Introduction to PCBs and their Functionshttps://cn.bing.com/
Printed Circuit Boards (PCBs) are the backbone of modern electronics. They are found in almost every electronic device we use today, from smartphones and laptops to medical equipment and aerospace systems. PCBs serve as the foundation for electronic circuits, providing a platform for components to be mounted and interconnected. In this article, we will dive deep into the functions of PCBs and explore their critical role in the world of electronics.
What is a PCB?
A PCB is a flat board made of insulating material, typically fiberglass or composite epoxy, with conductive pathways etched or printed onto its surface. These pathways, known as traces, connect various electronic components such as resistors, capacitors, integrated circuits (ICs), and connectors. PCBs can be single-sided (with components on one side), double-sided (with components on both sides), or multi-layered (with traces and components on multiple layers).
The Primary Functions of PCBs
PCBs serve several essential functions in electronic devices:
- Mechanical Support: PCBs provide a stable platform for mounting and securing electronic components. The board’s rigid structure ensures that components remain in place and protected from physical damage.
- Electrical Connectivity: The conductive traces on the PCB allow for the flow of electrical signals between components. These traces are designed to minimize signal interference and ensure optimal performance.
- Heat Dissipation: PCBs help dissipate heat generated by electronic components. The board’s material properties and layout design facilitate heat transfer, preventing components from overheating and failing.
- Space Optimization: PCBs enable the compact and efficient arrangement of electronic components, minimizing the overall size of the device. This is particularly important in modern electronics, where miniaturization is a key design goal.
The Role of PCBs in Different Industries
PCBs play a crucial role in various industries, each with its specific requirements and challenges.
Consumer Electronics
In the consumer electronics industry, PCBs are used in a wide range of products, including:
- Smartphones
- Laptops and tablets
- Televisions and displays
- Gaming consoles
- Wearable devices
PCBs in consumer electronics must be highly compact, lightweight, and energy-efficient. They often incorporate advanced features such as high-speed data transfer, wireless connectivity, and sensors.
Automotive Electronics
PCBs are extensively used in automotive electronics, powering various systems such as:
- Engine control units (ECUs)
- Infotainment systems
- Advanced driver assistance systems (ADAS)
- Body control modules
- Lighting and climate control systems
Automotive PCBs must be able to withstand harsh environmental conditions, including extreme temperatures, vibrations, and moisture. They also need to meet stringent safety and reliability standards.
Industrial Electronics
Industrial electronics rely on PCBs for a wide range of applications, including:
- Process control systems
- Automation and robotics
- Power electronics
- Instrumentation and measurement
- Renewable energy systems
PCBs in industrial settings must be rugged, reliable, and able to operate in demanding environments. They often require special features such as high-power handling, isolation, and protection against electromagnetic interference (EMI).
Medical Electronics
Medical electronics use PCBs in various devices and equipment, such as:
- Patient monitoring systems
- Diagnostic imaging equipment
- Implantable devices
- Surgical instruments
- Laboratory equipment
PCBs in medical applications must meet strict regulatory requirements for safety, reliability, and biocompatibility. They often incorporate specialized features such as high-precision sensing, low-noise signal processing, and wireless data transmission.
Aerospace and Defense Electronics
PCBs are critical components in aerospace and defense electronics, used in applications such as:
- Avionics systems
- Satellite communications
- Radar and sonar systems
- Missile guidance systems
- Unmanned aerial vehicles (UAVs)
Aerospace and defense PCBs must be able to withstand extreme environmental conditions, including high altitudes, radiation, and shock. They also need to meet rigorous standards for reliability, security, and electromagnetic compatibility (EMC).
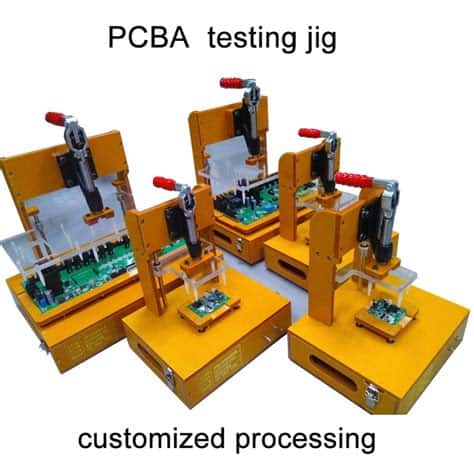
PCB Design and Manufacturing
The design and manufacturing of PCBs involve several key steps:
- Schematic Design: The electronic circuit is first designed using schematic capture software, which defines the components and their interconnections.
- PCB Layout: The schematic is then translated into a physical layout using PCB design software. This involves placing components and routing traces while adhering to design rules and constraints.
- Fabrication: The PCB layout is used to create a set of manufacturing files, which are sent to a PCB fabrication facility. The fabrication process involves applying copper layers, etching traces, drilling holes, and applying solder mask and silkscreen.
- Assembly: Once the PCB is fabricated, electronic components are mounted onto the board using various techniques such as through-hole or surface-mount assembly. The board is then soldered, either manually or using automated equipment.
- Testing and Inspection: The assembled PCB undergoes thorough testing and inspection to ensure proper functionality, reliability, and compliance with specifications. This may include automated optical inspection (AOI), in-circuit testing (ICT), and functional testing.
