Introduction
In today’s complex manufacturing landscape, managing supplier data for various components is a critical aspect of ensuring smooth operations and maintaining a competitive edge. Designing easy processes to create and link supplier data to any component can streamline supply chain management, improve transparency, and facilitate better decision-making. This article will explore the key elements of designing such processes and provide practical insights for implementation.
Understanding the Importance of Supplier Data Management
The Role of Supplier Data in Manufacturing
Supplier data plays a crucial role in the manufacturing industry, as it directly impacts the quality, cost, and delivery of components used in the production process. Accurate and up-to-date supplier data enables manufacturers to:
- Identify reliable suppliers
- Negotiate favorable terms and prices
- Ensure timely delivery of components
- Maintain quality standards
- Mitigate supply chain risks
The Challenges of Managing Supplier Data
Despite its importance, managing supplier data can be a challenging task due to various factors, such as:
- Fragmented data sources
- Inconsistent data formats
- Lack of standardization
- Manual data entry errors
- Insufficient collaboration between departments
These challenges can lead to inefficiencies, delays, and increased costs in the manufacturing process.
Key Elements of Designing Easy Processes for Supplier Data Management
1. Data Standardization
Establishing a standardized format for supplier data is the foundation of creating easy processes. This involves:
- Defining a consistent set of data fields (e.g., supplier name, contact information, product specifications)
- Determining the required level of detail for each field
- Establishing a naming convention for suppliers and components
- Ensuring compatibility with existing systems and databases
By standardizing supplier data, manufacturers can ensure that information is captured consistently across the organization, making it easier to analyze and utilize.
2. Centralized Data Repository
Creating a centralized repository for supplier data is essential for easy access and management. This can be achieved through:
- Implementing a dedicated supplier relationship management (SRM) system
- Integrating supplier data with existing enterprise resource planning (ERP) or product lifecycle management (PLM) systems
- Establishing clear data governance policies and access controls
- Ensuring data security and compliance with relevant regulations
A centralized data repository eliminates data silos, reduces duplication, and enables real-time visibility into supplier information.
3. Automated Data Capture and Validation
Automating the process of capturing and validating supplier data can significantly reduce manual errors and improve efficiency. This can be accomplished through:
- Implementing electronic data interchange (EDI) or web-based portals for suppliers to submit information
- Utilizing optical character recognition (OCR) technology to extract data from scanned documents
- Applying data validation rules and checks to ensure accuracy and completeness
- Integrating with third-party data providers for enrichment and verification
Automated data capture and validation minimize the need for manual intervention, saving time and resources while improving data quality.
4. Supplier Collaboration and Communication
Fostering collaboration and communication with suppliers is crucial for maintaining accurate and up-to-date supplier data. This can be facilitated through:
- Establishing regular communication channels (e.g., email, portal, meetings)
- Sharing performance metrics and feedback with suppliers
- Collaborating on continuous improvement initiatives
- Providing training and support for suppliers to ensure data accuracy
By engaging suppliers as partners in the data management process, manufacturers can build stronger relationships, improve transparency, and ensure a more reliable supply chain.
5. Data Governance and Maintenance
Implementing robust data governance and maintenance practices is essential for ensuring the long-term integrity of supplier data. This involves:
- Assigning clear roles and responsibilities for data management
- Establishing data quality metrics and monitoring processes
- Conducting regular data audits and cleansing exercises
- Implementing change management procedures for updating supplier data
- Providing training and support for internal users to ensure consistent data usage
Effective data governance and maintenance ensure that supplier data remains accurate, up-to-date, and aligned with business objectives.
