What are PCB Through Holes?
PCB through holes are small, plated holes drilled through the layers of a printed circuit board. These holes are typically lined with a conductive material, such as copper, to create an electrical connection between the layers of the PCB. Through holes can be used for various purposes, such as:
- Mounting components: Through hole components, such as resistors, capacitors, and connectors, can be inserted into the holes and soldered in place.
- Connecting layers: In multi-layer PCBs, through holes are used to connect the different copper layers, allowing for more complex circuit designs and improved signal integrity.
- Providing mechanical support: Through holes can also provide mechanical support for the PCB and its components, especially in applications where the board may be subjected to vibration or physical stress.
Types of PCB Through Holes
There are several types of PCB through holes, each with its own characteristics and applications:
1. Plated Through Holes (PTHs)
Plated through holes are the most common type of through holes found in PCBs. These holes are drilled through the board and then plated with a conductive material, usually copper, to create an electrical connection between the layers. PTHs are typically used for mounting through hole components and connecting the layers of a multi-layer PCB.
2. Non-Plated Through Holes (NPTHs)
Non-plated through holes are drilled through the PCB but are not plated with a conductive material. These holes are often used for mounting purposes, such as attaching the PCB to an enclosure or providing a path for mechanical components like screws or standoffs. NPTHs do not provide electrical connectivity between layers.
3. Blind Vias
Blind vias are a type of through hole that connects an outer layer to an inner layer of a multi-layer PCB, but does not go through the entire thickness of the board. These vias are typically used to save space on the PCB and reduce the overall size of the board.
4. Buried Vias
Buried vias are similar to blind vias, but they connect two or more inner layers of a multi-layer PCB without extending to the outer layers. These vias are used to create more complex interconnections between the layers and are not visible from the surface of the board.
Manufacturing Process of PCB Through Holes
The manufacturing process of PCB through holes involves several steps:
-
Drilling: The first step is to drill the holes into the PCB using a specialized drilling machine. The size and location of the holes are determined by the PCB design.
-
Deburring: After drilling, the holes are deburred to remove any rough edges or debris that may have been created during the drilling process.
-
Plating: For plated through holes, the next step is to plate the holes with a conductive material, typically copper. This is done using an electroplating process, where the board is immersed in a plating solution and an electrical current is applied to deposit the copper onto the walls of the holes.
-
Filling (optional): In some cases, the plated through holes may be filled with a non-conductive material, such as epoxy, to improve the mechanical strength of the board or to create a smooth surface for subsequent processing steps.
-
Solder mask application: A solder mask is applied to the surface of the PCB, covering the areas that should not be exposed to solder during the assembly process. The solder mask is typically applied using a screen printing or photoimaging process.
-
Surface finish: Finally, a surface finish, such as HASL (Hot Air Solder Leveling), ENIG (Electroless Nickel Immersion Gold), or OSP (Organic Solderability Preservative), is applied to the exposed copper areas of the PCB, including the plated through holes, to protect the copper from oxidation and improve solderability.
