Introduction to BuildStandards in Manufacturing
In modern manufacturing, efficiency and consistency are crucial for success. One key aspect of achieving these goals is the implementation of standardized build processes, also known as BuildStandards. These standards ensure that every product is manufactured using the same methods, materials, and quality control measures, resulting in a more streamlined production process and higher-quality end products.
Multilayer Standard Builds take the concept of BuildStandards a step further by incorporating multiple layers of standardization. This approach involves breaking down the manufacturing process into smaller, more manageable components, each with its own set of standards and best practices. By doing so, manufacturers can achieve even greater levels of efficiency, consistency, and quality control.
Benefits of Implementing Multilayer Standard Builds
- Increased efficiency
- Improved product quality
- Reduced waste and errors
- Enhanced communication and collaboration
- Faster time-to-market
Key Components of Multilayer Standard Builds
To effectively implement Multilayer Standard Builds, manufacturers must focus on several key components:
1. Process Standardization
The first layer of standardization involves establishing clear, well-defined processes for each step of the manufacturing process. This includes:
- Raw material selection and sourcing
- Equipment setup and maintenance
- Production steps and sequences
- Quality control and testing procedures
By standardizing these processes, manufacturers can ensure that every product is made using the same methods, reducing the risk of errors and inconsistencies.
2. Material Standardization
The second layer of standardization focuses on the materials used in the manufacturing process. This involves:
- Selecting high-quality, consistent raw materials
- Establishing strict material specifications and tolerances
- Implementing material tracking and traceability systems
- Conducting regular material testing and quality control
By standardizing materials, manufacturers can reduce the risk of product defects and ensure that every product meets the same high standards of quality.
3. Equipment Standardization
The third layer of standardization involves the equipment used in the manufacturing process. This includes:
- Selecting reliable, high-performance equipment
- Establishing equipment maintenance and calibration schedules
- Implementing equipment monitoring and performance tracking systems
- Providing regular training for equipment operators
By standardizing equipment, manufacturers can minimize downtime, reduce the risk of equipment failure, and ensure consistent product quality.
4. Personnel Standardization
The fourth layer of standardization focuses on the personnel involved in the manufacturing process. This involves:
- Establishing clear roles and responsibilities for each team member
- Providing regular training and skill development opportunities
- Implementing performance monitoring and feedback systems
- Fostering a culture of continuous improvement and collaboration
By standardizing personnel, manufacturers can ensure that every team member has the skills and knowledge needed to perform their tasks effectively and efficiently.
Implementing Multilayer Standard Builds
To successfully implement Multilayer Standard Builds, manufacturers should follow these steps:
- Assess current processes and identify areas for improvement
- Develop clear, well-defined standards for each layer of the manufacturing process
- Communicate standards to all team members and provide necessary training
- Implement monitoring and performance tracking systems to ensure compliance
- Continuously review and update standards based on feedback and performance data
Best Practices for Successful Implementation
- Involve all stakeholders in the development and implementation of standards
