Introduction to SMT Process Defects
Surface Mount Technology (SMT) has revolutionized the electronics manufacturing industry by enabling the production of smaller, faster, and more reliable electronic devices. However, the SMT process is not without its challenges, and various defects can occur during the soldering process. These defects can lead to reduced performance, reliability issues, and even complete failure of the electronic components. In this article, we will discuss the most common SMT process defects and how to avoid them to ensure high-quality soldering results.
Types of SMT Process Defects
1. Bridging
Bridging is one of the most common SMT process defects, occurring when solder inadvertently connects two or more leads or pads that should not be connected. This can cause short circuits and lead to device malfunction.
Causes of Bridging
- Excessive solder paste
- Incorrect solder paste viscosity
- Improper stencil design or alignment
- Inadequate cleaning of the stencil
- Incorrect component placement
Prevention Techniques
- Optimize solder paste volume and viscosity
- Ensure proper stencil design and alignment
- Regularly clean and maintain stencils
- Implement accurate component placement processes
2. Tombstoning
Tombstoning, also known as the “Manhattan effect” or “Stonehenge effect,” occurs when a component stands up on one end during the soldering process. This defect is most common with small, lightweight components such as chip resistors and capacitors.
Causes of Tombstoning
- Uneven heating of component leads
- Unbalanced solder paste on the pads
- Incorrect component placement
- Inadequate soldering temperature or time
Prevention Techniques
- Ensure even heating during the soldering process
- Balance solder paste on the pads
- Implement accurate component placement processes
- Optimize soldering temperature and time
3. Solder Balling
Solder balling occurs when small spheres of solder form on the surface of the PCB or component leads. These solder balls can cause short circuits and lead to device malfunction.
Causes of Solder Balling
- Excessive solder paste
- Incorrect solder paste composition
- Inadequate soldering temperature or time
- Contamination on the PCB or component surfaces
Prevention Techniques
- Optimize solder paste volume and composition
- Ensure proper soldering temperature and time
- Maintain cleanliness of the PCB and component surfaces
4. Insufficient Solder Joint
Insufficient solder joints occur when there is not enough solder to form a proper connection between the component lead and the PCB pad. This can lead to poor electrical conductivity and mechanical strength.
Causes of Insufficient Solder Joints
- Inadequate solder paste volume
- Incorrect solder paste viscosity
- Improper stencil design or alignment
- Incorrect soldering temperature or time
Prevention Techniques
- Optimize solder paste volume and viscosity
- Ensure proper stencil design and alignment
- Implement appropriate soldering temperature and time
5. Cold Solder Joint
Cold solder joints occur when the solder does not melt completely, resulting in a dull, grainy appearance and poor mechanical strength. This defect can lead to intermittent electrical connections and device failure.
Causes of Cold Solder Joints
- Insufficient soldering temperature
- Inadequate soldering time
- Contamination on the PCB or component surfaces
- Incorrect solder paste composition
Prevention Techniques
- Ensure proper soldering temperature and time
- Maintain cleanliness of the PCB and component surfaces
- Use appropriate solder paste composition
Defect Detection and Inspection Techniques
To ensure high-quality soldering results, it is essential to implement effective defect detection and inspection techniques. Some common methods include:
1. Visual Inspection
Visual inspection involves examining the soldered components and PCB surface for visible defects such as bridging, tombstoning, and solder balling. This can be done manually or using automated optical inspection (AOI) systems.
2. X-Ray Inspection
X-ray inspection is used to detect defects that are not visible on the surface, such as voids, insufficient solder joints, and component misalignment. This technique is particularly useful for inspecting components with hidden leads, such as ball grid arrays (BGAs) and quad flat no-leads (QFNs).
3. Electrical Testing
Electrical testing involves verifying the functionality and performance of the soldered components and circuits. This can be done using various methods, such as in-circuit testing (ICT), flying probe testing, and boundary scan testing.
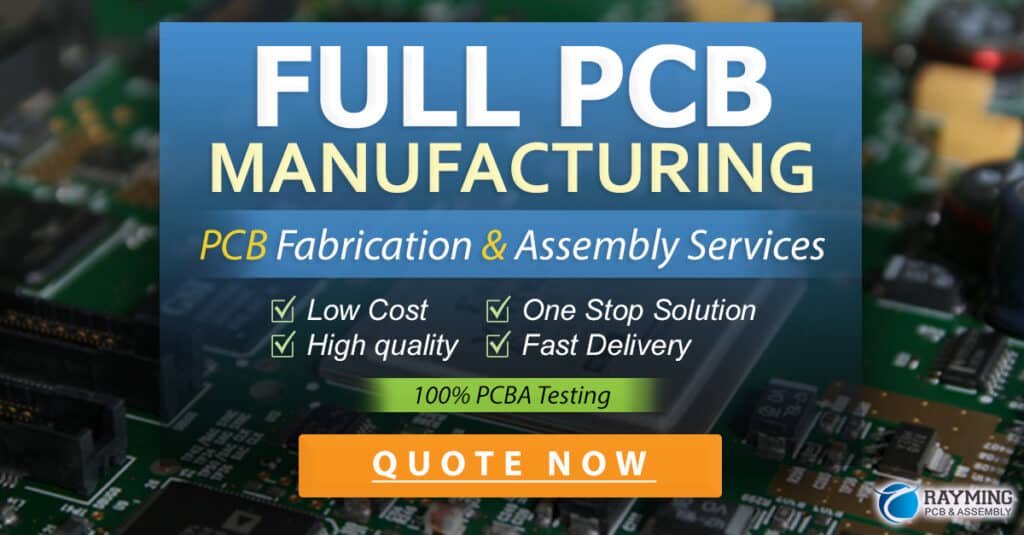
Best Practices for Avoiding SMT Process Defects
To minimize the occurrence of SMT process defects, consider implementing the following best practices:
- Use high-quality solder paste with the appropriate composition and viscosity for your specific application.
