What is Continuous Conduction Mode (CCM) in SMPS?
Continuous Conduction Mode (CCM) is one of the operating modes of Switch Mode Power Supplies (SMPS). In CCM, the current through the inductor never reaches zero during the switching cycle. This means that the inductor current remains continuous and does not drop to zero at any point.
How CCM Differs from Other Conduction Modes
To better understand CCM, let’s compare it with the other common conduction mode in SMPS: Discontinuous Conduction Mode (DCM).
Conduction Mode | Inductor Current | Advantages | Disadvantages |
---|---|---|---|
CCM | Never reaches zero | Lower peak currents, reduced EMI, higher efficiency at heavy loads | More complex control, higher switching losses |
DCM | Reaches zero during each switching cycle | Simpler control, lower switching losses | Higher peak currents, increased EMI, lower efficiency at light loads |
In DCM, the inductor current reaches zero during each switching cycle, resulting in a discontinuous current waveform. While DCM offers simpler control and lower switching losses, it comes with higher peak currents, increased electromagnetic interference (EMI), and lower efficiency at light loads.
On the other hand, CCM maintains a continuous inductor current, leading to lower peak currents, reduced EMI, and higher efficiency at heavy loads. However, CCM requires more complex control circuitry and may exhibit higher switching losses compared to DCM.
Working Principles of CCM SMPS
To grasp the working principles of CCM SMPS, let’s examine the basic components and their roles in the power conversion process.
Key Components of CCM SMPS
- Power Switch (MOSFET or IGBT)
- Inductor
- Diode
- Output Capacitor
- Control Circuitry
The power switch, typically a MOSFET or IGBT, is responsible for turning on and off rapidly to control the flow of current through the inductor. The inductor stores energy in its magnetic field when the switch is on and releases that energy when the switch is off. The diode ensures unidirectional current flow, while the output capacitor smooths the output voltage ripple. The control circuitry regulates the switching duty cycle to maintain a stable output voltage.
CCM Operation in Buck Converters
Buck converters are a common type of SMPS that step down the input voltage to a lower output voltage. In CCM operation, the buck converter’s inductor current never reaches zero during the switching cycle. The inductor current waveform consists of a rising slope when the switch is on and a falling slope when the switch is off.
The duty cycle (D) of the power switch determines the ratio of the output voltage (Vout) to the input voltage (Vin):
Vout = D × Vin
By adjusting the duty cycle, the control circuitry can regulate the output voltage to the desired level.
CCM Operation in Boost Converters
Boost converters, another type of SMPS, step up the input voltage to a higher output voltage. In CCM operation, the boost converter’s inductor current remains continuous and never drops to zero. The inductor current waveform has a rising slope when the switch is on and a falling slope when the switch is off.
The relationship between the input voltage (Vin) and the output voltage (Vout) in a boost converter operating in CCM is given by:
Vout = Vin ÷ (1 - D)
Where D is the duty cycle of the power switch. By controlling the duty cycle, the boost converter can achieve the desired output voltage.
Benefits and Advantages of CCM SMPS
CCM SMPS offers several benefits and advantages over other conduction modes:
-
Lower Peak Currents: In CCM, the inductor current never reaches zero, resulting in lower peak currents compared to DCM. Lower peak currents reduce stress on components and minimize conduction losses.
-
Reduced EMI: The continuous inductor current in CCM leads to smoother current waveforms and less high-frequency content. This reduction in electromagnetic interference (EMI) simplifies the design of EMI filters and helps meet electromagnetic compatibility (EMC) requirements.
-
Higher Efficiency at Heavy Loads: CCM SMPS exhibits higher efficiency at heavy load conditions compared to DCM. The continuous inductor current minimizes conduction losses and improves overall power conversion efficiency.
-
Smaller Inductor Size: CCM allows for the use of smaller inductors compared to DCM for the same power rating. Smaller inductors reduce the overall size and cost of the SMPS.
-
Improved Transient Response: CCM SMPS typically offers better transient response characteristics compared to DCM. The continuous inductor current enables faster response to load changes and minimizes output voltage deviations.
