Introduction to PCB Mechanical Layers
Printed Circuit Boards (PCBs) are essential components in modern electronic devices. They provide a platform for mounting and interconnecting various electronic components, enabling the functioning of complex circuits. While the electrical aspects of PCBs often receive the most attention, the mechanical layers play a crucial role in the overall design and manufacturability of the board.
PCB mechanical layers, also known as non-electrical layers or documentation layers, are additional layers in the PCB design that do not contribute to the electrical functionality of the board. Instead, they provide important information for manufacturing, assembly, and documentation purposes. These layers help ensure the proper fabrication, assembly, and testing of the PCB, ultimately contributing to the reliability and quality of the final product.
In this article, we will explore the various types of PCB mechanical layers, their purposes, and their significance in the PCB design process.
Types of PCB Mechanical Layers
There are several types of mechanical layers commonly used in PCB design. Each layer serves a specific purpose and provides essential information for the manufacturing and assembly process. Let’s take a closer look at some of the most common PCB mechanical layers:
1. Silkscreen Layer
The silkscreen layer, also known as the legend or overlay layer, is a non-conductive layer that contains text, logos, and other markings printed on the surface of the PCB. This layer provides visual information for component placement, orientation, and identification. It helps the assembly team correctly position and orient components on the board.
The silkscreen layer typically includes the following information:
– Component designators (e.g., R1, C2, U3)
– Component outlines and polarity indicators
– Board identification, revision numbers, and logos
– Test points and fiducial markers
– Warning symbols and handling instructions
2. Solder Mask Layer
The solder mask layer, also called the solder resist layer, is a thin protective coating applied to the copper traces and pads on the PCB. Its primary purpose is to prevent solder bridging and short circuits during the soldering process. The solder mask layer exposes only the areas where solder is intended to be applied, such as component pads and vias.
The solder mask layer offers several benefits:
– Protects the copper traces from oxidation and environmental factors
– Provides electrical insulation between adjacent traces and pads
– Improves the aesthetics of the PCB by providing a uniform color (usually green)
– Enhances the durability and longevity of the PCB
3. Solder Paste Layer
The solder paste layer, also referred to as the stencil layer, is used in surface mount technology (SMT) assembly. It defines the areas where solder paste should be applied on the PCB prior to component placement. The solder paste layer is typically generated based on the pad sizes and shapes defined in the copper layer.
The solder paste layer serves the following purposes:
– Guides the solder paste application process
– Ensures the correct amount of solder paste is deposited on each pad
– Helps achieve reliable solder joints during the reflow soldering process
4. Assembly Layer
The assembly layer, also known as the assembly drawing layer or mechanical layer, provides information for the assembly process. It includes details such as component placement, orientation, and assembly instructions. The assembly layer is used by the assembly team to accurately place components on the PCB.
The assembly layer typically includes the following information:
– Component outlines and designators
– Assembly notes and instructions
– Dimensional information for component placement
– Fiducial markers for machine vision alignment
5. Drill Layer
The drill layer specifies the locations, sizes, and types of holes to be drilled in the PCB. These holes are used for component leads, vias, and mounting purposes. The drill layer provides essential information for the PCB fabrication process, ensuring that the holes are drilled accurately and consistently.
The drill layer includes the following information:
– Hole sizes and locations
– Plated and non-plated holes
– Vias and through-holes
– Mounting holes and slots
6. Fabrication Layer
The fabrication layer, also called the fab layer or manufacturing layer, contains information specific to the PCB fabrication process. It includes details such as board outline, panel information, and tooling holes. The fabrication layer helps the PCB manufacturer produce the board according to the desired specifications.
The fabrication layer typically includes the following information:
– Board outline and dimensions
– Panel information for multi-board fabrication
– Tooling holes and fiducial markers
– Coupon and test point locations
– Layer stackup and material specifications
Importance of PCB Mechanical Layers
PCB mechanical layers play a vital role in the overall design and manufacturing process. They ensure that the PCB is fabricated, assembled, and tested accurately and efficiently. Let’s explore the significance of PCB mechanical layers in more detail:
1. Manufacturing Accuracy
The mechanical layers provide critical information for the PCB manufacturing process. They guide the fabrication and assembly teams, ensuring that the board is produced according to the specified dimensions, hole sizes, and component placements. Accurate mechanical layers help prevent manufacturing errors and improve the overall quality of the PCB.