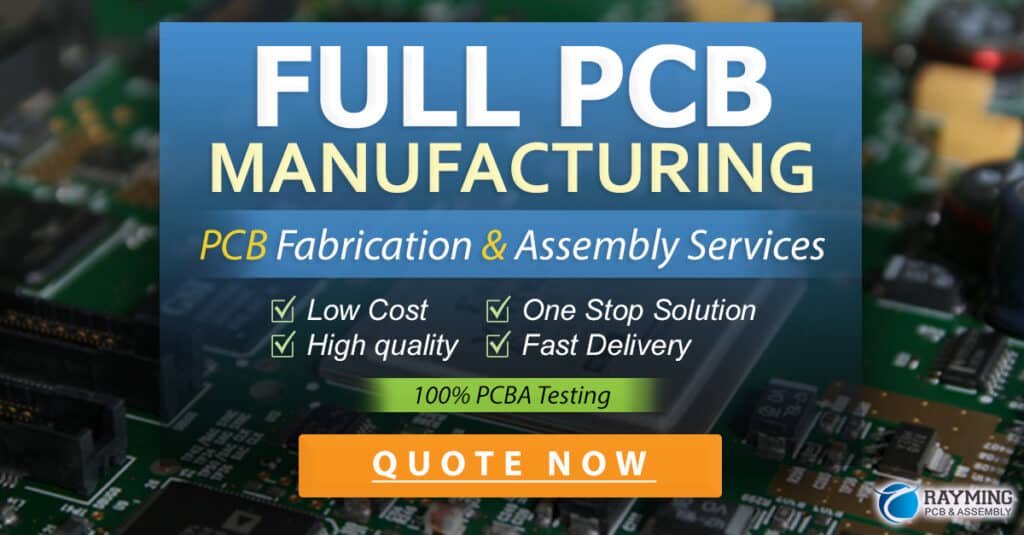
Design Considerations for PCB Through Holes
When designing a PCB with through holes, several factors must be considered to ensure the optimal performance and manufacturability of the board:
1. Hole Size
The size of the through holes is an essential consideration in PCB design. The hole diameter should be large enough to accommodate the component leads or wires that will be inserted into the hole, with some additional clearance to allow for easy insertion and soldering. However, the hole size should also be as small as possible to minimize the amount of space taken up on the board and to reduce the risk of signal integrity issues.
The standard hole sizes for through hole components are typically specified by the component manufacturer and should be followed to ensure compatibility. For example, a standard through hole resistor may have a lead diameter of 0.5mm, requiring a hole diameter of around 0.8mm to allow for proper insertion and soldering.
2. Pad Size and Shape
The pads surrounding the through holes play a crucial role in ensuring a good solder joint and providing mechanical stability for the component. The pad size and shape should be designed to provide sufficient area for the solder to flow and form a strong bond between the component lead and the pad.
The pad size is typically determined by the hole size and the component lead diameter, with some additional allowance for the solder fillet. A general rule of thumb is to make the pad diameter about 2-3 times the lead diameter, although this may vary depending on the specific component and the soldering process used.
The pad shape can also impact the strength and reliability of the solder joint. Common pad shapes include circular, oval, and rectangular. Circular pads are the most common and provide a good balance of solderability and mechanical stability. Oval and rectangular pads may be used in situations where space is limited, or where additional mechanical strength is required.
3. Hole-to-Hole Spacing
The spacing between through holes is another critical design consideration, particularly in high-density PCB designs. The hole-to-hole spacing should be sufficient to prevent any signal integrity issues, such as crosstalk between adjacent holes, while also allowing for proper soldering and component placement.
The minimum hole-to-hole spacing is typically determined by the PCB manufacturer’s capabilities and the design rules for the specific PCB fabrication process being used. In general, a minimum spacing of 1-2 times the hole diameter is recommended, although this may vary depending on the specific design requirements and the PCB fabrication process.
4. Layer Stack-Up
In multi-layer PCBs, the arrangement of the layers and the placement of the through holes can have a significant impact on the signal integrity and the overall performance of the board. The layer stack-up should be designed to minimize the impact of the through holes on the signal paths and to ensure that the holes are properly connected to the appropriate layers.
One common technique is to use blind or buried vias to connect the inner layers of the board, reducing the number of through holes that go through the entire thickness of the board. This can help to minimize the impact of the holes on the signal paths and reduce the overall size of the board.
Another consideration is the placement of the through holes relative to the signal layers. In general, it is best to avoid placing through holes directly above or below critical signal traces, as this can lead to signal integrity issues. Instead, the holes should be placed in areas of the board where they will have minimal impact on the signal paths.
5. Thermal Management
In some cases, through holes may be used for thermal management purposes, such as providing a path for heat to be dissipated from the components on the board. In these situations, the size and placement of the holes should be carefully considered to ensure that they provide adequate thermal conductivity without compromising the electrical performance of the board.
One common technique is to use thermal vias, which are plated through holes that are specifically designed to provide a low-resistance thermal path between the components and the heat sink or other cooling solution. Thermal vias are typically larger in diameter than standard signal vias and may be filled with a thermally conductive material, such as copper or a thermal epoxy, to improve their thermal performance.
