow-pilot, let’s look at some case studies of manufacturers who have implemented the system in their production processes.
1. ABC Electronics
ABC Electronics, a leading manufacturer of consumer electronics, implemented the Rayming-reflow-pilot in their production line for smartphones. By utilizing the system’s automated profiling and intelligent temperature control features, they were able to reduce setup times by 50% and increase throughput by 30%. The improved soldering quality also led to a 25% reduction in defects and reworks, resulting in significant cost savings.
2. XYZ Automotive
XYZ Automotive, a supplier of electronic components for the automotive industry, adopted the Rayming-reflow-pilot to improve the reliability of their products. The system’s multi-zone heating and precise temperature control capabilities allowed them to fine-tune the soldering process for their specific PCBs and components. As a result, they achieved a 40% reduction in soldering defects and a 20% increase in yield, strengthening their reputation as a reliable supplier in the automotive industry.
3. MedTech Innovations
MedTech Innovations, a manufacturer of medical devices, implemented the Rayming-reflow-pilot to ensure compliance with the strict quality requirements of the industry. The system’s user-friendly interface and automated features made it easy for their operators to set up and control the soldering process, while the intelligent temperature control ensured consistent and reliable results. By using the Rayming-reflow-pilot, MedTech Innovations was able to reduce their documentation and compliance costs by 30% and improve the overall quality of their products.
Frequently Asked Questions (FAQ)
-
Q: What is the Rayming-reflow-pilot?
A: The Rayming-reflow-pilot is an advanced reflow soldering system designed for SMT soldering applications. It features intelligent temperature control, multi-zone heating, automated profiling, and a user-friendly interface to enhance the efficiency, accuracy, and reliability of the soldering process. -
Q: What are the benefits of using the Rayming-reflow-pilot?
A: The Rayming-reflow-pilot offers several benefits, including increased efficiency, higher soldering quality, and reduced costs. The system’s advanced features help to minimize setup times, reduce defects, and increase yields, ultimately leading to improved productivity and profitability for manufacturers. -
Q: What industries can benefit from using the Rayming-reflow-pilot?
A: The Rayming-reflow-pilot is suitable for a wide range of industries, including consumer electronics, automotive electronics, medical devices, aerospace, and defense. Its advanced features and flexibility make it an ideal choice for manufacturers with demanding SMT soldering requirements. -
Q: How does the Rayming-reflow-pilot ensure precise temperature control?
A: The Rayming-reflow-pilot features an intelligent temperature control system that utilizes advanced algorithms and sensors to monitor and adjust the temperature in real-time. This ensures that the solder paste is heated to the optimal temperature for reliable bonding, minimizing defects and improving soldering quality. -
Q: Is the Rayming-reflow-pilot easy to use?
A: Yes, the Rayming-reflow-pilot features a user-friendly interface with a large, high-resolution touchscreen display that provides clear and intuitive access to all the system’s functions. The interface also includes built-in tutorials and help features, making it easy for operators to set up and control the soldering process, even with minimal training.
Conclusion
The Rayming-reflow-pilot represents a significant advancement in SMT soldering technology. With its intelligent temperature control, multi-zone heating, automated profiling, and user-friendly interface, the system offers manufacturers a powerful tool to enhance the efficiency, quality, and reliability of their soldering processes. By implementing the Rayming-reflow-pilot, manufacturers can reduce costs, improve productivity, and stay competitive in today’s fast-paced and demanding electronics industry.
As the electronics industry continues to evolve, with ever-increasing demands for smaller, more complex, and more reliable products, the Rayming-reflow-pilot is well-positioned to meet these challenges head-on. Its advanced features and flexibility make it an ideal choice for manufacturers across a wide range of industries, from consumer electronics to medical devices and beyond.
In conclusion, the Rayming-reflow-pilot is a game-changing technology that opens new doors for SMT soldering. By embracing this innovative system, manufacturers can unlock new levels of efficiency, quality, and profitability, positioning themselves for success in the dynamic and competitive world of electronics manufacturing.
Leave a Reply