2. Assembly Efficiency
The silkscreen and assembly layers streamline the PCB Assembly process. They provide clear instructions for component placement and orientation, reducing the chances of human error during manual assembly. These layers also facilitate automated assembly processes, such as pick-and-place machines, by providing machine-readable information.
3. Design Communication
PCB mechanical layers serve as a communication tool between the PCB designer, manufacturer, and assembler. They convey important design intent and requirements, ensuring that all stakeholders have a clear understanding of the board’s specifications. Clear and comprehensive mechanical layers help avoid misinterpretation and potential issues during the manufacturing and assembly stages.
4. Testing and Debugging
The mechanical layers, particularly the silkscreen layer, aid in PCB testing and debugging. Test points, fiducial markers, and component designators printed on the silkscreen layer enable efficient probing and troubleshooting of the board. This information is valuable for both manual and automated testing processes.
5. Documentation and Traceability
PCB mechanical layers contribute to the overall documentation and traceability of the board. They provide a visual representation of the PCB layout, component placement, and assembly instructions. This documentation is essential for future reference, maintenance, and troubleshooting purposes. It also helps in tracking revisions and ensuring the correct version of the board is used in production.
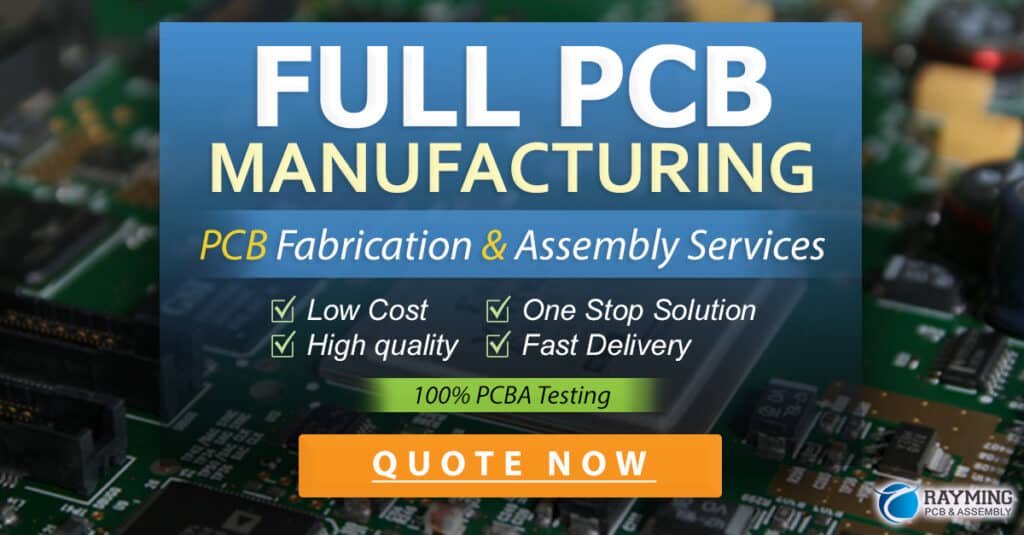
Best Practices for PCB Mechanical Layers
To ensure the effectiveness and accuracy of PCB mechanical layers, consider the following best practices:
- Adhere to industry standards and guidelines for layer naming and color conventions.
- Provide clear and concise text on the silkscreen layer, using appropriate font sizes and styles.
- Ensure adequate clearance between silkscreen elements and component pads to avoid interference.
- Use consistent and accurate dimensions for component outlines and placement on the assembly layer.
- Specify the correct hole sizes and types on the drill layer, considering the requirements for component leads and vias.
- Include relevant manufacturing information, such as board outline, panel data, and tooling holes, on the fabrication layer.
