Introduction to Rayming Stencil-Mate and its Printing Capabilities
The Rayming Stencil-Mate is a high-precision stencil printer designed for the electronics manufacturing industry. It is capable of printing solder paste onto printed circuit boards (PCBs) with exceptional accuracy and consistency, making it an ideal solution for both prototyping and low-volume production runs. One of the key factors that determine the effectiveness of a stencil printer is its ability to print fine-pitch components, which is directly related to the resolution of the printer.
What is Printing Resolution?
Printing resolution refers to the smallest feature size that a printer can accurately reproduce. In the context of stencil printing, resolution is typically measured in microns (μm) and relates to the smallest aperture size that can be reliably printed. The higher the resolution, the smaller the components that can be successfully printed.
Factors Affecting Printing Resolution
Several factors can influence the printing resolution of a stencil printer, including:
-
Stencil thickness: Thinner stencils generally allow for higher resolution printing, as they can accommodate smaller apertures without compromising the structural integrity of the stencil.
-
Stencil material: The choice of stencil material can impact the resolution, as some materials, such as nickel-plated stencils, offer better performance for fine-pitch printing compared to standard stainless steel stencils.
-
Solder paste properties: The rheology and particle size of the solder paste can affect the printability of fine-pitch components. Solder pastes with smaller particle sizes and optimized rheological properties are better suited for high-resolution printing.
-
Printer settings: Proper printer setup, including squeegee pressure, speed, and separation distance, is crucial for achieving optimal printing results and maintaining high resolution.
Rayming Stencil-Mate Resolution Capabilities
The Rayming Stencil-Mate is designed to handle a wide range of component sizes, from large chip components to fine-pitch SMD (Surface Mount Device) packages. The printer’s resolution capabilities are as follows:
Minimum Aperture Size
The Rayming Stencil-Mate can print apertures as small as 0.3mm (300μm) with a stencil thickness of 0.1mm (100μm). This allows for the successful printing of components with a pitch (distance between the centers of adjacent pads) as fine as 0.4mm (400μm).
Component Size Compatibility
The following table provides an overview of the component sizes that can be printed using the Rayming Stencil-Mate:
Component Package | Minimum Pitch |
---|---|
0201 (0603 metric) | 0.4mm |
0402 (1005 metric) | 0.5mm |
0603 (1608 metric) | 0.8mm |
0805 (2012 metric) | 1.0mm |
1206 (3216 metric) | 1.5mm |
SOIC | 1.27mm |
QFP | 0.5mm |
BGA | 0.8mm |
Please note that these values are based on typical industry standards and may vary depending on the specific component manufacturer and stencil design.
Stencil Design Considerations
To achieve the best printing results with the Rayming Stencil-Mate, it is essential to follow proper stencil design guidelines. Some key considerations include:
-
Aperture shape: The shape of the apertures should be optimized for the specific component being printed. For example, rectangular apertures are typically used for chip components, while circular or square apertures are used for BGA and QFP packages.
-
Aperture size: The aperture size should be slightly larger than the component pad to ensure proper solder paste coverage. A general rule of thumb is to use an aperture size that is 10-20% larger than the pad size.
-
Stencil thickness: The stencil thickness should be selected based on the desired solder paste volume and the pitch of the components being printed. Thinner stencils (e.g., 0.1mm) are better suited for fine-pitch components, while thicker stencils (e.g., 0.15mm or 0.2mm) are used for larger components or higher solder paste volumes.
-
Aperture wall angle: The aperture wall angle should be optimized to ensure proper solder paste release from the stencil. A wall angle of 5-7 degrees is typically recommended for most applications.
By following these design guidelines and leveraging the resolution capabilities of the Rayming Stencil-Mate, users can achieve high-quality solder paste prints for a wide range of component sizes.
Best Practices for High-Resolution Printing
To ensure consistent and reliable high-resolution printing with the Rayming Stencil-Mate, consider the following best practices:
-
Stencil cleaning: Regularly clean the stencil to prevent solder paste buildup and maintain print quality. Use an appropriate cleaning solution and follow the manufacturer’s recommended cleaning procedure.
-
Solder paste management: Ensure that the solder paste is properly stored and handled to maintain its rheological properties. Follow the paste manufacturer’s guidelines for storage temperature, shelf life, and printing conditions.
-
Printer maintenance: Perform regular maintenance on the Rayming Stencil-Mate, including cleaning the squeegee blades, inspecting the print head for damage or wear, and calibrating the printer as needed.
