Introduction to Placer-assisted pick-and-place
In the world of manufacturing and assembly, pick-and-place machines have become an essential tool for improving efficiency and accuracy. These machines are designed to pick up components from a specific location and place them onto a target area, such as a printed circuit board (PCB) or a product assembly line. While fully automated pick-and-place machines are widely used in high-volume production, placer camera-assisted manual pick-and-place machines offer a cost-effective and flexible alternative for smaller-scale operations or prototyping.
What is a Placer Camera-Assisted Manual Pick-and-Place Machine?
A placer camera-assisted manual pick-and-place machine is a semi-automated system that combines the precision of machine vision with the flexibility of human operators. The machine consists of a camera mounted above the work area, a display screen, and a manual placement tool. The camera captures images of the components and the target area, while the display screen provides visual guidance to the operator for accurate component placement.
Benefits of Using a Placer Camera-Assisted Manual Pick-and-Place Machine
- Cost-effective solution for low-volume production or prototyping
- Flexibility to handle a wide range of component sizes and types
- Improved accuracy and consistency compared to fully manual placement
- Reduced operator fatigue and strain
- Faster setup times and changeovers between different products
How Placer Camera-Assisted Manual Pick-and-Place Machines Work
Machine Vision System
The heart of a placer camera-assisted manual pick-and-place machine is its machine vision system. The camera, typically a high-resolution digital camera, captures images of the components and the target area. These images are then processed by software algorithms to determine the position, orientation, and quality of the components.
Image Processing Algorithms
The image processing algorithms used in placer camera-assisted manual pick-and-place machines can vary depending on the specific application and the types of components being handled. Some common algorithms include:
- Pattern matching: This algorithm compares the captured image to a pre-defined template to determine the position and orientation of the component.
- Edge detection: This algorithm identifies the edges of the component in the image, allowing the software to determine its size and shape.
- Color analysis: This algorithm can distinguish between different colored components, which is useful for applications involving color-coded parts.
Operator Guidance
Once the machine vision system has processed the images, the software generates visual guidance for the operator on the display screen. This guidance typically includes:
- A live video feed of the work area, with the target placement location highlighted
- Crosshairs or other visual indicators to help the operator align the component correctly
- Real-time feedback on the placement accuracy and quality
The operator uses the manual placement tool, which may be a tweezers, vacuum pen, or gripper, to pick up the component and place it onto the target area, following the visual guidance provided by the machine.
Applications of Placer Camera-Assisted Manual Pick-and-Place Machines
Electronics Assembly
One of the most common applications for placer camera-assisted manual pick-and-place machines is in the assembly of electronic components onto PCBs. These machines are particularly well-suited for prototyping or low-volume production runs, where the flexibility to handle a variety of component types and sizes is important.
Component Type | Size Range | Placement Accuracy |
---|---|---|
Chip Resistors | 0201 – 2512 | ±0.1 mm |
Chip Capacitors | 0201 – 2225 | ±0.1 mm |
SOT Packages | SOT-23, SOT-223, etc. | ±0.15 mm |
QFP Packages | LQFP, TQFP, etc. | ±0.2 mm |
Medical Device Assembly
Placer camera-assisted manual pick-and-place machines are also used in the assembly of medical devices, such as catheters, sensors, and implantable devices. The high precision and visual guidance provided by these machines ensure that the small and delicate components are assembled accurately and consistently.
Automotive Component Assembly
In the automotive industry, placer camera-assisted manual pick-and-place machines are used for assembling small components, such as sensors, connectors, and switches. The flexibility of these machines allows for quick changeovers between different product variants, making them ideal for the high-mix, low-volume production often found in the automotive sector.
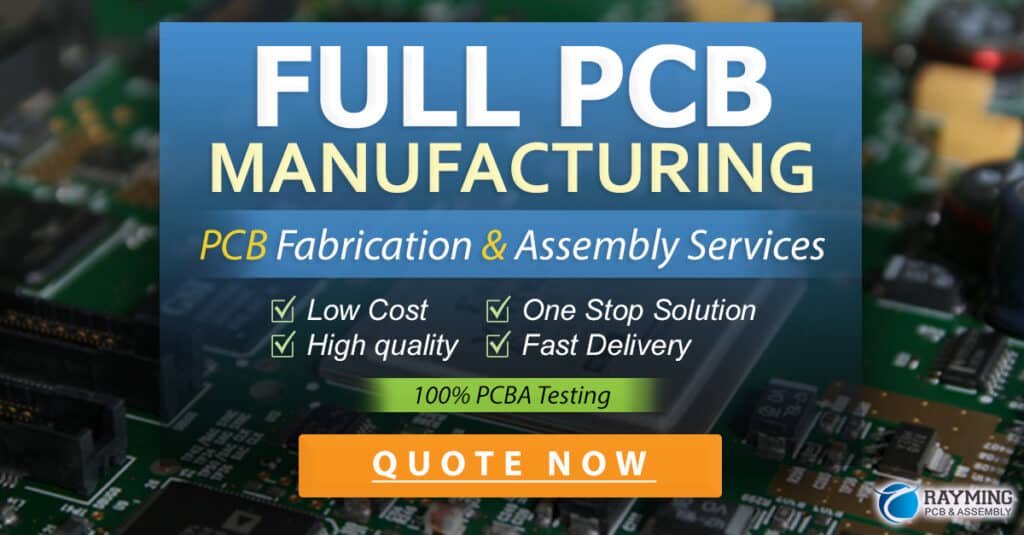
Advantages of Placer Camera-Assisted Manual Pick-and-Place over Fully Automated Systems
While fully automated pick-and-place machines offer high speed and throughput, placer camera-assisted manual pick-and-place machines have several advantages that make them a better choice for certain applications:
- Lower initial investment: Placer camera-assisted manual pick-and-place machines are significantly less expensive than fully automated systems, making them more accessible for small businesses and startups.
