Introduction to Coplanar Waveguide
A coplanar waveguide (CPW) is a type of electrical transmission line that is widely used in microwave circuits and integrated circuits. It consists of a center strip conductor with two ground planes running parallel on either side, all on the same plane. This configuration allows for easy integration with other planar circuits and provides a number of advantages over other transmission line structures, such as microstrip and stripline.
Advantages of Coplanar Waveguide
- Low dispersion: CPW has low dispersion, which means that the signal maintains its shape and integrity over longer distances compared to other transmission lines.
- Easy integration: The planar nature of CPW makes it easy to integrate with other planar circuits and components, such as antennas, filters, and active devices.
- Wide bandwidth: CPW can support a wide range of frequencies, from DC to several hundred GHz, making it suitable for high-frequency applications.
- Good isolation: The ground planes on either side of the center conductor provide good isolation between adjacent lines, reducing crosstalk and interference.
Design Considerations for Coplanar Waveguide
When designing a coplanar waveguide, several factors must be taken into account to ensure optimal performance. These include:
Characteristic Impedance
The characteristic impedance of a CPW is determined by the width of the center conductor, the gap between the center conductor and the ground planes, and the dielectric constant of the substrate. The characteristic impedance can be calculated using the following equation:
Z₀ = (60π / √ε_eff) × ln[(s + 2w) / s]
where:
– Z₀ is the characteristic impedance
– ε_eff is the effective dielectric constant
– s is the gap between the center conductor and the ground planes
– w is the width of the center conductor
To achieve a desired characteristic impedance, the dimensions of the CPW must be carefully chosen based on the substrate material and the operating frequency.
Substrate Selection
The choice of substrate material is crucial in CPW design, as it affects the propagation velocity, loss, and power handling capability of the transmission line. Common substrate materials for CPW include:
- Alumina (Al₂O₃): High dielectric constant, low loss, and good thermal conductivity. Suitable for high-power applications.
- Quartz (SiO₂): Low dielectric constant, very low loss, and good thermal stability. Ideal for high-frequency and low-loss applications.
- Gallium Arsenide (GaAs): Semi-insulating, high electron mobility, and good thermal conductivity. Used in monolithic microwave integrated circuits (MMICs).
- Rogers materials (e.g., RO3003, RO4003C): Low dielectric constant, low loss, and good thermal stability. Widely used in high-frequency printed circuit boards (PCBs).
The substrate thickness and dielectric constant determine the effective dielectric constant of the CPW, which in turn affects the characteristic impedance and propagation velocity.
Conductor Dimensions
The width of the center conductor and the gap between the center conductor and the ground planes are critical dimensions in CPW design. These dimensions determine the characteristic impedance, as well as the current carrying capacity and power handling capability of the transmission line.
Wider center conductors and smaller gaps result in lower characteristic impedance and higher current carrying capacity, but also increase the overall size of the CPW. Narrower center conductors and larger gaps have the opposite effect. A trade-off must be made between the desired electrical characteristics and the available space on the substrate.
Losses in Coplanar Waveguide
Like all transmission lines, CPW experiences losses due to conductor resistance, dielectric loss, and radiation. These losses increase with frequency and can limit the maximum operating frequency and the maximum transmission distance of the CPW.
-
Conductor loss: Caused by the resistance of the conductors, which increases with frequency due to the skin effect. Can be minimized by using high-conductivity materials, such as copper or gold, and by increasing the thickness of the conductors.
-
Dielectric loss: Caused by the loss tangent of the substrate material, which converts electromagnetic energy into heat. Can be minimized by using low-loss substrates, such as quartz or Rogers materials.
-
Radiation loss: Caused by the discontinuities in the CPW, such as bends, transitions, and open ends, which radiate energy into the surrounding space. Can be minimized by using smooth transitions and avoiding sharp bends or open ends.
The total loss of a CPW can be expressed as the sum of these three loss components:
α_total = α_conductor + α_dielectric + α_radiation
where:
– α_total is the total loss per unit length
– α_conductor is the conductor loss per unit length
– α_dielectric is the dielectric loss per unit length
– α_radiation is the radiation loss per unit length
By minimizing these losses, the performance and efficiency of the CPW can be optimized for the specific application.
