Why Was Lead Banned in Electronics Soldering?
For many decades, a eutectic tin-lead alloy composed of 63% tin (Sn) and 37% lead (Pb) was the predominant solder used in electronics assembly. However, concerns over the toxicity of lead and its harmful effects on human health and the environment led to the banning of lead in most consumer electronics.
Key reasons for the lead ban include:
- Lead is a toxic heavy metal that can accumulate in the body and cause serious health problems, especially in children.
- Improper disposal of lead-containing electronic waste can contaminate soil and groundwater.
- The RoHS directive, which took effect in 2006, restricted the use of lead and other hazardous substances in electrical and electronic equipment sold in the EU.
The move to lead-free soldering required the development of new solder alloys that could match or exceed the performance of tin-lead solders.
What Are the Challenges of Lead-Free Soldering?
Replacing tin-lead solders with lead-free alternatives presented several challenges for the electronics industry:
-
Higher melting points: Most lead-free solders have higher melting temperatures than tin-lead eutectic (which melts at 183°C). This requires higher soldering iron temperatures and can cause thermal stress on components.
-
Wetting and spreading: Lead-free solders often have poorer wetting and spreading characteristics compared to tin-lead, which can lead to incomplete joint formation and defects.
-
Tin whiskers: Some lead-free solders, particularly those with high tin content, are prone to the growth of tin whiskers – thin, conductive filaments that can cause short circuits.
-
Brittleness: Certain lead-free alloys, such as those containing high percentages of silver, can form brittle intermetallic compounds that reduce joint reliability.
To overcome these challenges, solder manufacturers developed specialized lead-free alloys optimized for different applications and process requirements.
Composition and Properties of HAL lead-free Alloys
Kester’s HAL (High-reliability Alloy) lead-free solder series comprises several alloys with varying compositions and properties. The most common HAL alloys are:
Alloy | Composition (wt%) | Melting Range (°C) | Key Properties |
---|---|---|---|
HAL-A | Sn96.5Ag3.0Cu0.5 | 217-220 | Good wetting, low cost |
HAL-B | Sn97.7Ag2.1Cu0.2 | 217-224 | Excellent wetting, low dross formation |
HAL-C | Sn95.5Ag4.0Cu0.5 | 217-219 | High strength, good thermal cycling performance |
HAL-D | Sn99.0Cu0.7Ag0.3 | 227-229 | Low silver content, reduced cost |
These alloys are designed to provide a balance of wetting, mechanical strength, thermal cycling performance, and cost-effectiveness. The choice of alloy depends on the specific application, substrate materials, and process parameters.
Advantages of HAL Lead-Free Alloys
HAL lead-free solders offer several advantages over other lead-free alternatives:
-
Optimized compositions: HAL alloys are formulated to provide the best combination of wetting, strength, and reliability for a wide range of applications.
-
Reduced tin whisker risk: The carefully controlled composition and microstructure of HAL alloys minimize the formation of tin whiskers.
-
Compatibility with existing processes: HAL solders are designed to be drop-in replacements for tin-lead solders, minimizing the need for extensive process changes.
-
Extensive testing and validation: Kester subjects HAL alloys to rigorous testing to ensure they meet the highest standards of performance and reliability.
