Introduction to PCB Electrical Tests
Printed Circuit Boards (PCBs) are essential components in modern electronic devices. To ensure the reliability and functionality of PCBs, various electrical tests are performed at different stages of the manufacturing process. These tests help identify defects, verify the board’s performance, and ensure compliance with industry standards. In this article, we will explore the different types of electrical tests for PCBs, their importance, and the techniques used to conduct them.
Importance of PCB Electrical Tests
PCB electrical tests are crucial for several reasons:
- Ensuring functionality
- Identifying defects
- Improving reliability
- Meeting industry standards
- Saving time and cost
Types of PCB Electrical Tests
There are several types of electrical tests performed on PCBs, each designed to assess specific aspects of the board’s functionality and reliability. Let’s explore some of the most common PCB electrical tests:
1. Continuity Test
What is a Continuity Test?
A continuity test is a basic electrical test that checks for the presence of a continuous electrical path between two points on a PCB. This test ensures that the connections between components are intact and that there are no open circuits or broken traces.
How is a Continuity Test Performed?
Continuity tests are typically performed using a multimeter or a dedicated continuity tester. The test involves placing probes on the two points of interest and checking for a low resistance reading, indicating a continuous electrical path.
Importance of Continuity Tests
Continuity tests are essential for identifying:
- Open circuits
- Broken traces
- Solder joint issues
- Incorrect component placement
2. Short Circuit Test
What is a Short Circuit Test?
A short circuit test checks for unintended electrical connections between two or more points on a PCB that should not be connected. Short circuits can cause various issues, such as excessive current draw, component damage, and even fire hazards.
How is a Short Circuit Test Performed?
Short circuit tests are usually conducted using a multimeter or a dedicated short circuit tester. The test involves checking for a low resistance reading between points that should not be connected, indicating the presence of a short circuit.
Importance of Short Circuit Tests
Short circuit tests are crucial for identifying:
- Solder bridges
- Conductive debris
- Damaged insulation
- Incorrect component placement
3. Insulation Resistance Test
What is an Insulation Resistance Test?
An insulation resistance test measures the resistance between two conductors that are separated by an insulating material. This test ensures that the insulation between conductors is sufficient to prevent current leakage and maintain the integrity of the PCB.
How is an Insulation Resistance Test Performed?
Insulation resistance tests are performed using a high-voltage insulation tester, also known as a megohmmeter. The test involves applying a high voltage between the conductors and measuring the resistance of the insulating material.
Importance of Insulation Resistance Tests
Insulation resistance tests are essential for identifying:
- Insulation degradation
- Moisture ingress
- Contamination
- Manufacturing defects
4. Dielectric Withstand Test
What is a Dielectric Withstand Test?
A dielectric withstand test, also known as a high potential (hipot) test, checks the insulation’s ability to withstand a specified voltage without breakdown. This test ensures that the PCB can operate safely under the intended voltage conditions.
How is a Dielectric Withstand Test Performed?
Dielectric withstand tests are conducted using a hipot tester, which applies a high voltage between the conductors and the ground plane. The test measures the leakage current and checks for any insulation breakdown.
Importance of Dielectric Withstand Tests
Dielectric withstand tests are crucial for identifying:
- Insulation weaknesses
- Voltage breakdown
- Safety issues
- Compliance with industry standards
5. Functional Test
What is a Functional Test?
A functional test is a comprehensive test that verifies the overall functionality of the PCB. This test ensures that the board performs as intended and meets the specified requirements.
How is a Functional Test Performed?
Functional tests are typically performed using automated test equipment (ATE) or custom-built test fixtures. The test involves applying input signals to the PCB and measuring the output signals to verify proper operation.
Importance of Functional Tests
Functional tests are essential for:
- Verifying overall functionality
- Identifying performance issues
- Ensuring compliance with specifications
- Detecting design flaws
Techniques for PCB Electrical Tests
Various techniques are used to conduct PCB electrical tests efficiently and accurately. Some of the common techniques include:
1. Flying Probe Test
Flying probe testing is an automated test method that uses movable probes to contact test points on the PCB. This technique is useful for testing prototypes and low-volume production runs, as it does not require custom test fixtures.
2. In-Circuit Test (ICT)
In-circuit testing involves using a bed-of-nails test fixture to make contact with test points on the PCB. This technique allows for rapid testing of multiple boards and is suitable for high-volume production.