Importance of PCB Through Holes
PCB through holes play a vital role in the overall functionality and reliability of a printed circuit board. Some of the key benefits of using through holes in PCB design include:
-
Electrical Connectivity: Through holes provide a means to electrically connect different layers of a multi-layer PCB, allowing for more complex circuit designs and improved signal integrity.
-
Mechanical Stability: Through holes can provide mechanical support for the PCB and its components, helping to reduce the risk of damage from vibration or physical stress.
-
Component Mounting: Through holes are used to mount through hole components, such as connectors, switches, and some types of sensors, providing a secure and reliable means of attaching these components to the board.
-
Thermal Management: In some cases, through holes can be used to provide a thermal path for heat dissipation, helping to keep the components on the board within their operating temperature range.
-
Manufacturing Efficiency: Through holes are a well-established and widely used technology in PCB manufacturing, with a range of standard processes and equipment available for drilling, plating, and soldering through holes. This can help to reduce manufacturing costs and improve production efficiency compared to other methods of interconnection, such as surface mount technology (SMT).
Frequently Asked Questions (FAQ)
1. What is the difference between a plated through hole and a non-plated through hole?
A plated through hole (PTH) is a hole that is drilled through the PCB and then plated with a conductive material, typically copper, to create an electrical connection between the layers of the board. A non-plated through hole (NPTH) is a hole that is drilled through the PCB but is not plated with a conductive material. NPTHs are often used for mounting purposes or to provide a path for mechanical components, but do not provide electrical connectivity.
2. What is the purpose of blind and buried vias in PCB design?
Blind vias and buried vias are used in multi-layer PCBs to create interconnections between the inner layers of the board without going through the entire thickness of the board. Blind vias connect an outer layer to an inner layer, while buried vias connect two or more inner layers. These types of vias are used to save space on the board, reduce the overall size of the board, and create more complex interconnections between the layers.
3. How does the hole size affect the design of a PCB?
The hole size is an important consideration in PCB design, as it determines the size of the components that can be used and the overall layout of the board. The hole diameter should be large enough to accommodate the component leads or wires, with some additional clearance for easy insertion and soldering. However, the hole size should also be as small as possible to minimize the amount of space taken up on the board and to reduce the risk of signal integrity issues.
4. What is the importance of pad size and shape in PCB through hole design?
The pad size and shape play a crucial role in ensuring a good solder joint and providing mechanical stability for the component. The pad size should be large enough to provide sufficient area for the solder to flow and form a strong bond between the component lead and the pad, typically 2-3 times the lead diameter. The pad shape, such as circular, oval, or rectangular, can also impact the strength and reliability of the solder joint and may be chosen based on space constraints or specific mechanical requirements.
5. How can through holes be used for thermal management in a PCB?
Through holes can be used for thermal management by providing a path for heat to be dissipated from the components on the board. Thermal vias, which are plated through holes designed to provide a low-resistance thermal path, can be used to connect components to a heat sink or other cooling solution. The size and placement of thermal vias should be carefully considered to ensure adequate thermal conductivity without compromising the electrical performance of the board. In some cases, thermal vias may be filled with a thermally conductive material, such as copper or thermal epoxy, to improve their thermal performance.
Conclusion
PCB through holes are a critical component of printed circuit board design and manufacturing, providing electrical connectivity, mechanical stability, and a means for mounting components. Understanding the different types of through holes, their manufacturing processes, and the key design considerations is essential for creating reliable and high-performance PCBs.
As PCB technology continues to evolve, the role of through holes may change, with new materials, processes, and design techniques being developed to meet the ever-increasing demands for smaller, faster, and more complex electronic devices. However, the fundamental principles of through hole design and manufacturing will remain relevant for the foreseeable future, making a deep understanding of this technology essential for anyone involved in the development or production of printed circuit boards.
By carefully considering the various factors involved in through hole design, such as hole size, pad size and shape, hole-to-hole spacing, layer stack-up, and thermal management, PCB designers and manufacturers can create boards that are optimized for performance, reliability, and manufacturability, while also meeting the specific requirements of the end application.
Leave a Reply