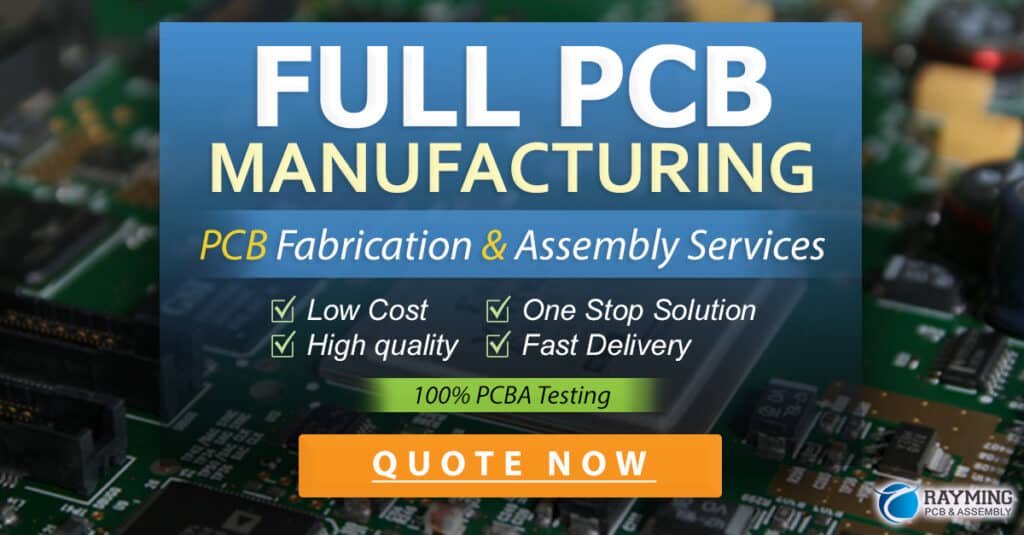
Practical Applications of CCM SMPS
CCM SMPS finds applications in various power conversion scenarios where efficiency, low EMI, and tight voltage regulation are crucial:
-
High-Power DC-DC Converters: CCM is commonly employed in high-power DC-DC converters used in industrial, automotive, and renewable energy applications. The lower peak currents and higher efficiency of CCM make it suitable for handling high power levels.
-
Battery Charging Systems: CCM SMPS is often used in battery charging systems for portable devices, electric vehicles, and energy storage systems. The continuous inductor current enables precise control of the charging current and voltage, ensuring optimal charging performance.
-
LED Drivers: CCM SMPS is widely used in LED lighting applications, particularly in high-power LED drivers. The continuous inductor current provides stable and efficient power delivery to the LEDs, ensuring consistent brightness and color rendition.
-
Power Factor Correction (PFC) Circuits: CCM is commonly employed in active power factor correction (PFC) circuits to improve the power factor and reduce harmonic distortion in AC-DC power supplies. CCM PFC circuits offer high efficiency and low EMI, making them suitable for a wide range of applications.
-
Uninterruptible Power Supplies (UPS): CCM SMPS is used in UPS systems to provide reliable and efficient power backup during mains power interruptions. The continuous inductor current enables smooth power transfer and minimizes voltage fluctuations during load transitions.
Frequently Asked Questions (FAQ)
-
What is the main difference between CCM and DCM in SMPS?
In CCM, the inductor current never reaches zero during the switching cycle, while in DCM, the inductor current reaches zero and remains at zero for a portion of each switching cycle. -
Why is CCM preferred over DCM in high-power applications?
CCM is preferred in high-power applications because it offers lower peak currents, reduced EMI, and higher efficiency at heavy loads compared to DCM. These characteristics make CCM suitable for handling high power levels while minimizing losses and interference. -
What are the disadvantages of CCM compared to DCM?
The main disadvantages of CCM compared to DCM are more complex control circuitry and higher switching losses. CCM requires more sophisticated control algorithms to maintain stability and regulate the output voltage accurately. -
How does CCM help in reducing EMI in SMPS?
CCM results in smoother inductor current waveforms with less high-frequency content compared to DCM. This reduction in high-frequency components minimizes electromagnetic interference (EMI) generated by the SMPS, simplifying the design of EMI filters and improving electromagnetic compatibility. -
Can CCM be used in both buck and boost converter topologies?
Yes, CCM can be employed in both buck and boost converter topologies. In buck converters, CCM enables efficient voltage step-down, while in boost converters, CCM allows for voltage step-up with high efficiency and low EMI.
Conclusion
Continuous Conduction Mode (CCM) is a crucial operating mode in Switch Mode Power Supplies (SMPS) that offers numerous benefits and advantages. By maintaining a continuous inductor current, CCM enables lower peak currents, reduced EMI, higher efficiency at heavy loads, and improved transient response compared to Discontinuous Conduction Mode (DCM).
Understanding the working principles and characteristics of CCM SMPS is essential for designing efficient and reliable power conversion systems. CCM finds applications in various domains, including high-power DC-DC converters, battery charging systems, LED drivers, power factor correction circuits, and uninterruptible power supplies.
By leveraging the advantages of CCM, power electronics engineers can develop SMPS solutions that meet stringent performance, efficiency, and EMC requirements. As the demand for efficient and compact power supplies continues to grow, CCM SMPS will play a vital role in shaping the future of power conversion technology.
Leave a Reply