-
Print parameter optimization: Optimize the printer settings, such as squeegee pressure, speed, and separation distance, for each specific job to achieve the best print quality. Conduct test prints and adjust the parameters as necessary.
-
PCB support: Use appropriate PCB support systems, such as dedicated support pins or a custom-designed fixture, to prevent PCB warpage and ensure consistent print results.
By following these best practices and leveraging the resolution capabilities of the Rayming Stencil-Mate, users can achieve reliable and high-quality solder paste printing for a wide range of component sizes and pitches.
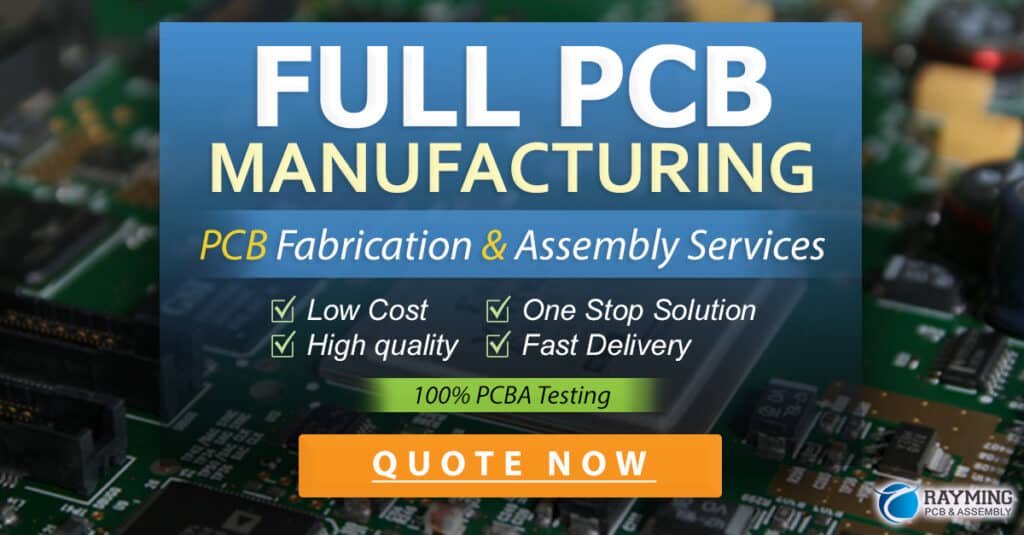
Frequently Asked Questions (FAQ)
-
What is the smallest component size that can be printed with the Rayming Stencil-Mate?
The Rayming Stencil-Mate can print components with a pitch as fine as 0.4mm (400μm), such as 0201 (0603 metric) chip components, when using a stencil thickness of 0.1mm (100μm) and an aperture size of 0.3mm (300μm). -
Can the Rayming Stencil-Mate print BGA components?
Yes, the Rayming Stencil-Mate is capable of printing BGA components with a minimum pitch of 0.8mm. To achieve the best results, use a stencil thickness appropriate for the desired solder paste volume and ensure proper aperture design. -
What stencil thickness should I use for fine-pitch components?
For fine-pitch components, such as 0201 (0603 metric) or 0402 (1005 metric) chip components, a stencil thickness of 0.1mm (100μm) is recommended. This allows for the creation of smaller apertures while maintaining the structural integrity of the stencil. -
How often should I clean the stencil when printing high-resolution components?
Stencil cleaning frequency depends on various factors, such as the solder paste type, printing volume, and environmental conditions. As a general guideline, clean the stencil every 4-8 hours of continuous printing or whenever print quality begins to degrade. For high-resolution printing, more frequent cleaning may be necessary to maintain optimal results. -
What solder paste is best suited for printing fine-pitch components with the Rayming Stencil-Mate?
When printing fine-pitch components, use a solder paste with a smaller particle size (Type 4 or Type 5) and optimized rheological properties. Consult with your solder paste supplier to select a paste that is specifically formulated for high-resolution printing applications.
Conclusion
The Rayming Stencil-Mate is a versatile and high-precision stencil printer capable of printing components with a minimum pitch of 0.4mm (400μm) when using a 0.1mm (100μm) thick stencil and 0.3mm (300μm) apertures. By following proper stencil design guidelines, implementing best practices for high-resolution printing, and leveraging the printer’s resolution capabilities, users can achieve consistent and reliable solder paste printing for a wide range of component sizes and pitches. As the electronics industry continues to push the boundaries of miniaturization, the Rayming Stencil-Mate is well-positioned to meet the evolving needs of PCB assembly and help manufacturers produce high-quality, densely populated circuit boards.
Leave a Reply