Composition of the Outer PCB
The outer PCB is typically composed of a copper layer laminated onto a substrate material. The most common substrate materials used in PCB manufacturing are:
Substrate Material | Characteristics |
---|---|
FR-4 | A flame-retardant epoxy laminate, widely used for its good mechanical and electrical properties |
Polyimide | A high-performance polymer offering excellent thermal stability and flexibility |
Teflon | A low-loss material with superior dielectric properties, ideal for high-frequency applications |
The copper layer on the outer PCB is usually applied through a process called electroplating. This involves depositing a thin layer of copper onto the substrate material using an electrical current. The thickness of the copper layer can vary depending on the specific requirements of the PCB, but it typically ranges from 0.5 oz to 2 oz per square foot.
Functions of the Outer PCB
Protection
One of the primary functions of the outer PCB is to protect the inner layers and components from external factors such as moisture, dust, and mechanical damage. The outer layer acts as a barrier, preventing contaminants from reaching the sensitive internal components of the PCB.
Component Mounting
The outer PCB provides a surface for mounting various electronic components, such as resistors, capacitors, and integrated circuits. These components are soldered onto the copper pads on the outer layer, establishing electrical connections between them and the rest of the circuit.
Electrical Connections
The copper traces on the outer PCB facilitate electrical connections between components and different layers of the board. These traces are created by selectively removing unwanted copper from the outer layer, leaving behind the desired conductive paths. The width and thickness of the traces are determined by factors such as the current-carrying requirements and the impedance characteristics of the circuit.
Communication with External Devices
The outer PCB often includes connectors, ports, or contact pads that enable communication between the PCB and external devices. For example, a USB connector on the outer layer allows the PCB to interface with a computer or other USB-compatible devices. Similarly, contact pads on the outer layer can be used for attaching the PCB to other boards or modules in a larger system.
Manufacturing Process
The manufacturing process for the outer PCB involves several steps, each of which contributes to the final quality and functionality of the layer.
-
Substrate Preparation: The substrate material is cut to the desired size and shape, and any necessary holes are drilled.
-
Copper Lamination: A thin layer of copper is laminated onto the substrate using heat and pressure.
-
Photoresist Application: A photosensitive material called photoresist is applied to the copper layer.
-
Exposure and Development: The photoresist is exposed to UV light through a patterned mask, which hardens the exposed areas. The unexposed areas are then removed using a developer solution, leaving behind the desired copper pattern.
-
Etching: The exposed copper is removed using an etchant solution, while the copper protected by the hardened photoresist remains intact.
-
Photoresist Removal: The remaining photoresist is stripped away, revealing the final copper pattern on the outer layer.
-
Surface Finish Application: A surface finish, such as solder mask or silkscreen, is applied to the outer layer to protect the copper and provide additional insulation.
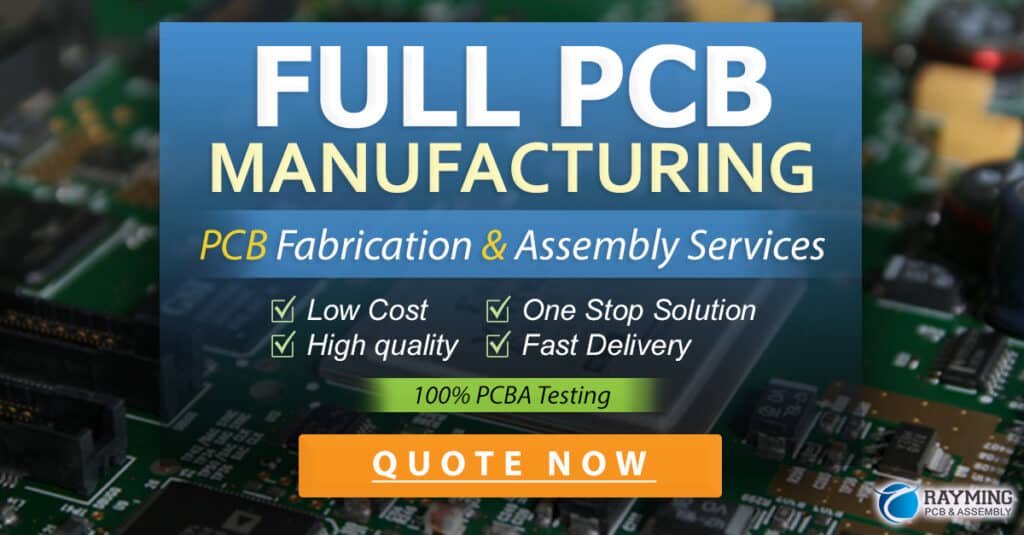
Key Considerations for Designers
When designing the outer PCB, there are several key considerations that designers must take into account to ensure optimal performance and reliability.