3. Boundary Scan Test
Boundary scan testing, also known as JTAG testing, is a method that uses dedicated test access ports (TAPs) on the PCB to test the interconnections between components. This technique is particularly useful for testing complex boards with high component density.
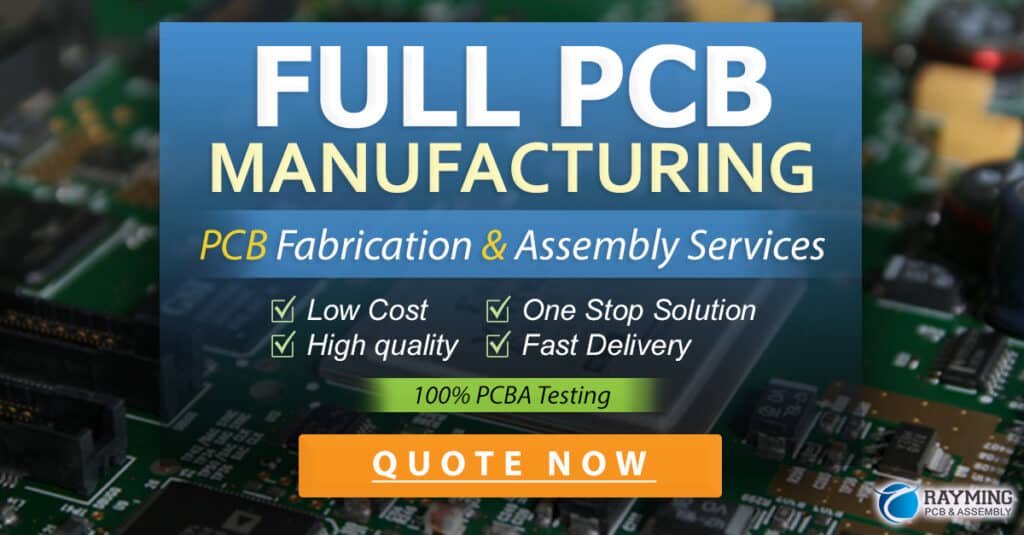
FAQ
1. What is the difference between a continuity test and a short circuit test?
A continuity test checks for the presence of a continuous electrical path between two points that should be connected, while a short circuit test checks for unintended connections between points that should not be connected.
2. Can PCB electrical tests be performed on assembled boards?
Yes, many PCB electrical tests, such as functional tests and in-circuit tests, are performed on fully assembled boards to verify the overall functionality and detect any issues that may have arisen during the assembly process.
3. How often should PCB electrical tests be performed?
The frequency of PCB electrical tests depends on various factors, such as the complexity of the board, the manufacturing process, and the end-use application. Typically, tests are performed at various stages of the manufacturing process, including prototyping, pre-production, and final production.
4. What are the benefits of automated PCB electrical testing?
Automated PCB electrical testing offers several benefits, including increased efficiency, improved accuracy, and reduced testing time. Automated tests can also provide detailed reports and data analysis, helping to identify trends and improve the overall quality of the PCB manufacturing process.
5. Are there any industry standards for PCB electrical testing?
Yes, there are several industry standards that provide guidelines for PCB electrical testing, such as IPC-9252A (Requirements for Electrical Testing of Unpopulated Printed Boards) and IPC-TM-650 (Test Methods Manual). These standards help ensure consistency and reliability in PCB electrical testing across the industry.
Conclusion
PCB electrical tests are essential for ensuring the functionality, reliability, and safety of printed circuit boards. By performing various tests, such as continuity tests, short circuit tests, insulation resistance tests, dielectric withstand tests, and functional tests, manufacturers can identify defects, verify performance, and ensure compliance with industry standards. The use of advanced testing techniques, such as flying probe testing, in-circuit testing, and boundary scan testing, has greatly improved the efficiency and accuracy of PCB electrical testing. As electronic devices continue to become more complex and sophisticated, the importance of comprehensive and rigorous PCB electrical testing will only continue to grow.
Test Type | Purpose | Technique |
---|---|---|
Continuity Test | Checks for continuous electrical path between two points | Multimeter or continuity tester |
Short Circuit Test | Checks for unintended electrical connections | Multimeter or short circuit tester |
Insulation Resistance Test | Measures resistance between conductors separated by insulation | High-voltage insulation tester (megohmmeter) |
Dielectric Withstand Test | Checks insulation’s ability to withstand specified voltage | Hipot tester |
Functional Test | Verifies overall functionality of the PCB | Automated test equipment (ATE) or custom-built test fixtures |
Leave a Reply