Applications of Coplanar Waveguide
Coplanar waveguides find use in a wide range of microwave and high-frequency applications, such as:
-
Microwave integrated circuits (MICs): CPW is used as the main transmission line structure in MICs, connecting various components such as amplifiers, mixers, and filters.
-
Monolithic microwave integrated circuits (MMICs): CPW is used as the on-chip transmission line in MMICs, which are fabricated on a single semiconductor substrate, such as GaAs or InP.
-
High-speed digital circuits: CPW is used as the interconnect between high-speed digital components, such as processors, memories, and serializer/deserializer (SerDes) devices.
-
Antennas: CPW is used as the feed line for planar antennas, such as patch antennas and slot antennas, providing a low-loss and wideband connection to the radiating element.
-
Filters: CPW is used to implement various types of microwave filters, such as low-pass, high-pass, and band-pass filters, using distributed elements like stubs and resonators.
-
Sensors: CPW is used as the sensing element in microwave sensors, such as moisture sensors, gas sensors, and temperature sensors, where the change in the CPW characteristics is used to detect the presence or quantity of the measurand.
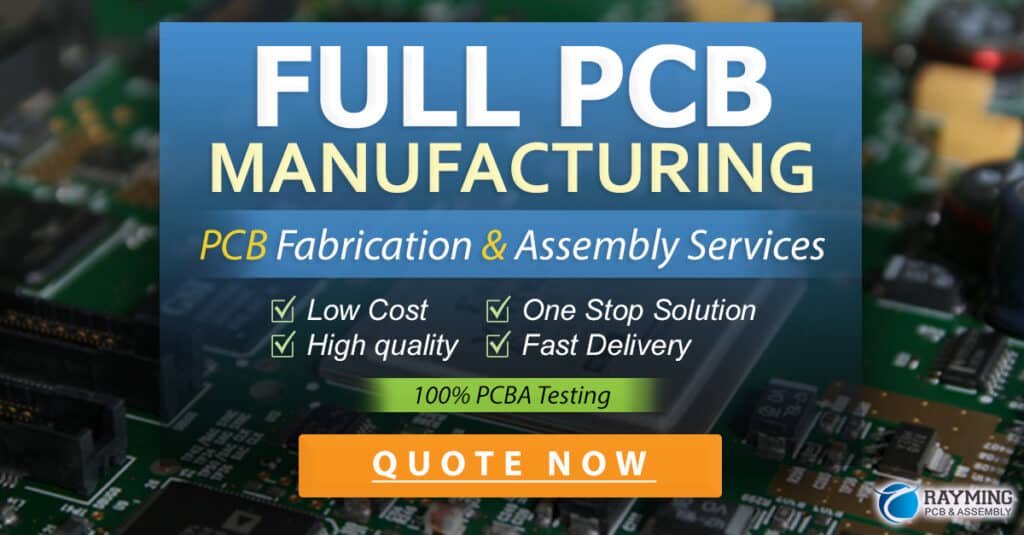
Coplanar Waveguide Discontinuities and Transitions
In practical CPW circuits, various discontinuities and transitions are encountered, such as bends, tees, crosses, and transitions to other transmission line structures. These discontinuities and transitions can cause reflections, losses, and mode conversion, which can degrade the performance of the circuit.
Bends
Bends in CPW are used to change the direction of the transmission line on the substrate. There are two main types of bends: right-angle bends and chamfered bends.
Right-angle bends have a sharp 90-degree turn, which can cause significant reflections and radiation losses. Chamfered bends, on the other hand, have a smooth transition with a 45-degree chamfer, which reduces the reflections and losses.
The chamfer length can be optimized to minimize the reflections over a wide frequency range. A common rule of thumb is to make the chamfer length equal to the center conductor width.
Tees and Crosses
Tees and crosses are used to split or combine signals in CPW circuits. A tee has three ports, while a cross has four ports.
At the junction of a tee or cross, there is a discontinuity in the characteristic impedance, which can cause reflections and mode conversion. To minimize these effects, the junction can be compensated by adjusting the width of the center conductor and the gap between the conductors.