- Communicate any special requirements or instructions through notes and annotations on the appropriate layers.
- Collaborate closely with the PCB manufacturer and assembler to ensure the mechanical layers meet their specific needs and capabilities.
FAQ
1. What is the difference between electrical and mechanical layers in PCB design?
Electrical layers in PCB design, such as copper layers, are responsible for the electrical connectivity and functionality of the board. They define the conductive paths, pads, and vias that allow signals and power to flow between components. On the other hand, mechanical layers, such as silkscreen and assembly layers, provide non-electrical information for manufacturing, assembly, and documentation purposes. They do not contribute to the electrical performance of the PCB but are essential for its physical realization.
2. Can mechanical layers affect the electrical performance of a PCB?
In general, mechanical layers do not directly impact the electrical performance of a PCB. However, improper design or placement of mechanical elements can indirectly affect the electrical characteristics. For example, if the silkscreen layer is placed too close to component pads or traces, it may cause unintended solder bridging or short circuits during the assembly process. Similarly, incorrect hole sizes or locations specified in the drill layer can lead to manufacturing defects that compromise the electrical integrity of the board.
3. What is the purpose of the solder mask layer?
The solder mask layer serves as a protective coating on the PCB, covering the copper traces and pads except for the areas where solder is intended to be applied. Its primary purpose is to prevent solder bridging and short circuits during the soldering process. The solder mask layer also provides electrical insulation, protects the copper from oxidation, and enhances the aesthetics of the PCB.
4. How do I ensure the accuracy of mechanical layers in my PCB design?
To ensure the accuracy of mechanical layers, follow these guidelines:
– Use reliable PCB design software that supports the creation and management of mechanical layers.
– Adhere to industry standards and guidelines for layer specifications and conventions.
– Collaborate closely with the PCB manufacturer and assembler to understand their specific requirements and capabilities.
– Conduct thorough design reviews and checks to verify the accuracy and completeness of the mechanical layers.
– Perform prototype testing and validation to identify any issues related to the mechanical layers before mass production.
5. Can I customize the color and appearance of the silkscreen layer?
Yes, the color and appearance of the silkscreen layer can be customized to some extent. While white is the most common color for silkscreen, other colors such as black, yellow, or red can be used depending on the PCB manufacturer’s capabilities and the designer’s preferences. However, it’s important to ensure that the chosen color provides sufficient contrast against the solder mask layer for clear visibility. Additionally, some PCB manufacturers may offer custom silkscreen options, such as logos or artwork, subject to their specific guidelines and limitations.
Conclusion
PCB mechanical layers are an integral part of the PCB design process, playing a crucial role in the manufacturing, assembly, and documentation of the board. These non-electrical layers, including silkscreen, solder mask, solder paste, assembly, drill, and fabrication layers, provide essential information that ensures the accurate and efficient realization of the PCB.
By understanding the types, purposes, and best practices associated with PCB mechanical layers, designers can create comprehensive and reliable PCB designs that meet the requirements of the manufacturing and assembly processes. Effective communication and collaboration with PCB manufacturers and assemblers are key to ensuring the successful implementation of mechanical layers.
As PCB technology continues to advance, the importance of mechanical layers remains paramount. By giving due attention to these critical aspects of PCB design, designers can contribute to the overall quality, reliability, and manufacturability of electronic products.
Layer Type | Purpose |
---|---|
Silkscreen | Provides visual information for component placement, orientation, and identification |
Solder Mask | Protects copper traces, prevents solder bridging, and provides insulation |
Solder Paste | Defines areas for solder paste application in SMT assembly |
Assembly | Provides component placement and assembly instructions |
Drill | Specifies hole locations, sizes, and types for component leads and vias |
Fabrication | Contains board outline, panel information, and fabrication-specific details |
Remember, the key to successful PCB design lies in the careful consideration and implementation of both electrical and mechanical aspects. By giving mechanical layers the attention they deserve, designers can ensure the optimal performance, manufacturability, and reliability of their PCBs.
Leave a Reply