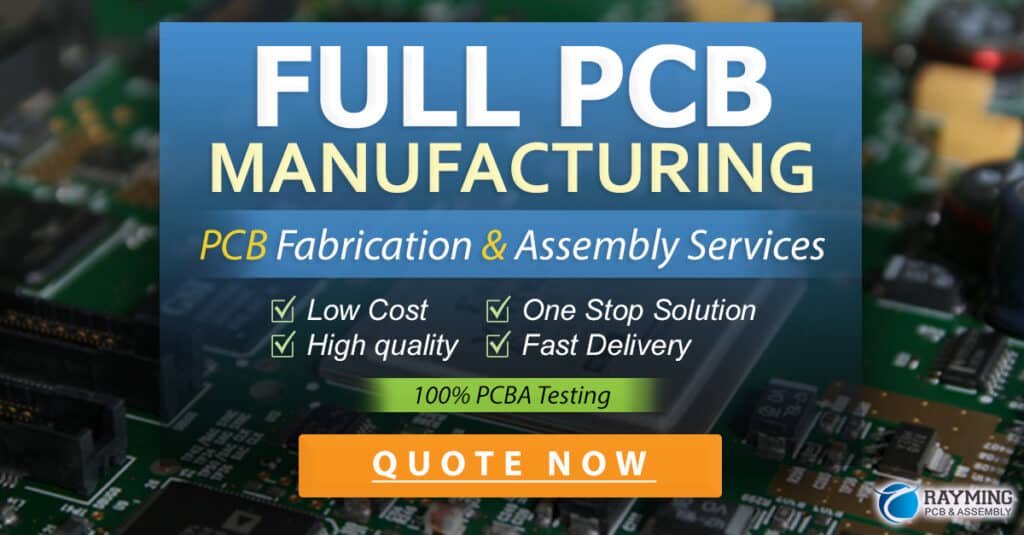
Advanced PCB Technologies
As electronics continue to evolve, so do PCB technologies. Some of the advanced PCB technologies include:
High-Density Interconnect (HDI) PCBs
HDI PCBs feature fine-pitch traces and micro-vias, allowing for higher component density and improved signal integrity. They are commonly used in smartphones, wearables, and other compact devices.
Flexible and Rigid-Flex PCBs
Flexible PCBs use thin, flexible substrates that can bend and fold, enabling unique form factors and improved reliability in applications such as wearables and automotive electronics. Rigid-flex PCBs combine rigid and flexible sections, providing the benefits of both technologies.
Embedded Components
Embedded component PCBs have components, such as resistors and capacitors, embedded within the layers of the board. This technology offers improved signal integrity, reduced board size, and enhanced thermal management.
3D-Printed Electronics
3D printing technology is being explored for the fabrication of PCBs, allowing for the creation of complex, three-dimensional structures with embedded electronics. This technology has the potential to revolutionize the design and manufacturing of electronic devices.
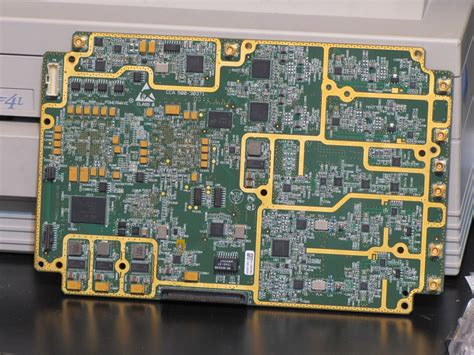
FAQs
- What materials are PCBs made of?
PCBs are typically made of a composite material called FR-4, which consists of fiberglass fabric impregnated with epoxy resin. The conductive traces are usually made of copper. - What is the difference between through-hole and surface-mount PCBs?
Through-hole PCBs have components with leads that are inserted into drilled holes and soldered on the opposite side of the board. Surface-mount PCBs have components that are mounted directly onto the surface of the board, allowing for smaller board sizes and higher component density. - How do PCBs dissipate heat?
PCBs dissipate heat through various means, such as using thermal vias (conductive paths that transfer heat to other layers), copper planes (large areas of copper that spread heat), and heat sinks (metal structures that absorb and dissipate heat). - What is the role of solder mask on a PCB?
Solder mask is a protective coating applied to the PCB that prevents accidental short circuits and protects the copper traces from oxidation and environmental damage. It also provides electrical insulation and improves the board’s appearance. - How are PCBs tested for reliability?
PCBs undergo various tests to ensure reliability, including environmental stress tests (thermal cycling, humidity, and vibration), electrical tests (continuity, insulation resistance, and dielectric withstanding voltage), and accelerated life tests (burn-in and highly accelerated stress testing).
Conclusion
PCBs are the unsung heroes of the electronic world, enabling the creation of ever-more sophisticated and compact devices. Their primary functions of providing mechanical support, electrical connectivity, heat dissipation, and space optimization are critical to the performance and reliability of electronic systems across various industries.
As technology continues to advance, PCBs will play an increasingly important role in shaping the future of electronics. From consumer gadgets to life-saving medical equipment, from autonomous vehicles to space exploration, PCBs will be at the heart of innovation, powering the devices that enhance our lives and push the boundaries of what is possible.
Industry | PCB Requirements |
---|---|
Consumer Electronics | Compact, lightweight, energy-efficient, high-speed data transfer, wireless connectivity, sensors |
Automotive Electronics | Withstand harsh environments, meet safety and reliability standards |
Industrial Electronics | Rugged, reliable, high-power handling, isolation, EMI protection |
Medical Electronics | Meet regulatory requirements for safety, reliability, biocompatibility, high-precision sensing, low-noise signal processing, wireless data transmission |
Aerospace and Defense Electronics | Withstand extreme environments, meet standards for reliability, security, EMC |
Leave a Reply