One technique is to use a symmetric tee or cross, where the width of the center conductor is increased at the junction to maintain a constant characteristic impedance. Another technique is to use a radial stub at the junction, which acts as a matching network to reduce the reflections.
Transitions to Other Transmission Lines
In some cases, it may be necessary to transition from CPW to another transmission line structure, such as microstrip or stripline. These transitions can cause impedance mismatch and mode conversion, which can lead to reflections and losses.
To minimize these effects, the transition should be designed to provide a smooth and gradual change in the electric and magnetic field distributions. This can be achieved by using tapered sections, where the width of the conductors and the gap between them are gradually changed to match the impedance and field distribution of the other transmission line.
Another technique is to use a via hole to connect the ground planes of the CPW to the ground plane of the other transmission line. This provides a low-impedance path for the return current and helps to suppress unwanted modes.
Simulation and Measurement of Coplanar Waveguide
To design and optimize CPW circuits, various simulation and measurement techniques are used. These techniques allow the designer to predict the performance of the circuit before fabrication and to verify the actual performance after fabrication.
Electromagnetic Simulation
Electromagnetic (EM) simulation is used to model the CPW structure and predict its electrical characteristics, such as characteristic impedance, propagation constant, and scattering parameters (S-parameters). There are several EM simulation methods, such as:
-
Finite Element Method (FEM): A numerical technique that divides the structure into small elements and solves Maxwell’s equations for each element. Suitable for complex geometries and inhomogeneous materials.
-
Method of Moments (MoM): A numerical technique that solves the integral equations for the currents on the conductors. Suitable for planar structures and open boundaries.
-
Finite-Difference Time-Domain (FDTD): A numerical technique that solves Maxwell’s equations in the time domain using finite differences. Suitable for broadband and transient analysis.
These simulation methods are implemented in commercial EM simulation software, such as Ansys HFSS, Keysight ADS, and CST Studio Suite. The designer can create a 3D model of the CPW structure, define the materials and boundary conditions, and run the simulation to obtain the S-parameters and field distributions.
Network Analysis
Network analysis is used to characterize the CPW circuit in terms of its S-parameters, which describe the reflection and transmission of signals at each port. The S-parameters can be measured using a vector network analyzer (VNA) or simulated using a circuit simulator.
The measured or simulated S-parameters can be used to derive other important parameters, such as:
-
Return loss: A measure of the reflection at each port, indicating how well the circuit is matched to the system impedance.
-
Insertion loss: A measure of the transmission through the circuit, indicating how much signal is lost due to dissipation and radiation.
-
Group delay: A measure of the phase distortion of the signal, indicating how much the different frequency components are delayed relative to each other.
-
Characteristic impedance: Can be extracted from the S-parameters using various methods, such as the reflection method or the transmission method.
By comparing the measured and simulated S-parameters, the designer can validate the simulation model and optimize the circuit for the desired performance.
Time-Domain Reflectometry
Time-domain reflectometry (TDR) is a technique used to characterize the impedance profile of a transmission line, such as CPW, in the time domain. In TDR, a fast-rising voltage step is sent down the transmission line, and the reflections from the discontinuities are measured as a function of time.
By analyzing the amplitude and timing of the reflections, the impedance profile of the CPW can be determined, including the characteristic impedance, the location and magnitude of the discontinuities, and the velocity of propagation.
TDR is particularly useful for detecting and locating faults in CPW circuits, such as open or short circuits, and for optimizing the impedance matching of the transitions and discontinuities.
Advanced Topics in Coplanar Waveguide
Slow-Wave Structures
Slow-wave structures are modified CPW structures that reduce the phase velocity of the propagating wave, allowing for shorter wavelengths and smaller circuit sizes. Some examples of slow-wave CPW structures are:
-
Periodically loaded CPW: The center conductor is periodically loaded with capacitive or inductive elements, such as patches or slots, which reduce the phase velocity.
-
Patterned ground CPW: The ground planes are patterned with periodic slots or holes, which increase the effective inductance and reduce the phase velocity.
