Introduction to PCB Packaging and Its Importance
Printed Circuit Board (PCB) packaging is a crucial aspect of electronics manufacturing that has seen significant advancements in recent years. As electronic devices become smaller, more powerful, and more complex, the need for innovative PCB packaging solutions has become increasingly important. Cutting edge technology in PCB packaging is essential for ensuring the reliability, performance, and longevity of electronic devices in various industries, including consumer electronics, automotive, aerospace, and medical devices.
PCB packaging involves the encapsulation and protection of electronic components and circuits on a PCB, as well as the interconnection of the PCB with other components or systems. The primary goals of PCB packaging are to:
- Protect the electronic components from environmental factors such as moisture, dust, and shock.
- Provide electrical insulation and prevent short circuits.
- Facilitate heat dissipation to prevent overheating and ensure optimal performance.
- Enable efficient and reliable interconnection between the PCB and other components or systems.
As the demand for high-performance, miniaturized, and cost-effective electronic devices continues to grow, the development of cutting edge technology in PCB packaging has become a top priority for manufacturers and researchers alike.
Advanced Materials for PCB Packaging
One of the key areas of cutting edge technology in PCB packaging is the development and use of advanced materials. These materials offer improved properties such as better thermal conductivity, higher strength, and enhanced electrical insulation compared to traditional materials. Some of the most notable advanced materials used in PCB packaging include:
1. High-Performance Polymers
High-performance polymers, such as polyimide and liquid crystal polymer (LCP), offer excellent thermal stability, mechanical strength, and electrical insulation properties. These materials are particularly suitable for applications that require high reliability and durability, such as aerospace and automotive electronics.
2. Ceramic Materials
Ceramic materials, such as aluminum nitride (AlN) and silicon nitride (Si3N4), are known for their high thermal conductivity, low coefficient of thermal expansion (CTE), and excellent electrical insulation properties. These materials are ideal for high-power applications that generate significant heat, such as power electronics and LED packaging.
3. Metal Matrix Composites
Metal matrix composites (MMCs) are materials that combine a metal matrix with ceramic or graphite reinforcements. These materials offer a unique combination of high thermal conductivity, low CTE, and good mechanical strength. MMCs are particularly suitable for applications that require efficient heat dissipation and dimensional stability, such as high-performance computing and telecommunications.
4. Nanomaterials
Nanomaterials, such as carbon nanotubes (CNTs) and graphene, have emerged as promising materials for PCB packaging due to their exceptional electrical and thermal properties. These materials can be incorporated into polymer matrices to create nanocomposites with enhanced performance characteristics, such as improved thermal conductivity and mechanical strength.
Material | Key Properties | Typical Applications |
---|---|---|
High-Performance Polymers | High thermal stability, mechanical strength, electrical insulation | Aerospace, automotive electronics |
Ceramic Materials | High thermal conductivity, low CTE, excellent electrical insulation | Power electronics, LED packaging |
Metal Matrix Composites | High thermal conductivity, low CTE, good mechanical strength | High-performance computing, telecommunications |
Nanomaterials | Exceptional electrical and thermal properties | Nanocomposites for enhanced performance |
Advanced PCB Packaging Techniques
In addition to advanced materials, cutting edge technology in PCB packaging also involves the development and implementation of innovative packaging techniques. These techniques aim to improve the performance, reliability, and manufacturability of PCB packages. Some of the most notable advanced PCB packaging techniques include:
1. 3D Packaging
3D packaging is a technique that involves stacking multiple PCBs or chips vertically to create a compact, high-density package. This approach enables the integration of more functionality into a smaller footprint, reducing the overall size and weight of the electronic device. 3D packaging also offers improved electrical performance by reducing the interconnect length between components.
2. Embedded Components
Embedded component technology involves the integration of passive components, such as resistors and capacitors, directly into the PCB substrate. This technique reduces the surface area required for component placement, enabling further miniaturization of the PCB package. Embedded components also offer improved electrical performance by reducing parasitic effects and improving signal integrity.