- Ensure proper stencil design and alignment to achieve optimal solder paste deposition.
- Implement accurate component placement processes using pick-and-place machines or other automation tools.
- Optimize soldering temperature and time based on the component and PCB specifications.
- Maintain cleanliness of the PCB and component surfaces to prevent contamination and ensure proper solder joint formation.
- Regularly clean and maintain stencils, pick-and-place nozzles, and other equipment to ensure consistent performance.
- Implement effective defect detection and inspection techniques, such as visual inspection, X-ray inspection, and electrical testing.
- Provide adequate training for operators and technicians to ensure they are familiar with SMT process best practices and can identify and prevent common defects.
Frequently Asked Questions (FAQ)
- What is the most common SMT process defect?
-
Bridging is one of the most common SMT process defects, occurring when solder inadvertently connects two or more leads or pads that should not be connected.
-
What causes tombstoning in SMT soldering?
-
Tombstoning can be caused by uneven heating of component leads, unbalanced solder paste on the pads, incorrect component placement, and inadequate soldering temperature or time.
-
How can solder balling be prevented in the SMT process?
-
Solder balling can be prevented by optimizing solder paste volume and composition, ensuring proper soldering temperature and time, and maintaining cleanliness of the PCB and component surfaces.
-
What are some effective defect detection and inspection techniques for SMT soldering?
-
Some effective defect detection and inspection techniques for SMT soldering include visual inspection, X-ray inspection, and electrical testing.
-
What are some best practices for avoiding SMT process defects?
- Best practices for avoiding SMT process defects include using high-quality solder paste, ensuring proper stencil design and alignment, implementing accurate component placement processes, optimizing soldering temperature and time, maintaining cleanliness, regularly cleaning and maintaining equipment, implementing effective defect detection and inspection techniques, and providing adequate training for operators and technicians.
Conclusion
SMT process defects can have a significant impact on the quality, reliability, and performance of electronic devices. By understanding the common types of defects, their causes, and prevention techniques, manufacturers can take steps to minimize their occurrence and ensure high-quality soldering results. Implementing best practices, such as using high-quality materials, ensuring proper process control, and employing effective defect detection and inspection techniques, can help to reduce the risk of SMT process defects and improve overall product quality.
Defect Type | Description | Causes | Prevention Techniques |
---|---|---|---|
Bridging | Solder inadvertently connects two or more leads or pads that should not be connected | – Excessive solder paste – Incorrect solder paste viscosity – Improper stencil design or alignment – Inadequate cleaning of the stencil – Incorrect component placement |
– Optimize solder paste volume and viscosity – Ensure proper stencil design and alignment – Regularly clean and maintain stencils – Implement accurate component placement processes |
Tombstoning | A component stands up on one end during the soldering process | – Uneven heating of component leads – Unbalanced solder paste on the pads – Incorrect component placement – Inadequate soldering temperature or time |
– Ensure even heating during the soldering process – Balance solder paste on the pads – Implement accurate component placement processes – Optimize soldering temperature and time |
Solder Balling | Small spheres of solder form on the surface of the PCB or component leads | – Excessive solder paste – Incorrect solder paste composition – Inadequate soldering temperature or time – Contamination on the PCB or component surfaces |
– Optimize solder paste volume and composition – Ensure proper soldering temperature and time – Maintain cleanliness of the PCB and component surfaces |
Insufficient Solder Joint | Not enough solder to form a proper connection between the component lead and the PCB pad | – Inadequate solder paste volume – Incorrect solder paste viscosity – Improper stencil design or alignment – Incorrect soldering temperature or time |
– Optimize solder paste volume and viscosity – Ensure proper stencil design and alignment – Implement appropriate soldering temperature and time |
Cold Solder Joint | Solder does not melt completely, resulting in a dull, grainy appearance and poor mechanical strength | – Insufficient soldering temperature – Inadequate soldering time – Contamination on the PCB or component surfaces – Incorrect solder paste composition |
– Ensure proper soldering temperature and time – Maintain cleanliness of the PCB and component surfaces – Use appropriate solder paste composition |
By addressing these common SMT process defects and implementing the appropriate prevention techniques, manufacturers can significantly improve the quality and reliability of their electronic products.
Leave a Reply