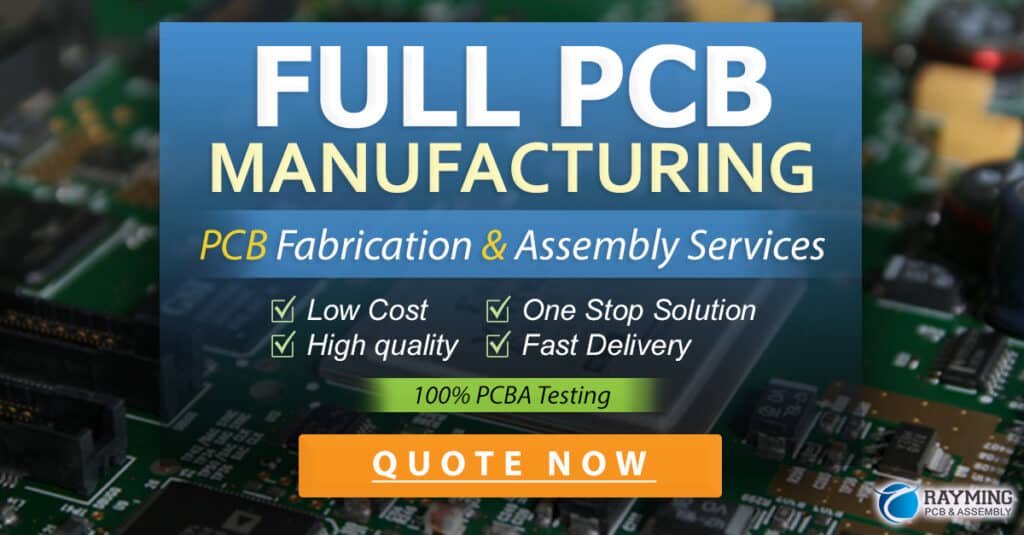
Linking Supplier Data to Components
The Benefits of Linking Supplier Data to Components
Linking supplier data to specific components offers several key benefits, including:
- Improved traceability and visibility into the supply chain
- Enhanced quality control and risk management
- Faster identification of potential supply disruptions
- Increased efficiency in sourcing and procurement processes
- Better informed decision-making for component selection and supplier evaluation
By establishing a clear link between suppliers and the components they provide, manufacturers can gain a more comprehensive understanding of their supply chain and make data-driven decisions.
Techniques for Linking Supplier Data to Components
There are several techniques for linking supplier data to components, depending on the complexity of the manufacturing process and the level of detail required. These include:
-
Direct Linking: Assigning a unique identifier to each component and linking it directly to the corresponding supplier in the centralized data repository.
-
Bill of Materials (BOM) Integration: Incorporating supplier data into the BOM structure, allowing for a hierarchical view of components and their associated suppliers.
-
Product Lifecycle Management (PLM) Integration: Integrating supplier data with PLM systems to track supplier involvement throughout the product development and manufacturing process.
-
Supplier Part Number Mapping: Establishing a mapping between supplier part numbers and internal component identifiers to enable easy cross-referencing and data integration.
The choice of technique will depend on the specific requirements and existing systems within the organization, but the goal is to establish a clear and maintainable link between suppliers and components.
Implementing Easy Processes for Supplier Data Management
Step 1: Assess Current State and Define Objectives
Before designing new processes, it is essential to assess the current state of supplier data management within the organization. This involves:
- Identifying existing data sources and systems
- Evaluating data quality and completeness
- Analyzing current processes and pain points
- Defining clear objectives and success metrics for the new processes
This assessment will provide a baseline for improvement and help prioritize areas of focus.
Step 2: Engage Stakeholders and Secure Buy-In
Engaging key stakeholders from across the organization is crucial for the success of any process redesign. This includes:
- Identifying relevant departments and individuals (e.g., procurement, engineering, quality, IT)
- Communicating the benefits and objectives of the new processes
- Seeking input and feedback on process design and implementation
- Securing executive sponsorship and resources for the initiative
By involving stakeholders early in the process, manufacturers can ensure alignment and support for the new processes.
Step 3: Design and Document Processes
Based on the assessment and stakeholder input, the next step is to design and document the new processes for supplier data management. This involves:
- Mapping out the end-to-end process flow
- Defining roles and responsibilities for each step
- Establishing data standards and governance policies
- Documenting procedures and guidelines for data capture, validation, and maintenance
- Identifying technology requirements and integration points
Clear and comprehensive process documentation is essential for ensuring consistency and facilitating training and adoption.