3. Wafer-Level Packaging (WLP)
Wafer-level packaging is a technique that involves packaging individual dies at the wafer level, before singulation into individual chips. This approach offers several advantages, including reduced package size, improved electrical performance, and lower manufacturing costs. WLP is particularly suitable for applications that require high-density packaging and low-profile devices, such as mobile phones and wearable electronics.
4. Fan-Out Wafer-Level Packaging (FOWLP)
Fan-out wafer-level packaging is an advanced version of WLP that involves encapsulating the die in a molding compound and redistributing the interconnects over a larger area. This technique enables the integration of multiple dies and passive components into a single package, offering improved flexibility and functionality. FOWLP also offers excellent thermal and electrical performance, making it suitable for high-performance applications such as 5G telecommunications and artificial intelligence (AI) processors.
Packaging Technique | Key Benefits | Typical Applications |
---|---|---|
3D Packaging | High-density integration, improved electrical performance, reduced size and weight | High-performance computing, mobile devices |
Embedded Components | Miniaturization, improved electrical performance | Space-constrained devices, wearable electronics |
Wafer-Level Packaging | Reduced package size, improved electrical performance, lower manufacturing costs | Mobile phones, wearable electronics |
Fan-Out Wafer-Level Packaging | Multi-die integration, improved flexibility and functionality, excellent thermal and electrical performance | 5G telecommunications, AI processors |
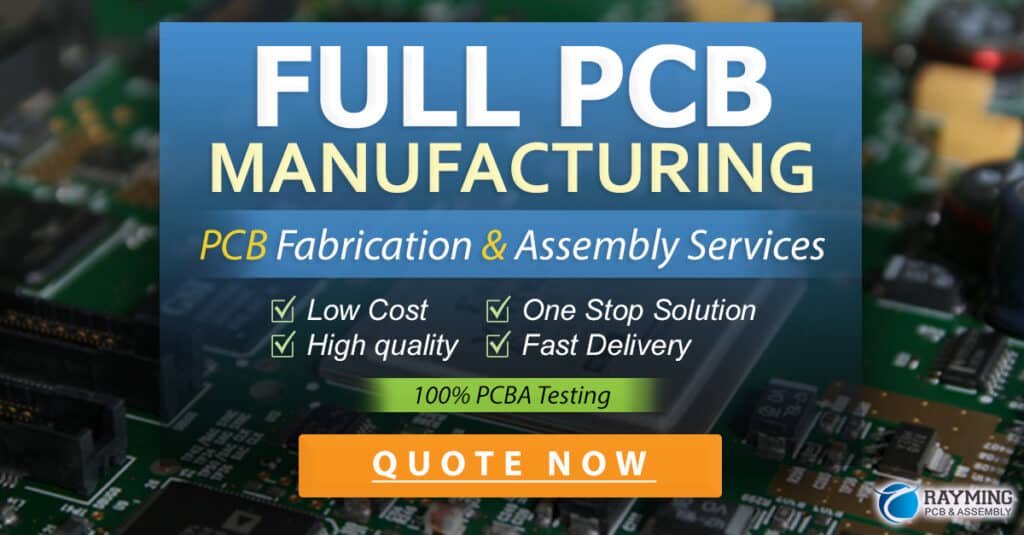
Challenges and Future Trends in PCB Packaging
Despite the significant advancements in cutting edge technology for PCB packaging, there are still several challenges that need to be addressed to ensure the continued growth and success of the electronics industry. Some of the key challenges include:
-
Thermal management: As electronic devices become more powerful and compact, the need for efficient thermal management solutions becomes increasingly critical. Developing advanced materials and packaging techniques that can effectively dissipate heat is a major challenge for PCB packaging.
-
Signal integrity: With the increasing speed and complexity of electronic systems, maintaining signal integrity is becoming more difficult. Designers must carefully consider factors such as impedance matching, crosstalk, and electromagnetic interference (EMI) when developing PCB packages.