-
Substrate integrated waveguide (SIW) CPW: The CPW is integrated with a substrate integrated waveguide, which confines the fields in a dielectric-filled cavity and reduces the phase velocity.
Slow-wave CPW structures are used in miniaturized microwave circuits, such as filters, couplers, and phase shifters, where a compact size is required.
Nonlinear Coplanar Waveguide
Nonlinear CPW structures are designed to exhibit nonlinear behavior, such as harmonic generation, mixing, and switching. This is achieved by integrating nonlinear elements, such as diodes, transistors, or ferroelectric materials, into the CPW structure.
Some examples of nonlinear CPW applications are:
-
CPW-based frequency multipliers: The nonlinear element generates harmonics of the input signal, which are filtered and output at a higher frequency.
-
CPW-based mixers: The nonlinear element mixes two input signals to produce sum and difference frequencies, which are used for frequency conversion or modulation.
-
CPW-based switches: The nonlinear element acts as a voltage-controlled switch, allowing the CPW to be turned on or off based on the control signal.
Nonlinear CPW structures are used in various microwave systems, such as radar, communications, and instrumentation, where signal processing and control are required.
Multilayer Coplanar Waveguide
Multilayer CPW structures consist of multiple dielectric and conductor layers, which are used to increase the functionality and performance of the circuit. Some examples of multilayer CPW structures are:
-
Stacked CPW: Multiple CPW layers are stacked vertically, with dielectric layers in between, to create a 3D transmission line structure. This allows for higher power handling, lower losses, and better isolation between the layers.
-
Conductor-backed CPW: A conductor layer is added below the substrate, serving as a ground plane for the CPW. This provides better mechanical support, heat sinking, and shielding from external interference.
-
Embedded CPW: The CPW is embedded within the substrate, with dielectric layers above and below, to create a buried transmission line structure. This provides better protection from environmental effects, such as moisture and contamination.
Multilayer CPW structures are used in high-performance microwave circuits, such as power amplifiers, antenna arrays, and multi-chip modules, where integration and packaging are critical.
Conclusion
Coplanar waveguide with ground is a versatile and widely used transmission line structure for microwave and high-frequency applications. Its planar geometry, low dispersion, and easy integration make it suitable for a variety of circuits, such as MICs, MMICs, antennas, and filters.
The design of CPW involves careful consideration of the characteristic impedance, substrate selection, conductor dimensions, and losses. Discontinuities and transitions, such as bends, tees, and crosses, must be properly compensated to minimize reflections and mode conversion.
Simulation and measurement techniques, such as EM simulation, network analysis, and time-domain reflectometry, are essential for the design and optimization of CPW circuits. Advanced topics, such as slow-wave structures, nonlinear CPW, and multilayer CPW, expand the capabilities and applications of this transmission line structure.
As the demand for high-frequency and high-speed circuits continues to grow, coplanar waveguide will remain an important building block for microwave and millimeter-wave systems.
Frequently Asked Questions
-
What is a coplanar waveguide with ground?
A coplanar waveguide with ground is a transmission line structure consisting of a center strip conductor with two parallel ground planes on either side, all on the same plane. -
What are the advantages of using a coplanar waveguide?
Coplanar waveguides offer several advantages, including low dispersion, easy integration with planar circuits, wide bandwidth, and good isolation between adjacent lines. -
How does the characteristic impedance of a coplanar waveguide affect its performance?
The characteristic impedance of a coplanar waveguide determines the reflection and transmission of signals at the interfaces between the waveguide and other components. Matching the impedance of the waveguide to the system impedance minimizes reflections and ensures maximum power transfer. -
What are some common applications of coplanar waveguides?
Coplanar waveguides are used in various microwave and high-frequency applications, such as microwave integrated circuits (MICs), monolithic microwave integrated circuits (MMICs), high-speed digital circuits, antennas, filters, and sensors. -
How can the performance of a coplanar waveguide be optimized?
The performance of a coplanar waveguide can be optimized by carefully selecting the substrate material, conductor dimensions, and layout, as well as by using appropriate compensation techniques for discontinuities and transitions. Simulation and measurement techniques, such as EM simulation and network analysis, are also essential for optimizing the waveguide design.
Leave a Reply