Step 4: Pilot and Refine Processes
Before rolling out the new processes organization-wide, it is recommended to conduct a pilot with a select group of suppliers and components. This allows for:
- Testing the processes in a controlled environment
- Identifying any gaps or issues in the process design
- Gathering feedback from users and suppliers
- Refining the processes based on lessons learned
The pilot phase provides an opportunity to fine-tune the processes and ensure they are effective and efficient before full-scale implementation.
Step 5: Train and Roll Out Processes
Once the processes have been refined based on the pilot, the next step is to train relevant personnel and roll out the processes across the organization. This involves:
- Developing training materials and guides
- Conducting training sessions for internal users and suppliers
- Communicating the go-live date and expectations
- Providing ongoing support and resources for users
- Monitoring adoption and performance metrics
Effective training and communication are critical for ensuring a smooth transition to the new processes and realizing the benefits of improved supplier data management.
FAQs
-
How long does it typically take to implement easy processes for supplier data management?
The timeline for implementation can vary depending on the size and complexity of the organization, but a typical project may take 3-6 months from assessment to roll-out. However, the specific duration will depend on factors such as the availability of resources, the scope of the project, and the level of customization required. -
What are the key challenges in linking supplier data to components?
Some of the key challenges include maintaining data accuracy and consistency across multiple systems, managing updates and changes to supplier information, and ensuring the integrity of the linking mechanism. Additionally, there may be challenges in integrating data from legacy systems or external partners. -
How can I ensure supplier adoption of the new processes?
Engaging suppliers early in the process, communicating the benefits and expectations clearly, and providing training and support are key to ensuring supplier adoption. It may also be helpful to incentivize suppliers for compliance and data quality, such as through performance-based contracts or recognition programs. -
What are the best practices for maintaining supplier data over time?
Best practices for maintaining supplier data include establishing clear data governance policies, conducting regular data audits and cleansing exercises, implementing automated data validation checks, and providing ongoing training and support for users. It is also important to have a clear process for updating and maintaining supplier information as changes occur. -
How can I measure the success of my supplier data management processes?
Success can be measured through a variety of metrics, such as data accuracy and completeness, supplier onboarding cycle times, procurement efficiency, and supply chain visibility. It is important to establish baseline metrics and track progress over time to demonstrate the value of the new processes. Additionally, gathering feedback from internal users and suppliers can provide valuable insights into the effectiveness of the processes.
Conclusion
Designing easy processes for creating and linking supplier data to components is essential for streamlining supply chain management and improving overall manufacturing performance. By focusing on data standardization, centralized data management, automation, collaboration, and governance, manufacturers can establish a solid foundation for supplier data management.
Implementing these processes requires careful planning, stakeholder engagement, and a commitment to continuous improvement. By following the steps outlined in this article and leveraging the techniques for linking supplier data to components, manufacturers can realize significant benefits in terms of increased efficiency, improved quality, and better-informed decision-making.
As the manufacturing landscape continues to evolve, investing in robust supplier data management processes will be a key differentiator for organizations looking to stay ahead of the competition and drive long-term success.
Supplier Data Management Process | Key Elements |
---|---|
Data Standardization | – Consistent data fields – Naming conventions – Compatibility with existing systems |
Centralized Data Repository | – Dedicated SRM system – Integration with ERP/PLM – Data governance and security |
Automated Data Capture and Validation | – EDI or web-based portals – OCR technology – Data validation rules and checks |
Supplier Collaboration and Communication | – Regular communication channels – Performance metrics and feedback – Training and support |
Data Governance and Maintenance | – Clear roles and responsibilities – Data quality metrics and monitoring – Regular data audits and cleansing |
By implementing these key elements and following the step-by-step approach outlined in this article, manufacturers can design easy processes for creating and linking supplier data to components, enabling them to drive efficiency, quality, and competitiveness in their operations.
Leave a Reply