-
Manufacturing complexity: Advanced PCB packaging techniques often involve complex manufacturing processes that require specialized equipment and expertise. Ensuring the reliability and consistency of these processes can be challenging, particularly for high-volume production.
-
Cost considerations: Implementing cutting edge technology in PCB packaging often comes with increased costs, both in terms of materials and manufacturing processes. Balancing the benefits of advanced packaging solutions with cost constraints is a significant challenge for the industry.
Looking to the future, several trends are expected to shape the development of cutting edge technology in PCB packaging:
-
Continued miniaturization: The demand for smaller, more compact electronic devices is expected to drive further advancements in PCB packaging, with a focus on 3D packaging, embedded components, and wafer-level packaging techniques.
-
Integration of heterogeneous technologies: The integration of multiple technologies, such as sensors, power management, and RF components, into a single PCB package is expected to become more prevalent, enabling the development of highly functional, compact devices.
-
Adoption of advanced materials: The use of advanced materials, such as high-performance polymers, ceramic materials, and nanomaterials, is expected to increase as the industry seeks to improve the thermal, mechanical, and electrical performance of PCB packages.
-
Sustainable packaging solutions: As environmental concerns continue to grow, the development of sustainable PCB packaging solutions, such as biodegradable materials and recyclable packaging, is expected to become a priority for the industry.
Frequently Asked Questions (FAQ)
-
Q: What is the importance of cutting edge technology in PCB packaging?
A: Cutting edge technology in PCB packaging is essential for ensuring the reliability, performance, and longevity of electronic devices in various industries. It enables the development of smaller, more powerful, and more complex devices while addressing challenges such as thermal management, signal integrity, and manufacturing complexity. -
Q: What are some of the advanced materials used in cutting edge PCB packaging?
A: Advanced materials used in cutting edge PCB packaging include high-performance polymers (e.g., polyimide and liquid crystal polymer), ceramic materials (e.g., aluminum nitride and silicon nitride), metal matrix composites, and nanomaterials (e.g., carbon nanotubes and graphene). -
Q: What are the benefits of 3D packaging in PCB packaging?
A: 3D packaging offers several benefits, including high-density integration, improved electrical performance, and reduced size and weight. By stacking multiple PCBs or chips vertically, 3D packaging enables the integration of more functionality into a smaller footprint and reduces the interconnect length between components. -
Q: What is the difference between wafer-level packaging (WLP) and fan-out wafer-level packaging (FOWLP)?
A: Wafer-level packaging involves packaging individual dies at the wafer level before singulation into individual chips, offering reduced package size, improved electrical performance, and lower manufacturing costs. Fan-out wafer-level packaging is an advanced version of WLP that involves encapsulating the die in a molding compound and redistributing the interconnects over a larger area, enabling multi-die integration and improved flexibility and functionality. -
Q: What are some of the future trends in cutting edge PCB packaging technology?
A: Future trends in cutting edge PCB packaging technology include continued miniaturization, integration of heterogeneous technologies, adoption of advanced materials, and the development of sustainable packaging solutions. These trends are expected to drive the development of highly functional, compact, and environmentally friendly electronic devices.
Conclusion
Cutting edge technology in PCB packaging is a rapidly evolving field that plays a crucial role in the advancement of the electronics industry. By leveraging advanced materials and innovative packaging techniques, manufacturers and researchers are able to develop smaller, more powerful, and more reliable electronic devices that meet the growing demands of various industries.
As the industry continues to face challenges such as thermal management, signal integrity, manufacturing complexity, and cost considerations, the development of cutting edge technology in PCB packaging will remain a top priority. Future trends, such as continued miniaturization, integration of heterogeneous technologies, adoption of advanced materials, and sustainable packaging solutions, are expected to shape the direction of PCB packaging technology in the coming years.
By staying at the forefront of cutting edge technology in PCB packaging, manufacturers can ensure their products remain competitive in an increasingly demanding market, while also contributing to the overall growth and success of the electronics industry.
Leave a Reply