Trace Width and Spacing
The width and spacing of the copper traces on the outer PCB play a crucial role in determining the electrical characteristics of the circuit. Designers must carefully calculate the appropriate trace dimensions based on factors such as the current-carrying requirements, the desired impedance, and the available space on the board.
Electromagnetic Compatibility (EMC)
The outer PCB can have a significant impact on the electromagnetic compatibility of the overall circuit. Designers must consider factors such as signal integrity, crosstalk, and electromagnetic interference (EMI) when laying out the copper traces and placing components on the outer layer. Techniques such as proper grounding, shielding, and the use of ground planes can help mitigate EMC issues.
Thermal Management
The outer PCB also plays a role in thermal management, as it helps dissipate heat generated by the components mounted on its surface. Designers must ensure that the copper traces and pads are adequately sized to handle the expected current loads without overheating. In some cases, additional features such as thermal vias or heatsinks may be incorporated into the outer layer to enhance heat dissipation.
Manufacturing Constraints
Designers must also consider the manufacturing constraints associated with the outer PCB. Factors such as the minimum trace width and spacing, the size of the via holes, and the clearance between components can all impact the manufacturability of the board. Designers should work closely with the PCB manufacturer to ensure that the design is compatible with their specific manufacturing capabilities and tolerances.
FAQ
What is the difference between the outer PCB and the inner layers?
The outer PCB is the topmost and bottommost layers of a multi-layer PCB, while the inner layers are sandwiched between these outer layers. The outer layers primarily provide protection, component mounting, and external connectivity, while the inner layers are used for additional signal routing and power distribution.
Can the outer PCB have different thicknesses of copper?
Yes, the thickness of the copper on the outer PCB can vary depending on the specific requirements of the circuit. Common copper thicknesses range from 0.5 oz to 2 oz per square foot, with thicker copper being used for high-current or high-power applications.
What is the purpose of the solder mask on the outer PCB?
The solder mask is a protective layer applied to the outer PCB that covers the copper traces and pads, leaving only the areas intended for soldering exposed. It serves several purposes, including:
- Preventing accidental short circuits by insulating the copper traces
- Protecting the copper from oxidation and corrosion
- Providing a visual aid for identifying component placement and orientation
How does the choice of substrate material affect the outer PCB?
The choice of substrate material can have a significant impact on the performance and reliability of the outer PCB. For example, FR-4 is a common choice for general-purpose applications due to its good mechanical and electrical properties, while polyimide is preferred for flexible or high-temperature applications. The substrate material also affects factors such as the dielectric constant, dissipation factor, and thermal expansion coefficient of the outer layer.
What are some common surface finishes applied to the outer PCB?
Some common surface finishes applied to the outer PCB include:
- Hot Air Solder Leveling (HASL): A tin-lead alloy is applied to the exposed copper pads and then leveled using hot air.
- Electroless Nickel Immersion Gold (ENIG): A layer of nickel is deposited onto the copper, followed by a thin layer of gold to prevent oxidation.
- Organic Solderability Preservative (OSP): A thin, organic coating is applied to the copper to prevent oxidation and enhance solderability.
The choice of surface finish depends on factors such as the desired solderability, shelf life, and compatibility with the selected assembly process.
Conclusion
The outer layer of a PCB is a critical component that serves multiple functions, including protection, component mounting, electrical connectivity, and communication with external devices. The composition, manufacturing process, and key design considerations for the outer PCB all contribute to its overall performance and reliability.
By understanding the intricacies of the outer PCB, designers can make informed decisions that optimize the functionality and manufacturability of their circuit boards. From selecting the appropriate substrate material and copper thickness to carefully managing trace routing and component placement, the outer PCB plays a vital role in the success of any electronic device.
As technology continues to advance and the demand for more complex and compact electronic devices grows, the importance of the outer PCB will only continue to increase. By staying up-to-date with the latest design techniques and manufacturing processes, designers can ensure that their outer PCBs are well-equipped to meet the challenges of the future.
Leave a Reply