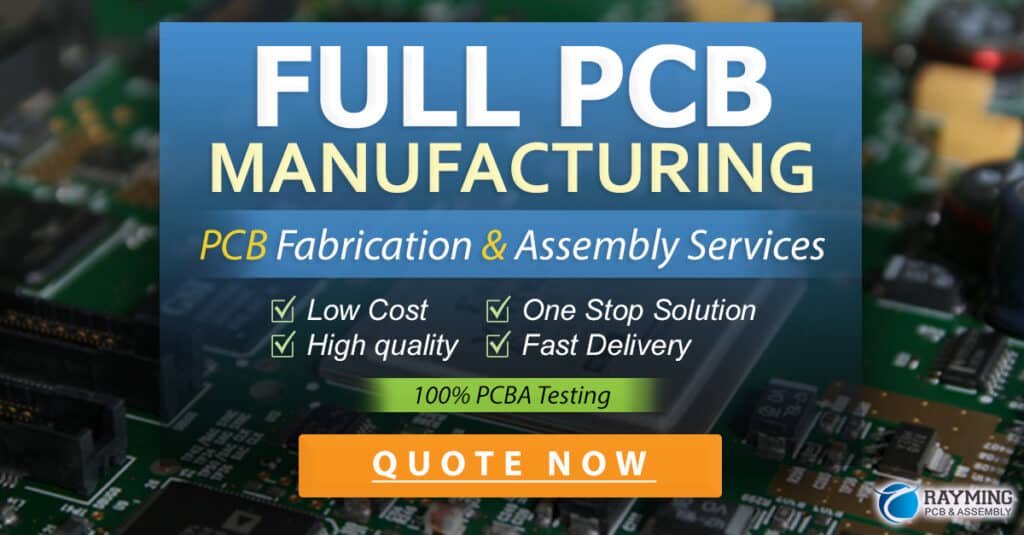
Applying HAL Lead-Free Solders in Electronics Manufacturing
To achieve the best results with HAL lead-free solders, consider the following guidelines:
-
Choose the appropriate alloy: Select the HAL alloy that best suits your application based on the required properties, substrate materials, and process conditions.
-
Optimize soldering parameters: Adjust soldering temperature, time, and flux selection to ensure proper wetting and joint formation. HAL solders generally require higher soldering temperatures than tin-lead.
-
Control the soldering environment: Maintain a clean, oxygen-free soldering environment to minimize oxidation and dross formation. Use nitrogen inerting where possible.
-
Manage thermal profiles: Carefully control the thermal profile during reflow soldering to avoid thermal shock and minimize intermetallic growth.
-
Implement quality control measures: Regularly inspect solder joints for defects and monitor process parameters to ensure consistency and reliability.
By following these guidelines and leveraging the advantages of HAL lead-free solders, electronics manufacturers can achieve high-quality, reliable lead-free solder joints that meet the demands of today’s applications.
Frequently Asked Questions (FAQ)
-
Q: Are HAL lead-free solders compliant with RoHS regulations?
A: Yes, all HAL lead-free solders are fully compliant with the RoHS directive and other global lead-free regulations. -
Q: Can HAL solders be used for both wave and reflow soldering?
A: Yes, HAL alloys are suitable for use in both wave and reflow soldering processes, as well as hand soldering applications. -
Q: How do HAL solders compare to tin-lead solders in terms of cost?
A: Lead-free solders, including HAL alloys, are generally more expensive than tin-lead solders due to the higher cost of raw materials (tin, silver, and copper). However, the cost difference has narrowed over time as lead-free soldering has become more widespread. -
Q: Are there any special handling or storage requirements for HAL solders?
A: HAL solders should be stored in a cool, dry environment to prevent oxidation and contamination. Proper handling techniques, such as wearing gloves and using clean tools, should be employed to maintain the integrity of the solder. -
Q: Can HAL solders be used for high-reliability applications, such as aerospace or medical devices?
A: Yes, HAL alloys are designed to meet the stringent performance and reliability requirements of high-reliability applications. However, it is essential to carefully evaluate the specific needs of each application and validate the solder’s performance through rigorous testing.
The transition to lead-free soldering, driven by environmental concerns and regulations like RoHS, has necessitated the development of new solder alloys that can replace traditional tin-lead solders. Kester’s HAL lead-free solder series offers a range of alloys with optimized compositions and properties to meet the challenges of lead-free soldering.
By understanding the advantages and proper application of HAL lead-free solders, electronics manufacturers can ensure the production of high-quality, reliable solder joints that comply with global lead-free regulations while meeting the performance demands of modern applications.
Leave a Reply