- Prioritize safety and quality throughout the manufacturing process
- Foster a culture of continuous improvement and open communication
- Regularly review and update standards to ensure they remain relevant and effective
- Celebrate successes and recognize team members who contribute to the success of the program
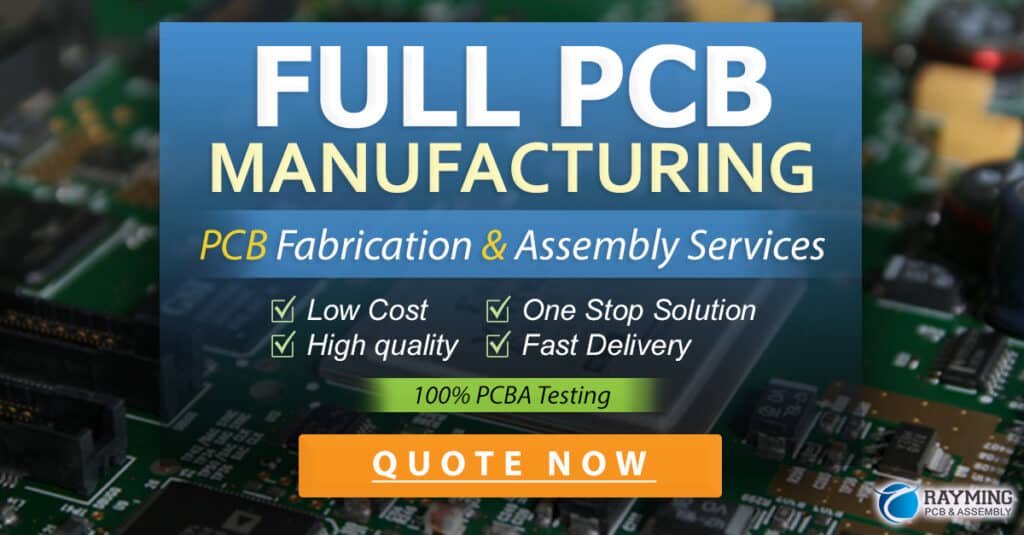
Case Studies: Successful Multilayer Standard Build Implementations
Company A: Automotive Parts Manufacturer
Company A, a leading automotive parts manufacturer, implemented Multilayer Standard Builds to improve efficiency and reduce defects in their production process. They focused on standardizing their raw material specifications, equipment maintenance procedures, and quality control measures.
Metric | Before Implementation | After Implementation |
---|---|---|
Production Efficiency | 75% | 92% |
Defect Rate | 5% | 1.5% |
Equipment Downtime | 10% | 3% |
On-Time Delivery | 85% | 98% |
As a result of their efforts, Company A achieved significant improvements in production efficiency, defect rates, equipment downtime, and on-time delivery.
Company B: Electronics Manufacturer
Company B, an electronics manufacturer, implemented Multilayer Standard Builds to streamline their production process and improve product quality. They focused on standardizing their assembly procedures, testing protocols, and personnel training programs.
Metric | Before Implementation | After Implementation |
---|---|---|
Production Cycle Time | 30 days | 22 days |
First Pass Yield | 85% | 95% |
Customer Returns | 3% | 0.8% |
Employee Satisfaction | 60% | 85% |
By implementing Multilayer Standard Builds, Company B was able to reduce their production cycle time, improve first pass yield, decrease customer returns, and increase employee satisfaction.
Frequently Asked Questions (FAQ)
- What are the main benefits of implementing Multilayer Standard Builds?
-
Increased efficiency, improved product quality, reduced waste and errors, enhanced communication and collaboration, and faster time-to-market.
-
How long does it typically take to implement Multilayer Standard Builds?
-
The implementation timeline can vary depending on the size and complexity of the manufacturing operation. However, most companies can expect to see significant improvements within 6-12 months of starting the implementation process.
-
What are the key components of Multilayer Standard Builds?
-
The four key components are process standardization, material standardization, equipment standardization, and personnel standardization.
-
How can manufacturers ensure successful implementation of Multilayer Standard Builds?
-
Manufacturers should involve all stakeholders in the development and implementation of standards, prioritize safety and quality, foster a culture of continuous improvement, regularly review and update standards, and celebrate successes.
-
Can Multilayer Standard Builds be applied to any manufacturing industry?
- Yes, Multilayer Standard Builds can be adapted to suit the specific needs and requirements of any manufacturing industry, from automotive and electronics to food and beverage production.
Conclusion
Multilayer Standard Builds offer manufacturers a powerful tool for optimizing their production processes, improving product quality, and reducing waste and errors. By focusing on standardization at every layer of the manufacturing process, from raw materials and equipment to personnel and processes, manufacturers can achieve significant improvements in efficiency, consistency, and overall performance.
While implementing Multilayer Standard Builds can be a complex and challenging process, the benefits are well worth the effort. By following best practices and involving all stakeholders in the development and implementation of standards, manufacturers can unlock the full potential of their operations and position themselves for long-term success in an increasingly competitive market.
Leave a Reply