- Greater flexibility: Manual systems can easily accommodate changes in component types, sizes, and placement locations, without requiring extensive reprogramming or retooling.
- Shorter setup times: With a placer camera-assisted manual pick-and-place machine, operators can quickly set up a new job by simply loading the appropriate component reels and programming the target placement locations.
- Easier maintenance: Manual systems have fewer complex mechanical and electronic components, making them easier and less costly to maintain compared to fully automated machines.
Choosing the Right Placer Camera-Assisted Manual Pick-and-Place Machine
When selecting a placer camera-assisted manual pick-and-place machine, there are several key factors to consider:
- Camera resolution: Higher resolution cameras provide more detailed images, allowing for more accurate component recognition and placement.
- Software capabilities: Look for a machine with software that offers a wide range of image processing algorithms and is easy to use and customize for your specific application.
- Placement accuracy: Consider the placement accuracy required for your components and choose a machine that meets or exceeds those requirements.
- Ergonomics: Since an operator will be using the machine for extended periods, it’s important to choose a machine with a comfortable and ergonomic design to reduce fatigue and strain.
Training and Best Practices for Operators
To ensure optimal performance and accuracy when using a placer camera-assisted manual pick-and-place machine, it’s important to provide proper training for operators and follow best practices:
- Familiarize operators with the machine: Provide comprehensive training on the machine’s features, software, and operation to ensure that operators are comfortable and confident when using the machine.
- Maintain a clean and organized work area: Keep the work area clean and free of debris to prevent contamination of components and ensure clear images for the machine vision system.
- Use appropriate lighting: Ensure that the work area is well-lit and free of glare or shadows, which can interfere with the machine vision system’s ability to accurately recognize components.
- Handle components carefully: Train operators to handle components gently and avoid damaging them during the pick-and-place process.
- Regularly calibrate the machine: Perform regular calibration of the camera and software to maintain accurate component recognition and placement.
Future Trends in Placer Camera-Assisted Manual Pick-and-Place Technology
As technology advances, placer camera-assisted manual pick-and-place machines are expected to become even more sophisticated and user-friendly. Some potential future developments include:
- Improved machine vision: More advanced cameras and image processing algorithms will enable machines to recognize and place an even wider range of component types and sizes with greater accuracy.
- Augmented reality guidance: Integrating augmented reality technology into the display screen could provide operators with more intuitive and immersive visual guidance for component placement.
- Collaborative robots: Combining placer camera-assisted manual pick-and-place machines with collaborative robots could create a more efficient and flexible assembly process, with the robot handling the repetitive tasks while the operator focuses on quality control and exception handling.
- Cloud-based software: Developing cloud-based software for placer camera-assisted manual pick-and-place machines could enable remote monitoring, data analysis, and software updates, improving the overall efficiency and reliability of the machines.
Frequently Asked Questions (FAQ)
-
Q: What is the typical placement accuracy of a placer camera-assisted manual pick-and-place machine?
A: The placement accuracy of these machines can vary depending on the specific model and application, but most machines offer an accuracy of ±0.1 mm to ±0.2 mm for common component types. -
Q: Can a placer camera-assisted manual pick-and-place machine handle both SMT and through-hole components?
A: Yes, most machines are capable of handling both surface mount (SMT) and through-hole components, as long as the appropriate placement tools and software settings are used. -
Q: How long does it take to set up a new job on a placer camera-assisted manual pick-and-place machine?
A: Setup times can vary depending on the complexity of the job, but most machines allow for quick changeovers in less than 30 minutes. -
Q: What is the maximum component size that a placer camera-assisted manual pick-and-place machine can handle?
A: The maximum component size depends on the specific machine and its placement tool options, but most machines can handle components up to 50 mm in size. -
Q: Can a placer camera-assisted manual pick-and-place machine be used for other applications besides PCB assembly?
A: Yes, these machines can be adapted for a wide range of applications that require precise component placement, such as medical device assembly, automotive component assembly, and even jewelry making.
Conclusion
Placer camera-assisted manual pick-and-place machines offer a cost-effective and flexible solution for low-volume production, prototyping, and applications that require precise component placement. By combining the accuracy of machine vision with the adaptability of human operators, these machines bridge the gap between fully manual and fully automated assembly processes. As technology continues to advance, placer camera-assisted manual pick-and-place machines are poised to become even more capable and user-friendly, making them an essential tool for manufacturers across a wide range of industries.
Leave a Reply